Confocal chromatic sensors provide the latest modern technology combined with maximum precision and high speed. These characteristics make these versatile distance and displacement sensors perfect for the high requirements of Industry 4.0.
In a world of Industry 4.0, sensors must be able to carry out high speed measurements and deliver high precision results so as to ensure reliable quality assurance. Optical measurement technology is non-contact and independent of the target material and surface properties, and as a result they are becoming more critical for production and inspection processes. This is a major advantage in a ‘live’ production process, where tactile measurement technology is operating at its limits, especially if the target is located in a difficult-to-access area.
Confocal chromatic sensors provide ground-breaking technology, high precision and high speed. In addition, the confocal chromatic measuring technique allows distance measurements, multi-layer thickness measurements of transparent materials, intensity evaluation and measurements within boreholes and recesses. The measurement process is wear-free, non-contact and practically independent of surface properties. Thanks to the extremely small measurement spot size, even very small objects can be detected. As a result, the confocal chromatic measuring technique is suitable for inline quality control.
A wide range of controllers and sensors are available from Micro-Epsilon. Various interfaces open up a host of applications, for example in consumer electronics, plastics production, medical engineering, glass and the semiconductor industry.
The Measuring Principle
The confocal chromatic measuring principle is built on polychromatic light which is categorized into individual spectral colors by being focused through a multi-lens optical system at varied distances from the sensor. More than long-wave, red light (700 nm), short-wave, blue light (400 nm) is refracted. The start of the measuring range is with blue light, while the end is with red light. Each wavelength is in a different focal plane because of controlled chromatic aberration. Each wavelength is assigned with a specific distance to the target through a factory calibration.
In the case of a sensor system, this wavelength of light is used for the measurement that is precisely focused on the target. The light that is reflected is imaged by an optical arrangement onto a light-sensitive sensor element, on which the related spectral color is detected and evaluated. Part of this light is reflected back with each change of different materials’ refractive index, allowing even one-sided thickness measurements of transparent materials. In multi-peak measurements, a number of distance points are evaluated.
The Advantages of Confocal Chromatic Measurement Systems
Micro-Epsilon’s modern sensor technology allows accurate measurements of objects exhibiting different surfaces. The material and surface properties of the target object have almost no effect on measurement accuracy. It is possible to perform high precision measurements on reflecting surfaces such as polished or high-gloss metals and liquids, on matt surfaces such as black rubber and plastics, and even on transparent materials such as plastic and glass plates. The very small measurement spot which, based on the system, measures only a few µm, allows for the measurement of, for example, bonding wire, IC pins on PCBs, and small contours of mechanical parts.
.jpg)
The extremely small and constant laser spot size allows the sensor to precisely detect very small objects e.g. in the semiconductor industry.
The confocalDT 2471 HS is ideal for dynamic measurement tasks and is specially developed for high speed processes. At 70 kHz, it is the world’s fastest confocal measurement system.
confocalDT 2471 HS is suitable for inline measurements with high dynamics, as needed by the glass industry for instance. Data is typically evaluated in real time, allowing for rapid intervention measures in production, for example, through EtherCAT.
Further, the automatic control of exposure time allows for high-speed measurements on different, changing surfaces, because the system can automatically control the line exposure time and adapt rapidly to a wider range of reflecting surfaces. This system allows measurements on directly reflecting and diffuse surfaces without having to modify the installation arrangement. High precision measurements are possible even with tilted objects.
These passive sensors do not transfer any heat onto the measurement object, are flexible in use and are available as special vacuum versions. The axial beam path prevents shadowing effects, allowing measurements even in recesses and sleeves. For measuring diameter and dimensional accuracy of boreholes, special sensors with a 90° beam path are also available. boreCONTROL is particularly developed for the inspection of small boreholes.
A user-friendly web interface is used to configure the controller and the sensors without any additional software. It is possible to access the web interface through Ethernet and this interface provides set up and configuration options. For multilayer measurements and thickness measurements, materials are stored in a comprehensive, individually expandable materials database. Ethernet, EtherCAT, Analog Out and RS422 are the various interfaces.
.jpg)
Measuring the diameters and the dimensional accuracy of boreholes is possible using special sensors equipped with a 90° beam path.
