Despite being colorless, different colors (grey, blue, turquoise or green) are assigned to the hydrogen based on the way in which it is produced. The German government is focused in particular on green hydrogen - as a part of its national climate protection and hydrogen strategy for the future - which is produced in a climate-neutral way.
Grey hydrogen, however, is produced in a climate-damaging way and is currently the most widely produced. In this case, hydrogen is split off from a fossil hydrocarbon - natural gas - by means of steam reforming. The natural gas undergoes a reaction with steam, producing H2 and CO2.
In the event of a leakage, the CO2 will displace the oxygen in the ambient air, thus endangering human life. CO2 gas monitoring is therefore critical throughout this production process.
Properties and Effects of Carbon Dioxide
CO2 is extremely dangerous and can even be deadly in higher concentrations: The danger of poisoning begins at 0.5 % vol CO2, while a concentration of over 10 % vol can cause asphyxiation leading to fatality.
Since carbon dioxide is one of the colorless gases without any odor, the danger is usually only registered when it is too late.
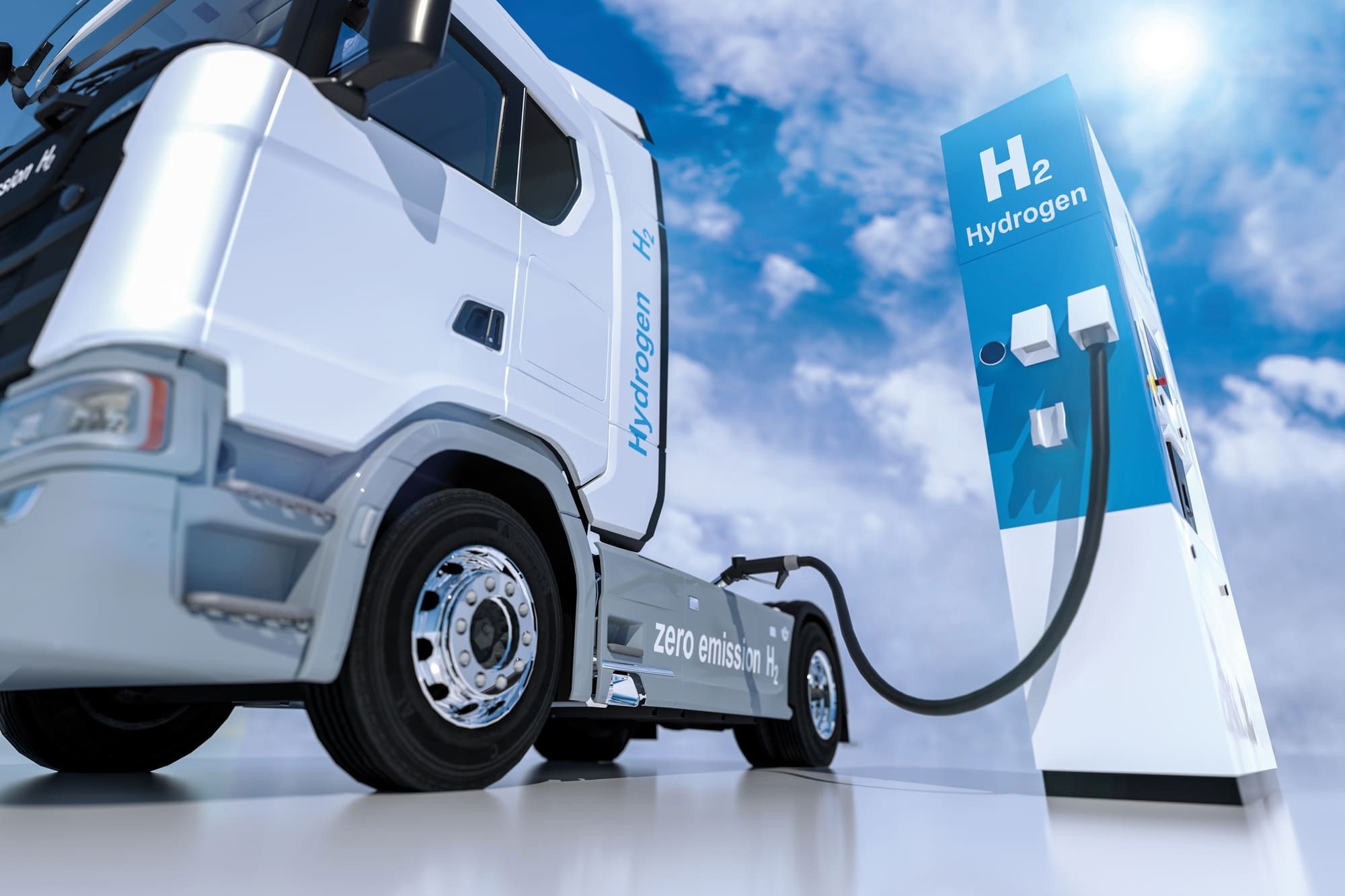
Image Credit: MSR-Electronic GmbH
During both the production and transportation of hydrogen, e.g., by ship, truck or pipeline, gas sensors and controllers from MSR-Electronic warn of the explosive gas; because H2 is highly inflammable - comparable to diesel or petrol - and impossible to detect by sight or smell alone.
