In Bulk Cryogenic Tank Level Monitoring, measuring instruments are used to determine the level of cryogenic liquified gases. Differential pressure is an easy and dependable method of monitoring the liquid level in cryogenic gas tanks. These sensors operate by measuring the pressure at the tank’s top and bottom and estimating the pressure difference between the two ends.
The subsequent value represents the cryogenic liquified gas pressure, which is then transformed into an accurate level value.
Oxygen is used to clean differential pressure transmitters, and pressure transmitters are broadly used in cryogenic gas tanks to monitor the liquid level and pipeline. Cleaning standards must be ASTM-93 and CGA 4.0 compliant.
Even though oxygen pressure measurement is quite sophisticated, Micro Sensor will concentrate on Oxygen pressure measurement solutions in this article.
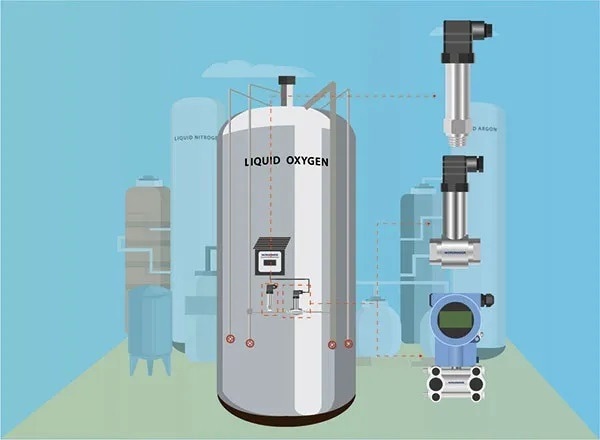
Image Credit: Micro Sensor Co., Ltd
The Smart Industrial Oxygen Production and Storage Monitoring Methods Users Need to Know
Oxygen is a common gas used in industrial processes like welding, gas welding, and gas cutting. The industrial oxygen production process involves liquefying air with equipment and storing the retrieved oxygen or liquid oxygen in a sealed tank that is easy to transport and use.
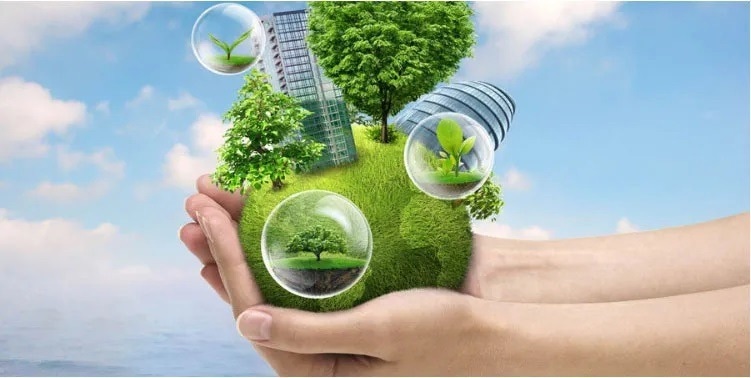
Image Credit: Micro Sensor Co., Ltd
From Production to Storage of Oxygen, There Are Many Steps That Matters
The oxygen extraction process appears simple, but there are numerous safety risks throughout the process, from preparation to transportation and storage. In the case of severe temperatures, open flames, or even friction and compression heating, risky accidents like explosions may occur if close monitoring is not conducted. Outlined below are some procedures that should be followed from industrial oxygen production to storage.
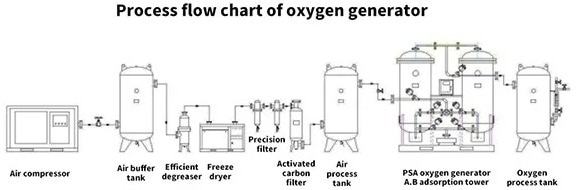
Image Credit: Micro Sensor Co., Ltd
How Should Oxygen Be Extracted?
The varied boiling points of oxygen and nitrogen are used to distinguish oxygen in the industrial production of oxygen. After purifying the air to remove contaminants, the air is liquefied under high-pressure and low-temperature conditions, and the temperature is constrained to evaporate liquid nitrogen.
Nitrogen will evaporate first, followed by light blue liquid oxygen with a greater boiling point, which can be retained under pressure in a cylinder for future use. As a result, in the process of producing oxygen, pressure is critical to the process’s achievement.
How Should Oxygen Be Transported?
The pipeline must be thoroughly cleaned of combustible residues like grease and soluble fat during the industrial oxygen transportation process. Alternatively, as a strong oxidizing agent, oxygen may heat up or explode when subjected to friction, compression heat, impact force, arc, resonance, and other conditions.
How Should Oxygen Be Stored?
No flammable items should be stored nearby, they should be at least 10 m away from open flames, and the storage environment temperature should be less than 30 °C. When storing liquid oxygen, the liquid level in the tank should never be less than 20%.
