Differential pressure sensors may be required to function under fluctuating temperatures, through strong vibrations or in dusty air. Regardless of your environment you will usually find an accurate and reliable pressure sensor that is suitable for your specific conditions. However, be sure to carefully check whether your chosen differential pressure sensor complies with the tolerances that you have defined for your application in all relevant parameters. Such information can be found on the product data sheets issued by the manufacturers. These data sheets provide a specific overview of all important decision parameters. A few guidelines are detailed below to help you make sense of this data.
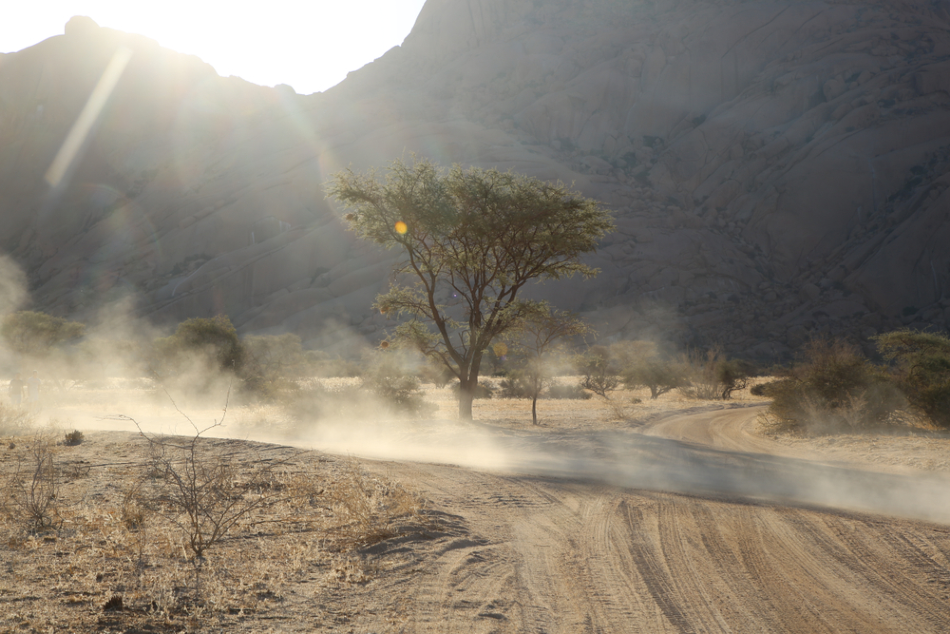
Image Credit: Shutterstock/Evert Vorster
Overall Accuracy
The maximum total error is the sum of all the individual error variables that may occur in a sensor over the entire temperature range. This is known as the Total Error Band (TEB). To give an example, with First Sensor all error variables (such as offset and sensitivity calibration, offset and sensitivity temperature dependence, non-linearity and hysteresis) are incorporated in the overall accuracy.
One thing to be aware of is that many applications will only tolerate a minimal total error within the working temperature range.
Temperature Errors
Piezoresistive differential pressure sensors use silicon as the semiconductor material which is temperature-dependent. This means that any change in temperature could potentially alter the measuring behavior of the sensor and lead to temperature-induced zero offsets and span errors. The mechanical functionality of electrical connections or cables may also be affected by temperature - 100 °C is the absolute maximum for most standard materials.
A temperature error demonstrates the greatest deviation of the sensor characteristic curve from a reference temperature within the compensated temperature range. The zero-point (offset) temperature error and also that of the span should be considered individually. A temperature coefficient of % per °C is often used to express the temperature error.
Temperature compensation is used to adapt the differential pressure sensor to specific temperature conditions. As such, you should first define the expected operating temperature before deciding on a particular differential pressure sensor.
Position Sensitivity
Piezoresistive silicon pressure sensors have a very thin and highly sensitive diaphragm to enable them to operate at ultra-low pressure ranges of just a few millibars. In some cases the diaphragm may also react sensitively to sensor movements and vibrations which may impact on the stability of the sensor output signals and cause zero offsets.
Special compensation technology can be used to eliminate the zero offset in a moving situation if you do want to use a highly sensitive ultra-low pressure sensor.
Calibration
To ensure quality measurements from the pressure sensor long term a complete calibration (traceable to national standards) is not only important but also a fundamental part of ISO 9001 certification. The starting calibration will deteriorate over time with aging materials and the influence of ambient conditions.
A pressure sensor is unable to provide long-term reliable, exact, comparable or usable measurements without calibration. A regular zero point calibration is recommended more frequently in working environments with greater stress.
Measurement Range
Both thermal and piezoresistive differential pressure sensors are sensitive to even the smallest pressure loads or differential pressures. However, differential pressure sensors also experience ambient pressures. These are determined by the over- load limit and burst pressure of the sensor.
The overload range determines the level of ambient pressure that a differential pressure sensor can tolerate without permanent changes to its electrical properties. The sensor is at risk of being damaged when the ambient pressure exceeds the “overload limit”. However, the sensor may be destroyed entirely if the burst pressure is exceeded.
Long-Term Stability
The maximum change of the zero point and output span is examined under laboratory conditions over a one-year period to determine the long-term stability. This is then reported as a percentage. The long-term stability will be impacted by excessive temperatures, mechanical loads and other operating stresses. Infinite long-term stability is not possible even if manufacturers and users are careful.
The Sensor Design
The level of sophistication in a sensor design will ultimately affect the quality of a differential pressure sensor. An optimally tailored design in terms of material, shape and processing will ensure that a sensor will deliver long-term reliable and precisely measured values. Likewise, a good connection design will also ensure simple, smooth and safe installation and commissioning - regardless of whether a sensor is soldered to printed circuit boards, installed in a manifold or connected with a screw thread.
Mechanical connections:
- Screw threads
- Manifold connection
- Hose connection
- Etc.
Electrical connections:
- Plug-in connection
- Soldering on board
- Direct cable outlet
- Etc.
Conclusion
Choosing a differential pressure sensor is not an easy process. Firstly, the choice is so great. On the other hand, the pressure sensor is often such an important system component that you simply cannot afford to make the wrong decision.
Therefore manufacturers such as First Sensor make sure you’re not on your own when you choose a sensor.

This information has been sourced, reviewed and adapted from materials provided by First Sensor AG.
For more information on this source, please visit First Sensor AG.