Graphene is an ideal material for use in nanoelectromechanical system (NEMS) applications, thanks to its low density and high strength. Chemical, biological and physical sensors are examples of applications where NEMS can exhibit sensitivity much higher than competing technologies.
The small footprint of Graphene sensors and NEMS is leading to increasing interest in medical and remote sensing applications.
First Studies of Graphene Membranes for NEMS
Studies on graphene membranes for NEMS began in the late 2000’s with some of the first papers released by the research team headed by Paul McEuen at Cornell University. Those first sensors demonstrated sub-millielectron sensitivity, detecting the most minute variations in electronic charge.
With an active dimension of only one atom, the sensor, composed of graphene membranes hanging over trenches in the underlying substrate represent the thinnest mechanical resonators ever produced. The devices can operate either optically or electronically at frequencies in the megahertz range thereby providing designers and engineers with a versatile sensing solution.
.png)
The properties of graphene make it ideal for use in NEMS sensors. Image: Photos.com.
Research into Graphene Mass and Temperature Sensors
Following these initial breakthroughs the research group at Columbia University, extended the scope of the research with the production of graphene mass and temperature sensors.
In 2013, Max Lemme and colleagues at KTH in Sweden published their ground-breaking research on the development of graphene based pressure sensors that are highly sensitive with a small footprint.
In recent papers, the Lemme team have shown the superior pressure-sensing ability of graphene NEMS sensors over competing technologies. The graphene sensor is fabricated by cutting open a trench in a silicon dioxide substrate followed by the deposition of a graphene sheet over the trench. The graphene suspends freely like a drum membrane above the trench (Figure 2). The sensor has a cross-sectional area of only 65 by 6 µm.
To test the sensor, the pressure of the surrounding atmosphere is modified; however, the pressure inside the drum remains unchanged due to the impermeability of the graphene sheet to air. The pressure gradient between the drum and its surroundings creates a force proportional to the pressure, causing the graphene sheet to expand by up to 200 nm.
The bulging of the graphene sheet is determined through the piezoelectric property of the nanomaterial. This piezoelectric property causes the electrical resistance variation under strain. The increase in pressure causes a decrease in the resistance, which, in turn, increases current.
.jpg)
Figure 1. Graphene NEMS pressure sensor, consisting of a single graphene layer suspended above a trench in the substrate.
This graphene-based NEMS pressure sensor has demonstrated a pressure sensitivity of 4 µV/V/mmHg. This novel sensor has 2 to 10 fold sensitivity per unit area compared to standard silicon or carbon nanotube based microelectromechanical sensors (MEMS).
Given a specific requirement on sensitivity, it is possible to scale down the graphene sensor to much smaller footprint compared to traditional sensors. This technique employs conventional CVD graphene and the graphene transfer process developed by Graphenea.
Conclusion
These research results indicate the promising future for graphene NEMS sensors and their ability to become a serious competitor to existing sensor technologies. Pressure sensors are deployed in controlling and monitoring operations in a myriad of everyday applications, for example, automobile sensing, aerospace and weather monitoring. A graphene-based pressure sensor is especially advantageous for the aerospace sector due to the ultra-small scale of the device.
About Graphenea
Graphenea is a leading graphene producer for industrial and research needs. Graphenea has developed a leading synthesis and transfer process to obtain high uniformity monolayer graphene films on any substrate.
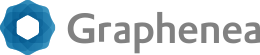
This information has been sourced, reviewed and adapted from materials provided by Graphenea.
For more information on this source, please visit Graphenea.