AZoSensors speaks with Paul Allen from the University of Huddersfield's Institute of Railway Research about the integration of an ultrasonic sensor into railway track lubrication monitoring and maintenance. We discuss the benefits of sensor systems in the railway system, and why partnerships between SME, universities, and larger organizations can be advantageous for innovation.
Please could you introduce yourself and your current position at the University of Huddersfield?
My name is Paul Allen and I am a Professor of Railway Engineering and Technology and Director of the University of Huddersfield's Institute of Railway Research (IRR).
Could you provide an overview of this new partnership between Network Rail and the University of Huddersfield?
The IRR leads the Centre of Excellence in Rolling Stock within the UK Rail Research and Innovation Network (UKRRIN), a group of rail research-active UK universities working together to improve the rail system.
UKRRIN has a framework in place to provide research resources and capability to Network Rail (NR). This particular project is part of the HORIZON 2020, European-funded PIVOT 2 project, an initiative to develop technologies that increase the operational reliability of trains.
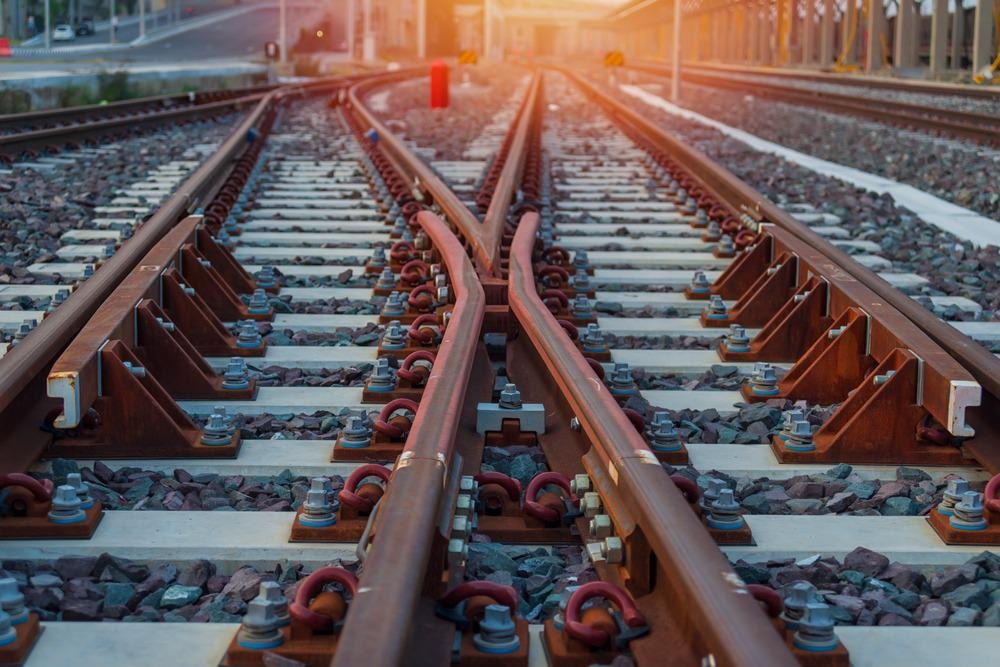
© Viewfoto studio/Shutterstock.com
How did you become involved with the project?
Perhaps three or four years before we began working with NR on this project, I developed the idea of using an ultrasonic sensor embedded within a railway wheel to detect the presence of rail gauge corner lubrication.
Working with Tribosonics Ltd, we discussed the concept with NR, who could see its benefit and embedded the development within its own involvement in the existing EU PIVOT and, subsequently PIVOT 2 project.
The importance of track lubrication is not necessarily known to the general public, yet its proper maintenance is essential for a capable railway system. What are the main issues that prevent proper maintenance?
Track lubrication is used for two primary reasons; to help manage the wear of the wheel and rail in plain line curves and through switches and crossings (S&C) and as a means of reducing the potential risk of flange climb derailments.
Track lubrication is applied at hundreds of discrete track locations across the entire railway network. The lubricant is delivered using relatively simple mechanical or electro-mechanical devices that can sometimes fail or run out of lubricant.
Manual inspection is time-consuming and requires personnel to be on track, so NR is trying to reduce this for safety reasons. As well as this, the result of manual inspections can be subjective – it's based on a fairly simple 'rub of a thumb' on the rail technique.
