Laser measuring technology offers a number of advantages over other technologies. Installation is flexible and affordable, there is no need for echo mapping or on-site calibration, and lasers are able to detect virtually any liquids or solids.
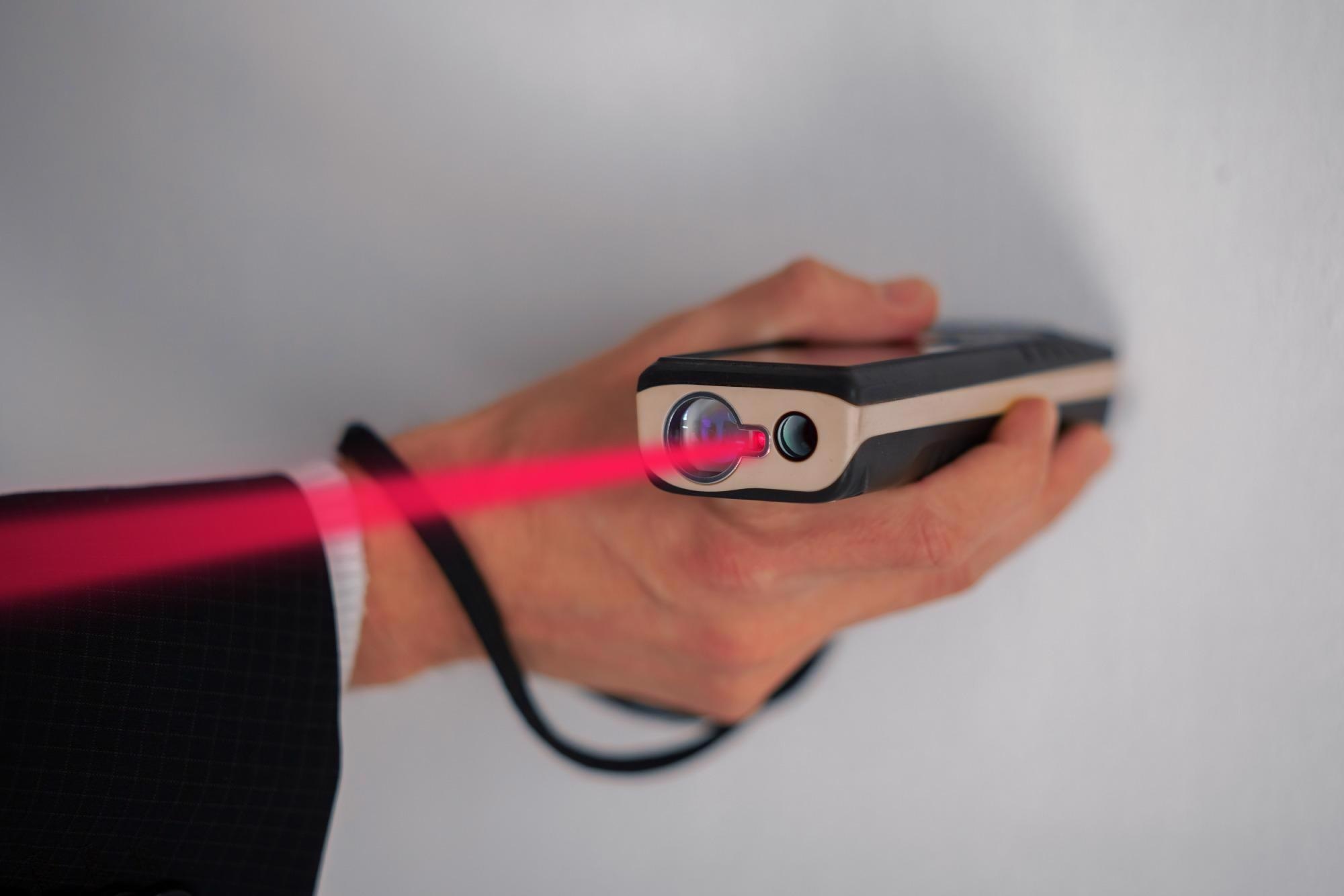
Image Credit: Shutterstock
ABB has been working with laser technology for more than ten years. The company offers a family of laser level transmitters, including the LLT100 - the latest addition to the product line, having been specifically developed for industrial applications.
ABB also offers the older LM80, primarily used in bulk solid applications, and the LM200, which is a version of the LM80 with larger lenses, allowing the instrument to measure at a much longer range.
Lasers have been used for measuring distances and ranges for some time, having become highly prominent in the industrial measurement and level measurement arenas. There are many ways to measure a distance with a laser beam.
Laser Level Measurement in Practice
Many industrial applications will use laser post time of flight. Here, short laser pulses are sent by the unit, traveling through space until they hit an object: a liquid or a solid surface. The pulses then bounce back toward the instrument into the sensor.
