For improved inventory accuracy in silos, tanks and bins, multiple-point measurement is always better when compared to single-point measurement. Acoustical-based technology includes multiple-point measurement and uses 3D mapping software that shows the bin’s topography to provide volume precision that is better than single-point measurement devices.
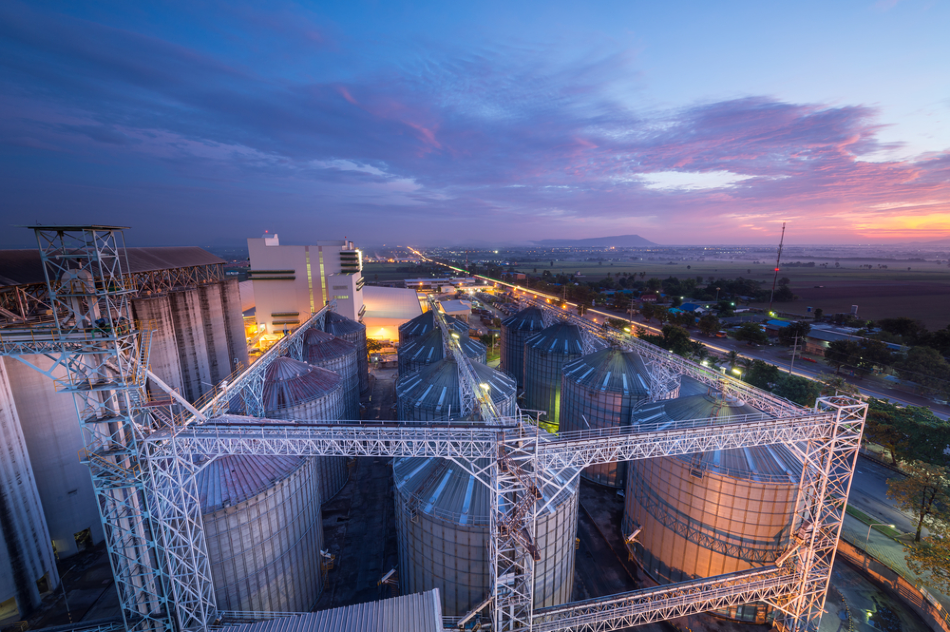
Image Credit: Shutterstock/worawit_j
Volume Accuracy
3D technology provides a volume accuracy of approximately 0.5% to 3%, when placed in an appropriate location and utilized in a bin measuring less than 45 ft in diameter. For bins measuring more than 45 ft in diameter, accuracy of volume decreases but will still be more precise in contrast to other single-point devices. Reduced accuracy in wider bins is attributed to the fact that the device gives out acoustical pulses within a 70-degree beam angle. Accuracy will therefore be reduced if the entire surface of the material is not covered. Alternatively, more than one 3D device will be required in the bin to cover the whole material surface. Also, placing the device in inappropriate location will affect accuracy. Other factors that may affect accuracy are extreme noise during filling process that can disrupt acoustical pulses, and obstructions in the bin that may intrude with the signal.
.jpg)
3D scanning device.
3D Technology
Usually, a single-point device will provide 5% to 7% accuracy when placed 1/6” from the external diameter in a center-fill, center-discharge bin. Guided radar-type devices or weight- and cable-based sensors offer this level of precision. Certain devices, such as ultrasonic or radar, claim down to 1”; however, this applies only for that single point in the silo. Alternatively, some technologies may not be this precise when there is dust in the bin.
Principle Operation of 3D Technology
A scanning device transmits acoustical pulses of low frequency and receives echoes of the pulses from numerous points in the bin. 3D technology takes measurements from numerous points inside the bin and utilizes these points to calculate the level as well as the volume of material in the bin, unlike most devices that measure one point and calculate a single distance. 3D technology uses low frequency pulses that work in dusty conditions and can even be used on cement and flour. It is a self-cleaning device and requires very minimum maintenance.
3D Mapping
When there is numerous filling or emptying points or an up or down cone, the material will build up in sidewalls. If the material is in powder form then it is prone to bridging. This can promote irregular material topography where there will be points in the bin that are either higher or lower when compared to the majority of the bin contents. Taking a single measurement at a random point may not actually represent the volume of material left in the bin. This problem is overcome by 3D technology that takes multiple-point measurements and provides minimum, average and maximum distances that are determined based on real measurement points.
3D Technology for Silos
For the scanning device, the optimal mounting location is ascertained by utilizing a program that takes the size of the bin and creates a drawing. This drawing depicts the mounting location that will offer excellent precision. Then the scanning device is positioned on top of the bin by employing a mounting plate, which makes certain that the device is completely level.
Benefits of Improved Accuracy
Whether facilities are looking to monitor the inventory of plastic resins in small silos or the quantity of corn in a bushel bin, better accuracy has become a new standard. In most operations, reduced accuracy can prove costly. Plant personnel are looking for ways to boost inventory turns, cut down carrying expenditures, and optimize procuring cycles and delivery logistics. 3D accuracy can aid in explaining the differences by tracking changes in build-up and bin topography, and simultaneously help plant managers to schedule maintenance and minimize downtime.
Conclusion
No level measurement device can provide 100% volume accuracy. Hence, it is essential to understand how much precision is required for a particular operation, and then calculate the cost of achieving better accuracy against the value of the operation. For optimum results, it is necessary to know the exact specifications of silos, to apply strapping tables so as to account for variations in bulk density across the silo, and have the perseverance to perfect the technology to suit specific silo parameters. For plants seeking improved accuracy, 3D technology provides an ideal solution as it offers volume accuracy that is better than other single-point level measurement devices.
.bmp)
This information has been sourced, reviewed and adapted from materials provided by BinMaster.
For more information on this source, please visit BinMaster.