Accurate volume measurements are important in various industries and across an extensive range of applications. Different types of devices are available for this purpose, with each device having a specific purpose and a distinct level of accuracy associated with it.
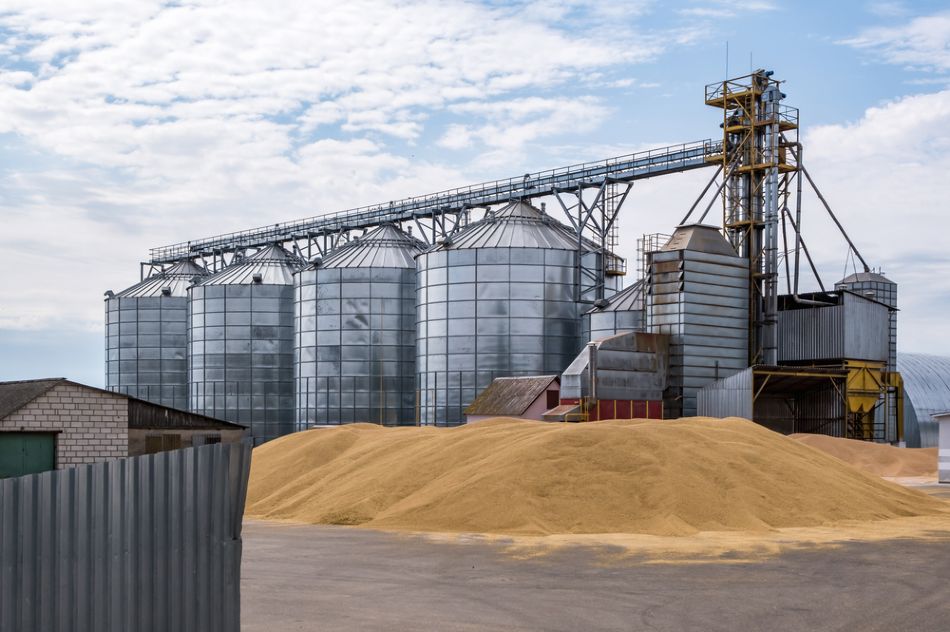
Image Credit: Shutterstock/hiv360
Case Study
A food processor requires highly precise volume measurements in order to determine the optimum time to refill the bin, since the bin is often emptied prior to filling again to prevent material damage.
The customer was looking for both stability and precision at batch empty rates of about one-half ton per minute, and was mainly interested in distance to the product from the top of the silo. However, the material in question is extremely dusty and is prone to sidewall accumulation and bridging, with the surface of the material being characterized by uneven topography during the emptying process.
Mapping and Visualization of Complex Material
.jpg)
Figure 1. 3DLevelScanner
.jpg)
Figure 2. Scanner mounted on existing flange, using an adapter plate.
Several vendors evaluated the 3DLevelScanner (Figure 1), a low frequency acoustics-based technology, against radar systems. The MV model of the 3DLevelScanner was positioned on a carbon steel silo containing granular rice. The silo is a center fill, center discharge configuration. Using the BinMaster adapter plate, the device was mounted on an existing flange and then positioned one-sixth in from the silo diameter (Figure 2). Although the internal bin environment was very dusty, the 3DLevelScanner was easily able to penetrate the dust.
The MV model of the 3DLevel-Scanner is capable of sampling multiple measurements within a 70 degree beam angle within the bin, unlike the single point measurement radar devices. Allowing the material to settle in the bin provided a more precise estimate of the bin volume, and visual mapping of the contents helped the customer to closely manage inventory and schedule refilling at an optimal time. In view of the success of the initial silo, 27 additional units were installed at the location.
Multipoint Measurements
.jpg)
Figure 3. Bridging is detected and mapped by 3D software.
When compared to a single point measurement device, sampling measurements from multiple points when the material surface of the bin is irregular provides a more accurate headroom measurement and bin volume. The 3DLev-elScanner MV model comes with a sophisticated mapping and visualization software (Figure 3), which is useful when utilized in material prone to sidewall buildup and bridging, and where there are points in the bin that are higher or lower than the majority of the bin contents.
In addition, when multiple point measurement is utilized, volume measurement after a fill or empty cycle will also be more precise. However, if a single measurement is used, bin volume estimates may be considerably lower or higher than the actual volume.
MVL 3D Level Sensor System for Inventory Management — BinMaster
Selecting Continuous Level Sensors
BinMaster offers a range of level measurement systems that can be used for various applications. These include SmartBob, GWR-1000 Guided Wave Radar Level, SmartWave Open Air Radar Level, SmartSonic Level, and 3DLevelScanner Level systems. However, these systems have certain disadvantages, which must be weighed carefully before using them for specific applications.
