Chris Jones, Managing Director at Micro-Epsilon UK, discusses some of the more challenging automotive applications for non-contact displacement measurement and infrared temperature sensors.
With increasing pressure on vehicle manufacturers to downsize engine components, minimise the weight of onboard systems and therefore reduce fuel consumption and vehicle emissions, the requirement for extremely compact, high performance sensors is now critical, especially if installation space is also restricted.
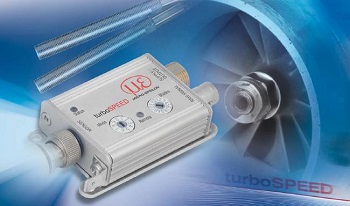
This is also true for integration – both in terms of electronics and building more intelligence into the sensor, without the need for any bulky, separate controllers. This means that displacement and laser profile sensors are more frequently required to perform signal conditioning directly in the sensor, therefore reducing component count, whilst offering faster measurement speeds.
Extensive range of sensors for automotive applications
Micro-Epsilon has been developing non-contact displacement measurement and infrared temperature sensors for automotive applications for more than 45 years. These sensors are used in automotive R&D, test cells, production and for on-vehicle testing in almost every conceivable area of a vehicle.
Applications range from eddy current sensors for measuring turbocharger speeds, piston ring movement, cylinder head lubrication gap and crankshaft bearing gap; inductive sensors for measuring engine valve lift; draw wire sensors for measuring suspension spring/damper movements; laser sensors for measuring brake disc deformation, vehicle ride height, monitoring the integrity of welds and adhesive beads during assembly or production and for the inspection of tyres for bulges or dents; and non-contact temperature sensors and thermal imaging cameras for measuring the temperature of on-vehicle components.
For more than 15 years, Micro-Epsilon has developed specific sensor variants for turbocharger speed measurement, enabling turbocharger manufacturers to test the performance limits of their products. Measurement systems are required to monitor the temperature and speed of the blades as they rotate.
Due to huge material stresses and extremely high speeds (up to 400,000rpm), turbocharger blades are made from either aluminium or titanium, which presents a challenge in terms of measurement technologies.
Titanium is a very poor electrical conductor and so eddy current sensors cannot be used easily on titanium. However, using special linearisation and advanced electronics, measurement systems have been developed, such as the TurboSPEED DZ140 from Micro-Epsilon, which are able to accurately measure the speed (and temperature) of both aluminium and titanium turbocharger blades over the complete speed range – in both multiple test cell and on-vehicle testing.
Having temperature measurement capability is particularly useful (and an industry first) as it allows the user to monitor the temperature inside the turbocharger without having to fit a separate thermocouple.
These sensors are robust, resistant to oil and dirt, extremely compact and slim, with some sensor variants measuring just 3mm in diameter and weighing just 85g. This allows the sensor and controller to be installed in engine compartments where space is tight. The sensors offer a high ambient operating temperature of up to 285°C. Due to its 9-30V DC power supply, the DZ140 can also be used for on-vehicle testing, with the sensor powered from a standard vehicle battery.
Vehicle ride height
In automotive and motorsport applications, measuring vehicle ride height is important. Non-contact laser displacement sensors have been developed to withstand the shock and vibration of being mounted to a vehicle.
With the laser window pointing down towards the ground or racing track, these high speed sensors are able to accurately measure and monitor the ride height of the vehicle as it travels around the track. Suspension characteristics and engine power mapping can also be adjusted in order to optimise vehicle performance and handling, whilst also reducing energy consumption.
Thermal imagers & I-R temperature sensors
For measuring the temperature profile of vehicle components, Micro-Epsilon has developed a range of extremely compact thermal imaging cameras. These operate at high speed data capture of up to 120Hz full frame rate, re-transmit either full temperature data or provide alarm limits for pre-set events such as overheating or maximum hot spot. This high speed data capture and re-transmission of full temperature image information allows play back at a later date – an important feature in many automotive R&D and failure diagnostics work.
The thermoIMAGER TIM400/450, for example, can be fixed into position in an automotive production line or R&D test cell lab in order to monitor the temperature profile of target materials or objects.
The cameras are even being used for on-vehicle testing and to monitor hotspots on vehicle cooling systems, exhaust manifolds, radiators and electrical terminals, as well as electrical systems on the latest all-electric and hybrid electric vehicles.
As well as thermal imagers, compact, infrared temperature sensors can be mounted on the vehicle to monitor the temperature of tyres, brake discs, engine and power train – almost any location where temperature needs to be measured.
Sensors even come with integral software that allows the user to change the emissivity of the sensor to suit different target materials such as steel, carbon or rubber.
For more information, please call the Micro-Epsilon sales department on 0151 355 6070 or email [email protected].