The Polymer Test LME Laboratory Mixing Extruder from Dynisco is an exclusive laboratory tool designed to assess the processability of a wide range of rubbers and plastics before production.
The LME fulfills several extruding requirements, ranging from coarse materials to very fine powders. It features a movable header and also a dial gauge that enables continuous mixer adjustability.
While operating the LME, the rotational shearing (mixing) is regulated by altering the distance between the inside header and the end of the rotor. This exclusive feature is not available in other extruders and enables users to perform numerous extrudate mix levels in just one sample run. Within the LME system, the rotational shearing enables intensive and extensive mixing and can be used in the manufacture of alloys or polymer blends.
Such blends are uniform enough to be spun into fibers across the whole composition range. Since mixing can be separately adapted, agglomerates of additives, like pigments or fillers, may be precisely regulated.
Features
- Three-part system—extruder, chopper accessories and optional Take Up
- Uses only a few grams of material
- Research and development tool
- Two separate temperature controls—header heater and rotor heater
- Four optional headers are available—tube, spinnerette, ribbon and wire coating rod
- Typical configuration offers a rod header with a replaceable 1/8″ (0.3175 cm) orifice
- Exclusive, screwless design
- Complete processing instrument that allows mixing, compounding and extrusion
- Short residence time—minimal thermal degradation at the time of the mixing process
- Water-cooled feed hopper
- Variable speed control—5 to 260 rpm
- Highest temperature—400 °C
Procedure
The sample material is first loaded into a cooled hopper, where it subsequently falls onto the heated surface of a cylindrical rotor. When the rotor turns, the sample material is dragged against the inclined surface of the stationary scroll and this movement initiates the transport toward the outlet die.
When the material accumulates in the radial gap, it is compressed by the converging space between the end of the header case and the scroll surface. The material subsequently travels to the axial gap, where it is rotationally sheared between the inside of the case and the end of the rotor. This movement introduces a centripetal pumping effect, which allows the material to travel to the outlet die and come out through the orifice.
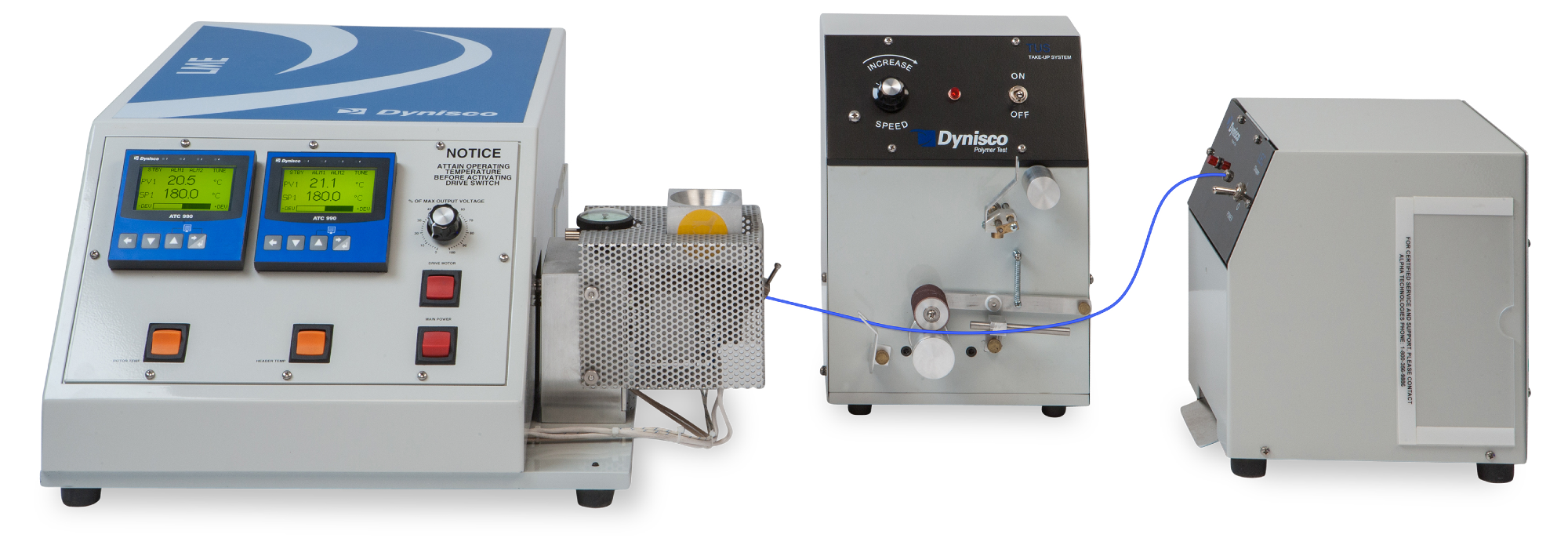
Image Credit: Dynisco
Recommended Features
LME Take-Up System
The Take Up System is a versatile variable drive machine. It can draw larger rods via a couple of nip rollers, or draw and wind extremely small diameter extrudate fibers from the LME system onto a spindle.
The nip rollers can even be used with the ribbon header, which is available as an option. In each case, the system speed can be modified to correspond with the speed of extrusion and can offer the required ribbon/tape width or rod/fiber diameter. Besides, the nip rollers are used to direct the extrudate rod to the chopper or pelletizer system.
LME Chopper
The LME Chopper pelletizes the extrudate from the Take Up System. This extrudate feeds into the chopper inlet from the nip roller provided in the Take Up System. The feed speed to the chopper can be used to determine the pellet size.
Uses and Applications
- Pelletizing
- Melt spinning
- Plastics and rubbers
- Wire coating
- Polymer blends
- Shape extrusions
- Fiber spinning
- Film extrusions
Compounding of:
- Fillers
- Additives
- Stabilizers
- Flame retardants
- Pharmaceuticals
- Plasticizers
- Antioxidants
- Pigments
Specifications
Source: Dynisco
. |
. |
Dimensions: |
19"W x 24"D x 9"H
(49 cm x 61 cm x 23 cm) |
Standard Header Included: |
1/8 (0.312 cm) diam. orifice
(replaceable) rod extrusion |
Weight: |
120 lbs. (54.5 kg) |
Cooling Water Feed Hopper: |
1 gal/hr tap water (3.785/hr) |
Electrical: |
230 V, 50 Hz/120 V, 60 Hz |