Pressure Sensors from Dynisco
For more than six decades, Dynisco pressure sensors have been employed in a variety of applications globally. Since obtaining the original patent for the melt pressure sensor employed in extrusion, Dynisco continues to hold its place as the world class industry frontrunner in this technology by working closely alongside its end users to meet the constantly developing needs of the plastics market.
Selection of Diaphragm Material
The application in which it will be employed determines the choice of diaphragm material used on the Dynisco pressure sensor. The first question that should be addressed is whether the sensor will be in contact with a pure material or a blend of materials. Next, the properties of these materials should be considered, with a focus on the classification of the individual polymer components.
The polymer categories are elastomers, thermoplastic elastomers, thermoplastics and thermoset. The polymer families within these categories are Urethanes, Polyesters, Amides and Polyolefins.
Extrusion, injection molding, and compression molding are all methods involved with thermoplastic and elastomer processing, and each makes use of pressure sensors to permit pressure measurement and control.
Features of Dynisco Pressure Sensors
Dynisco pressure sensors have been developed to withstand challenging environments, and, provided the appropriate features are chosen to match the application, can deliver many years of dependable service.
It is important to determine whether the material is abrasive or corrosive, as well as noting the temperatures of the process. For example, if the application makes use of polypropylene, Dynisco would advise the use of its standard diaphragm option on the pressure sensor chosen.
The company’s standard diaphragm is Dymax® coated stainless steel (15-5PH), which holds up well against abrasive material flow, and is a dependable choice in most extrusion environments.
If a process application requires material that will adhere to the standard diaphragm, such as an elastomer (TPE), Dynisco may advise the use of a titanium nitride coating (TiN) to avoid adhesion and minimize the risk of the material deforming the diaphragm.
The standard diaphragm may also be inappropriate in other applications which make use of polymers with corrosive properties and materials such as fluoropolymers (PTFE or FEP). Here, the standard diaphragm’s lifespan may be shortened due to oxidation, and so Dynisco may advise using an alternative diaphragm material, such as an Inconel or a Hastelloy.
Materials and coatings which can be selected for diaphragm construction are:
.jpg)
15-5 PH Stainless steel with Dymax® coating – Delivers robustness with abrasion resistance and is standard on most sensor models.
Hastelloy – Offers resistance to corrosion, but is not recommended for prolonged use in high temperatures.
Inconel 718 – Offers abrasion and corrosion resistance and is recommended for use in temperatures up to 750˚F or higher.
Dymax® – Hard-wearing, and boasts a proprietary surface coating as well as abrasion resistance.
Borofuse – Offers the best abrasion resistance coating available. Can only be used on Inconel.
Titanium Nitride – Abrasion and adhesion resistant. Can be used on most diaphragm materials.
Titanium Aluminum Nitride – Heightened abrasion and adhesion resistance, and comes standard on Dynisco Echo sensors (inconel diaphragm material).
Note* Consult Dynisco for alternative materials and coatings not listed*
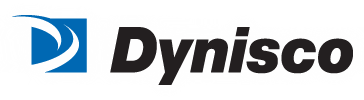
This information has been sourced, reviewed and adapted from materials provided by Dynisco.
For more information on this source, please visit Dynisco.