The term “Robot” creates thoughts of futuristic yet clunky droids such as Star Wars or C-3PO, or maybe the less exciting industrial robots used in car production lines – big metallic motorized arms. However, the robots of the future may be quite different.
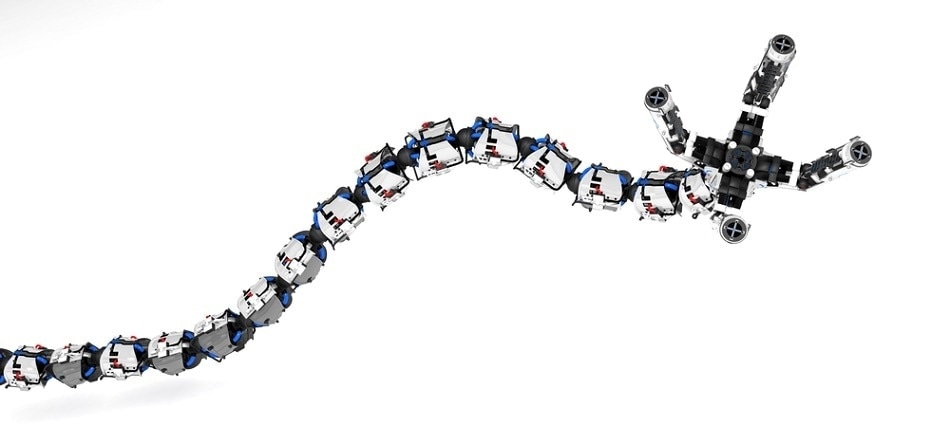
Shutterstock | higyou
Soft robotics refers to a multidisciplinary field incorporating mechanical engineering, chemistry, materials science, and biology. Dr. Rebecca Kramer, of Purdue University, is one of the leading researchers in soft robotics. She was named in Forbes’ 30 under 30, and has also received the NSF CAREER award including a number of other accolades.
As advanced as modern machines are, the building blocks that we use to create them have changed very little since the Industrial Revolution. The structures that we use in them, such as motors and gears, are typically rigid, bulky and heavy.
Dr. Rebecca Kramer, Purdue University
In contrast, Dr. Kramer’s lab is producing sensors suitable for use in “soft” robots that are responsive, conductive, and flexible.
The Science of Soft Robotics
The science of soft robotics is still in its early stages. Currently, Dr. Kramer’s work is focused on stretchable and flexible sensors, manufacturing with soft materials, soft-bodied control, and responsive material actuators.
“In order to begin considering robots as material systems rather than mechanical assemblies, we must consider biological inspiration.” Dr. Kramer works with a number of collaborators in the materials science, chemical and biological fields.
I am collaborating with a colleague in chemistry to explore tuned interfacial interactions to control liquid-metal nanoparticle self-assembly during evaporation for drop-on-demand thin film devices. While this effort may find many end-uses, my primary interest is in producing a scalable manufacturing process for thin film sensory skins.
Dr. Rebecca Kramer, Purdue University
The Development of Sensory Skins
The novel sensors from Dr. Kramer focus on replacing the visual sensors that are currently used for soft robotics. Visual sensors need direct line-of-sight, while her team recommends the sensors to be worn in motion capture clothing and provide 3D data related to motion and movement.
The sensing and power transport of soft machines is carried out by deformable soft electronics. Dr. Kramer’s lab develops both capacitive and resistive sensors. “Currently, our resistive sensors are based on liquid-metals embedded in elastomer films, and our capacitive sensors are based on graphene-elastomer composite electrodes and silicone dielectric films.”
Such systems are capable of functioning as highly stretchable electrical wiring or sensors that transform electrical resistance in response to deformation.
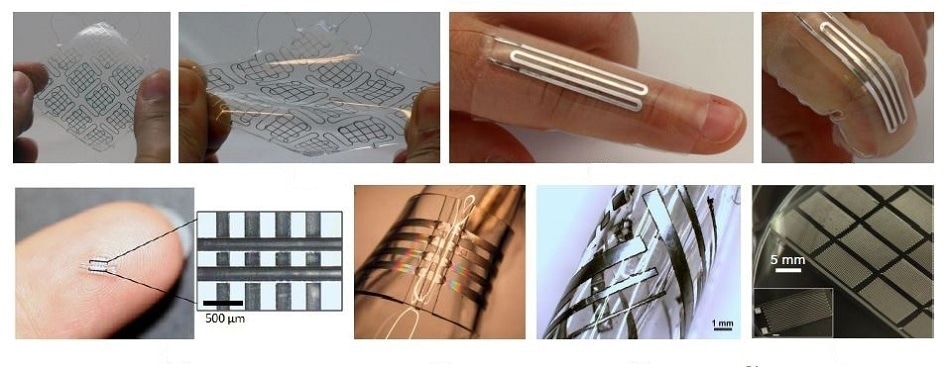
Examples of the soft sensors that Dr. Kramer's laboratory have developed. The sensors consist of elastomers embedded with liquid metal
Barriers to Scaling the Technology
Currently, methods borrowed from lithography and molding are being used to fabricate most soft robotic devices one-at-a-time. This limits the maximum size of features that can be fabricated and also hampers batch production, which is critical for increased implementation of soft robotic systems.
Dr. Kramer’s group addresses this issue by analyzing a number of complementary approaches ideal for processing conductive composites and liquid metals in their liquid form, such as controlled wetting, drop-on-demand (ink-jet) printing, and direct writing.
Developing the processes was one challenging task. However, a much different challenge faced by the team existed in validating the viability and success of these approaches.
