Airborne contaminants such as gasoline fumes, NO2, and CO will always be present until electric cars finally take over. This is because of vehicles situated in underground or otherwise confined parking structures, loading docks, tunnels, and warehouses, which represent an ever-present source of these contaminants.
.jpg)
Clearly, these gases are not wanted and there are a number of reasons for monitoring them in order to prevent potential buildups via ventilation and air changes.
Reasons for Monitoring Airborne Contaminants
Evidently, the primary reason is safety. Involving both staff and the public, parking managers need to guarantee a breathing environment which is safe. Carbon Monoxide is liable to cause headaches and dizziness over 200 ppm, as it is extremely toxic. When concentrations exceed 3000 ppm, it can quickly become fatal.
On the other hand, continued exposure to elevated levels of Nitrogen Dioxide is liable to cause emphysema and chronic bronchitis. If a large number of diesel-powered vehicles are present inside a structure, NO2 is the primary contaminant which must be taken into account.
Benefits and Drawbacks of Ventilation Systems
The majority of international standard and codes stipulate that ventilation must be installed in order to protect against the risk of dangerous levels of contaminant concentration being reached.
Typically, these regulations are intended to keep a maximum CO average of between 25 and 50 ppm across an eight-hour period, while the maximum average concentration must not exceed 200 ppm in short-term exposures. The ventilation which is necessary for the adequate disposal of CO is typically sufficient to make sure all other contaminants are kept at bay.
However, it is neither efficient nor practical to keep a ventilation system running continuously or at fixed intervals, irrespective of the actual concentration of gas. This is a result of energy expenditure, greater wear on the fan motors, and concomitant increases in maintenance requirements.
This means that another major reason for employing gas detection systems and monitoring contaminant levels is financially motivated. Substantial savings can be made in terms of costs in the long term by using automatic contaminant sensing devices, which modulate the ventilation system activation to a minimum.
The last reason for employing such systems is to ensure the quality of the environment, as well as the health of workers and users of the car park. A ventilation system which is continuously running causes great levels of heat and noise to be produced, negatively impacting the overall comfort level of the facility.
Use of Sensors to Control Ventilation Systems
By considering a radius of coverage of 15.2 m (50 feet) per carbon monoxide monitor, or 2,310 m2 (7,580 sq.ft), the quantity of sensors which will be deployed is determined.
CENELEC – EN 50545-1 outlines the general requirements for construction and testing in Europe. It delineates the test methods which are used on fixed apparatus for the detection and/or the measurement of nitrogen monoxide (NO), carbon monoxide (CO), and nitrogen dioxide (NO2) in tunnels and car parks.
Its intention is to control ventilation systems and/or to provide indications, alarms, or other signals which provide advanced notice of toxic hazards.
N.E.T Flat line and Safety line electrochemical cells are made in such a way that they meet or exceed the EN 50545-1 specifications (for repeatability, linearity, humidity and temperature dependence, recovery from high gas concentrations, interfering gases, response time, and long-term stability). They are tested and approved with a Certificate No. S 459 2014 C2 by TUV Rhineland.
Typical Gases (RANGES/TLV)
- CO (300 ppm)
- NO (100 ppm)
- NO2 (30 ppm)
- CO2 – 0.5% (5000 ppm)
- C6H14 – Hexane (50 ppm)
Products
- SAFETY LINE
- FLAT LINE
- IRNET-P 32 mm
- IRNET-P 20 mm
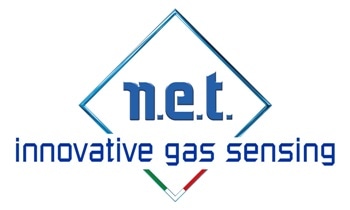
This information has been sourced, reviewed and adapted from materials provided by Nano Environment Technology (N.E.T).
For more information on this source, please visit Nano Environment Technology (N.E.T).