The sensor has a very narrow field of view, while the laser beam itself has a very low divergence of only 0.3 degrees. The picture also has a very narrow field of view, and the picture can be understood as like looking through a telescope – it only sees straight in front of itself, meaning that it only detects the first surface that it sees.
If there are other objects in front of the sensor; for example, a cloud, dust or even a grid, this will generate other spikes, but the last spike is always the final surface because the beam cannot bounce back everywhere - it simply travels in a straight line, and then back towards the unit.
Because the final target is the real target, there is no need to identify which pulse to track – everything is evaluated automatically and the correct result is obtained.
Lasers cannot measure an interface; for example, measuring something through the water. The laser will only detect the top of the water, but this feature is precisely why lasers are especially applicable to these types of level measurements.
A typical laser level measurement device like the LLT100 can measure liquids up to 100 ft (30 m) or solids up to 330 ft (100 m). For positioning applications that measuring the position of a moving object as opposed to a level, a reflective panel allows the instrument to reach up to 650 ft (200 m).
The instrument can operate between -40 °C and 55 °C. Its output is 4-20 mA with HART 7, meaning the instrument can be configured remotely. It can also be powered from the loop. Only 2” (5 cm) of aperture is required to perform the measurement, meaning the instrument is ideal for working within pipes etc. The LLT100 is a SIL2 device.
This technology means that the same instrument can be used for a number of applications – all that is required is for the process interface to be adjusted.
The base model works with a standard flat-faced flange, but higher pressure models are available bigger flanges that are rated for higher pressures; for example, class 150 pound or class 300 pound. Hygienic models are also available with a tri-clover clamp interface.
A range of accessories is available for ABB’s selection of laser level measurement instruments, allowing the devices to be deployed in an increasing number of challenging or specific environments. For example, an application in a grain silo may require additional protection to ensure the window remains free of dust.
If the window is too dusty, the laser beam will not be able to travel through it. A very typical accessory is the dust tube, which is a piece of tubing placed in front of the device facing upside-down. This passive device prevents dust from making its way inside and reaching the window without impacting the measurement in any way.
A purge ring is also available, which can be placed between the dust tube and the instrument. An application with, for instance, too much moisture forming from steam can be purged with dry air to further protect the window from condensation and/or dust.
Laser level measurement applications can be divided into three categories. The first is process control, whereby a level is measured to facilitate automation of a process.
For example, a rock crusher can be made more efficient by controlling the level of rocks inside the crusher. Live measurements mean that the speed of the conveyor belt can be automated, ensuring the optimum amount of rocks is present at any given time.
The second category is inventory monitoring, which, at its core, involves knowing how much of a material is available in order to manage it and know when to source more. This is perhaps the most common category of applications, with many applications either measuring solids, liquids, gases to maintain appropriate levels.
The third category is positioning and proximity detection. The laser beam can be fired at a moving object, allowing users to know where that object is at all times. For example, this type of application is commonly used with rail cars or tripper cars in factories that move over long ranges.
Installation Considerations
Laser level measurement technology can generally be installed with little or no modification required on the vessel or site. The laser device can be installed at any angle without any issue.
In vessels that use an agitator, it is possible to install the laser device between the side of the wall and the blade without impacting the performance of the narrow beam. The narrow beam also makes the laser level measurement ideally suited for unconventionally shaped vessels such as ‘v’ shapes.
If it is not possible to install the laser between the wall and the blade, advanced software functionality can be used to essentially block out the blade from any measurements. It is also possible to install the laser device while there are still materials in the silo – there is no need to empty the vessel.
The laser instrument can also be installed on a window if there is one present at the top of the vessel. The laser will then be able to perform measurements through the window. Laser level measurement’s ability to work at long range is ideal for applications where there is a risk of falling material, corrosive products, or other dangerous conditions.
Installing the device requires the user to enter a range of parameters such as vessel height, upper and lower limits. The process is relatively straightforward, even for novice users who may be unfamiliar with the technology.
Material Considerations
The laser level measurement device is able to work with many types of material, including solids, clear or dark liquids, mixtures, slurries. Reflections are reliable, even if the texture of the products changes. The LLT100, in particular, can also provide reliable measurement of transparent liquids.
If a process involves waves, turbulence, or agitation, advanced software functions are available that can smooth the signal, removing any spikes resulting from the waves and turbulence.
A key benefit of laser technology is that it can accommodate any dielectric, including a low dielectric. Because of this, the technology is widely used when measuring plastics or oil. Laser beams reflect off different types of materials with relative consistency.
Unlike other technologies, laser level measurement is also able to accurately measure the top of the foam. This is a common consideration in breweries, the pulp and paper industry, and the steel industry, where it is important to avoid overfill by measuring to the top of the foam.