The demand for an appropriately large H2 filling station network is increasing in parallel to the use of the energy source of the future. Not only do flow, temperature and pressure have to be monitored at hydrogen filling stations, but the detection of gas is also becoming a great necessity.
Solutions from MSR-Electronic for Reliable CO2 and H2 detection and for Monitoring O2 Deficiency.
MSR-Electronic utilizes several methods of gas detection. As a result, MSR develops individual gas sensors and controllers for a range of applications, such as underground garages, tunnels, laboratories, petrochemical plant and medical facilities, in addition to the waste disposal industry, wherever concentrations of combustible or toxic gas may form.
MSR Solutions for Fixed Gas Warning Systems
Measuring devices for gases protect people and facilities located in hazardous zones.
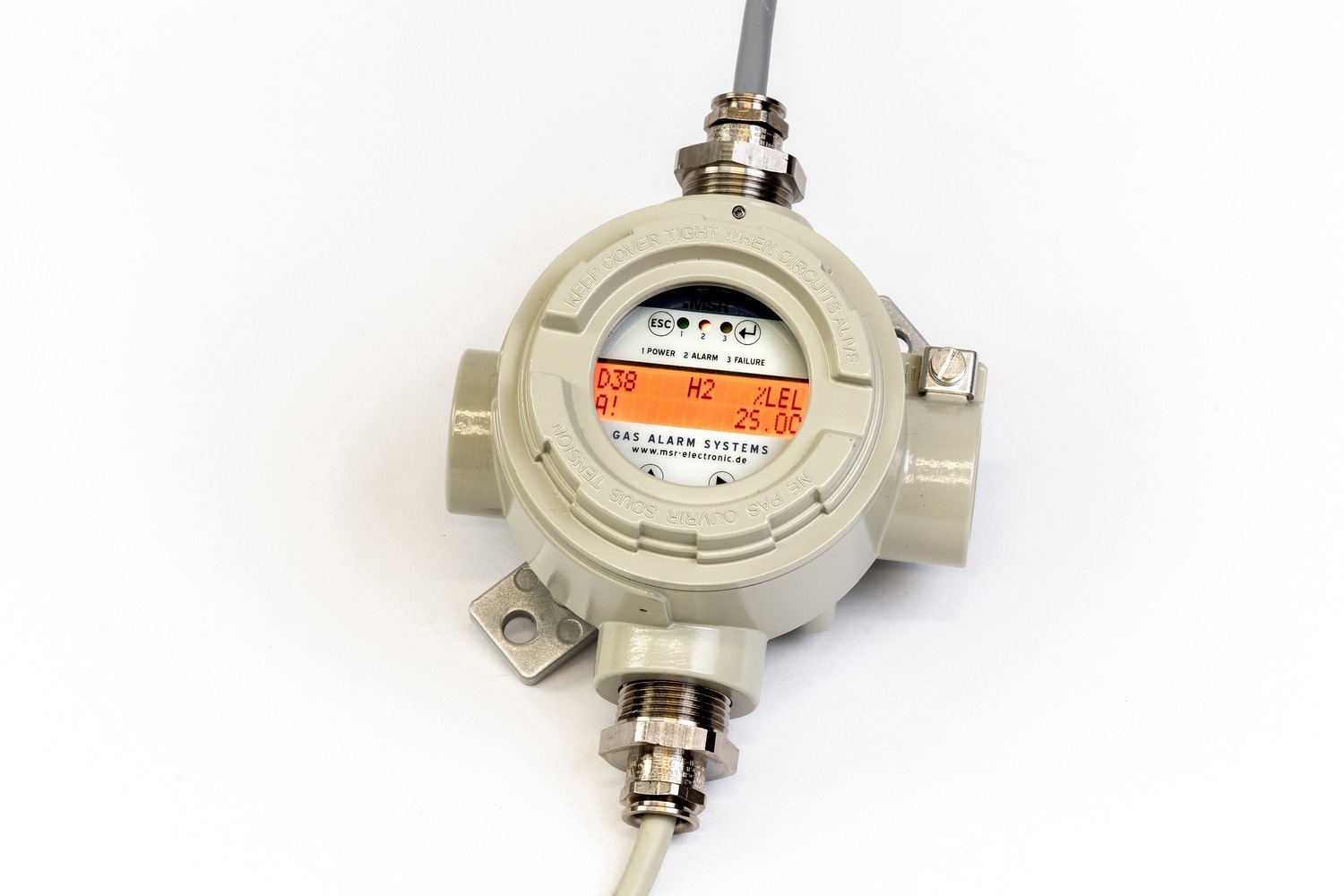
Image Credit: MSR-Electronic GmbH
