Sponsored by PolytecReviewed by Maria OsipovaJan 30 2023
MEMS pressure sensors are some of the first micro-electro-mechanical devices (MEMS) to be manufactured in series production, and they are now available in a variety of configurations (relative or absolute pressure measurement) for a wide range of applications, many of which are safety critical.
Pressure sensors are utilized in a wide range of applications, including diaphragms, medical and biomedical applications, diagnostic imaging, wearables, and more.
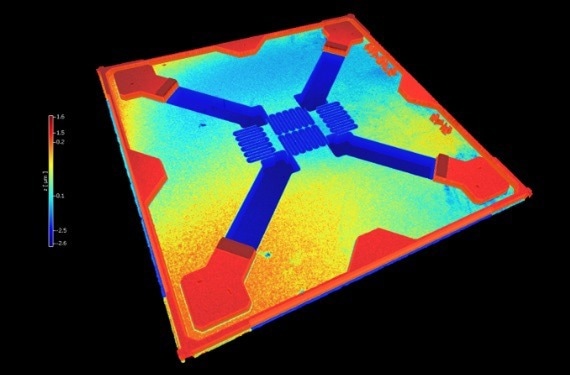
Image Credit: Polytec
How Do Pressure Sensors Work?
The fundamental working principle of MEMS pressure sensors lies in the conversion of physical load and pressure into an analog electrical signal. Pressure alteration causes the pressure sensor membrane to change shape, and the electrical voltage signal is proportional to the deflection of the membrane.
A thorough evaluation and characterization of MEMS pressure sensors are essential to guarantee the product's performance and quality, particularly in safety-critical applications. MEMS pressure sensors require non-contact optical testing techniques as a result of their size and sensitivity.
Measuring the 3D Topography of MEMS Pressure Sensors
Some pressure sensor performance parameters cannot be monitored electronically; therefore, the industry is dependent on alternative methods. One method is to determine the 3D topography of the thin and sensitive pressure sensor membrane, as well as the membrane thickness.