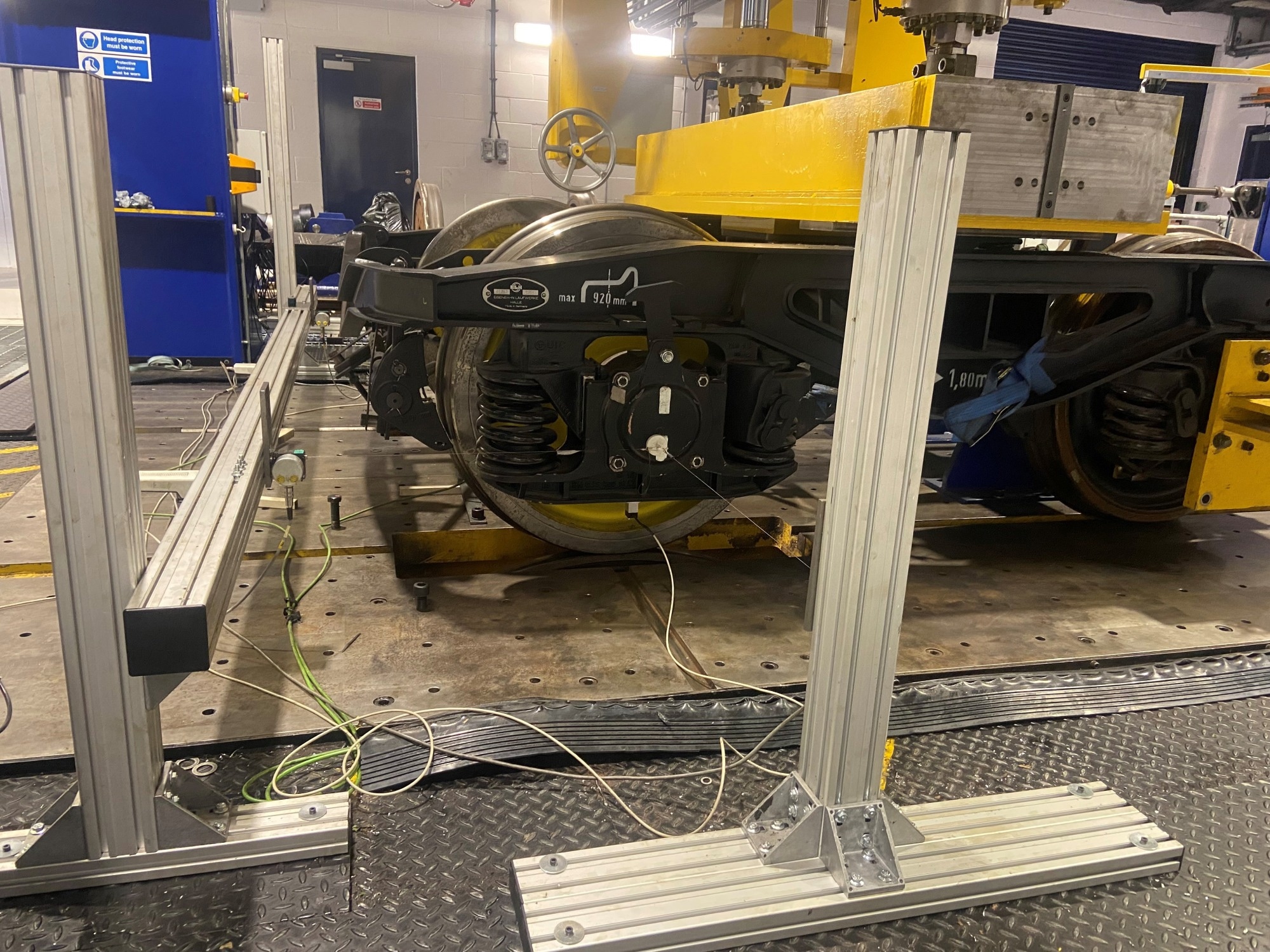
Test setup on HAROLD rig. © Paul Allen/University of Huddersfield
How can ultrasonic technologies be used to monitor track lubrication, and what are the benefits of such a remote sensing strategy?
The ultrasonic sensor contains a transmitter and receiver. Emitted ultrasound waves are passed through the wheel flange and into the rail gauge corner, where the lubricant is applied.
Very small differences in the time of flight of the reflected signals are detected and analyzed to differentiate between a dry (unlubricated) rail and one that is effectively lubricated; the system can also distinguish between lubricant and water – an essential performance requirement!
By developing a vehicle-mounted sensor solution, the disbenefits of manual inspection can be overcome, and a quantitative indicator and location of failed or defective lubricators will ultimately become available via NR's developing remote condition monitoring (RCM) platform.
We have seen ultrasound systems utilized in sectors like the biomedical and aerospace field, yet these sensors are relatively new to the railway network. Do you predict that the use of these advanced sensors will broaden in the future?
You could argue the rail industry has been relatively slow in adopting advanced sensors within smart RCM and prognostic systems. Still, it is now applying significant research and development effort, from both a rolling stock and infrastructure perspective, to embed these technologies within the rail system.
If deployed effectively in terms of both hardware and software (decision support) then the rail sector will begin to realize its undoubted benefits.
Are there any other applications, maintenance or otherwise, in the railway industry to which ultrasonic technologies could be applied?
The technology could potentially be applied to other condition monitoring challenges such as bearing faults or track faults, or maybe even detecting problematic low adhesion (leaves on the line) as they have excellent capabilities that make them particularly useful in detecting the presence of 3rd body layers, films or contaminants.