The PolyXeta®2 PX2 is a microprocessor-based gas detector with 4-20 mA / RS-485 Modbus output signal, alarm and fault relay for monitoring the ambient air to detect toxic gases and oxygen concentration (O2) using an electrochemical sensor element. A catalytic sensor element is used to detect combustible vapors and gases (H2), and an infrared sensor element is used to detect carbon dioxide (CO2).
Sensors that do not have an LC display are calibrated using the handy calibration device STL06-PGX2 or the PC software PCE06-PGX2.
Sensors with LC display have a calibration routine - which can be done without opening the housing - integrated into the sensor that is started from the outside with a permanent magnet. Additionally, the background lighting changes to red from green in the event of an alarm or error.
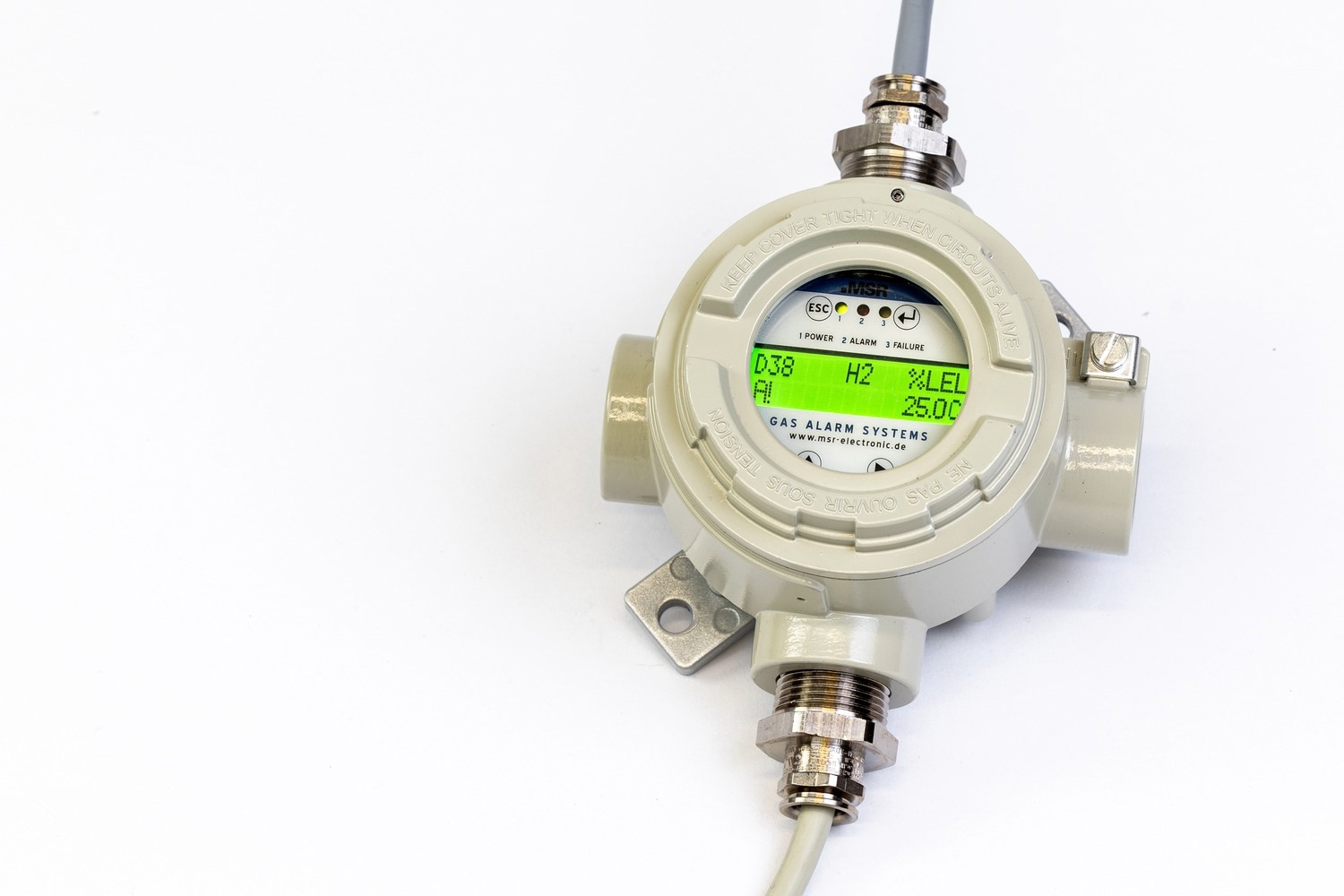
Image Credit: MSR-Electronic GmbH
Benefits
- ATEX 1/2 and IECEx certificates (for electrical Ex protection)
- Approved Measuring Function & SIL2 safety functions 4–20 mA, RS-485 and relays
