As contamination is one of the most frequent causes of mass air flow sensor failure and malfunction, especially for sensors in unhygienic environments such as car engines, knowing how to test mass airflow sensors, and how to clean mass air flow sensors is a beneficial method of extending their lifetimes.
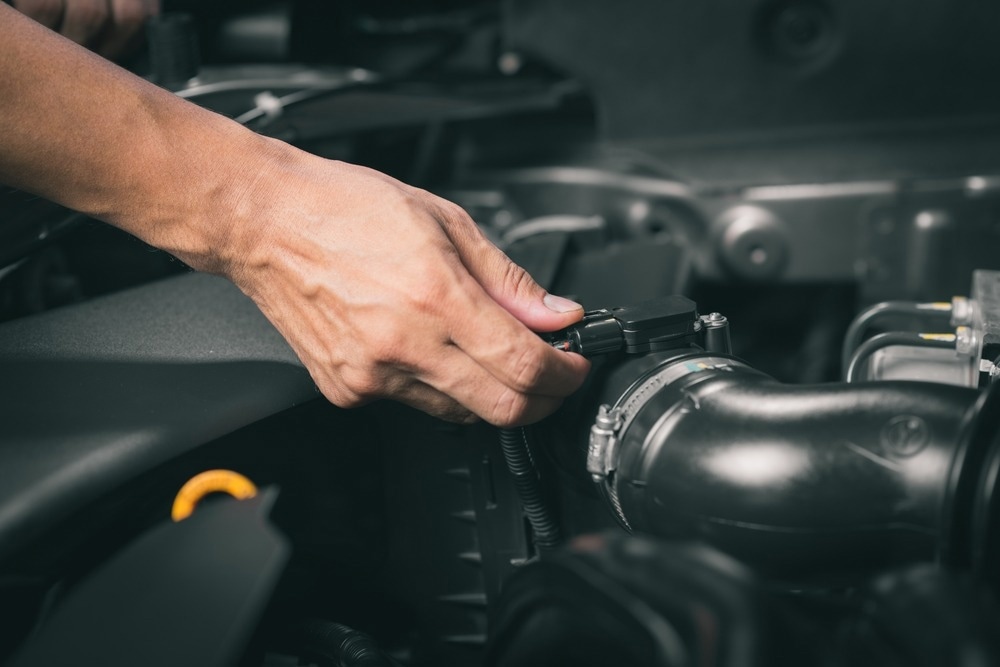
Image Credit: Nor Gal/Shutterstock.com
Cleaning Mass Airflow Sensors
The main reason that hot-film and hot-wire type sensors require cleaning is due to oils, dust, and other particles that collect onto the films or wires; adjusting their resistivity. To analyze mass airflow sensors, one wire (or surface) is utilized as a reference, and the other is left vulnerable to incident airflow.
As mass airflow (MAF) is determined by a difference in resistivity between the reference and exposed wires, any factor that influences this will result in inaccurate readings.1
While several modern sensor designs (for example, microcontroller-based mass air flow sensors) try to reduce exposure to possible contaminants, even these devices will require cleaning from time to time.
Download the Full eBook Here
Chemical solvents are one cleaning agent option, however, care should be taken to make sure that they do not react with the sensor housing or the sensor itself. For example, toluene is very incompatible with most of the plastics employed in sensor housings and should therefore be used with care or avoided.
There are several commercial cleaners sold as mass airflow (MAF) sensor cleaners that are commonly purchased as sprays. Many of these are made from methanol which will generally dissolve molecules such as hydrocarbons that have built up on the sensor, without causing damage to the sensor itself.
Another important feature that should be considered when choosing a mass airflow sensor cleaner in the selection of sensor-cleaning solvents, is whether or not they leave a residue when they dry. Volatile compounds such as acetone, isopropyl alcohol, and methanol are commonly preferred for their quick-drying qualities; however, the solvents must be of adequately high purity so that they do not leave a residue once they have evaporated. Denatured alcohol should be avoided for this reason.
Mass airflow sensors must be delicately wiped with clean high-grade tissue to reduce scratches, and one should always avoid scrubbing as this may break parts or otherwise cause damage.
In the case that cleaning the mass airflow sensor does not create an improvement in performance or a correction of previous issues, the air intake filters should also be examined. This is because contaminated filters can add to the quick re-contamination of sensors or can enhance limited air intake from blockages. These issues may appear with the same symptoms as a malfunctioning mass airflow sensor.
How To Test Mass Airflow Sensors
Mass airflow sensor testing performs two purposes. The first is to verify that the device definitely works at its desired specifications, and the second is to define the working specifications.
