A 3D-printed insole with embedded sensors is being developed by researchers at ETH Zurich, Empa, and EPFL, which will enable the measurement of the sole’s pressure within the shoe and throughout any activity. Athletes or patients can use this to gauge their performance and therapeutic progress.
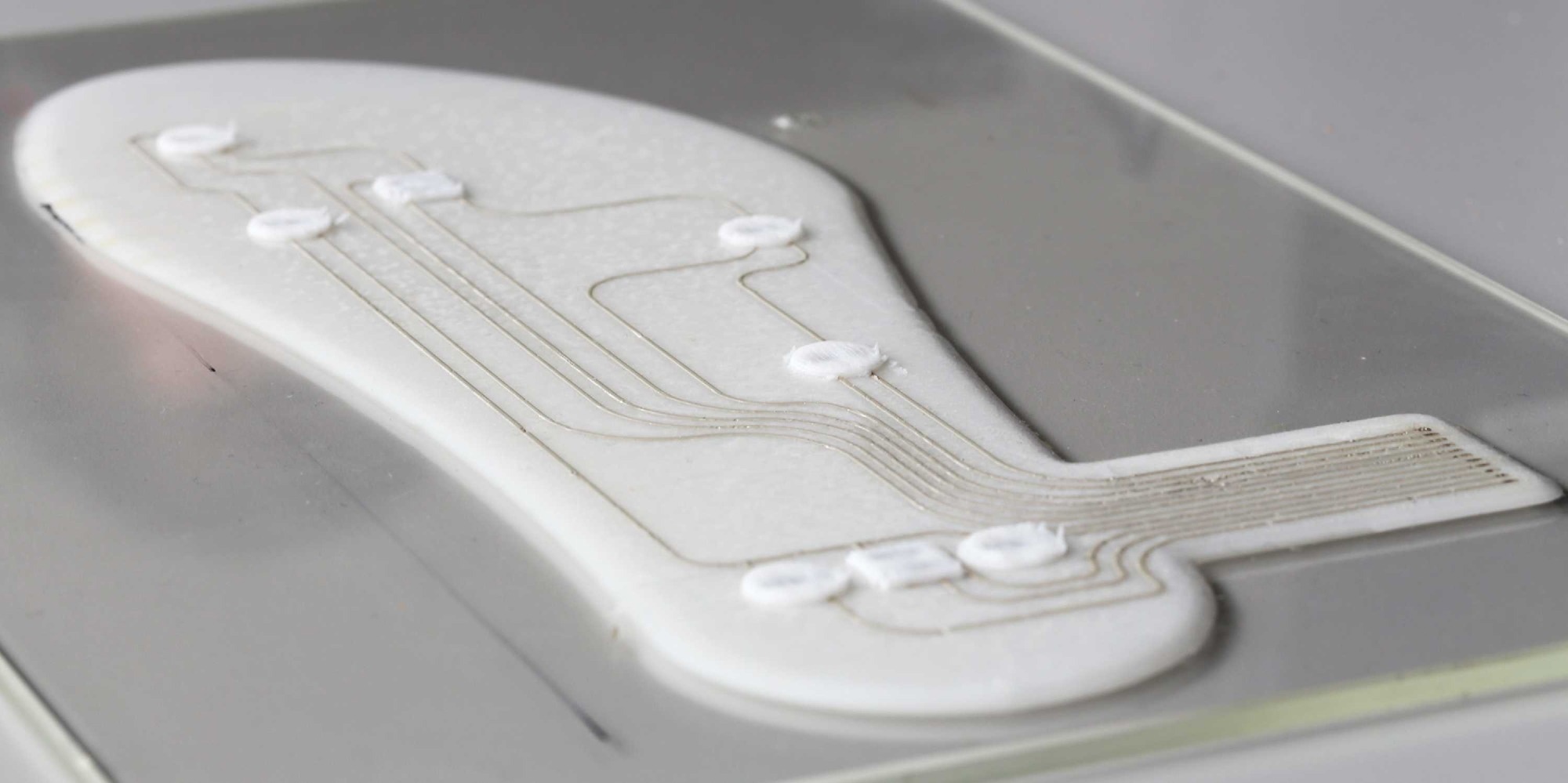
The insoles, together with the integrated sensors and conductive tracks, are produced in just one step on a 3D printer. Image Credit: Marco Binelli / ETH Zurich
Fractions of a second can separate winners from losers in competitive sports, and athletes utilize specialized insoles to improve their performance. Insoles are also used by people with musculoskeletal pain to relieve their suffering.
