Named half-facetiously after the well-known comedian Rodney Dangerfield who always claimed he got, “No respect I tell ya!”, the Dangerfield Effect refers to the overt lack of care among first-time users of four-gas monitors in ensuring that their devices are set to achieve accurate outputs.
While formerly single-gas hydrogen sulfide (H2S) monitors were the norm, more and more oil and gas companies have switched to using four-gas monitors as they have become aware that there are many more hazardous gases than just H2S. This dramatic increase in usage has led to a large number of people using these instruments for the first time, as well as many companies who are still achieving familiarity with the detectors.
Unfortunately, this has led to a general disregard for the importance of gas detection, among individuals in the workforce as well as the companies who order their usage. This in turn is likely to be accompanied by grave consequences if not corrected soon.
.jpg)
Dangerfield performing in 1972.
Reasons for Ignoring Important Recommendations in the Use of Four-gas Monitors
All electronic devices require some inputs to produce some outputs. For instance, a cell phone is a useful device for an oilfield worker who values connectivity, getting information irrespective of location, and remaining in touch with the work situation all the time. This value placed upon the outputs ensures that the phone receives the required inputs, namely, regular charging, payments for data usage and due care of the device.
On the other hand, an individual who has no use for these outputs would never pay for a good phone or for its maintenance, but rather buy the least expensive phone available which lacks connectivity features, because the phone will be very seldom in use. When the outputs more than balance the inputs, the device and the user have a good relationship.
.jpg)
Solutions like the Bump-N-Go gas cylinder make it easier for mobile works to perform daily bump tests before using the gas detector.
So, with four-gas monitors: first-time users often ignore the fact that these instruments need to be bump tested, charged, and calibrated on a regular basis to perform as designed. Users often feel negatively about the primary output, namely, the alarms.
They think of them as unnecessary, false, and irritating. In their minds, the alarm outputs result in a disruption of their work, financial loss, and lowering of productivity. Since these are important consequences, they cause the user to devalue the instrument which is responsible, the gas detector. In addition, the earlier single-gas monitor to which most of them were used had only a few alarms in contrast to the many more situations in which the four-gas monitor activates alarms.
This has led to the Dangerfield Effect, where the users do not think the outputs are worth the trouble and inconvenience of the input tasks. They consider the required inputs to be unimportant, performing them very infrequently or not at all. They seriously think of leaving off the device altogether. This is because they truly want to ensure that their work will not be disturbed by the alarm going off – the only good alarm is no alarm.
One such case is when the bump testing strongly recommended by all manufacturers for very good reasons (as given in the fine print section of the instrument’s manual) is ignored or excused away.
How to Correct this Trend
It is sadly true that many individuals and companies wake up to the necessity of putting in the required inputs and paying attention to the outputs too late, after an accidental tragedy involving gas detection in their own oilfield. However, it is possible to avoid such situations altogether, by taking the following three simple steps:
Step one is just arranging for proper training on the use of the detector (internal or external training may be selected as appropriate), how it responds in various situations, its limitations, and the right way to react to an alarm. This should be reinforced by first-hand stories, from the company or from other sources in the industry. This is essential if the path to learning about the proper use of the four-gas monitor is to begin with personal bonding to the content presented.
Step two consists of supervising the gas detection program, with respect to maintaining the equipment as recommended, the way the monitors are used, and the level and range of exposure. This data is easily retrieved from the data logs and should be studied. If not, the reason for insisting upon workers wearing these detectors is not clear.
Step three is based upon discussing the feelings and thoughts of the workforce with respect to the detectors, giving and getting feedback on the data received. It is important to understand how workers feel about the devices and about having to wear them, asking for their thoughts on how their use can be eliminated or greatly reduced by avoiding gas exposure, if possible, by altering the workflow, for instance. Employees who adhere to safe policies should be rewarded if feasible and advisable.
This short list of tips is meant to help to begin an interaction with the workforce about the reason for the use of gas detectors, their scope of use and their limitations. It is important to realize that these instruments are designed to be reliable gas detectors and are not just creators of frustrating false alarms.
This is possible only if the workers are trained to understand their significance, use them in a correct and thoughtful manner, and understand the basic truth that the inputs are essential to achieve a possibly lifesaving output from these unassuming and often unappealing devices. While their role is to protect the workers rather than glamorize them, they may very well be solely responsible for preventing a fatality in the oilfield, and this truth must rule their use.
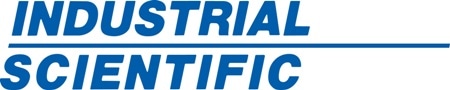
This information has been sourced, reviewed and adapted from materials provided by Industrial Scientific.
For more information on this source, please visit Industrial Scientific.