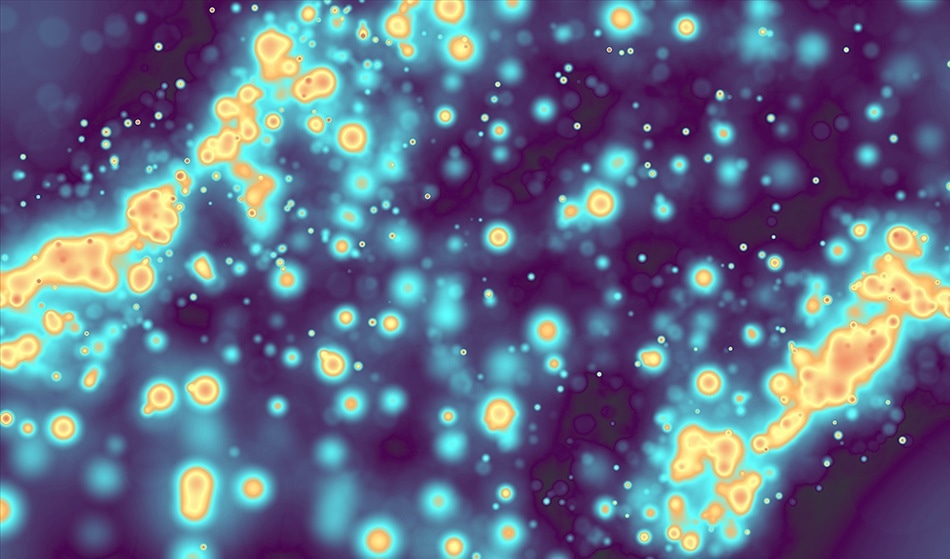
HaHanna/Shutterstock
Thin films are becoming widely-used across a range of different applications. The switch from bulk materials to thin films has arisen in many industries thanks to advancements in bottom-up fabrication methods and the utilization of nanomaterials. In this article, we look at one of the application areas that benefits from thin films, sensors, and explore why thin films are used in many different types of sensors.
Why Thin Films Are Used in Sensors
A thin film is a deposited formulation, coating or layered material that has a thickness ranging from less than a nanometer (i.e. an atomic monolayer) to several micrometers. There are many ways that a thin film can be fabricated, depending on the type of sensor, and these range from chemical vapor deposition (CVD) methods, physical vapor deposition (PVD) methods such as sputtering and molecular beam epitaxy, atomic layer deposition (ALD) and various conformal and non-conformal coating techniques.
Thin films have found an array of uses in sensor technology, because they are more sensitive to changes in a local environment than many bulk materials. The thin nature of these sensors means that they often have a high relative surface area, can be deformed a lot more easily than bulk materials, and the small changes in a film’s conductivity and/or resistivity are much more noticeable. All of these properties are perfect for use in various types of sensing tasks, e.g. for absorbing (or desorbing) molecules on a surface more easily, for use in flex sensors, or for withstanding high temperature environments. This versatility – along with the fact than film sensors can be fabricated at much smaller sizes - is why thin films are being used more and more.
Types Of Sensors That Employ Thin Films
Thin films can be created from a wide range of materials, including (but not limited to) polymers, nanomaterials, oxide complexes, thermoelectric materials and silicon-based materials. Therefore, thin films can be tailored to suit a wide range of applications by varying the composition (and therefore the properties) of the thin film. Here, we look at a few of the different types of sensors that benefit from the use of thin films.
Gas Sensors
Thin films can be used to determine the concentration of a wide range of gaseous molecules and volatile organic compounds (VOCs) in an environment, including oxygen, nitrogen dioxide, organic amines, ammonia and ethanol, to name a few. Thin films have a high surface area for gaseous molecules to bind to, and upon absorption, a change in the conductivity and/or resistivity occurs within the thin film. This change is measurable even with small localized changes, and the number of absorbed molecules is relative to the change in conductivity/resistivity (i.e. a greater amount of absorption equates to a greater electrical change, and vice versa), which enables the concentration of these gases to be deduced.
Strain Sensors
The thin nature of thin films enables them to be flexed and strained much more than bulk materials. They are also a lot more stable and resistant to fracture than bulk materials. Thin films can be used to measure localized strain, such as in some wearable devices or strain gauges in the construction industry. As the film becomes strained, the deformation causes the electronic properties of the film to change, which enables any strains, stress or abnormal movements to be measured and monitored.
