Red laser triangulation displacement sensors have been in operation for over 20 years, while blue laser versions are now available as a new addition. It is important to know the type of laser that performs bests on particular target material before choosing the color of the laser.
Laser triangulation is a widely used non-contact method for measuring industrial displacement. This sensor technology traditionally uses a red laser light. For more than 20 years, red laser sensors have been in use and they are well-known for their performance. In recent years, these sensors have been improved to provide excellent measurement stability on fast-moving objects as well as on a broad range of changing surfaces, including matt and low reflective surfaces. However, red laser sensors perform worse on certain materials. So, when can a blue laser triangulation sensor be used at its best compared to a red laser triangulation sensor? A number of factors need to be considered when answering this question.
Laser Triangulation Principle
In the principle of laser triangulation, a laser diode projects a visible light point onto the surface of the object that is being measured. Then the back-scattered light reflected from this visible point is projected onto a CMOS or CCD array by a high-quality optical lens system. When the target changes position, the movement of the reflected light is projected on the CCD array and analyzed to output the accurate position of the target. The measurements are digitally processed in the integral controller and subsequently converted into scaled output through analog (I/U) and digital interface RS422, EtherCAT or Ethernet.
.jpg)
Target Material
The target material or measurement object is important in determining how a stable measurement can be obtained. Certain materials, such as red-hot glowing metals, or objects release a high amount of light at the wavelengths in which red lasers function. Since this floods the CMOS/CCD detector, it is difficult to achieve stable measurements. When the target becomes hotter and releases high intensity light, the laser measurement completely fails.
A blue laser, on the other hand, operates at a shorter wavelength of 405 nm that is far from the red section of the visible spectrum. This makes the sensor not affected by the emitted light that is blocked from entering the detector with the help of a simple optical filter and ensures very stable signals. Originally developed for use on red-hot glowing metals in the steel processing industry as well as for measuring vibration on exhaust manifolds and for automotive brake disc deformation testing, blue laser sensors have also been used for other applications.
.jpg)
Other Materials
While measuring on foodstuffs, organic materials, transparent or translucent materials (e.g. plastics), blue laser light has a lower intensity, due to its shorter wavelength, and so it penetrates much less into the surface compared to a red laser. Since traditional red laser light penetrates more into the target material and gets diffused there, it results in a de-focused spot on the target surface. This causes a blurred spot to be reflected back onto the detector, controlling the sensor from defining the exact distance. On the contrary, the blue laser light, due to its reduced wavelength and intensity, does not penetrate into the target object. It creates a very small focused laser point on the surface and provides stable and precise measurement results.
Highly Polished Surfaces
The blue laser sensor, due to its shorter wavelength, performs better on gloss or highly polished surfaces. A red laser light can get distorted by the shiny surface and result in a “speckle” effect, increasing signal noise on the detector and reducing measurement accuracy. In contrast, the blue laser sensor with shorter wavelengths performs exceptionally well with less speckling and results in 3 times less noise levels than the red laser sensor.
2D/3D Profile Measurements
The benefits of triangulation using a blue laser light are not restricted to one-dimensional measurements, i.e. displacement, distance, thickness and vibration, but can also be applied to multi-dimensional 2D and 3D inspection such as contour or profile measurements. In this case, using blue laser sensors instead of red ones have introduced new measurement applications that were not possible previously by using red laser sensors. Therefore, a blue laser profile sensor can be used to measure profiles of red-hot glowing metals, foodstuffs, organic materials, highly polished surfaces and transparent materials.
.jpg)
When Red is Best
Red laser sensors will be more suitable in a high percentage of measurement applications than blue laser sensors. A red laser sensor with high intensity can perform better on matt or lower reflective surfaces, especially on fast-moving targets. Additionally, in terms of measuring ranges, sensor performance, and more cost effective solutions, suppliers typically offer more options and variants for red laser sensors.
Conclusion
When choosing a laser triangulation sensor for a distance, displacement or profile measurement application, it is important to take into account the surface and temperature characteristics of the target object. Questions need to be considered such as does the target appearance change from dark to white? Does the surface or material change dynamically as the measurements are taking place? How fast is the target object moving and how accurate do the measurements need to be? These will determine whether a red or blue laser is more appropriate for the application. Furthermore, some suppliers can provide both red and blue laser sensors in their product portfolio, which could result in a customer getting more reasonable advice before purchasing and improved technical support and advice.
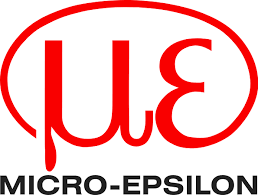
This information has been sourced, reviewed and adapted from materials provided by Micro-Epsilon.
For more information on this source, please visit Micro-Epsilon.