A broad variety of material forms range from fine sawdust and shavings, to pellets, chip and coarse hog fuel. On the other hand, precise measurement and ongoing monitoring of the content of the material stored in silos, tanks and bins can present a lot of difficulties. However, constant checking of sensors or levels not only wastes time but also poses a high risk.
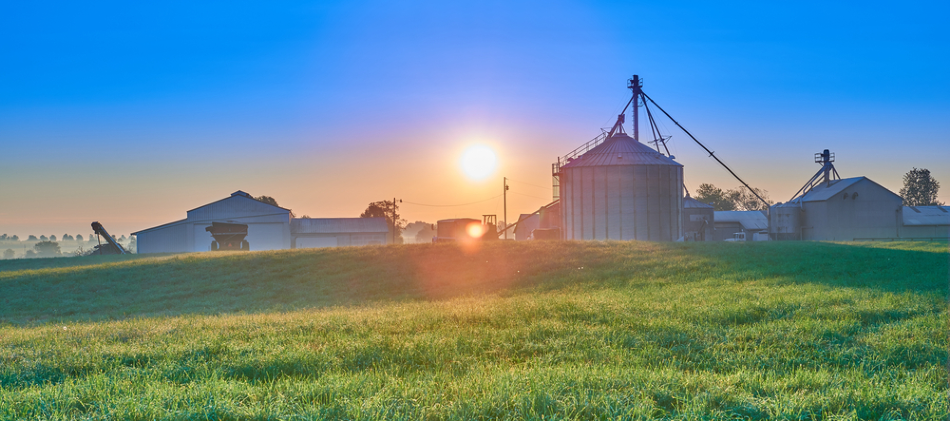
Image Credit: Shutterstock/Patrick Jennings
Level Sensors to Meet Material Challenges
Such issues can be overcome with the help of level sensors, which have made it considerably easy to remove manual measurements. These devices can be used with complex materials. For instance, hog fuel can behave unpredictably because the material is shredded. It also differs in length, interweaves together when being discharged, and clumps into irregularly-shaped forms, making it difficult to determine.
On the other hand, pellets have a consistent size and can flow freely, particularly in a center-fill, center-discharge vessel. There are certain level sensing technologies that do not work properly with shavings and sawdust. These materials tend to have low-bulk density and are fluffy and light. Wood chips, because of their uneven shape, can prove difficult to determine as they tend to clump together and do not flow freely in and out of a bin. This makes the surface of the material irregular, wherein wood chips differ from one part of the bin to another.
Continuous Inventory Monitoring
The type of sensor utilized depends on the type of material used. Some sensors include acoustic scanners, weight and cable-based sensors, and point level indicators.
Sensor Type |
Sawdust |
Pellets |
Wood chips |
Hog fuel |
3D Acoustic |
|
√ |
√ |
√ |
Cable-based |
√ |
√ |
√ |
√ |
Rotary |
√ |
√ |
√ |
|
Vibrating rod |
√ |
√ |
√ |
|
Acoustic Scanners
Non-contact level sensors are utilized in some facilities as they do not interrupt and remove the danger posed to employees. Although these devices are more expensive when compared to single-point measurement devices, they are suitable for those facilities desiring improved inventory precision. A 3D acoustic scanner determines various points in a tank to provide a high level of inventory accuracy and also detects the highest, lowest as well as the average levels. In addition, the approximate volume of material in the tank is also reported by the 3D acoustic scanner. Since it can work at extremely low frequency, it can be used in dusty environments where other non-contact sensors can prove ineffective.
.jpg)
3D scanner.
Although developed for monitoring and controlling inventory, the 3D acoustic scanner is not suitable for process control. Instead, it is utilized to measure the uneven material surface and to report the build-up of material in a tank. Also, It can be used in materials having a bulk density of 12 lb./ft3 or above.
In biomass facilities, the 3D acoustic scanner has been successfully used in silos, bins and tanks comprising woody biomass in vessels that range between 25' and 45' in diameter. The device is highly precise than other non-contact devices that only calculate a single point.
Weight and Cable-based Sensors
For solid materials, such as wood chips or pellets that flow easily, weight and cable-based sensors provide an ideal choice. The principle operation of this sensor is that it works by dropping a weight to the material surface and then draws back. The measurement data obtained is precise and can be transmitted to a control console or to a computer for monitoring. The device is cost-effective and reliable, and in order to gain maximum benefit it should be placed at the right location of the tank. Mounting approximately 1/6th from the external perimeter of the tank provides a high level of precision in center-fill, center-discharge vessels.
Point Level Indicators
Point level indicators are generally deployed in load-out bins and storage tanks. They are used at the top or base of a bin to notify when full or empty, respectively. Other devices are rotary level indicators and vibrating rods that are suitable for free-flowing materials such as wood chips and wood pellets. The latter has a more consistent size and hence can be easily measured. In addition, rotaries can also be utilized in sawdust, as long as it is not wet. But, they should not be used in stringy material like hog fuel as it tends to cover around the paddle and produces a fake signal. Likewise, vibrating rods can be utilized in lighter materials, such as shavings and sawdust.
Conclusion
The guidelines provided above will help facilities to do away with manual measurements, reduce the time spent on repeated checking of bin levels and benefit from improved safety.
.bmp)
This information has been sourced, reviewed and adapted from materials provided by BinMaster.
For more information on this source, please visit BinMaster.