Lasers are unable to measure interfaces, meaning that in these examples, the results returned would only be the top of the foam.
Where an application may necessitate measuring the liquid, it may be possible to use magnetostrictive products or differential pressure to measure the liquid, combining this with the laser to achieve a comprehensive solution.
This approach is useful if, for example, a user is looking to control the amount of de-foaming agents used in a tank, automating this measurement to better manage costs and avoid using more agents than is necessary.
Laser level measurement is widely used with ball valves. The device can be isolated from the process, allowing for easy installation and improving the safety of a wide range of processes.
Example Applications
Laser level measurement is suitable for use in virtually every industry across many applications. A number of key applications for each industry are outlined below.
Because lasers can work with low dielectric constants, laser level applications are common in the plastic industry, particularly in the manufacture of polypropylene, plastic objects, plastic pellets, nylon pellets and polymers.
Because the laser level instrument is not physically in contact with the products, it is ideal for plastics that may be melting or otherwise sticky. It is also common practice to measure plastic pellets in silos for inventory management purposes.
Laser level measurements are also ideal for better managing process control, and the laser is widely used in the mining industry for crusher applications. As well as the use of lasers to optimize conveyor belt speed already mentioned, the laser’s ability to work at a distance makes it ideal for use away from any falling materials, even if this involves a change in the angle of the materials.
In floating roof applications, it is useful to measure the position of the roof as this is moving up and down with the liquid level. Laser level measurement can be used for this, as well as being used to measure the angle of the roof in order to notify users of any potential collapse or related risk.
One key advantage of the laser in these applications is that it can be installed very close to the wall or on a support, allowing easy access to the device. This is especially important where multiple lasers are required.
Where multiple lasers are used, there is no interference between devices, meaning that one device does not pick up a signal from another if these are positioned appropriately. There is also no risk of false echoes – a common issue with floating roof applications.
Liquid storage tanks are used in a diverse arrange of industries, but because lasers are highly efficient when measuring different types of liquids, they can be used with solvents, acids, water, oil and many more liquids.
When working with corrosive or other dangerous liquids, users may opt to use a fused glass configuration and a bigger flange for a pressurized tank, if required. In this instance, users simply use a portal on the tank, set the beam perpendicular to the surface and begin measurements.
Wastewater processing sees a number of typical applications for laser level measurement. The device can measure solids, mud, liquids, and it is also ideal for biomass level monitoring because it is not affected by buildup on the wall due to its narrow beam.
When working with applications like sludge monitoring, where the solid-to-liquid ratio changes over time, laser level measurements are able to offer good reliability.
Deepwater wet wells often employ laser level measurements for wastewater and municipal water monitoring. Ultrasonic devices are popular and widely used in these applications, but the limits of this technology mean it is not ideal for extremely deep wells where laser level measurement is likely a better option due to its increased range.
Importantly, the laser beam is not affected by sewer gases, build up or other issues which may cause false echoes.
Positioning applications like the use of tripper cars in a large factory will see the cars moving on rails over a long-range. Position switches are traditionally used on the rail, but these mechanical devices are subjected to a lot of wear and tear.
In large factories which may have thousands of position switches, their ongoing maintenance and replacement will likely have significant cost and productivity implications.
Laser level measurement offers an alternative to this practice. Laser devices can simply target beam the moving target or the wall, measuring distance to track position. Reflective panels can also be used to increase the range and reliability of the measurement.
The LM200 offers a maximum range of 1300 ft (400 m), meaning that using reflecting panels, a single device can cover an extremely long range. This ensures that operators know where moving objects like tripper cars are at all times, improving safety and efficiency.
Summary
Laser technology offers unique advantages for a wide of industrial measurements. It is able to effectively measure all liquids, solids, and even solids at different angles.
Lasers perform non-contact measurements, meaning they are low maintenance. The unit does not touch the media being measured, increasing reliability because the laser is not affected by the material. There is no need for vessel mapping, which is unique for this technology, while the narrow beam offers many advantages.
Installation is simple and there is no need for expert-level understanding of the technology to interpret signals and set thresholds – the technology handles these aspects. Once the instrument is set for one vessel and the parameters are known, it is easy to repeat this process on any number of similar vessels.
These could even be pre-programmed before being installed on-site, removing any need for vessel-specific measurements, which can be difficult and dangerous.
Lasers do not need to be recalibrated and they do not shift over time. A base configuration can be set, then amended for specific vessels as required; for example, if a vessel is thinner than others on the site.
Overall, laser level measurement instruments like the LLT100 can be used in a substantial number of applications across all industries, and ABB offers accessories and custom solutions for virtually any application.
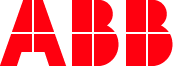
This information has been sourced, reviewed and adapted from materials provided by ABB Measurement & Analytics.
For more information on this source, please visit ABB Measurement & Analytics.