- MED Certificate and TA Certificate: Approval according to Marine Equipment Directive 2014/90/EU by DNV
- For zone 1/2: Type “Ex db” protection flame-proof enclosure
- For zone 2: Type “Ex nR” protection
- Enclosure: Additional FM and CSA certificates for Class I, Div. 1
- Continuous self-monitoring
- Easy calibration
- Microprocessor with 12-bit converter resolution
- Calibration service by exchanging the sensor head
- Proportional 4–20 mA output
- Alarm and fault signal relays
- Serial interface to the control center
- Alarm and fault signal relays
- Reverse polarity protection and overload protection
- Option: LCD display with status LEDs (optional)
Thanks to the X-Change technology, calibration may be carried out simply by exchanging the sensor head (type SX1) or using the convenient, integrated calibration routine directly on the system.
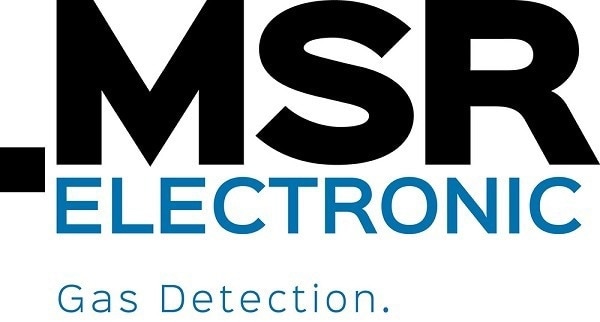
This information has been sourced, reviewed and adapted from materials provided by MSR-Electronic GmbH.
For more information on this source, please visit MSR-Electronic GmbH.