In this interview, AZoSensors speaks with Rob Podoloff, Tekscan’s CTO, and Roger Grace, President of Roger Grace Associates, a sensor marketing consultancy. They discuss printed sensing technology as an industry and market, as well as the history of printed force sensors and more technical questions.
Can you provide a brief introduction to your career path and current roles?
Rob Podoloff: I am Tekscan’s Chief Technology Officer and one of the founders of the company in the 1980s. I currently oversee Tekscan’s engineering and applications departments and maintain an active appointment with the Massachusetts Institute of Technology as a lecturer and lab instructor.
Roger Grace: I am the president of Roger Grace Associates, a sensor marketing consultancy with a particular focus on MEMS and printed electronics. I have written several technical papers, articles, and presentations on printed sensors. I am also a member of the editorial advisory board at Sensors Magazine and Commercial Manufacturing International and a co-founder and past president of the Micro and Nanotechnology Commercialization Education Foundation. I currently serve as its Vice President of the Americas.
Why is printed sensor technology important?
Roger Grace: In recent years, the wearables market has become very powerful because people need things that conform to their bodies. The materials on which these sensors are manufacturable can be either sheet-fed or continuously roll-processed. There are almost no limitations on the size of the material these sensors can be printed on. This provides the opportunity of making large sensor arrays since many future wearable electronic applications will be sensor array-oriented.
Moreover, these sensors can be manufactured on various substrates such as plastic and paper with a manufacturing cost much less than a silicon foundry producing an eight or twelve-inch silicon wafer.
This means that the barriers to entry in the printed sensor industry are significantly reduced, and many companies are capable of manufacturing these products, leading to a reduction in production costs.
What are the important functional elements of a printed sensor-based system?
Roger Grace: The front end is generally comprised of the sensor, and the sensor has a raw signal output, whether it be a printed sensor, printed circuit sensor, or silicon sensor. Signal conditioning electronics are used to amplify, filter, and process the signal. Typically, these functions are performed by an FPGA field programmable gate array or an application-specific integrated circuit.
The system also comprises power control electronics such as an energy harvesting device or a battery. A wireless Bluetooth is present at the back to provide a connection to the outside world. The system also consists of the packaging and the interconnects, which are the most difficult to manufacture parts.
Companies in the printed flexible sensing industry have to be very careful about these parts because they can make or break the product.
What are microelectromechanical systems (MEMS)? Are they being replaced with printed flexible sensors?
Roger Grace: Microelectromechanical systems (MEMS) have been the technology of choice for many sensor applications. In the early ‘60s, MEMS received significant attention because they are made of silicon and use processing techniques similar to logic circuits. However, they are being quickly replaced by printed flexible sensors.
This is because every product has a specific life cycle which consists of an introductory period, a growth period, a maturity period, and a decline period. At present, MEMS are peaking out at the top, and printed circuits are coming in.
The good news is that the industrial ecosystem and the supply chain sector are very mature for companies looking to invest in printed flexible sensor technology. The infrastructure is in place, and the ink and materials needed to print flexible sensors on paper or plastic are readily available. According to recent studies, printing a sensor on plastic or paper is 2 to 2.5 orders of magnitude less expensive than printing it on silicon.
What are some important applications of printed sensors?
Roger Grace: The wearables market is expanding greatly in many areas because the new wearable devices are becoming very sophisticated with advanced electrochemical printed sensors that can accurately measure biological functions.
These sensors can sense things like blood, urine, and perspiration to determine that a person is suffering from dehydration or any other physiological condition. These sensors also have potential applications in disposable items such as diapers for adults to measure whether the diaper has been soiled.
Thin Film, a European company with offices in California, has some very sophisticated package tracking that measures temperatures and humidity levels on critical materials like drugs using printed sensors.
Flex in San Jose is leading the charge regarding the production of printed sensor technologies and is helping many companies understand how to manufacture these products in high volumes.
When was Tekscan founded? What were its first products?
Rob Podoloff: Tekscan was originally founded in 1981. Interestingly, we were founded to solve a very specific problem. A dentist in the Boston area had gone to an adult education class and wondered whether or not a sensor technology could tell him how a patient’s teeth came together. He wound up getting in touch with me.
I was at the artificial intelligence lab at MIT at the time and had to give him the bad news that such a sensor did not exist. At this time, I started working on the printed sensors and made our very first sensors by hand painting inks onto etched flex substrates and trying to read them with the PDP-8 computers from Digital Equipment Corporation.
We made great progress after our initial investigations and came up with a suitable method of making the sensors. This method is based on screen printing the sensors, a very similar and basic concept that is often used for making silk-screened t-shirts and other ornamental things.
