Shape memory alloys (SMA) are an amalgamation of metals that can remember their shape; upon heating, a deformed SMA will return to its original configuration. They have applications in biomedicine, robotics and the automotive and aerospace industry as lightweight, solid-state alternatives to conventional actuators.
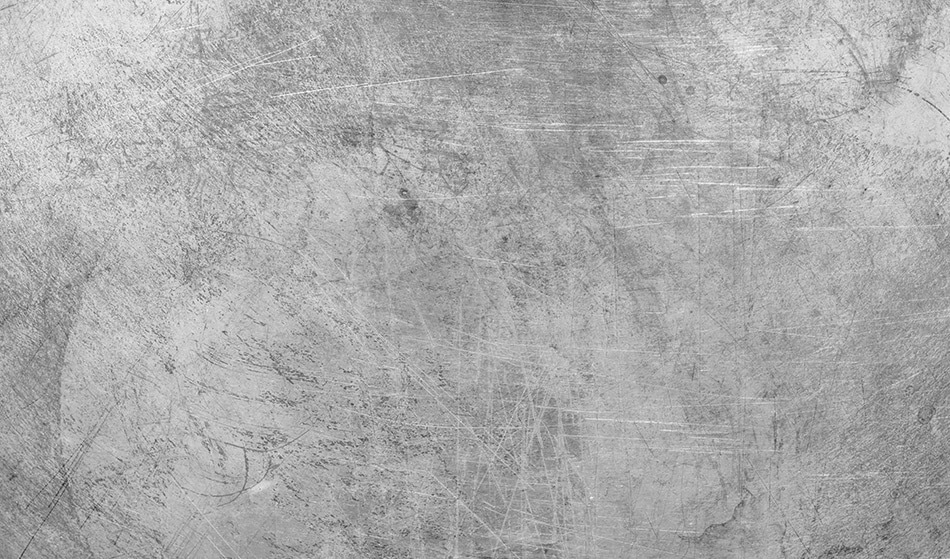
mxbfilms/Shutterstock
Also known as a smart metal, SMA’s are often made of copper-aluminum or nickel-titanium alloys, but zinc, gold, and iron may also be used. Iron and copper-based SMAs are available commercially and relatively cheap, but nickel-titanium is the preferred choice as it is more stable, practical and offers superior thermo-mechanic performance.
The crystal structure of an SMA changes upon heating; nickel-titanium for example, changes martensite - a robust crystalline structure – to austenite, a gamma-phase, upon heating. As it changes shape in response to a temperature change, the SMA is acting not only as an actuator but as a sensor too. They combine significant motion, high forces, and small size to produce a substantial work output, and their fast response to change means they can be used in applications including thermal compensation, thermal actuation, and thermal protection.
SMAs offer new possibilities for the intelligent design of sensor-actuators; they are capable of changing their shape in many ways, with the shape memory effect employed to generate motion and force in actuators, fastenings, and couplings.
Indeed, SMAs have already been employed in force sensing. The variation in electrical resistance in an SMA wire with a passive bias allows the SMA to act as an actuated sensor for a contact force. It can provide an accurate static and dynamic force measurement
Medical Applications
The use of SMAs has shown great promise in minimally invasive surgery and therapy as actuators and strain sensors. Surgeons require flexible instruments capable of measuring tool-tissue contact forces which are low cost, biocompatible and lightweight as an alternative to their large, cumbersome existing robotic equipment. One research project has developed a novel ultrathin strain sensor, using a superelastic wire to measure the strain and forces for many surgical and intervention instruments; with its force sensing capability validated using sensorized surgical equipment.
SMAs have been employed in the tips of active or robotic catheters to help provide positional feedback to maintain control and ensure positioning, especially in the heart. The sensors have been designed to be easily integrated onto an active catheter substrate and could help improve medical devices and benefit patient care and safety.
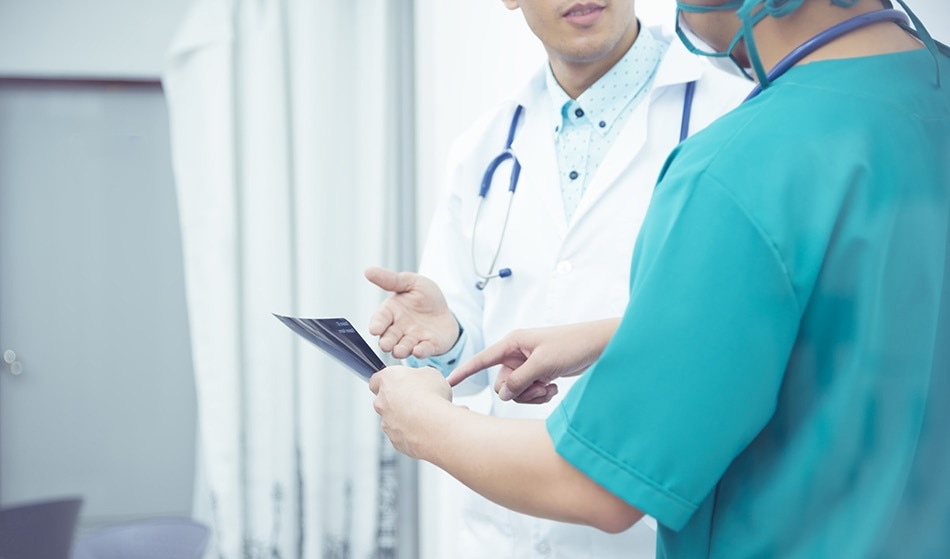
kittipong053/Shutterstock
Another idea under investigation is an actively controlled implantable device for drug delivery. The device contains a microvalve and is capable of delivering small amounts of the drug on a regular basis to avoid multiple injections each day. The valve is topped with a small pincher opened by an SMA wire that contracts when warmed, and the possibility that further sensors might too be incorporated.
Other applications include in a bending actuator for endoscopy - a vertebral design of SMA wires, strips and springs results in a modular actuator capable of navigating the complex system of the intestines – or an endoscopic mirror activator where an SMA wire rolled around a mirror axis causes the mirror to rotate upon heating.
Other uses of SMAs in medicine include as fixation devices for osteotomes (bone lengthening or shortening procedures) or in dental braces to exert constant moving forces on teeth. They’ve even been used in glasses frames which can undergo extreme distortion and still return to their normal shape.
Automotive Industry
Thin film SMAs have been used to develop an environmental pressure sensor for combustion monitoring and control in cars. The sensors are integrated into the engine to monitor combustion in turbine engines continuously, or each combustion event in diesel and spark-ignited engines. Pressure applied to the sensor causes deformation and the film changes from austenite to martensite with the fraction transformed corresponding to the applied pressure. This strain induced sensor has a high response rate, and is immune to temperature fluctuations of the engines are they operate above the local temperature.
References and Further Reading
Disclaimer: The views expressed here are those of the author expressed in their private capacity and do not necessarily represent the views of AZoM.com Limited T/A AZoNetwork the owner and operator of this website. This disclaimer forms part of the Terms and conditions of use of this website.