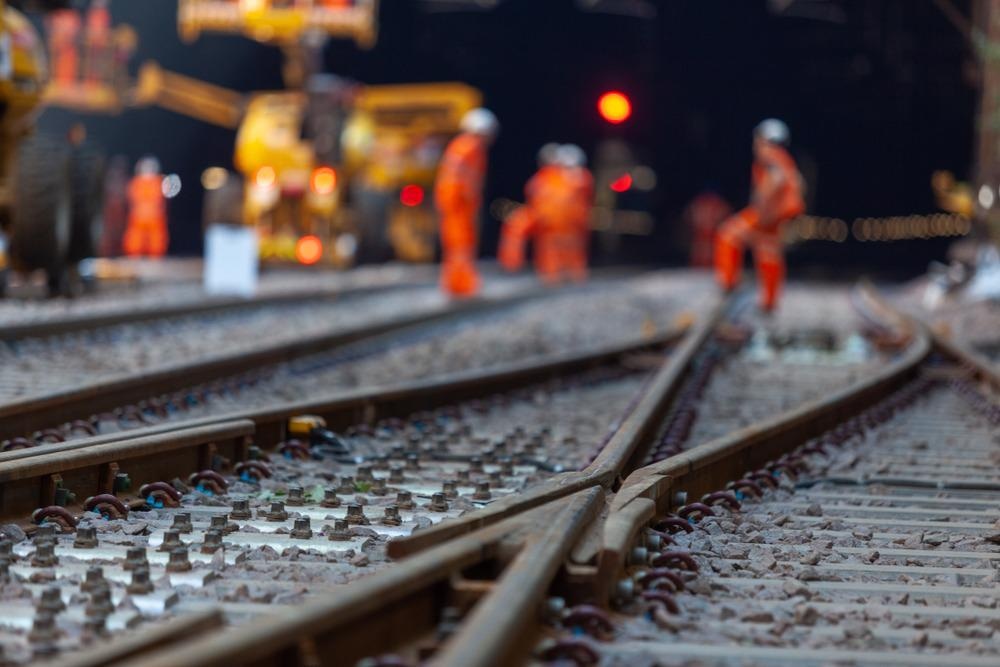
© Matthew Nichol/Shutterstock.com
The project involves a partnership between the university's dedicated railway research institute, a small-medium enterprise Tribosonics Ltd and larger organizations such as Network Rail. What advantages can multifaceted collaboration bring, especially for large-scale projects such as national transport?
Bringing together academia, SMEs and large organizations such as NR offers great benefit in terms of cross-fertilization of knowledge between the entities, providing smaller businesses with access to expensive test equipment, and of course, the business benefits to the SME if they have subsequent commercial opportunities to the products that are developed.
The larger organization also sees benefits in ensuring the project has a delivery mechanism to move technology solutions from academia to adoption on operational railways.
What are you most looking forward to with this project?
We are all very excited about the full-scale testing that will be carried out at the university this summer. Here, we will prove the target 100mph measurement speed and develop the detection algorithms, which will ultimately lead to an effective and robust RCM system to automatically detect and alert NR to the status of track lubrication.
Where can our readers go to stay up to date with the project and its activities?
The project does not have a live webpage but do follow me and the IRR on Twitter, where we'll be posting pictures and updates! @PaulAllenIRR, @IRRHud, plus some links below that may be useful.
About Paul Allen
Paul has over 20 years of experience as a leading railway researcher and industrial consultant. As a technical expert, his specialist field is railway vehicle dynamics and wheel-rail interface engineering. He has led a wide range of research and consultancy projects for many clients and collaborators in the UK and internationally.
Examples include wheel-rail interface consultancy, damage and cost modeling, vehicle optimization, vehicle safety approval, Railway Group Standards development, peer review and litigation work. He also has detailed knowledge in the light rail and freight vehicle sectors, specifically vehicle acceptance support, accident investigation and prevention and has led projects on behalf of the Health and Safety Executive, Rail Accident Investigation Branch and major metro system operators.
Paul leads the IRR's Centre for Innovation in Rail and works closely with the rail supply chain to promote new technologies within the rail sector. As a Co-Investigator for the £98M HEFCE RPIF funded UK Rail Research and Innovation Network (UKRRIN) Paul is leading the development of advanced experimental equipment to support a number of key research facilities to be built within the UKRRIN Centre of Excellence in Rolling Stock hosted within the IRR.
Paul has led and being involved in a number of EU-funded projects including DRAIL, INNOTRACK and DYNOTRAIN and PIVOT. He has a wide-ranging knowledge of the UK railway research funding landscape, having also bid for projects under Innovate UK, RSSB and RRUK-A funding calls. He resides on the NR data systems working group, the RIA VT-SIC Suppliers' Group, RSSBs Adhesion Research Group and Vehicle-Vehicle Systems Interface Committee, the Centre for Innovation in Rail's Steering Group and the IRR's Strategic Advisory Board. Paul has advised recent and current major projects including Crossrail, HS2 and LU's New Train for London programme.
Disclaimer: The views expressed here are those of the interviewee and do not necessarily represent the views of AZoM.com Limited (T/A) AZoNetwork, the owner and operator of this website. This disclaimer forms part of the Terms and Conditions of use of this website.