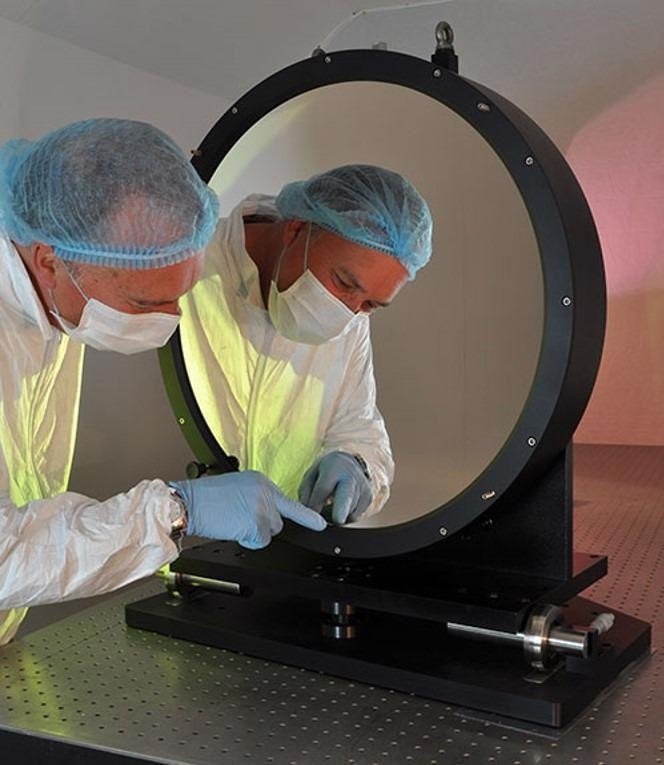
High precision prototype and custom optics. Image Credit: Optical Surfaces Ltd.
Benefiting from a uniquely stable manufacturing environment - Optical Surfaces Ltd. can routinely produce challenging prototype and custom optics to the highest levels of precision possible.
The company’s ISO 9001-2015 approved manufacturing workshops and test facilities are deep underground in an area excavated from solid chalk. This provides an environment where the temperature is naturally constant, and vibration is extremely low. These are important considerations when making, mounting, and testing high precision optics.
Working with these natural advantages Optical Surfaces can supply high precision off-axis parabolic, spherical, and flat mirrors, etalons, aspherics, reference flats, windows, collimators, and beam expanders for the most demanding applications. With such stable conditions testing, particularly with long path lengths, becomes quantifiable and reliable. Investment in large aperture interferometers allow detailed direct testing of optics up to 600 mm in diameter. Topographic and fringe analysis provides precise testing of surface roughness and confirms the wavefront of various surface forms. A rolling program for calibration of test optics where possible to national standards ensures that the quality of prototype and custom optics from Optical Surfaces is second to none.
Combining these natural advantages, with its team of experienced and knowledgeable optical craftsmen, Optical Surfaces Ltd has over the last 50 years produced the ultra-high precision prototype and custom optics that lie behind technological breakthroughs in areas including fundamental physics, astronomy, space, defence, medical, material sciences and the environment.
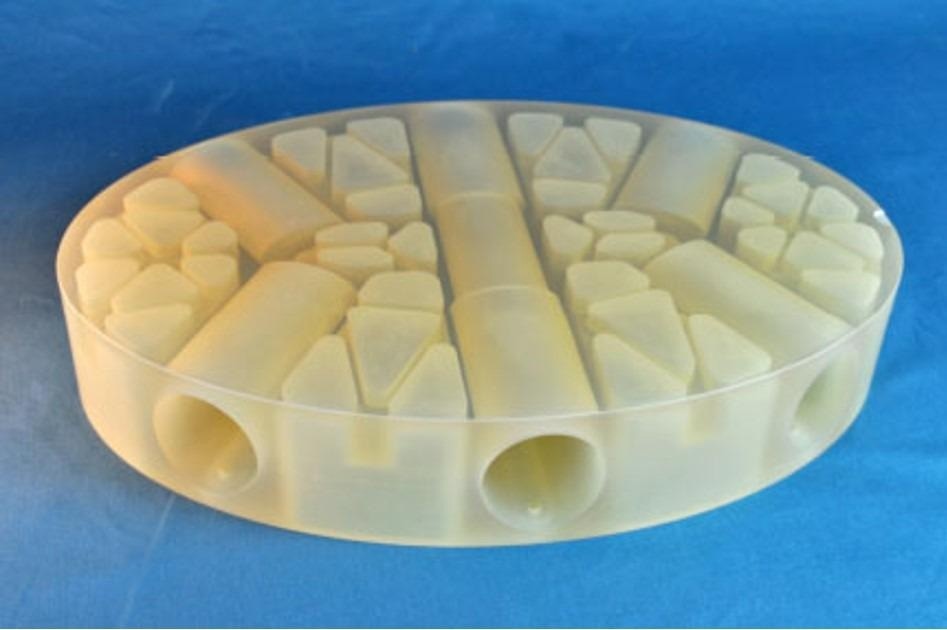
High precision prototype and custom optics. Image Credit: Optical Surfaces Ltd.