Article updated on 11 November 2020
Lubricants are vital for any modern industrial equipment with moving mechanical parts, as they are used to reduce friction between the parts (usually made of metal) when they pass over each other. Without lubricants, these mechanical parts would wear, degrade and break down very quickly, and it would soon become a costly endeavor for any company that was using them. However, lubricants themselves can slowly degrade over time, and in this article, we look at the ways in which sensors are used to measure various properties of a lubricant to ensure that it is still fit for use.
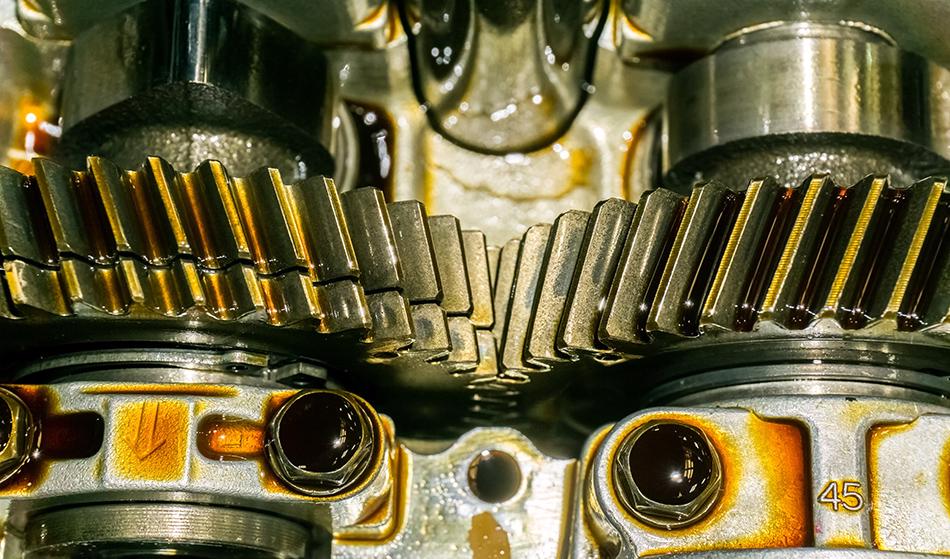
jeab05/Shutterstock
While lubricants are an essential fluid in mechanical systems, they can become less effective over time; the most common cause being the presence of contaminants, which reduce the lubricating effects. If a lubricant is not performing optimally or contains contaminants (especially metal contaminants, which detach from the mechanical parts), then it can cause harm to the mechanical system, and this defeats the purpose of using lubricants in the first place.
In these scenarios, the lubricant must be replaced. However, to ensure that the lubricant does not reach a stage where it will cause harm, it must be monitored—either continuously or at regular intervals. There are many different scenarios and environments that can cause the lubricant to degrade, and so sensors are required to monitor the fluid. In many cases, multifunctional sensors can be employed to measure more than one factor that could impact the lubricants. Below, we look at some of the common parameters that are measured in industrial lubricant systems.
Temperature
Sensors that measure temperature changes can be used in lubricant reservoirs. This is where the lubricant is stored before it is released into the mechanical system, and where it returns once it has passed through the system. Changes in a lubricant’s temperature indicates a change in the lubricant system. This could be caused by something as simple as a leak, to the lack of lubrication at one or more points in the process (the subsequent increase in friction raises the temperature of the lubricant). It could also be caused by the accumulation of dirt or other contaminants, which effectively create a thermal reservoir blanket that causes the lubricant temperature to rise.
Aside from using the temperature as a gauge for problems in the lubricant system, increases in lubricant temperature can significantly reduce the useful life of the lubricant; hence the need for regular monitoring of the temperature through sensors.
Moisture
The presence of moisture in a lubricant is a serious matter, as there are many ways in which water can damage the fluid. Traditionally, lubricants are immiscible with water as they are oils. However, under the shear stresses that can exist in mechanical systems, the presence of water can cause the lubricant to emulsify, free water globules to form in an oil matrix, or dissolve the water into the lubricant; all of which reduce the lubricating properties of the lubricant.
The presence of water can also cause the lubricant to oxidize, changing its chemical composition, and resulting in the depletion of additives and the formation of acids and sludges. The chemical change in the lubricant can also cause degradation of some of the metallic mechanical parts through chemical reactions, which further degrades the quality of the lubricant through the presence of metallic contaminants (see below), as well as potentially rendering the components unusable. Therefore, the use of water sensors when monitoring a lubricant is crucial.
Particulate Matter
Aside from water, other contaminants can be detrimental to lubricants, with two common particulate contaminants being dirt and metal pieces. Metal pieces can be broken off, either over time or as a result of other contaminants, and where a lubricant would normally provide a low-friction barrier between components, friction is actually increased. Additional metallic shards can then also be formed resulting in a circular problem solved only by changing the lubricant to remove the wear stimulus.
Dirt can enter if the lubricant as well if the reservoir is not fully sealed, which can also reduce the lubricating properties; as well increase its temperature. Sensors must be utilized to ensure that there are no particulate contaminants in the lubricant.
Lubricant Levels
Like any system that employs a fluid reservoir, the levels of fluid must be measured and this is no different for lubricant systems. Sensors can be used to measure the level of lubricant in a reservoir to ensure that the levels are between predetermined upper and lower limits.
If the sensors measure the level to be below the lower limit, there could be issues with leakage, oxidation or under-filling, which must be investigated. Likewise, if the reading is above the upper limit, as it could indicate the presence of water or over-filling.
Sources and Further Reading:
Disclaimer: The views expressed here are those of the author expressed in their private capacity and do not necessarily represent the views of AZoM.com Limited T/A AZoNetwork the owner and operator of this website. This disclaimer forms part of the Terms and conditions of use of this website.