When winter storms resulted in hundreds of drivers being stranded and stuck on I-95 in Virginia for hours, some people raised concerns about what would have happened had the cars been electric vehicles (EV), given that EV batteries are known to be susceptible to temperature extremes.
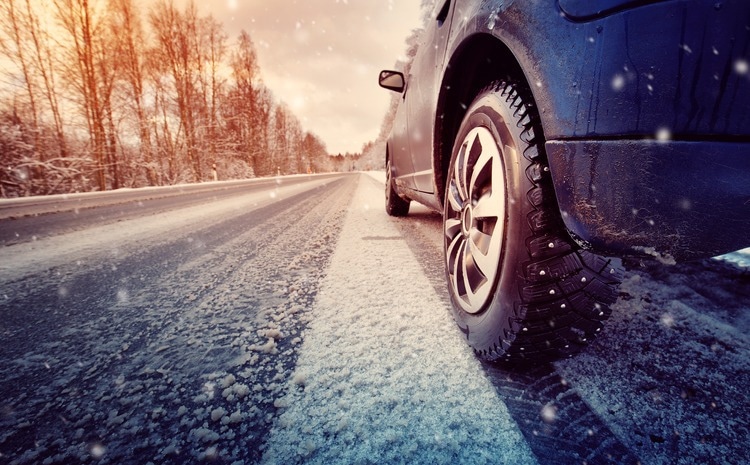
Image Credit: Amphenol Advanced Sensors
Alex Lauer put it to the test, sitting in a Ford Mustang Mach-E for 12 hours in temperatures ranging between 13 ℉ and 24 ℉.
After 12 hours of operating time with the vehicle’s HVAC system fully engaged for a comfortable temperature for the driver, the battery of his EV still had 75% remaining charge and a range of 132 miles, performing substantially better than its ICE counterparts under comparable conditions.
Despite the public view of EV performance in cold weather sometimes being pessimistic, the results of Lauer’s impromptu experiment should not be surprising. EVs are designed with efficiency in mind and are commonly performance tested at temperatures as low as -40 degrees Fahrenheit.
What makes this possible is the integration of sensor technology into the design of an EV.
One such contributor to improved battery efficiency is EV heat pumps. Regarded as a new tool for increased battery life, EV heat pumps are providing the alternate route for improved efficiency and range.
EV Heat Pumps: A Leap Forward for Comfort and Improved Battery Life
Heat pumps are relatively new to the world of EV design. A large number of major manufacturers have quickly embraced heat pumps as an alternative to resistive heaters.
Heat pumps are showing themselves to be an important addition to EVs, providing a new level of optimized power conservation. Heat pumps for climate control represent efficiency in action since they leverage the heat produced in the usual operation and use an EV’s existing systems for climate control.
The movement toward using heat pumps as a means of cabin climate control flips the model of heating used by internal combustion engine vehicles. The absence of waste heat created by combustion means that an EV must generate heat by other means.
Acting as an air conditioner working in reverse, a heat pump in an EV uses a system with two loops. The first loop has a cooling medium (coolant or refrigerant) moving around a component — the EV battery in this case — with tubing connected to a “cold plate” attached to the battery array.
Excess heat that is captured is then carried by the coolant pump into a liquid-to-liquid heat exchanger in the second loop.
In the second loop, heat is released by an evaporator and sent into the cabin to work as heating in cold weather. Furthermore, the refrigerant usually used to cool the cabin can be flowed in reverse through the use of new combinations of flow control and expansion valves, thus adding heat to the cabin in cold weather.
Heat pumps lead to improved and more efficient use of power, which increases battery life by reserving more power and extending range.
Instead of achieving passenger comfort by using the battery’s energy to generate new electric heat, an EV can conserve power or use it for other luxuries, such as heated steering wheels and seats.
EV Heat Pumps, Sensor Technology and Battery Life: A Closer Look
To use heat pumps effectively to increase battery life, the system uses refrigerant pressure and temperature sensors.
Both temperature and pressure sensors help control enthalpy (internal energy plus pressure and volume). This helps create a high coefficient of performance by using a minimum amount of energy to produce a maximum amount of heat exchange.
More specifically, temperature and pressure sensors assist the vehicle in regulating the thermal management system and, by extension, the cabin’s climate for heat with precise control.
A high level of precision is required when controlling pressure – and thereby the expansion and compression of cooling fluids – in a thermal management system.
It impacts how the elements of both loops, for instance, the expansion valves and the condenser, function in moving refrigerants in liquid and gas under various pressures through the system.
Compression of refrigerant gas releases heat into the environment from the refrigerant, with the expansion of the gas extracting energy from the environment in turn.
By controlling the location of the expansion or compression cycles and reversing the direction of flow, the same refrigerant and controls can provide both cooling and heating of the cabin within the same hardware.
The precision control requires the understanding of the temperature and pressure of this refrigerant in the system at various critical control points.
In heat pump systems, like those employed in Tesla’s Octovalve design, the precision controls driven by accurate sensing improve the range of the vehicle by more than 10% in cold weather as compared to the standard heating loop.
Additionally, these sensors help the vehicle manage how these elements are using power to achieve the required high coefficient of performance. It all results in improved efficiency when it comes to using available power to extend the battery’s life per charge and range.
While cold temperatures can reduce the driving range for some EVs by up to 40%, thermal management systems using heat pump technology and sensors can recover a significant amount of energy loss.
Sensor Technology for Enhanced EV Performance
Visit the EV/HEV Sensor Resource Hub to learn more:
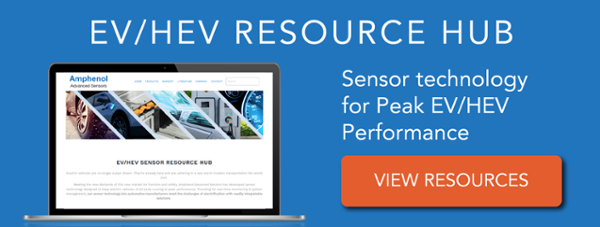
Image Credit: Amphenol Advanced Sensors
EV Heat Pumps For Getting More from Ev Batteries
EV cooling and heating systems are a far cry from those used in internal combustion engines and the stress it puts on the vehicle, but heat pumps and their required sensors are a key component in thermal management for improving performance.
Heat pumps do not eliminate the effect cold weather has on battery life; however, they do enable EVs to make better use of available energy than their internal combustion engine (ICE) counterparts.
Pair EV Heat Pumps with Robust Sensor Technology
Schedule a consultation with one of Amphenol Advanced Sensors’ engineers today.
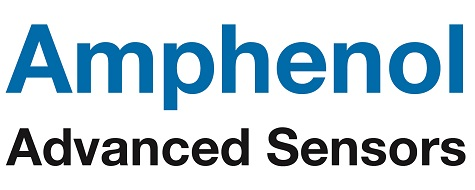
This information has been sourced, reviewed and adapted from materials provided by Amphenol Advanced Sensors.
For more information on this source, please visit Amphenol Advanced Sensors.