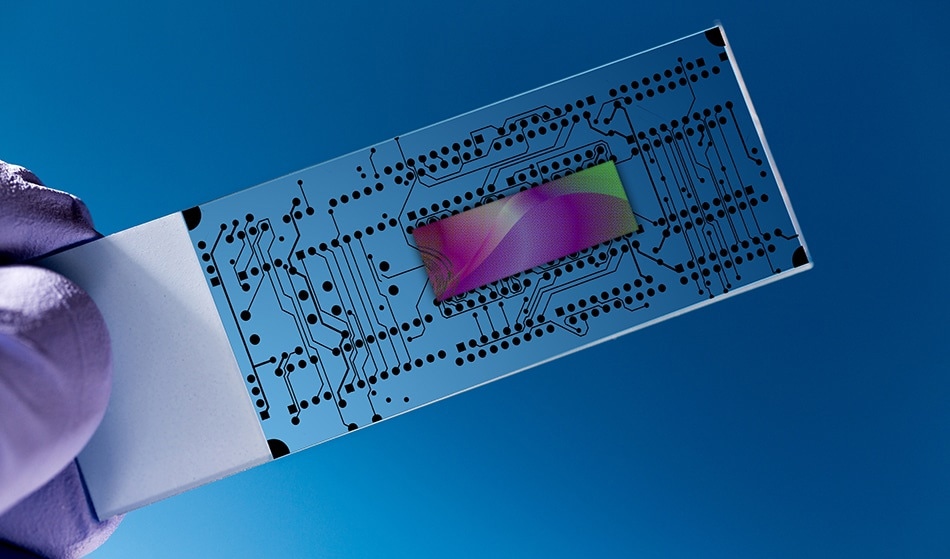
science photo / Shutterstock
MEMS technology has contributed significantly to improving the performance of various devices, while simultaneously drastically reducing their size. While this may be true, the widespread use of these incredible devices in certain areas is hindered by the poor tribological performance and adhesion issues associated with these microstructures.
Research on the tribological properties of these surfaces has led to the development of novel approaches to minimize frictional forces and to improve their performance. Topographical modifications by thin film coating and surface modification seem promising in the development of new and improved MEMS devices.
Micro-Electro-Mechanical Systems (MEMS) are a technology of miniaturized mechanical and electrical elements on the scale of micrometers to millimeters, created using techniques such as microfabrication. This technology is used in various structures and devices incorporated within simple to complex electromechanical systems, some of which include sensors, actuators and microelectronics. MEMS therefore have a wide variety of applications in electronics, the automobile and aerospace industries.
However, the high surface-to-volume ratio in MEMS can result in adhesive and frictional forces, which can ultimately affect the performance of the system. This is especially a problem in actuator-based MEMS, where the frictional forces hinder smooth movement and affect the function of the device. Novel approaches to address the tribological issues surrounding MEMS devices are sought after but still need more work.
Advantages of MEMS
The miniaturization of complex electromechanical structures has several advantages over their macroscale counterparts including smaller size, high-throughput, ease of integration into the electrical circuit, reduced cost and excellent performance.
With the improvements in nanotechnology, MEMS technology has been growing at an incredible pace over the past few decades. To this end, MEMS technology is increasingly used in the manufacturing of sensors, switches, accelerometers, resonators, gyroscopes, pumps and microvalves.
Challenges Facing MEMS Technology
Integrated circuits (IC) are mainly composed of silicon as a result of the well-established manufacturing and fabrication technologies available for this material. While silicon is well-known for several material advantages, it is also associated with poor tribological properties.
Transducers, such as sensors and actuators, are devices that convert energy from one form to another. While sensor-based MEMS primarily based on sensing elements are widely available, actuator-based MEMS are non-existent. The frictional forces resulting from the relative motion in actuator-based MEMS prevent the smooth movement and performance of these devices.
Surface forces, such as meniscus forces, viscous drag, surface tension, friction and adhesive forces, can dramatically alter the integrity of miniature MEMS devices by decreasing the systems’ performance and overall life-span. In particular, capillary forces that arise as a result of meniscus bridges, which form from the condensation of environmental water, are associated with causing the biggest problems in MEMS.
An additional challenge in this area is that conventional liquid and solid lubrication techniques that are typically used to manufacture the macro-counterparts of MEMS cannot be used during the manufacturing of MEMS.
Approaches to Counteract the Tribological Issues in MEMS
With this in mind, it is clear that the surface forces of MEMS should be minimized in order to improve the performance and increase the life span of these devices. Researchers have therefore been investigating several approaches capable of effectively reducing these surface forces, either by modifying the topography or performing chemical modifications.
Topographic modifications involve techniques that are capable of changing the device surface by roughening the surface, texturing the surface and even modifying the local geometry of the surface. On the other hand, chemical modification can involve coating the surface with both natural and inorganic substances to reduce friction and wear.
Chemical modification of the surface of MEMS devices results in an increased lubricity, as well as a reduced occurrence of surface capillary forces from environmental water by increasing the hydrophobicity of the device’s surface. Examples of these types of specialized thin film coatings include ionic liquids (IL), diamond-like carbon coatings (DLC) and self-assembled monolayers (SAM).
The frictional behavior of these microstructures is affected by the speed of the relative motion between the surfaces, rest time and the environment of the microstructures. Tribological modification minimizes these frictional forces to improve the performance of MEMS devices.
Sources
Disclaimer: The views expressed here are those of the author expressed in their private capacity and do not necessarily represent the views of AZoM.com Limited T/A AZoNetwork the owner and operator of this website. This disclaimer forms part of the Terms and conditions of use of this website.