What are some common types of force sensors?
Rob Podoloff: One of the most common types of force sensors is load cells. These are typically mechanical packages used for an industrial setting and require calibration and relatively sophisticated electronics for reading the sensor data. These cells are either made up of a micromechanical system or a more traditional strain gauge, a resistive device that can measure the deformation of a surface and give an indication of the internal strain on the device.
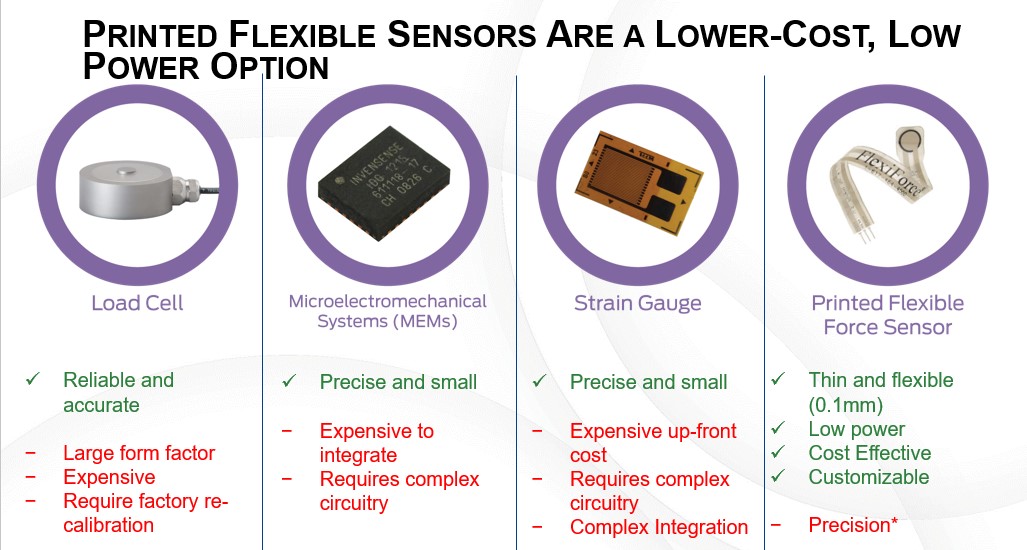
These force sensors are very precise devices but are often difficult to incorporate into a final solution. They either have to be mounted in a specific way or packaged in a certain fashion to protect the delicate instrument quality device.
On the other end of the spectrum is a printed flexible force sensor. It has many of the characteristics of the other sensors and can give an analog indication of the force on its surface. It uses low power and is flexible and easy to apply.
The downside is that the printed flexible force sensors are not very precise in some applications. However, these sensors are accurate enough for use in many industrial applications. These flexible sensors are referred to as FSRs, which stands for force sensing resistor.
The electrical characteristic that inherently changes when a force is applied to these sensors is their electrical resistance. There are two different constructions for the FSR. One is called a thru mode, while the other is called a shunt mode.
A shunt mode sensor essentially has sets of interdigitated fingers that are printed on the same side of a flexible substrate. The opposite side has a second flexible substrate coded with a pressure-sensitive material that comes down and shunts across the conductive fingers on the first layer. The resistance between the two conductive traces drops as the pressure-sensitive layer shunts. In a thru mode sensor, a sandwich configuration exists where there are silver conductors on each side of the sensor.
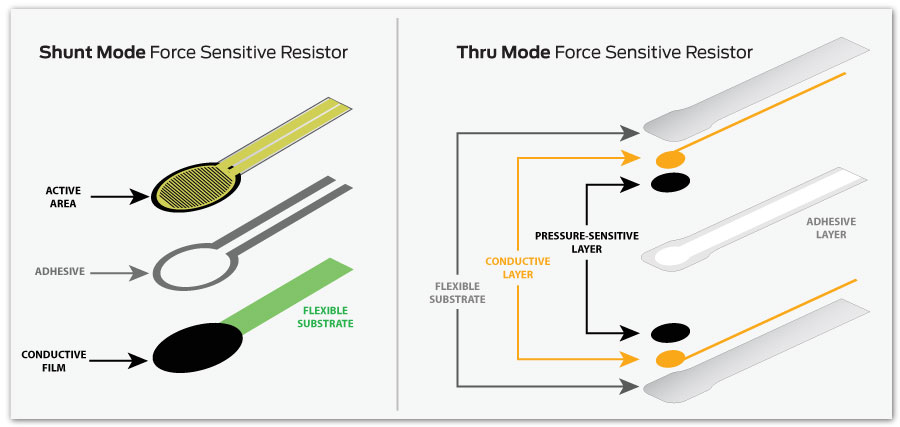
Different calibration techniques can improve the accuracy of these printed force sensors for specific applications. Moreover, these are thin, flexible devices printed on a plastic substrate, and yet they have tremendous durability for normal force-type loading.
