The task of mineral oil logistics is the reliable distribution of combustible substances from the producer to the end consumer.
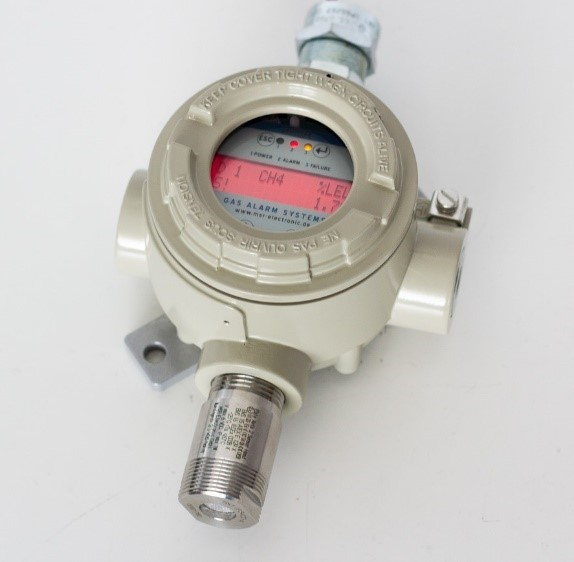
The main substances which are distributed are petrol and diesel fuels, kerosene, fuel oils, methanol and benzene. Distribution can take place directly ex refinery or via an intermediate tank farm using tank trucks. When tank farms are used, a high safety level of gas monitoring is required. To meet the SIL requirements, the MSR-Electronic product PolyXeta®2 with the innovative exchangeable X-Change sensor can be used. The MSR-Electronic product PolyXeta®2 detects volatile organic hydrocarbons due to the reliable safety calibration of the sensor.
Wherever flammable or toxic gases are present, the risk potential for people is particularly high, as they often cannot be smelled or seen. Fixed gas warning systems significantly reduce these risks for people and plants. With innovative products, MSR-Electronic reliably protects lives against dangerous gases. The international company successfully sells gas warning systems via branch offices and partners worldwide. The newly developed Bremen tank storage area requires a solid safety concept meeting the strict safety requirements from the authorities.
The measuring method with integrated temperature and drift compensation stands for highest accuracy and reliability with the long service life of the sensor. The device has a standard 4-20 mA analog output and two relays with adjustable switching thresholds. In the case of a leakage, an early warning of the occurrence of an ignitable gas concentration and countermeasures can be initiated. Installation and maintenance are carried out by the partner Gawando Gaswarnsysteme in this project. Regular functional and system checks in accordance with BG RCI T023 ensure the reliability of the gas monitoring system and the compliance with the requirements.
Decisive core size for combustible gases
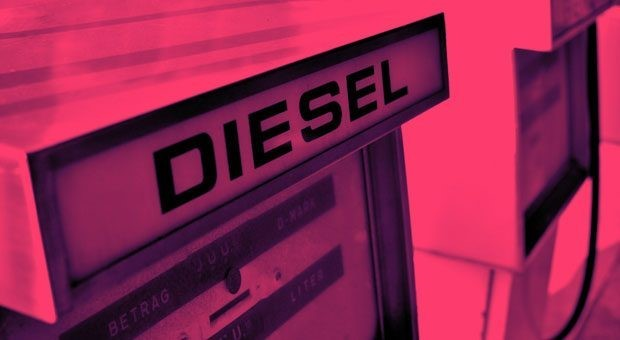
When combustible gases combine with air, they form explosive mixtures. There is only a limited range of gas/air concentration in which an explosive mixture occurs. An important core size for the hazard is the explosive range - the space between LEL and UEL. This area, which is defined by an upper explosive limit (UEL) and a lower explosive limit (LEL), is specific for each gas and each vapour. Outside these limits, the mixture is not flammable. Each gas reacts differently and therefore has different limits. In the past, these properties of combustible gases have led to sometimes large fires. In North Rhine-Westphalia, for example, there was an expansive tank farm fire in Duisburg harbour in 1979. However, the fire at the Buncefield tank farm in Great Britain in December 2005, which lasted for several days, was even more devastating.
MSR-Electronic offers a wide range of methods for the permanent detection of gases. On this basis, MSR-Electronic develops individual gas sensors for industrial applications where extreme conditions prevail.
The task of mineral oil logistics is the reliable distribution of combustible substances from the producer to the end consumer. The main substances which are distributed are petrol and diesel fuels, kerosene, fuel oils, methanol and benzene. Distribution can take place directly ex refinery or via an intermediate tank farm using tank trucks. When tank farms are used, a high safety level of gas monitoring is required. To meet the SIL requirements, the MSR-Electronic product PolyXeta®2 with the innovative exchangeable X-Change sensor can be used. The MSR-Electronic product PolyXeta®2 detects volatile organic hydrocarbons due to the reliable safety calibration of the sensor.
Wherever flammable or toxic gases are present, the risk potential for people is particularly high, as they often cannot be smelled or seen. Fixed gas warning systems significantly reduce these risks for people and plants. With innovative products, MSR-Electronic reliably protects lives against dangerous gases. The international company successfully sells gas warning systems via branch offices and partners worldwide. The newly developed Bremen tank storage area requires a solid safety concept meeting the strict safety requirements from the authorities.
The measuring method with integrated temperature and drift compensation stands for highest accuracy and reliability with the long service life of the sensor. The device has a standard 4-20 mA analog output and two relays with adjustable switching thresholds. In the case of a leakage, an early warning of the occurrence of an ignitable gas concentration and countermeasures can be initiated. Installation and maintenance are carried out by the partner Gawando Gaswarnsysteme in this project. Regular functional and system checks in accordance with BG RCI T023 ensure the reliability of the gas monitoring system and the compliance with the requirements.
Decisive core size for combustible gases
When combustible gases combine with air, they form explosive mixtures. There is only a limited range of gas/air concentration in which an explosive mixture occurs. An important core size for the hazard is the explosive range - the space between LEL and UEL. This area, which is defined by an upper explosive limit (UEL) and a lower explosive limit (LEL), is specific for each gas and each vapour. Outside these limits, the mixture is not flammable. Each gas reacts differently and therefore has different limits. In the past, these properties of combustible gases have led to sometimes large fires. In North Rhine-Westphalia, for example, there was an expansive tank farm fire in Duisburg harbour in 1979. However, the fire at the Buncefield tank farm in Great Britain in December 2005, which lasted for several days, was even more devastating.
MSR-Electronic offers a wide range of methods for the permanent detection of gases. On this basis, MSR-Electronic develops individual gas sensors for industrial applications where extreme conditions prevail.