The most commonly used Mobile Elevating Work Platforms (MEWPs) are self-propelled scissor lifts that utilize a scissor mechanism that moves vertically through folding supports in an ‘X’ pattern.
Their power source and usage environment determine two primary categories of scissor lifts. Battery-powered or electric scissor lifts are used indoors on slab surfaces. In contrast, engine-powered scissor lifts are best suited for outdoor environments with uneven surfaces, referred to as "rough terrain."
Regardless of the power source, scissor lifts have multiple sensors and controls to manage movement, safety, and stability. Ensuring the safety of operators on the platform is a top priority due to the risk of fall hazards.
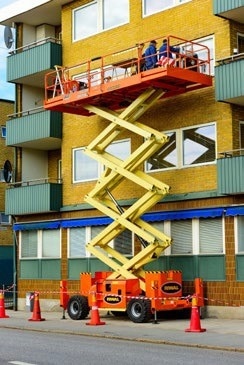
Rough Terrain (engine-powered) scissor lift. Image Credit: Sensata Technologies, Inc.
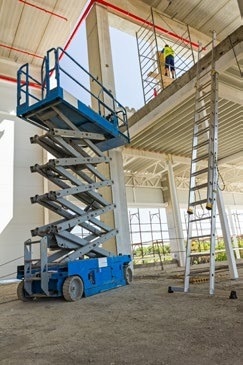
Slab (battery-powered) scissor lift. Image Credit: Sensata Technologies, Inc.
Solution
Operator Controls
Sensata has been a prominent supplier of complete platform control systems for battery and engine-powered scissor lifts for several decades.
The platform control unit and electronic control unit (or ground control unit for the engine-powered) can connect to and control various digital and analog machine interfaces, such as joysticks, sensors, limit switches, motor controllers, and push buttons and alarms, using a dedicated CAN-bus system.
The latest generation of scissor lift controllers, the K610, integrates an open-source platform, CoDeSys, which allows manufacturers to customize their functionality according to their needs.
Motor Controls
The M700 is a controller designed for high-power hydraulic pump motors, with the ability to program and control DC series wound motors. With microprocessor-based logic and programmable parameters, it allows for maximum flexibility at a minimum cost. Both the hardware and software are redundant, ensuring reliable operation.
Sensors
Sensata also offers a complete set of primary sensors, including the PTE series high-pressure sensor for hydraulic pressure control, the 9360 Series angle sensor for determining platform height, and the T series or other inclinometer for controlling chassis inclination for safety.
Combining the pressure and angle sensors also helps monitor platform overload conditions, an essential requirement for compliance with the ANSI 92 and EN280 safety standards.
Related Products
Table 1. Source: Sensata Technologies, Inc.
Reference on Diagram |
Product |
Features |
Function |
1 |
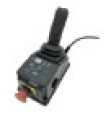 |
P610 |
- 3 Analog Inputs integrated
- IP65
- USB
|
Platform Control Unit |
2 |
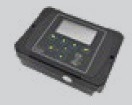 |
E610 |
- 2 CAN, 2 USB
- 40 input/output
- Multi-language,
- Large LCD
|
Electronic Control Unit |
3 |
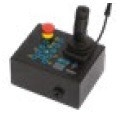 |
PCU100 |
- Extensive integrated controls
- IP65
|
Platform Control Unit |
5 |
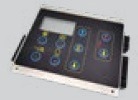 |
GCU120 |
|
Ground Control Unit |
6 |
 |
PTE7100 |
- High pressure
- MSG (Micro Silicon Strain Gauge)
|
Pressure Sensor |
7 |
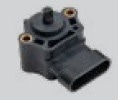 |
9360 Series |
|
Angle Sensor |
8 |
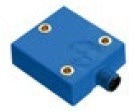 |
T Series |
- High resolution 0.01°
- High accuracy 0.1°
|
Inclinometer |
9 |
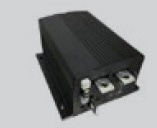 |
M700 |
- Pre-charge control
- Redundant design hardware and software
- Short duration boost capability
- Can communication with ECU
|
DC Motor Controller |
General Diagram
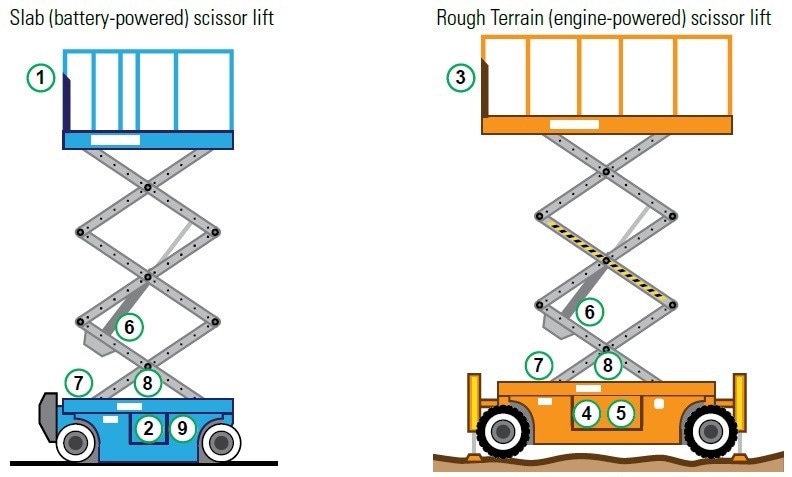
Image Credit: Sensata Technologies, Inc.

This information has been sourced, reviewed and adapted from materials provided by Sensata Technologies, Inc.
For more information on this source, please visit Sensata Technologies, Inc.