The TopMap series of white-light interferometers’ optical surface profilers accurately disclose form parameters and curvature of the pressure sensor membrane at varying applied pressures, preventing undesired stress and guaranteeing that the etching process works as intended.
Resistors on the pressure sensor membrane can also be evaluated to validate and optimize placement and attachment.
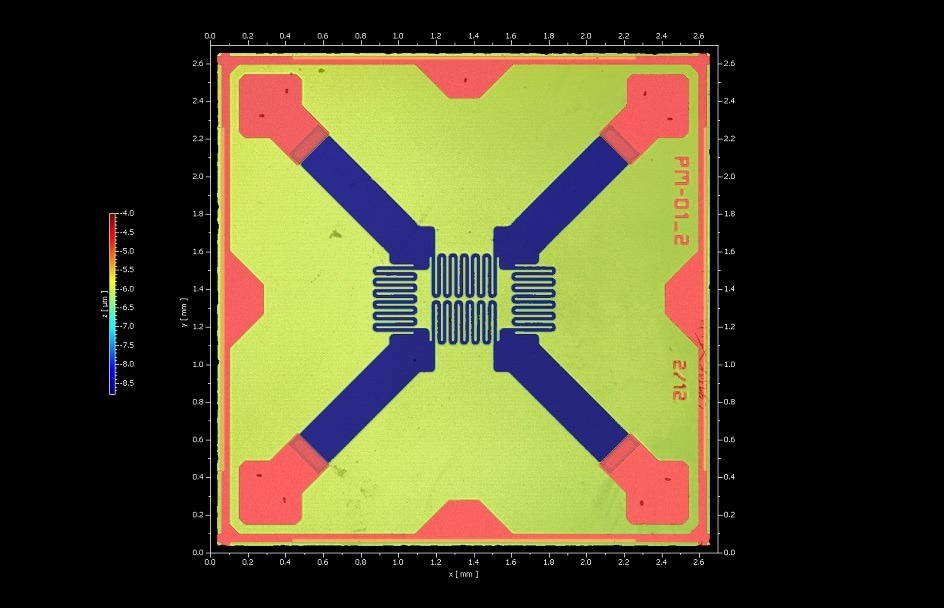
Areal surface profile of MEMS pressure sensor as 2D/3D profile. Image Credit: CiS Forschungsinstitut für Mikrosensorik GmbH
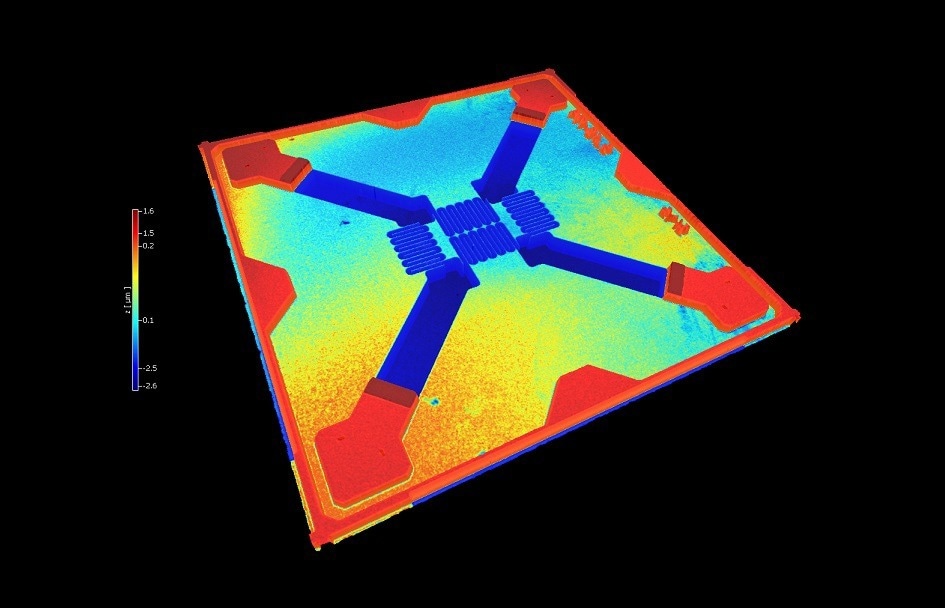
2D/3D profile of MEMS pressure sensor with 2.5x magnification and microscope measurement. Image Credit: CiS Forschungsinstitut für Mikrosensorik GmbH
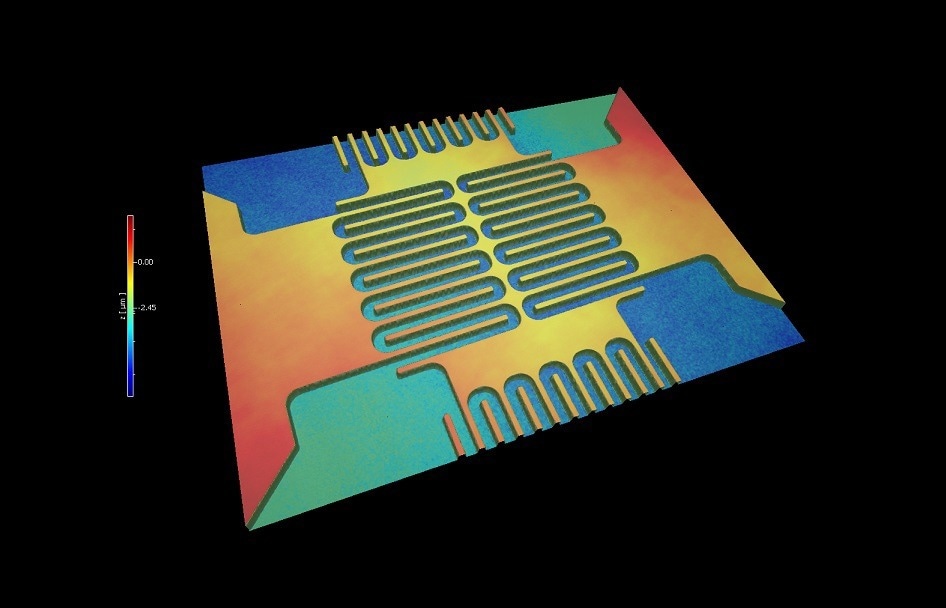
Close-up of MEMS pressure sensor for surface topography characterization. Image Credit: CiS Forschungsinstitut für Mikrosensorik GmbH
Testing Pressure Sensor Dynamics and Performance
Microscope-based laser Doppler vibrometry can precisely identify the resonance frequency and vibration amplitude of MEMS pressure sensor membranes. For each resonance, the operational deflection shape of the membrane can be compared against the predicted mode shapes of a finite elements (FE) simulation.