SmartBob Weight and Cable Level
.jpg)
Figure 4. SmartBob
Advantages of SmartBob |
Disadvantages of SmartBob |
Unaffected by material buildup on sensor |
On-demand system, does not offer a fast response to change in the material level |
Unaffected by dust or other adverse process conditions |
Seasonal maintenance may be needed to clean out mechanical cavity in extremely dusty conditions, if air-purge is not used |
Unaffected by material characteristics such as low dielectric constant or angle of repose |
Not recommended in high pressure bins |
Can be utilized in extremely light, signal-absorbing materials |
|
Measures bins up to 180 feet (SmartBob-TS1 up to 60 feet) |
|
Remote sensor requires no calibration |
|
Consistent, repeatable, and accurate measurements |
|
Minimal contact with stored material |
|
Very simple setup and installation |
|
High temperature models available up to 1000°F |
|
Low cost |
|
Advanced eBob networkable PC software available |
|
A variety of digital and analog outputs available |
|
Cable replacing, wireless interfaces available |
|
Hazardous location approvals available |
|
GWR-1000 Guided Wave Radar Level
.jpg)
Figure 5. GWR-1000 Guided Wave Radar Level
Advantages of GWR-1000 Guided Wave Radar Level |
Disadvantages of GWR-1000 Guided Wave Radar Level |
Performs in vessels prone to humidity, temperature, dust, pressure, and bulk density changes |
Sensing probe is in constant contact with material |
Continuous level measurement in liquids, powders, granules, and bulk solids |
Minimum dielectric constant of material must be above 2.2 |
Can be used on high pressure vessels (232psi max.) |
Maximum range is limited to 78 feet, and may be limited for heavier materials due to tensile load |
Suitable for vessels of any shape or diameter, including narrow tanks |
Material like large rock may damage probe and be difficult to sense |
Accuracy of ± 0.2 inches (5mm) |
|
High temperature range up to 392°F |
|
Microwave energy is focused and travels along a wave guide, focusing the radar beam within a small diameter |
|
SmartWave Open Air Radar Level
.jpg)
Figure 6. SmartWave Open Air Radar Level
Advantages of SmartWave Open Air Radar Level |
Disadvantages of SmartWave Open Air Radar Level |
Non-intrusive, non-contact design |
Low dielectric products are difficult to measure. Not enough radar energy can be reflected from the product surface. Requires a minimum dielectric constant of 2.0 |
Continuous level measurement |
Cone-bottom vessels can sometimes be problematic when nearing empty. The cone acts as an excellent reflector, throwing energy around the vessel someimes confusing the transmitter |
High temperature applications up to 350°F |
High purchase cost |
Ranges up to 100 feet |
|
In liquid applications, radar is not adversely affected by steam or foam |
|
Measurement is virtually unaffected by changes in process temperature, pressure, density or gas/vapor composition within the vessel |
|
SmartSonic Level
.jpg)
Figure 7. SmartSonic Level
Advantages of SmartSonic Level |
Disadvantages of SmartSonic Level |
Non-intrusive, non-contact design |
Performance affected by dusty conditions, pressure fluctuations, turbulence in vessel, and large particulate size |
Continuous level measurement |
Not recommended if steam will be present in vessel |
High temperature applications up to 260°F |
Will measure the surface of the foam, if present |
Ranges up to 90 feet (liquids) |
Maximum pressure of 29psi |
Sanitary models are available with tri-clover fittings |
|
Self-cleaning transducer face |
|
Low purchase cost |
|
Analog and digital communication options |
|
Automatic compensation for temperature changes |
|
Easy to install and calibrate |
|
PC software used to diagnose and calibrate sensor is free with purchase of SmartSonic unit |
|
Available in multiple voltages |
|
3DLevelScanner Level
.jpg)
Figure 8. 3DLevelScanner Level
Advantages of 3DLevelScanner Level |
Disadvantages of 3DLevelScanner Level |
Non-intrusive, non-contact design |
Since 3DLevelScanner is an acoustic device, elevated background noise can have an affect on its performance |
Continuous level measurement |
Time required to process multiple pulse echoes limits the sample rate |
Measures uneven powder or solid material surfaces |
Setup requires care in mounting the sensor in the proper location, and mapping the vessel |
Provides minimum, maximum and average distances |
Corrugation on small vessels can cause false echoes |
Detects cone up, cone down and sidewall buildup |
Not recommended for liquid applications |
Performs in extreme levels of dust |
Not recommended for materials with a bulk density under 11 lb./cu. ft. due to absorbing the acoustic pulse |
Calculates highly accurate bin volume due to mapping the surface of the material with multiple measuring points |
|
Measuring range up to 200 feet |
|
Self-cleaning with minimal maintenance |
|
High temperature applications up to 365°F |
|
Automatic compensation for temperature changes |
|
Analog and digital communication options |
|
Can generate a 3D image of material surface |
|
Advanced 3D MultiVision networkable PC software available for multiple vessel monitoring |
|
Cable-replacing, wireless interfaces available |
|
Approved for hazardous locations |
|
Unaffected by material characteristics or low dielectric constants |
|
Conclusion
BinMaster’s advanced level measurement systems provide highly accurate volume measurements and allow mapping and visualization of complex materials in food processing applications.

This information has been sourced, reviewed and adapted from materials provided by BinMaster.
For more information on this source, please visit BinMaster.