In the production of aluminum strips, strip thickness is considered to be one of the most significant parameters, since it plays a major role in further processing. Width also plays a major role – among other things when the material is cut into individual rings. Production deviations would cost a lot of time and money. Therefore, highly accurate production monitoring is an absolute ‘must’ in the production process, and it can be ensured reliably by the use of laser line sensors from the company Micro-Epsilon.
The aluminum production and processing market is a hard-fought one in which competition is intense. Thus, Manufacturers will have to face different challenges in order to be and remain competitive. Demands on the production process are becoming majorly strict, numerous standards need compliance with different limits and the use of raw materials must be optimized. To comply with all the conditions, parameters, regulations and standards and to be able to measure and determine with precision, measuring instruments are considered to be the only economical and rational solution.
They function as reliable, consistent and highly accurate control units in the production process. In both cold and hot rolling processes, deviations from the specified dimensions frequently occur right at the beginning of the production chain. If the thickness and/or width deviate from their nominal values and thickness fluctuates, then not only are the material costs no longer acceptable but the result may be quality deteriorations which, among other things, lead to an increase in difficulties during the further processing of production goods and can result in massive financial losses and complaints.
Comparison of Measurement Methods
The sector of metal thickness measurement is governed by three different principles. The first refers to contact methods in which, preferably, measurement heads are used, one below and one above the object. Owing to the contact during measurements such devices frequently wear more rapidly and so thus generate problems during production. Furthermore, measurements are made only at individual points, so that only approximate information can be obtained about the variation in thickness.
Radiometric methods function with isotope radiation or an X-ray source, which however is damped by the sheet itself. In this case, radiation is emitted and received by a transmitter and the mean thickness is determined from the difference between the emitted and received radiation. Depending on the condition of the material and the alloy, the method can be more reliable or less so. On top of that there are costs for regular safety testing and radiation protection, which of course entails regular expenses.
Optical methods based on laser triangulation have benefits when compared with other methods. They measure without contact and thus without wear. Moreover, independently of the condition of the material it is possible to perform an exact geometrical measurement in relation to the strip surface. In the most recent generation of thickness measuring units from Micro-Epsilon laser line triangulation sensors (= profile sensors) are employed, which produce further benefits. During the processing of cold strip, huge vertical movements often take place, for example in longitudinal slitting machines because of the forces exerted by the blades on the strip. Laser point sensors come up against their limits in this application.
.jpg)
The laser spot is extended to a laser line, so that more measurement values over a larger area are averaged (best-fit line), giving substantially greater precision.
The higher information density produced by a profile sensor here demonstrates its benefits. The laser spot is extended to a line in the profile sensor. The measurement is obtained from a “best-fit line” via the cloud of points produced by the sensor.
As a result, the distance-to-resolution relation is significantly better than with the point sensor, since the difference of the said line is calculated from the interplay of numerous partial resolutions. In essence, more measurement values over a bigger area are available, which when averaged provide greater precision. Thus, by virtue of the best-fit line this characteristic is so enhanced that eventually the resolution of the line sensor at a bigger measurement distance is considered to be better than that of the point sensor. With line-scanners, a working gap of 190 mm with a measuring range of 40 mm and a precision of ±5 µm is achieved because of the above measures, whereas with point sensors in the same range only about ±25 µm can be obtained.
Solution: C and O-Frame Systems
A constant sensor distance is vital for differential thickness measurement with distance sensors. As a rule two different design types are used, which on account of their shape are referred to as O-frames or C-frames.
In the C-frame, the sensors are mounted and fixed on an upper arm and a lower arm and the frame is then moved as a unit to reach the measurement position.
.jpg)
C-frames are particularly suitable for narrower strips. They can be moved completely clear of the production line, but for that they need more space than an O-frame.
C-frames are best suited for applications involving narrow strips, since with increasing material width the oscillation susceptibility of the upper boom increases. For the calibration of the C-frame, during coil exchange a master-component automatically moves into the measuring gap and so balances the system for new measurements. The benefit of the C-frame is that during threading-in or in hazardous situations due to so-termed ski effects (the strip curves upward on one side) or alligator effects (the strip curves downward and upward) at the start of the strip, the C-frame can be removed completely from the line. However this demands space, which above all in the area of the service center is often not available.
