When solid material reaches a certain point in the vessel, point level indicators detect and give out an alert through a horn, light or alarm panel. Personnel are notified when a vessel is either full or empty. Point level indicators help in optimizing storage capacity and enhance inventory management. They prevent overfilling of material and help prevent spills, material waste, and subsequent downtime. Point level indicators also improve safety by removing the need to climb bins to check material level, and thus save significant amount of time. The systems are durable, reliable and cost effective.
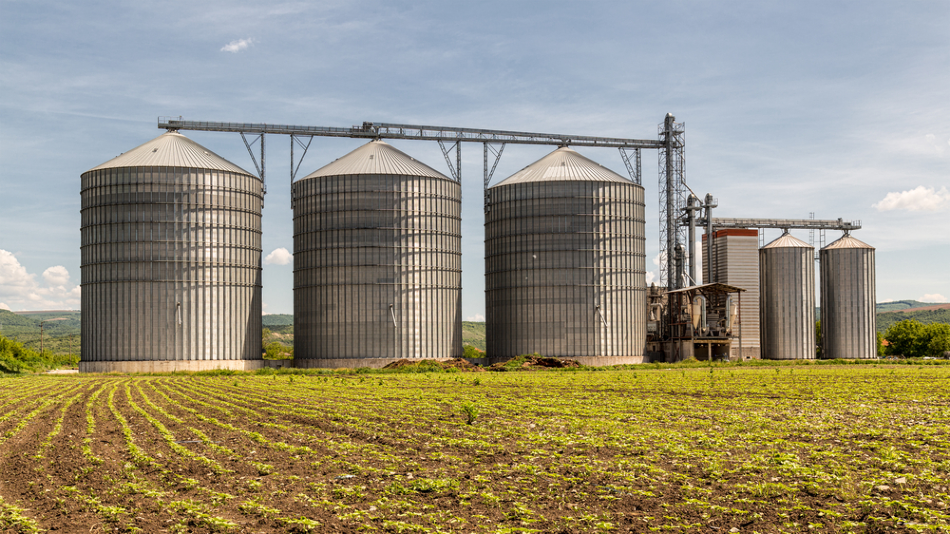
Image Credit: Shutterstock/nikifortodorov
Rotaries
Rotaries are popular devices that are utilized for point level indication. They are generally employed in ethanol plants and biodiesel facilities. Rotaries operate on simple principles. When the device is utilized as a high level indicator while the bin is filling, the paddle turns continuously until the material reaches the paddle. In case the paddle meets resistance owing to the presence of material, it stops turning and gives out an alert. Likewise, as a low level indicator, the paddle turns when the material falls under the level of the paddle and sends an alert.
Based on the type and weight of material, the proper paddle for the rotary should be selected. BinMaster provides 14 different paddles for different applications. Another important thing to consider is the types of rotaries. Binmaster’s BMRX is a standard rotary that is designed to ensure protection from system power failure. The device includes a “de-energized” motor that shuts down automatically in the presence of a material. This feature extends the life of motor. Another model is the BinMaster MAXIMA+, a fail-safe rotary that constantly self diagnoses and sends an alert in the event of a failure. The rotary is equipped with all the features of the BMRX, and includes an LED light to monitor the motor’s status. BinMaster offers vertical and horizontal extensions for the rotary for centerfill bins and thick-walled bins, respectively.
.jpg)
BinMaster BMRX genuine fail-safe rotary.
.jpg)
Vertical rotary extensions up to 144? for high level detection.
.jpg)
The vertical extension with collapsible paddle allows installation without entering the bin.
Vibrating Rods
For point level detection, a vibrating rod can also be applied. It can be utilized to identify the level of pellets, wood chips, wood shavings or sawdust. The vibrating rod is highly sensitive and can detect extremely light materials, such as fine sawdust. The device provides exceptional benefits with its single-blade, double-edged sword design that eliminates material build-up on the rod. This also removes the problem of bridging and false alarms, which are common in a tuning fork design.
.jpg)
The vibrating rod has a single blade design to prevent build-up.
Advanced systems for Continuous Inventory Management
For inventory management and process control, continuous level indicators are normally utilized. They determine the material level and report the data to a PC or console at predetermined time intervals or on a continuous basis. Continuous inventory management enables improved inventory correctness for month-end inventory or daily operations. Better precision can aid in optimizing inventory turns and carrying expenditures and simultaneously help plant management to improve storage capacity and transportation logistics.
Weight and Cable-based Systems
.jpg)
SmartBob installed on a sawdust bin.
The weight and cable-based system can be used in a variety of applications in the bioenergy industry as it is resistant to temperature, humidity, dust, fumes and dielectric constant that may be present in the bin. The system makes minimal contact with the material and operates in most types of materials, irrespective of bulk density or particle size. It utilizes different probes for heavy and dense materials like wood pellets and for extremely light materials like sawdust. When the sensor probe descends and retracts, redundant measurements are taken to guarantee accuracy.
Acoustical-based Systems
Acoustical-based systems are integrated with a non-contact, dust-penetrating sensor that has acoustics-based technology. The 3D mapping capabilities of the sensor enables users to view the contents of bin, detect cone up or down, and also view material build-up on sidewalls. The build-up detection feature enables preventive maintenance and cleaning and thus prevents damage to the bin. For bins that measure more than 45' in diameter, a multi-scanner system can be used to record measurement data from two or four 3D scanners and consolidate the data to report volume.
Conclusion
A variety of level control solutions are available in the market that range from a few hundred dollars to thousands of dollars. With recent advancements in product design combined with the robust range of level control technologies, users can opt for safe and smart solutions to realize better profitability and optimized operation.
.bmp)
This information has been sourced, reviewed and adapted from materials provided by BinMaster.
For more information on this source, please visit BinMaster.