“We were looking to acquire a multifunctional tool that could characterize both surface morphology and interfacial interactions,” she said. Dr. Kramer wanted to define a liquid from every angle.
A characterization instrument is yet to be discovered in the market that could meet the requirements of Dr. Kramer’s research. However, one instrument did come close but all it needed was a Kramer-specific modification.
Looking Under a Liquid
Dr. Kramer’s group needed a tool to help characterize a surface from various angles, without moving the sample. Most microscopists would generally tilt a sample, but the liquid application would require the instrument to be tilted, which is a challenging task with bulky, large instrumentation tools.
Kramer examined more than a dozen different characterization methods, including three-dimensional optical profilers, conventional profilometery, and confocal microscopy, but all of these methods failed to meet the requirements of the project.
The Zeta-20 Optical Profiler was one instrument that delivered excellent performance but only from one angle. “All of the hardware was there, it just needed to be rotated.”
Looking above, sideways and under a liquid sample is harder than it sounds. When Rebecca told us what she was trying to do – that she wanted to be able to rotate the microscope to capture contact angles of liquids on surfaces – we knew we had a challenge on our hands.
Ben Garland, KLA
The standard Zeta-20 Optical Profiler will have to be altered in order to meet the requirements of Kramer’s team. However, Kramer’s start-up professor’s budget did not allow an exorbitant custom price.
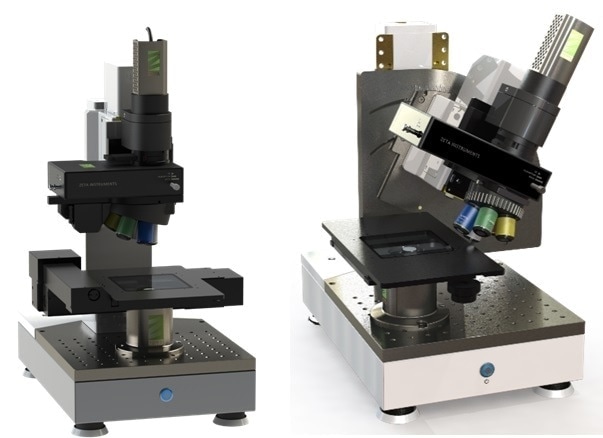
Left: KLA's Zeta-20 3D Optical Profiler; Right: The modified Zeta-20, with tilt-head, originally built for Dr. Rebecca Kramer’s Faboratory at Purdue University, and now a standard option available to customers.
Hardware Flexibility, Without Customization Costs
“Every KLA characterization tool is built to a customer’s exact order right here in our factory in California,” says Vamsi V, Marketing Director for KLA. “Since we’re not a cookie-cutter, one-tool-fits-all shop, we can provide customization for our customers at a very minimal cost.”
The modified swivel-head Zeta-20 was developed by the KLA team without any additional delays or special fees for custom work. Kramer’s Zeta-20 has a 0-90° swivel-tilt mounted head, which takes measurements from a top view of the line traces all of the way to the side, with quantifiable measurements.
Kramer was satisfied with the final product. “We use the Zeta-20 Optical Profiler daily for measurements and quality control.” she says.
The new instrument was able to meet both the technical qualifications and budget requirements. “The Zeta-20 Optical Profiler was the best value of all of the microscopes I evaluated for my research. The level of performance as a function of cost is truly optimized. When I was first starting my lab on a tight start-up budget, balancing performance and cost were important to me.”
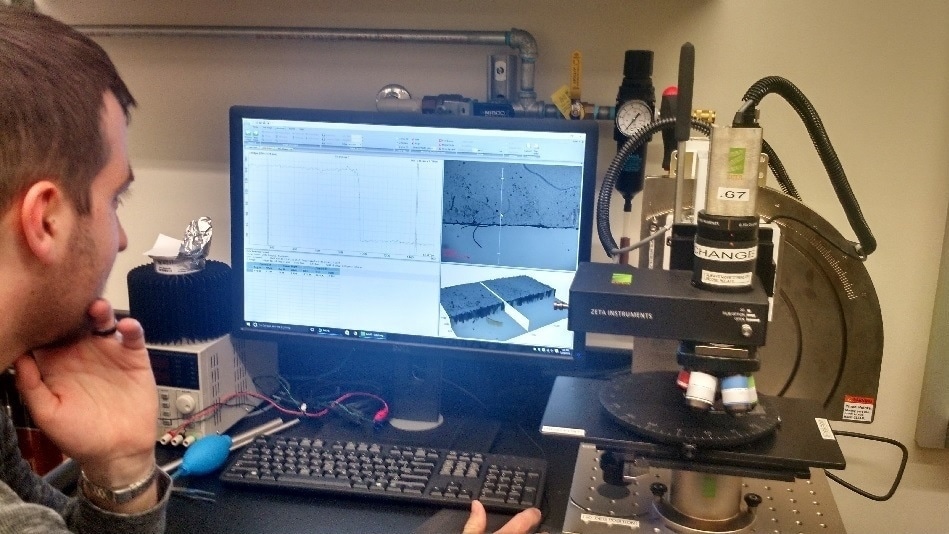
The Zeta-20 Optical Profiler in use at Dr. Kramer's 'Faboratory'
Conclusion
The work in the laboratory now continues, and testing is carried out for new and different materials. In the future, instead of a smart watch logging an individual’s steps, sensory skins could provide more details regarding the individual’s vital signs and various other bio-physical characteristics.
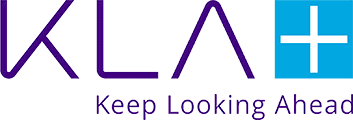
This information has been sourced, reviewed and adapted from materials provided by KLA Corporation.
For more information on this source, please visit KLA Corporation.