When vibrometer measurement data is combined with FE simulation data, the correlation enables the estimation of characteristics like boundary conditions, thickness, stiffness, and stress. Polytec optical testing solutions can measure the membrane thickness of a 300 nm thick pressure sensor membrane with an accuracy of less than 1%.
Wafer-level automation is highly beneficial when it comes to in-line quality control as it can detect faulty MEMS pressure sensor membrane units prior to packaging, which saves rejects and money.
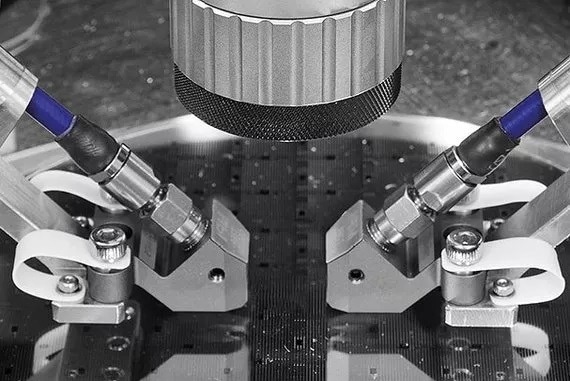
Probe-station integrated measurement for dynamic characterization of MEMS pressure sensors on wafer-level. Image Credit: Polytec
Membrane Thickness, Film and Layer Thickness Measurement
Layer and film thickness measurement | TopMap - optical 3D surface metrology
Video Credit: Polytec
Further Applications
Vertical Interconnect Access (VIA)
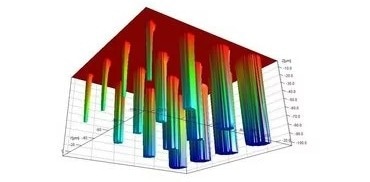
Image Credit: Polytec
Die Bonding
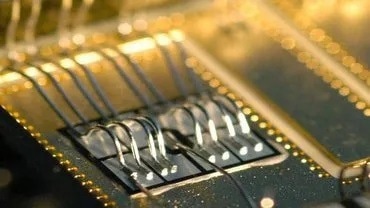
Image Credit: Polytec
Flexible Electronics
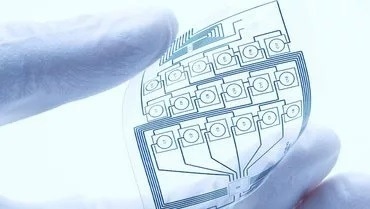
Image Credit: Polytec
Surface Roughness

Image Credit: Polytec
Layer Thickness
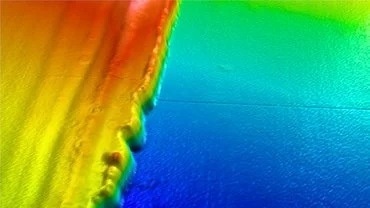
Image Credit: Polytec
<
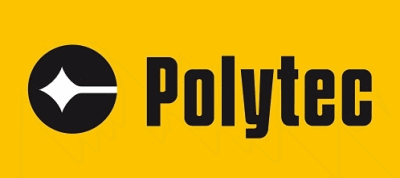
This information has been sourced, reviewed and adapted from materials provided by Polytec.
For more information on this source, please visit Polytec.