High Precision Inspection of Finest Surface Structures Using Intensity Evaluation Combined with Distance Measurements
Confocal chromatic measurement systems are employed for displacement as well as intensity evaluation and distance measurements. Using this method, surface properties of the smallest precision parts can be established to micrometer accuracy. For instance, scratches can be reliably detected.
.jpg)
Using this method, the surface properties of very small precision parts can be determined to micrometer accuracy. Scratches or similar defects can be detected reliably.
Surface topographies of objects can be carried out based on the determination of the distance. Applying both techniques is a specialty of Micro-Epsilon. Confocal chromatic sensors can also be used to measure the roundness, diameter, roughness and surface structure of cylinder liners. When a measurement object contains different types of materials such as plastics and metals, it is the reflectivity that highlights the differences in the materials albeit the distance values remain unchanged. Scratches and unevenness affect the degree of reflectance and become visible. After detecting the changes in the signal intensity, the system creates an exact image of the target and its fine structures.
.jpg)
Another option, in addition to distance measurement, is to perform measurements using signal intensity, which enables the visualization of the finest of structures. With constant exposure time, additional information about the surface evaluation can be made which would not be possible with just distance measurement.
Specialist in Container Glass Production
The confocal chromatic measuring principle allows precise, one-sided thickness measurements of glass and other transparent materials and is largely insensitive to tilting. Using just a single sensor, the thickness of the material is detected to micrometer accuracy. An editable, expandable materials database is provided by the controller. The thickness calibration feature allows continuous thickness measurements across the whole measuring range. Refractive indexes are material-specific parameters that can be adapted using the web interface. Up to five layers can be evaluated with multi-peak measurements. This is how multi-layer objects like laminated glass can be measured reliably.
.jpg)
Inspection of wall thickness and roundness of the bottles during glass production.
During the production of container glass, the roundness and wall thickness of the bottles represent important quality features. As a result, these parameters must be completely inspected. Any defective containers are instantly rejected and returned to the glass melt. The high processing speeds combined with the need to prevent damage to the bottles calls for a fast, non-contact measurement procedure. Micro-Epsilon’s confocal chromatic confocalDT 2422 dual-channel measurement system is suitable for this measurement task. This system measures synchronously on two points. Data is output in real time through an EtherCAT interface, and the thickness calibration feature allows for precise thickness measurements across the whole measuring range of the sensor. Irrespective of the glass color, automatic exposure control enables stable measurements.
Display Assembly Gap and Thickness Measurement of Multilayer Transparent Material
Solar cells, laminated glass, smartphone displays and flat screens present a huge challenge for measurement technology since they consist of several layers and different transparent materials. In order to guarantee high quality, the exact thickness of each layer and the air gap between those layers need to be established. Considering the high cycle rates involved, the measurements have to be carried out rapidly and precisely. Following the assembly process, for example, in smartphone production, the mounting tolerances of the components must be inspected to achieve continuous quality in all production batches.
.jpg)
For the highest product quality with multi-layer glass used in the consumer electronics industry, it is important to determine the exact layer thicknesses and the air gaps in between.
The determining factors in the electronics industry are increased production speeds and miniaturization along with rising economic efficiency. Function, quality and touch-screen communications of the end product require reliable measurement and inspection procedures in each manufacturing stage. Precise thickness measurement of each layer is crucial when producing multi-layer, curved and laminated glass for automotive, airplanes and architectural applications.
.jpg)
Confocal sensors perform non-contact measurements and provide reliable measurement values largely independent of the material and surface properties of the target.
These tasks are easily handled by confocal sensors. If the curvature of the adjoining layers fails to conform to the specifications, there is a risk of increased stress which may ultimately result in deficiencies or delamination of the glass. Micro-Epsilon offers high speed, compact and easy-to-integrate sensors that ensure highest reliability in practically any area where high precision is expected, ranging from machine monitoring to fully automatic quality control of the end product.
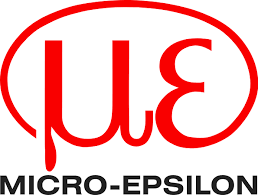
This information has been sourced, reviewed and adapted from materials provided by Micro-Epsilon.
For more information on this source, please visit Micro-Epsilon.