In the consumer electronics industry Line Confocal Imaging technology is explicitly designed for various applications.
Curved Edge Display Inspection
There are many challenges posed by curved edge display inspection with traditional imaging technologies. The profiles of mobile phone displays can be illustrated using Line Confocal Sensors on 2.5D or 3D curved glass.
Detecting Defects in Curved Edge Displays
It is possible to identify defects using a combination of 3D tomography and 2D intensity imaging. Such defects include delamination, scratches, or dust on the surface or inside of laminated glass, mobile phone displays, or other forms of transparent multi-layered material.
Unlike many other types of imaging systems, the location of the defect can be detected with Line Confocal Sensors as well as the layer that the defect is in. It is also possible to measure the dimensions of the defects at microscopic level.
Surface Angle in Curved Edge Display Inspection
The profile of curved screen glass can be illustrated with FocalSpec sensors at a surface angle of up to 20 degrees. If the surface angle is higher than this, either the sample or the sensor can be tilted or another FocalSpec sensor can be used to illustrate the sample.
Difficult materials, such as curved, transparent, or multi-layered surfaces can be inspected using 3D imaging with Line Confocal Sensors.
.jpg)
Partial enlargement of a defect on curved edge screen glass illustrated with the Line Confocal Sensor LCI1201
.jpg)
Mobile phone display layers illustrated with the Line Confocal Sensor LCI1201.
Component Assembly and Inspection
Quick and accurate component and final assembly inspection can be carried out using FocalSpec sensors for both inline and offline applications. Particularly when measuring complex materials and surfaces, Line Confocal Sensors exceed standard inspection methods.
The sensors can be used to measure component dimensions, orientation, step height, gap and offset, material thickness, and surface properties such as roughness and flatness. It is also possible to inspect soldering and gluing quality.
2D Intensity Imaging in Component Assembly and Inspection
3D topographic and 2D intensity imaging data can be collected with a Line Confocal Sensor simultaneously. The data corresponds to traditional microscopic data. Unlike with a microscope, millions of data points are automatically produced at once with an LCI Sensor. This facilitates a full inspection of electronic components and their assembly.
PCB Quality Inspection
In order to identify and take measurements of height, diameter, distances, profiles, orientation, and shapes of the selected elements, a scan was taken of a PCB with a LCI1201 sensor installed in 3D Line Confocal Scanner UULA. A comparison was then made between the data and known design 3D data to determine any potential deviations.
.jpg)
Contour analysis of a conductive track.
.jpg)
3D surface profile scan of an PCB board. The measurement place and direction is marked on the image.
Detection of Missing Objects
.jpg)
3D image of a BGA sample with a missing droplet.
A scan was taken of a BGA sample with droplets on the surface using a LCI1201. “Islands” functionality in FocalSpec Map was used to detect a single missing droplet.
Transparent Material Inspection
Transparent material inspection and quality control can be carried out with Line Confocal Sensors. It is possible to illustrate surfaces of mobile device displays and detect layers inside and under the screen glass.
.jpg)
Smartphone display layers illustrated as 2D grayscale intensity images. Separate display layers can be clearly visualized due to Line Confocal Sensor’s large depth of view.
All the surface layer 3D profiles in the tomographic images are detected through fast signal processing units embedded within the sensors. It is then possible to process the height information of each measured data point in calibrated micrometers. Finally, the intensity is calculated with high resolution (>12 bits) for every detected surface point.
.jpg)
Smartphone display layers visualized by using FocalSpec Line Confocal Sensor LCI1201 and CloudCompare, a 3D point cloud processing software.
Imaging and Measurement Options for Transparent Material Inspection
- 3D topography profile
- Surface roughness
- 3D tomography imaging
- 3D dimensions
- 2D grayscale intensity imaging
Printed and Flexible Electronics Inspection
Printed electronics can be efficiently measured through FocalSpec Line Confocal Imaging (LCI) technology using a combination of all 3D topography, tomography and 2D intensity imaging in one sensor.
The most appropriate sensor is chosen for the purpose which will vary the imaging speed and accuracy. Feedback is provided significantly quicker and much more accurately with the FocalSpec 3D Line Confocal Sensors compared to conventional methods. Quality control in roll-to-roll manufacturing of printed electronics can also be carried out using FocalSpec sensors.
.jpg)
3D image of printed patterns on transparent PET illustrated with LCI1600.
.jpg)
Sensors for Printed and Flexible Electronics Inspection
FocalSpec sensors can be utilized at various different stages of the printed electronics manufacturing process, starting from the substrate material development and manufacturing where a key measurement is that of surface roughness. All substrate materials can be detected with FocalSpec sensors whether they are shiny, glossy or transparent, for example glass or PET foil. Furthermore, defects, such as delamination, scratches, or impurities in coating and transparent substrates, can be identified with FocalSpec LCI sensors.
FocalSpec sensors provide quick and accurate 3D topography imaging whether it’s for screen-printing, inkjet printing or dispensing materials. They also provide step height and width measurement of the printed structures.
Cemented or glued components on transparent substrates are inspected using FocalSpec sensors in the hybrid electronics industry. Traditional 3D dimensional measurements can be taken but the sensors also allow for the study of air gaps, bubbles, and other types of delamination on or through the transparent substrate.
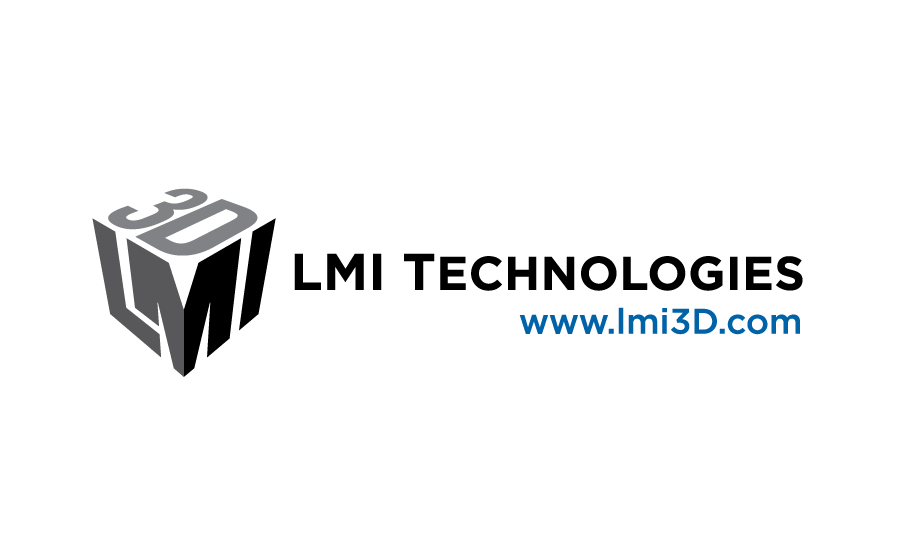
This information has been sourced, reviewed and adapted from materials provided by LMI Technologies.
For more information on this source, please visit www.lmi3d.com.