The underlying acetylene content must be analyzed within the time limit specified, and appropriate measures must be taken to correct the abnormal situation. The liquid inside the tank should not be left unused for an extended period. It must be packed and discharged regularly to avoid the accumulation of harmful impurities.
As per the oxygen production trilogy, it is obvious that industrial oxygen must be carefully monitored throughout the process, from production to storage, to avoid risks and ensure normal functioning.
Due to the properties of oxygen, its tracking must be more stringent. It not only has stringent requirements for measurement accuracy, but it also has criteria for the equipment’s material:
- The monitoring instrument have to use fluorinated oil, production procedure has to be grease prohibited.
- The monitoring instrument must be robust and easy to operate, maintain, calibrate and verify.
- The monitoring instrument has high accuracy, and the measurement data is stable and reliable.
Oxygen Tank Monitoring Requires the Use of Professional Instrument, and Micro Sensor Provides Professional Oxygen Monitoring Equipment
Oxygen pressure is typically measured using a monitoring instrument filled with inert oil. Micro Sensor offers a wide range of oxygen monitoring products. They are packed with fluorinated oil, which is specialized for oxygen measurement and has good precision, consistency, and protection.
These oxygen pressure measurement instruments are used in the manufacturing industry and can resolve the issue of measuring gas pressure in industrial oxygen storage tanks in a professional way.
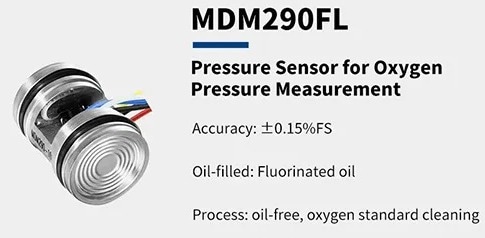
Image Credit: Micro Sensor Co., Ltd
Micro Sensor provides pressure sensors for oxygen pressure measurements, like the MDM290FL, MPM280FL, MPM281VCFL, and other series, in hazardous industrial settings. Designers also offer professional pressure transmitters that are specifically designed for oxygen tracking.
- CE/RoHS certified
- Range: 0~0.35 bar…35 bar
- Output: 2-wire 4 mA~20 mA DC; 3-wire 0V~5V DC
- Power supply: 15 V~28 V DC
- Temperature-compensated, steady and consistent
- Explosion-proof, intrinsic safe version
- The product can alter the zero point and full scale externally
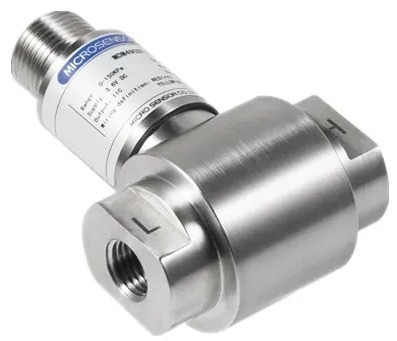
Image Credit: Micro Sensor Co., Ltd
MDM6861GFL Wireless Differential Pressure Transmitter:
- Several ports can be attached to monitor multiple scenes at the same time
- Battery-powered supply, long life span
- Online monitoring, PC and mobile terminal offered, easy for data query
- Wireless type, support remote monitoring
- Explosion-proof products, appropriate for explosion-proof places
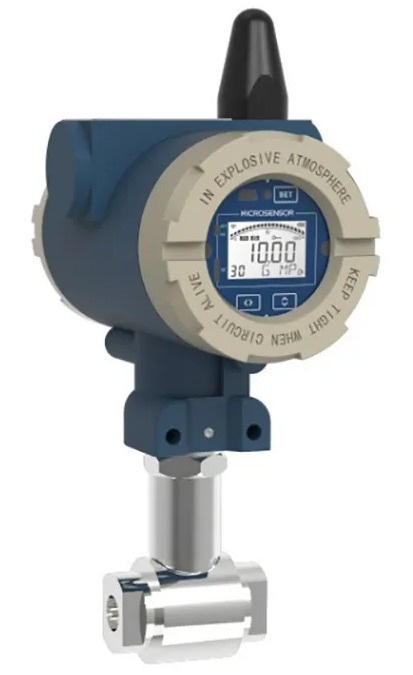
Image Credit: Micro Sensor Co., Ltd
MDM4902FL Differential Pressure Transmitter:
- Power supply: 3.3 V~5 V DC
- Wide temperature-compensated -10 ℃~70 ℃
- Range: 0~1.5 bar
- Output: Digital I2C
- Long-term steadiness
Micro Sensor is dedicated to the research and innovation of oxygen monitoring devices. It provides a set of highly qualified industrial oxygen tank storage monitoring solutions based on years of experience and uses stringent monitoring and accurate information to accompany the safe production of the industrial industry.
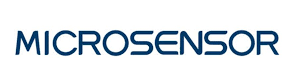
This information has been sourced, reviewed and adapted from materials provided by Micro Sensor Co., Ltd.
For more information on this source, please visit Micro Sensor Co., Ltd.