The functionality of a polymer can only be understood when its chemistry and surface topology have been well studied. Polymers are utilized in a host of areas and applications, including many protective coatings and films, and in all these cases surface properties and interactions at the interface are crucial.
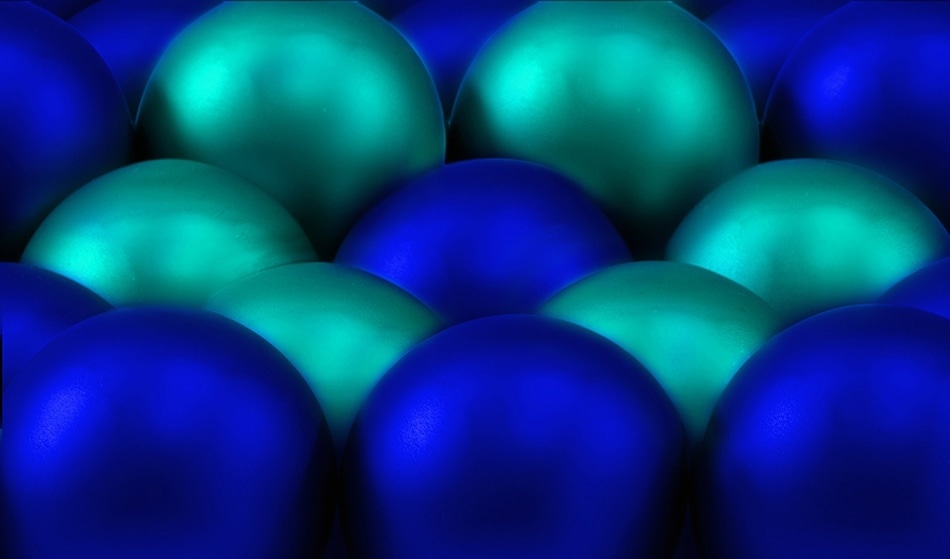
Image credit: photoinnovation/Shutterstock
Scanning electron microscopy and transmission electron microscopy are standard techniques used for the study of surface features. Both are based on the use of an electron beam to scan the surface of the sample. However, the risk of damaging the sample and the restriction of the final image to two dimensions are serious limitations of these methods. This, therefore, led to the development of atomic force microscopy (AFM).
AFM is derived from the use of interatomic forces to model the surface of the sample. It preserves the sample in an intact form, as well as providing a three-dimensional map of the surface. It is a modification of the scanning tunneling microscope and was introduced in 1986 by Binnig and Quate.
The AFM has now become vital in biological studies, polymer sciences, material sciences, and pharmaceutical studies.
Basic Principle
The various components of the AFM include the following:
- Cantilever - a very flexible spring that provides the change in position during the scanning of the sample surface by the probe or sensor tip
- Probe Tip - senses the surface characteristics
- Laser Diode - emits the optical beam
- Mirror - redirects the reflected beam to the photodetector
- Position-Sensitive Photodetector - measures the cantilever deflection
- Piezoelectric Scanner - positions the sample to an accuracy of within Angstrom units
- Computer - controls the setup and carries out the acquisition, display, and analysis of data
Working of the AFM
The probe tip of the AFM is attached to a spring cantilever. When the tip is brought close enough to the surface to be within the interatomic separation distance, the atoms on the sample surface and the probe tip interact at an atomic level. These interatomic potentials cause the vibrating cantilever to deflect in accordance with the sample surface topography. This can be converted to a visual map of the surface.
A laser beam is directed at the cantilever tip, and the reflected beam changes position with the deflection of the cantilever. This is picked up by a photodetector. The sample holder is an important component that uses the sensor output as feedback to keep the sample surface within a predefined interatomic distance, via a piezoelectric scanning tube.
The cantilever motion is converted into the final three-dimensional image, and this is often achievable at atomic resolution with the use of the laser beam.
Imaging speed increases with the resonance frequency of the cantilever. By reducing the cantilever size or by selecting the right material, the frequency can be modulated, and the image quality, as well as the signal-to-noise ratio, can be enhanced as well.
Sensors in AFM
The sensor or probe tip is all-important in the functioning of AFM. While most AFMs currently make use of micromachined force sensors produced from silicon crystals, more and more machines are switching to piezoelectric quartz sensors, especially when a vacuum is in use. These are self-sensing and are found in two types: a needle sensor and a qPlus sensor. These are based on a length-extensional resonator and a tuning fork, respectively.
Self-Sensing Force Sensors
Self-sensing force sensors make it easy to convert a scanning tunneling microscope to an AFM. The qPlus types use one prong of a tuning fork, which is attached to a solid mount while the other prong bears the sensor tip. These have made it possible to reduce the costs, and achieve small amplitudes of cantilever oscillation by increasing the stiffness. This allows an improved signal-to-noise ratio, with higher sensitivity to short-range interactions between the sample surface and the tip.
Self-sensing qPlus probes can use a variety of materials for the tips and have compact dimensions. They may be built even in local labs. Their imaging speed is vastly improved. Moreover, the measuring head is now the moving part rather than the sample stage, which allows the structure of the AFM to be simplified and the scale reduced. In addition, the need for calibration is avoided, though required with optical AFMs.
However, the assembly of qPlus probes at a local level may lack repeatability and reliability. This is because the complex sensor architecture makes the outcome very much dependent upon the expertise of the individual who assembles it.
The use of soft silicon cantilevers completely immersed in liquids was introduced when scanning biological samples, to minimize the interaction force and avoid sample damage or permanent deformations. Softer levers are better at sensing deflection.
However, studies show that the stiffer qPlus sensors can be used with frequency modulation AFM to achieve submolecular resolution on biological samples. Here the sensor is made to oscillate at a selected amplitude, and the frequency shift is measured as a reflection of the force gradient between the sample surface and the tip. Optimal imaging is achieved by the maximum detectable force gradient possible with the least instrumental noise.
Whereas the use of a soft cantilever driven through the liquid by a mechanical drive leads to the production of a ‘forest of peaks’ around the resonance frequency, the use of a stiffer sensor avoids this effect and produces more stable feedback by a monotonic phase response. This can be combined with piezoelectric detectors in vacuum to achieve amplitudes smaller than 100 pm, which is more sensitive to short-range forces.
Multiple Sensor Arrays
Another improvement envisaged in AFM is in the use of multiple sensors in the piezo controller regulating the vertical z-movement of the sample stage. Here there is an inner-outer control setup which minimizes the results of high-frequency dynamics that could produce artifacts in images. This is expected to improve the performance of imaging.
Nanomechanical Cantilever Sensors and Microcantilever-Based Biosensors
Chemical interactions between the AFM and the sample surface can be studied using nanomechanical cantilever sensors (NCS) and microcantilever-based biosensors (MC-B), which allow simple, cost-effective in situ detection of specific chemicals with high speed and sensitivity during chemical force microscopy (CFM). These AFM tips are specially designed by chemical modification to have specific functional groups carefully exposed to pick up certain groups and orientations of molecules on the scanned surface. These sensors transmit the data on the chemical properties they detect into other signals like electrical conductivity or resistance, for instance. This could provide a powerful tool to study surface chemistry and forces between atoms in both biological and inorganic samples.
Sources
Disclaimer: The views expressed here are those of the author expressed in their private capacity and do not necessarily represent the views of AZoM.com Limited T/A AZoNetwork the owner and operator of this website. This disclaimer forms part of the Terms and conditions of use of this website.