Here the O-frame is considered to be a better option due to its compact structure. Precisely because of the constant measuring gap, which is a crucial criterion for the precision of such a unit, the O-frame has significant advantages.
.jpg)
Measurements made using an O-frame are extremely precise and, thanks to their compact structure, can also be made when space is limited.
The design of this version is based on a stable frame which is incorporated in the production line. By virtue of the rigid frame, it is possible to inspect strip widths of up to 4,000 for thickness, width, profile, etc. This version also has an auto-calibration unit. During the measurement, the sensor system continually moves across the metal strip and thus gathers profile data over the full width of the strip material.
Constant Measuring Gap
In combination with the O-frame, a constant measuring gap is a fundamental prerequisite for precise results. Here, monitoring of the measuring gap with an additional displacement-measuring sensor technology or by iterative calibration at process-uncritical times has proved its worth. Temperature variations influence the geometry of the machine frame and consequently the measuring gap.
However, there is as a rule sufficient time for taking the necessary action without compromising the manufacturing process since these temperature-related changes take place only slowly. In this context, help is offered by the concept of the “compensation frame” patented by Micro-Epsilon. For this an additional, temperature-invariant frame is incorporated into the system parallel to the lower and upper booms, and the support of each measurement sensor is extended with a so-termed compensation sensor.
These sensors establish the distance of the support from the compensation frame. A variation of the measuring gap is thus transformed to the extent of 100% to the distances of the compensation sensors from the compensation frame. In that manner, the change can – so to speak – be eliminated and the measuring gap held constant at an uncritical level.
Thickness Measurement with Integrated Width Measurement in Longitudinal Slitting Shears
Besides thickness measurement, the edges of the material being measured can be very accurately identified because of the high lateral resolution of the linear sensors. In longitudinal slitting shears this makes it possible to determine the transverse profile for every single ring. For methods with a large measurement spot that is extremely difficult, the lateral resolution of the method is often not sufficient for this measurement task if the slit strips are narrow. For rings that are cut from strips and which are extremely close to the minimum tolerance limits, with the help of a thickness measurement unit based on profile scanners the yield obtained from a coil can be increased.
A ring developed can still be within tolerance while those adjacent to it can no longer be sold, or not as part of the order concerned. A ring with acceptable dimensions is no longer brought into circulation when there is only one thickness profile, whose lateral resolution is imprecise. The possibility of edge detection also allows precise width measurement. In addition to the sensor system for thickness measurement, a third laser line sensor is incorporated in the system, which can be separately positioned.
Thus, the two edges of a strip can be synchronously detected and any clustering has no effect on the measurement result. While the thickness sensor system is shifted constantly across the width of the material as a whole, the width sensor is in each case positioned at the next cutting gap. The width measurement for the strips is carried out immediately after both sensors detect the edges of the strip.
.jpg)
Thickness measurement with integrated width measurement in a single system.
Thickness Measurement of Laminate Sheets
The thickness measurement of laminate sheets is considered to be an additional application for which the laser line sensors are predestined. For this, it is not possible to use methods involving penetrating radiation. For instance, radiation methods only measure the material fraction in the measuring gap but not the dimensional accuracy of the product if the laminates are developed with outer sheets and a web structure on the inside. Laser line scanners only determine the geometrical dimensions of such sheets and recognize undulations, which provide information about problems during processing.
Thickness Measurement of Corrugated and Dimpled Sheets
Laser profile sensors display their strengths especially in measurements on structured surfaces. In the manufacture of dimpled or corrugated sheets, both the basic thickness of the material and the overall thickness of the finished product are of interest. Both methods with a large measurement spot, such as the use of X-ray or isotope radiation, and also ones with an extremely small measurement spot such as point-shaped laser triangulation, or even contact methods, cannot perform this task. Laser line sensors have a maximum line width of up to 64 mm depending on the measuring range. Since the geometry of the rolls used to roll the dimpled or embossed profile into the sheet is known, it is possible to position the sensor in such a manner that both the dimple peaks and also the basic thickness of the sheet can be determined in a reliable manner by the laser line.
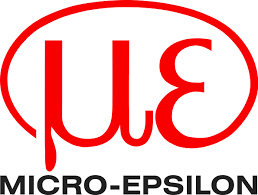
This information has been sourced, reviewed and adapted from materials provided by Micro-Epsilon.
For more information on this source, please visit Micro-Epsilon.