The word ‘sensor’ refers to a device that offers measurement of a physical value by transmitting this value in the form of a signal output that can be recorded by a user or through instrumentation.
Applications of Pressure Sensors
Pressure sensors are utilized in a number of different applications to assist users in monitoring and controlling process stability, as well as ensuring the safety of equipment.
This piece is focused on the melt pressure transducer employed in plastic extrusion and injection molding. It is seen as vital that the signal output from the sensor should be calibrated with instrumentation to ensure the accuracy and reliability of the pressure measurement.
Calibration of Pressure Sensors Using Dynisco Pressure Transducers
Proper calibration should be carried out with the transducer at rest (no application of pressure) and at operating temperature, to counterbalance temperature impact on zero. Each Dynisco pressure transducer includes a rating of temperature effect on zero, and this rating can vary depending on the chosen fill media in the transducer capillary.
The liquid fill media’s physical features will have an impact on where the zero output level of the signal will be, and this value should be taken into account when determining the range with instrumentation, making adjustments as required to offset this.
This fine-tuning would be comparable to setting a TARE on a balance, where the temperature effect is equal to the package of the product being weighed.
The published temperature effects for the 3 liquid fill options are as follows:
- Hg= 15 psi/ 100 °F or 27 psi/ 100 °C
- Oil= 36 psi/ 100 °F or 65psi/100 °C
- NaK= 30 psi/ 100 °F or 54psi/ 100 °C
With these values in mind, it can be expected that it will be necessary to configure the instrument to accept the signal input as zero by calibrating at the operating temperature of the process.
Example: Process temperature = 400 °F, Hg type sensor showing signal output of 60 psi @ zero pressure*
*Depending on the complete scale pressure range of the transducer, this offset would be on top of the standard combined error specification, so a 10,000 psi range with a 0.5% combined error (+/- 50 psi) would in fact, seem to have an offset of 110 psi or more at any time.
It is key to note that during the process of calibration, no alterations are made to the signal output, with the aim simply being to verify that the output is still within the tolerance limits of the model specifications.
Conclusion
Dynisco instruments have been developed to simplify the process of calibrating pressure sensors. The company’s indicators and controllers can assess the high and low limits of the signal output with just a few key strokes.
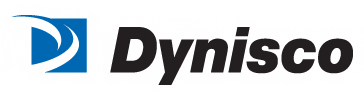
This information has been sourced, reviewed and adapted from materials provided by Dynisco.
For more information on this source, please visit Dynisco.