Heat-Flux Sensors
Thin films have been employed in a few different types of heat-flux sensors; namely, thermopile-type and RTD-based heat flux sensors. In the case of thermopile-type sensors, thin film thermocouples are used to measure the temperature difference across an insulating area with a defined thickness, and higher sensitivities can be achieved by using more thermocouple pairs along the temperature monitoring path. In RTD-based sensors, thin film RTD’s are used to measure the temperature difference across a defined area of insulating material. RTD-based thin film sensors are easier to fabricate and possess a larger signal than thermopile-type thin film sensors.
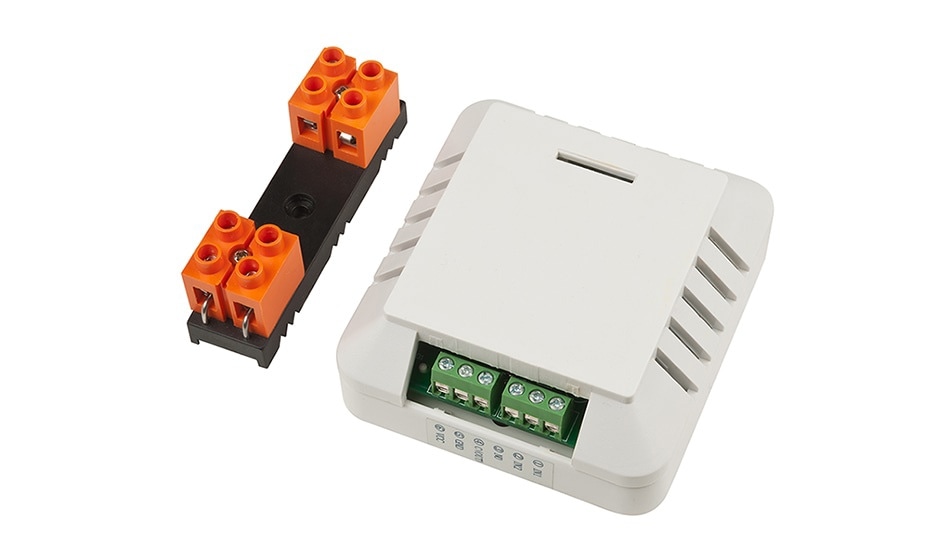
Valt Ahyppo / Shutterstock
Humidity Sensors
In a similar fashion to gas sensors, thin films can be used as the sending component to measure the relative humidity of an environment. As relative humidity is dependent upon how many water molecules are in the atmosphere, the high surface area adsorbs water molecules, which causes a measurable and quantifiable change in the conductivity/resistivity of the thin film. This enables the relative humidity of an environment to be processed as a function of the concentration of water molecules.
Corrosion Sensors
Thin films can also be employed in sensors which measure multiple parameters to determine whether a coating has become degraded, even at early stages. These sensors can measure the temperature, moisture, pH and chloride content of a coating and its surrounding environment, all of which can be used to determine the time to corrosion initiation, corrosion by-products and corrosion rate of a coating. These sensors use an electrochemical mechanism to see if any oxidation or reduction has occurred on a coating by producing a current that is linearly proportional to the gaseous by-products of these reactions.
Sources
- NASA: https://www1.grc.nasa.gov/research-and-engineering/physical-sensors/
- “Thin films of In2O3/SiO for Humidity Sensing Applications”- Arshak K. and Twomey K. T., Sensors¸ 2002, DOI: 10.3390/s20600205
- “Stretchable, Skin-Mountable, and Wearable Strain Sensors and Their Potential Applications: A Review”- Sitti M. et al, Advanced Functional Materials, 2016, DOI: 10.1002/adfm.201504755
- “Thin film sensors for measuring small forces”- Schmaljohann F. et al, Journal of Sensors and Sensor Systems, 2015¸ DOI: 10.5194/jsss-4-91-2015
- “Highly Selective and Sensitive CdS Thin Film Sensor for Detection of NO2 Gas”- Patil V. B. et al, RSC Advances, 2014, DOI: 10.1039/C4RA06531J
- “Thin Film Sensors In Corrosion Applications”- Reiner L. and Bavarian B., CORROSION 2007, 11-15 March, Nashville, Tennessee
- “VOx thin films for gas sensor applications”- Schneider K. et al, Procedia Engineering¸ 2015, DOI: : 10.1016/j.proeng.2015.08.1009
Disclaimer: The views expressed here are those of the author expressed in their private capacity and do not necessarily represent the views of AZoM.com Limited T/A AZoNetwork the owner and operator of this website. This disclaimer forms part of the Terms and conditions of use of this website.