These sensors can go from any millions of cycles with only a slight change in linearity over that range. In addition, depending on the material choices, these sensors can be made to withstand extreme temperature swings from below freezing to well over the boiling point of water.
How do printed force sensors measure force?
Rob Podoloff: The characteristics of these sensors can be tuned in many different ways. In addition to changing the sensing electronics, the composition of the inks can also be changed to adjust the ink sensitivity. Typically, these sensors are operated in the range of mega-ohms with no load applied to the tens of kilo-ohms at the rated load for the sensor.
The simplest way to read a resistor is through a voltage divider. However, the output from a voltage divider is far from linear. An inverting op-amp configuration can be used to overcome this limitation, where the sensor resistance is fed directly into the negative terminal of an op-amp.
With this kind of configuration, an output voltage is obtained that is directly proportional to the inverse of the sensor resistance. By adjusting that resistor, the sensitivity of the entire system can be changed.
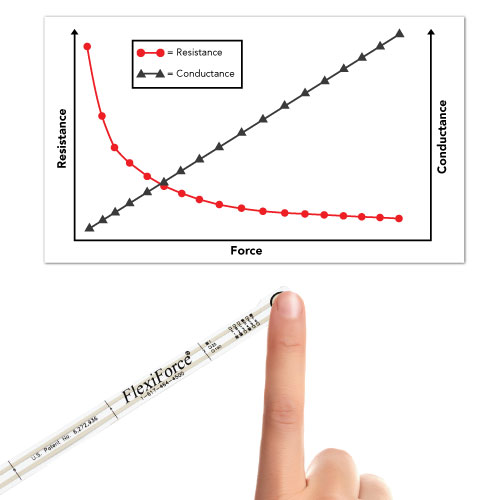
What are some use cases for Tekscan’s FlexiForce sensors?
Rob Podoloff: Tekscan’s FlexiForce can detect and measure relative changes in force or applied load. When a user pushes on the sensor, the LEDs on the indicator will illuminate higher up the scale, indicating a larger relative change in force. This type of measurement approach is useful in applications that monitor real-time changes in force, such as shifts in weight, position, expansion of components, grip forces, joystick controllers, and robotic manufacturing.
FlexiForce sensors can also be used to detect and measure a rate of change in force or applied load. This measurement approach is useful for applications that pair a four-sensing element with a timing mechanism. Some common examples include velocity control, manual therapy tools, and monitoring medication levels.
A wearable pump manufacturer needs to be able to detect whether or not there are blockages or occlusions in the medication delivery line. Tekscan’s FlexiForce sensors can be mounted where the tubing meets the housing, and if an increase or change in force over a specific period is detected, an alarm will trigger, indicating a potential occlusion to the user.
FlexiForce sensors can be used for the detection of contact and/or touch. The clamping mechanism opens or closes when contact with the sensor is detected. This approach is useful for monitoring soft bumps or hard impacts such as human or mechanical touches, window seals, and door latches.
If the printed sensor technology was introduced in the 1980s, why did it take so long for it to become widely accepted?
Rob Podoloff: It took time for the electronics and software to catch up to the fast-advancing printed sensor technology and for the intended audience to become used to that technology.
Roger Grace: Another reason for the delayed response to the printed sensor technology was the lack of information available. However, as time goes on and more and more studies become available, we are going to start to see a faster adoption rate for printed sensors and more of these products in the market.
Does the sensor respond differently to a point load than to a pressure load?
Rob Podoloff: Sensor response is dependent upon a few different metrics and whether it is a point load or a distributed load is one of them. For instance, if the point load is a true single point, there could be some localized heating within the sensor relative to the rest of the sensor’s printed area.
This can be minimized using a force concentrator, otherwise known as a puck. This spreads the load out and engages more of the active area even though a point load is being used. This also helps with repeatability and linearity and extends the lifespan of the sensor.
What physical property allows the FSR to return to the previous less conductive position, and how is that maintained over usage cycles?
Rob Podoloff: Three different mechanisms come into play when the sensor is pressed together. The first effect is called the surface contact effect. As previously mentioned, the construction of a thru-mode sensor is like a sandwich.
As the sensor is pressed, the peaks and valleys intersperse with each other, and as they get into more and more contact, the surface resistance between those two layers decreases.
