Fast-steering mirrors (FSMs) are extremely useful in various sectors, such as laser communication, astronomy, and military/defense applications. Motion control is a crucial element of these assemblies, requiring accurate positioning, a significant need for responsiveness, and minimal cogging.
In various design configurations, voice coil actuators offer the precise, reliable motor control required – along with smooth acceleration and close to zero hysteresis. The system accuracy limits are governed solely by the internal position sensor.
Voice Coil Actuator – Design Basics
At its core, a voice coil actuator contains a stationary coil assembly attached to a soft magnetic housing. The housing also provides a back iron for the magnetic circuit. The field assembly comprises an axially magnetized cylindrical magnet positioned between two soft magnetic pole pieces.
The coil assembly consists of several coils positioned in the circular cavities of the coil base, which is attached to the magnetic cylinder or housing. Commonly, the axial length of the magnetic cylinder is minimized for a given stroke, with other effects not considered.
When currents move through the coil, the flux in the airgap is altered, causing the coil to travel along its bearings. As temperature compensation is considered, the force becomes proportional to the coil current and flux density product. For the given current, flux density decides the applied force. This dynamic produces a very linear input signal.
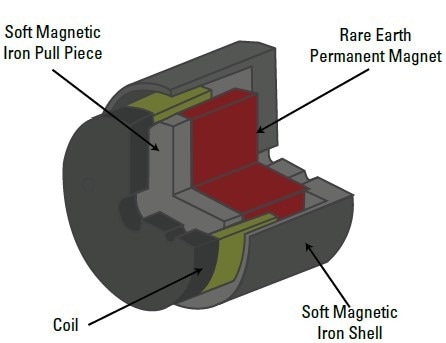
Image Credit: Sensata Technologies, Inc.
Due to this design – without teeth or commutated coils – there is also no force ripple or torque. The field is highly responsive, which means there are no hysteresis losses caused by relative movement between back iron and magnets. VCAs do not have a detent position, which means the actuator does not have a “preferred position” outside of any external forces without additional input.
VCAs also possess a high force-to-moving mass ratio, a key challenge in aerospace applications because each ounce of weight is crucial.
Vcas in Fast-Steering Mirrors
Every application is unique. However, most FSM designs comprise a mirror attached to a transient platform, typically manipulated by a feedback system. The feedback system measures the mirror's position and transfers control signals to the actuator to adjust its position.
FSMs aim to greatly reduce the delay between measuring the mirror’s position and correcting its orientation, enabling the mirror to accurately reflect light beams in the preferred direction. VCAs can effectively position the mirror in a variety of configurations. One of the more simple methods demands four actuators mounted to surround the support frame with a 90-degree separation. The opposing pairs of actuators function with a push-pull dynamic, which allows the mirror to offer an effective range of motion.
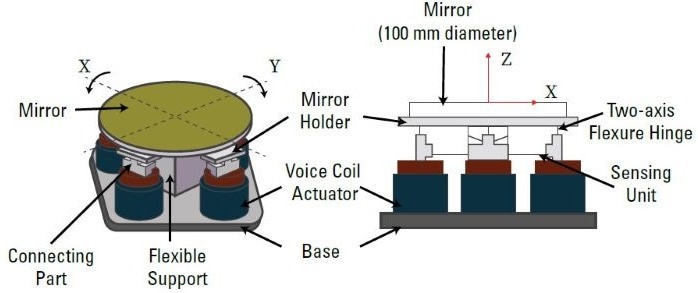
Image Credit: Sensata Technologies, Inc.
This design is not without flaws. The coils have current, which means that a field assembly is usually required to stop heat, which could cause distortion, from accessing the mirror. This field assembly adds some weight to the system. To enable motion from all four actuators, the air gap must also be increased to permit the appropriate clearance.
It is effective; however, the system does not permit a great deal of rotary motion (less than ±1 degree) and a relatively small amount of angular motion.
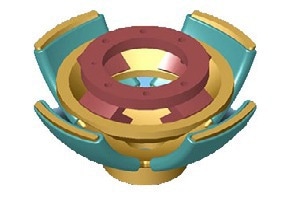
Image Credit: Sensata Technologies, Inc.
When the application is appropriately defined, a spherical voice coil actuator can offer the most desirable solution for FSM applications. This design contains four coils on a common frame, each located 90º from the other. When appropriately controlled, the coils can position a load at any point within the 15° x 15° angular envelope. It provides both roll and pitch motion in one device, offering an improved solution for larger angular strokes.
However, it is not optimal for every application due to the clearances and dimensions requiring close definition.
In some applications, deploying a pair of moving coil rotary voice coil actuators may be preferable. Each actuator can deliver strokes of up to 15° in either a clockwise or counter-clockwise direction, offering a further option to position the mirror.
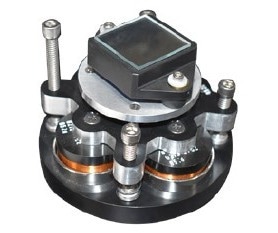
Image Credit: Sensata Technologies, Inc.
Conclusion
These options offer the same linear signal for position control and feedback. While non-linearities may create distortions in the reflected light beam (along with errors in control and measurement), they aid in ensuring that the mirror’s orientation accurately reflects the input signal.
In the example of FSMs, the input signal is the error between the actual and the desired mirror position. VCA design also enables high bandwidth, possibly managing several kilohertz for quick response times.
A range of voice coil actuator design options can effectively manage a rapid-steering mirror application—be it for targeting lasers, space applications, or other purposes. Engineers would benefit from evaluating each VCA option, considering their initial designs, to create the best solution for their finished product.

This information has been sourced, reviewed and adapted from materials provided by Sensata Technologies, Inc.
For more information on this source, please visit Sensata Technologies, Inc.