Specialists must first establish a pressure profile of the feet to appropriately install such insoles. To do this, athletes or patients are required to walk barefoot over pressure-sensitive mats, leaving their unique imprints. Using this pressure profile as a reference, orthopedists can manufacture specialized insoles.
This method has a shortcoming in that it takes time to optimize and adjust. The pressure-sensitive mats are also limited to enclosed spaces rather than allowing measurements while exercising or engaging in outside activities.
An idea developed by a research team from ETH Zurich, Empa, and EPFL could significantly improve things. The researchers created a customized insole with embedded pressure sensors that can monitor pressure on the sole of the foot directly in the shoe during varied activities using 3D printing.
You can tell from the pressure patterns detected whether someone is walking, running, climbing stairs, or even carrying a heavy load on their back—in which case the pressure shifts more to the heel.
Gilberto Siqueira, Co-Project Leader and Senior Assistant, Empa
This eliminates the need for time-consuming mat tests. The discovery was just published in the journal Scientific Reports.
One Device, Multiple Inks
These insoles are not only simple to use but also easy to produce. They are made in a single phase, including the integrated sensors and conductors, using a single extruder 3D printer.
The researchers print with a variety of inks designed for this use. The materials employ a combination of silicone and cellulose nanoparticles as the basis for the insole.
The conductors are then printed on this initial layer using conductive ink that contains silver. The sensors are then individually printed on the conductors using carbon black-containing ink.
The sensors are positioned precisely where the pressure on the foot is the highest; they are not dispersed randomly. The researchers apply a second coating of silicone to the conductors and sensors to further protect them.
Initially, getting adequate adhesion between the various material layers was a challenge. By applying hot plasma to the silicone layers’ surface, the researchers were able to find a solution.
They make use of piezo components, which transform mechanical pressure into electrical signals, as sensors to measure normal and shear forces. The researchers have also incorporated a sole interface for reading the generated data.
“So, with data analysis, we can actually identify different activities based on which sensors responded and how strong that response was,” Siqueira added.
Running Data Soon to Be Read Wirelessly
To read out the data, Siqueira and his team have inserted a contact on the side of the insole since they still require a cable connection. He claims that making a wireless connection will be one of the next developments.
Siqueira stated, “However, reading out the data hasn’t been the main focus of our work so far.”
Future athletes and physiotherapists could employ 3D-printed insoles with built-in sensors to monitor training or therapy progress, for instance. Training programs can then be modified based on such measurement data, and 3D printing can be used to create insoles for shoes that are permanent and have various hard and soft zones.
Siqueira and his colleagues have not yet started the commercialization process, despite the fact that they feel there is a large demand for their product, particularly in elite sports.
The insole was developed in collaboration with researchers from Empa, ETH Zurich, and EPFL. Researchers from ETH and Empa created the inks and the printing platform, while EPFL researcher Danick Briand oversaw the project, and his team provided the sensors.
The Lausanne University Hospital (CHUV) and the orthopedics company Numo were also involved in the initiative. The Advanced Manufacturing Strategic Focus Areas program of the ETH Domain provided funding for the study.
3D-printed insoles measure sole pressure directly in the shoe
Video Credit: Nicole Davidson / ETH Zurich
Journal Reference
Binelli, M. R., et al. (2023) Digital manufacturing of personalised footwear with embedded sensors. Scientific Reports. doi:10.1038/s41598-023-29261-0.