By Kalwinder KaurJun 19 2012
Coal mining became a large-scale industry at the beginning of the 18th century. With coal being the main energy source, the low cost and high abundance of this material made coal mining important for the growth of the economic industry. Despite a shift in the use of energy sources from coal to electromechanical generators in later years, coal remains a valuable energy source via modern-day open-pit extraction methods.
An early method of extracting coal involved tunneling into the earth; however, this procedure produced harmful vapors (i.e., carbon monoxide with 0.1 per cent concentration that is capable of causing death within minutes of exposure; carbon dioxide; and hydrogen sulfide) during the oxidation of coal as a result of spontaneous combustion in mining procedures. The use of sensors designed for gas detection in mines has developed from the miner’s canary to infrared sensors.
A Miner’s Canary
The canary (Serinus canaria) was commonly used by miners to alert them of the presence of toxic vapors such as the odorless carbon monoxide in hazardous areas of underground mining pits. The use of a canary was a low-tech gas sensor solution for the safety of miners in an uncertain working environment.
In the event of an explosion or a fire in a mine, rescuers would descend into the mine carrying a canary in a cage. A canary was known to be sensitive to carbon monoxide poisoning and so any distress shown by the canary would alert the miners to toxic gas exposure and give them enough time to return to safety. Mice were also used as carbon monoxide detectors; however, canaries displayed more obvious signs of distress to small concentrations of carbon monoxide. For instance, in the presence of toxic concentrations of carbon monoxide, a canary would sway from side to side before falling off its perch.
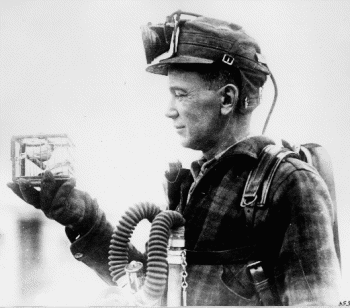
Figure 1. Rescue miner using a canary to help detect noxious gases in a mining pit.
By 1987, the use of canaries in mining pits to help detect noxious gases were phased out by the government. The canaries were deemed ineffective and unsafe to detect the presence of pollutants in the atmosphere. Also, maintenance was higher, which was not ideal in a constricted underground working environment. Modern-day technology in detecting toxic gases was soon developed; they were considered cost-effective and long-term solutions to gas monitoring in mining pits.
The Pellistor
The mid-1960s introduced catalytic pellistors as successors to the canary. This sensor is made of two platinum wires positioned within a ceramic mass. Both wires are connected to a Wheatstone-bridge circuit. Part of the ceramic mass contains a bead catalyst for oxidation and an additional ceramic bead that will inhibit the process of oxidation.
A working principle to the pellistor involves transmitting an electrical current through the platinum wire which then generates enough heat for the oxidation of a noxious gas (about 450°C). During exposure to a toxic vapor, the gas diffuses through a permeable membrane in the sensor, becomes oxidized, and initiates a catalytic reaction that creates resistance of the metal coils.
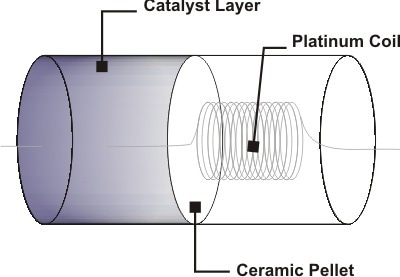
Figure 2. Schematic drawing of a basic pellistor.
The pellistor also contains an inactive ceramic bead to control the impact of ambient temperature and humidity interfering with it. The presence of a gas flow results in heat generation between the two metal coils, altering the resistance of the conductive wire, and creating an imbalance in the bridge circuit directly proportional to the gas concentration. The pellistor is designed to combust carbon-based compounds including carbon monoxide, but combustion of this has an impact on neighboring combustible compounds.
Pellistors are useful for sensing a wide range of flammable gases and toxic vapors. Application of the pellistor involves positioning the sensor in a strategic point within an environment at risk of contamination by hazardous gases. Although the pellistor is a more effective detector for poisonous gases, it still carries many limitations::
- A pellistor will malfunction when contaminated by chemicals containing halogen, sulfur, chlorine compounds, or metals containing lead or silicon;
- Contamination by silicon will impact the sensitivity of the pellistor; and
- Regular calibration and high maintenance of the pellistor does not make this sensor cost-effective.
Pellistors are prone to a calibration drift. Thus, they tend to be unreliable and give inaccurate readings on gas contamination in the surrounding area.
Infrared LED-based gas sensor
Infrared (IR) LED gas sensors, engineered with a dual-beam, have become the preferred method for monitoring gas. The use of such modern-day technology helped shape current practices in the mining industry, especially when considering the safety of a mining environment.
Miran SapphIRe XL Ambient Air Analyzer
Figure 3. Miran SapplRe XL gas analyzer
Compared to existing old-age methods for monitoring gas, IR-based gas monitoring carries certain advantages, such as the following:
- IR gas sensors carry a wide measurement range which allows for the detection of gas concentrations from a few parts per million to 100 percent;
- There is a rapid response rate, approximately 0.1 seconds from the time it takes for the gas to enter the analyzer to the time it takes to measure the gas concentration;
- Background gases cannot affect the IR LED gas sensor; and
- Individual gases can be measured accurately.
The evolution of gas sensors appears to have shaped the mining industry, allowing technology such as the IR gas sensor set to work effectively for five years with increased accuracy in the measurement of noxious gases. Catalytic sensors such as the pellistor are more susceptible to contamination, and with limited inspection principles, it is struggling in its competition with IR technology.
Sources and Further Reading
- https://www.clairair.co.uk/
- Xie, H., Golosinki, T.S. (1999). Mining Science and Technology '99. Vermont, USA: A.A. Balkema Publishers. 703–706.
- Hillstrom, K., Hillstrom, L.C. (2006). The industrial Revolution in America. California: ABC-CLIO, Inc. 202–205.
- Comini, E., Faglia, G., Sberveglieri, G. (2009). Solid State Gas Sensing. New York: Springer Science and Business Media, LLC. 241–255.
This article was updated on 13th February, 2020.
Disclaimer: The views expressed here are those of the author expressed in their private capacity and do not necessarily represent the views of AZoM.com Limited T/A AZoNetwork the owner and operator of this website. This disclaimer forms part of the Terms and conditions of use of this website.