Once that happens in a polymer matrix, and as that polymer matrix is squeezed, the conductive and semiconductive particles are brought closer together, reducing the resistance of the electrical resistance of the ink.
As the sensor is continuously pressed, an effect of the conductive and semiconductive particles is observed that resembles a piezo resistance behavior. These three effects combine to provide a large dynamic range of the sensor.
Can FlexiForce sensors be used in commercially available products? What are some key considerations when integrating FlexiForce sensors into any product?
Rob Podoloff: The simple answer is yes. Some of the overlooked elements that should be taken into account is properly characterizing the four-sensor before using it in any commercial device. One of the biggest hurdles encountered by our users is that they try to directly embed FlexiForce sensors into their prototype or proof-of-concept product.
Although FlexiForce does provide sensing data in this scenario, the client does not have a full understanding of the loading environment. This can cause an unforeseen output or a dynamic shift.
A better approach is to properly characterize the sensor in a controlled loading environment before embedding it into a prototype. We also provide users with a series of tools to investigate the performance of the sensors.
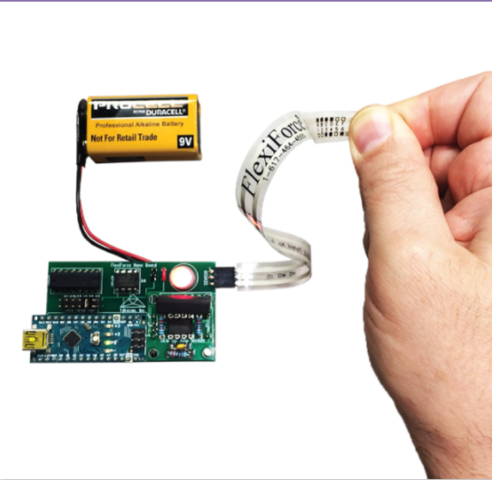
What is the average lifetime of the FlexiForce sensors? How does repetitive use affect their lifetime?
Rob Podoloff: Our FlexiForce sensors have been tested for up to 6 million actuations with very slight changes in linearity. It is important to note that the intended use of these sensors is in normal force conditions or perpendicular loading environments.
If the applied load is maintained perpendicular to the sensor and the environment is controlled or at least within the specifications of the sensor, only a slight increase in sensitivity over repetitive loading or repetitive actuations will be observed.
We have tested many different load conditions for the sensor, and as such, we have developed several techniques for protecting the sensor in various environmental conditions and for ensuring that sheer loads do not seriously damage the sensor.
About Rob Podoloff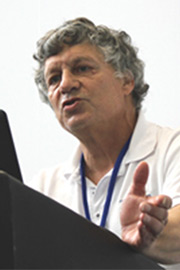
Rob Podoloff, Chief Technology Officer at Tekscan, was one of the original founders of the company in the 1980’s. Rob developed the printed, flexible sensor technology that today continues to be sought after by design engineers seeking a force sensitive embedded component that is flexible, accurate, and easy to integrate.
Listed inventor of over 20 US patents, and multiple patents worldwide, Rob currently oversees Tekscan’s engineering and applications teams and maintains an active appointment with the Massachusetts Institute of Technology as a lecturer and lab instructor.
About Roger Grace
Roger Grace has specialized in sensors for over 30 years with a focus on microelectromechanical systems (MEMS) and nanotechnology and is acknowledged internationally as one of the leaders and pioneers of this industry. While at Foxboro ICT, Mr. Grace was instrumental in helping create the disposable blood pressure transducer, currently one of the largest applications of MEMS devices at over 30 million units per year.
Currently President of Roger Grace Associates, a marketing consulting firm specializing in high technology, Mr. Grace also serves as a member of the editorial advisory board of Sensors Magazine, ECN, NASA Nano TechBriefs, and the R&D Magazine Micro/Nano Newsletter. He also serves on Northeastern University's School of Engineering Industrial Advisory Board, Nanomanufacturing Research Center and National Council.
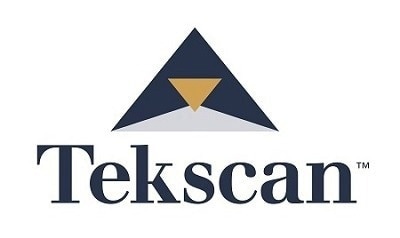
This information has been sourced, reviewed and adapted from materials provided by Tekscan, Inc.
For more information on this source, please visit Tekscan, Inc.
Disclaimer: The views expressed here are those of the interviewee and do not necessarily represent the views of AZoM.com Limited (T/A) AZoNetwork, the owner and operator of this website. This disclaimer forms part of the Terms and Conditions of use of this website.