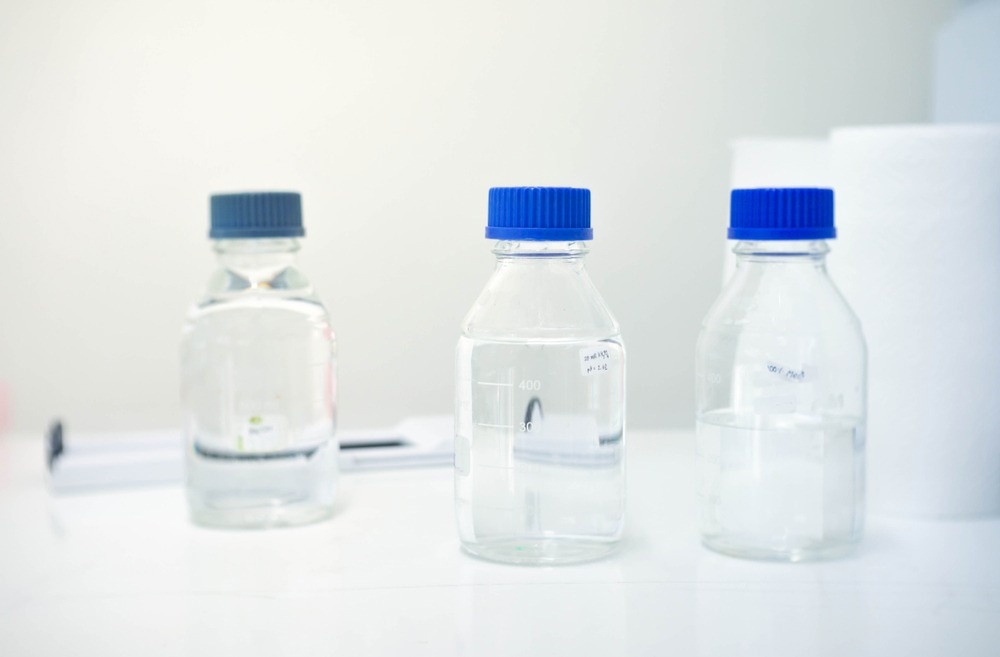
Image Credit: Charoenrak Sonthirat/Shutterstock.com
Testing also offers the chance to carry out any required calibrations. Mass airflow sensor performance is often characterized by frequency testing, especially for hot-film or hot-wire based systems.
Although the features of interest are commonly time-dependent, for example, the MAF sensor response time, direct measurement in the time domain for mass air flow sensors presents multiple technical limitations. These issues mostly arise from the fact that the sensor response is reliant on the mass airflow. Therefore, a single-time measurement is not a valid representation of sensor performance in every condition. Changing the steps in airflow can also be challenging as well.
The output voltage from the mass airflow sensor can be measured under various conditions by using variable airflow and a test signal as inputs. By observing the frequency response and phase, an inverse transform can then be applied to change this into a time-domain measurement.
Characterizing mass airflow sensor response times is highly essential for mass air flow sensors because, for multiple applications, the sensor must be able to detect any instant real-time variations in mass airflow. This is important for the efficient running of an engine or for artificial ventilation, where the airflow produced has to be in harmony with the patient’s breathing.
Alternative properties that are commonly tested are the airflow range over which the sensor can operate, the dynamic range or sensitivity of the sensor, and the stability of the sensor in relation to environmental conditions.
Multiple modern mass air flow sensors provide temperature-compensated outputs over a particular range, meaning that any readings are instantly adjusted for temperature changes to ensure higher accuracy.
Testing for malfunctioning or sensor failure can be performed by testing the resistivity of the reference and exposed wires for hot-wire sensors. A shorted sensor or a snapped wire should read infinite resistance and signifies the critical issue of mass airflow sensor failure.
Another method is to connect the sensor to an oscilloscope and, for sensors on engines, operate the engine under snap conditions of acceleration. Once the pressure in the mass air flow sensor is the same as atmospheric pressure, the airflow speed should be in proportion to the speed of the engine.
The output voltage throughout acceleration should also reach a value similar to the highest engine load. As contamination on the sensor begins to increase, these values under various conditions will adjust and begin to deviate.
Consistent cleaning can help to correct the majority of these issues, and various approaches to sensor testing can be beneficial diagnostics for establishing the source and magnitude of any issue with the mass air flow sensor.
Download the Full eBook Here
References and Further Reading
- Fleming, W. J. (2001). Overview of Automotive Sensors. IEEE Sensors Journal, 1(4), 296–308. https://doi.org/10.1109/7361.983469
- Asad, U., Kumar, R., Han, X., & Zheng, M. (2011). Precise instrumentation of a diesel single-cylinder research engine. Measurement: Journal of the International Measurement Confederation, 44(7), 1261–1278. https://doi.org/10.1016/j.measurement.2011.03.028
- Solvent Compatibilities (1975), https://apps.dtic.mil/dtic/tr/fulltext/u2/a305226.pdf
- Mass Air Flow Cleaner MSDS (2019), http://docs.crcindustries.com/msds/5110.pdf
- Bugli, N. J., & Green, G. S. (2010). Performance and Benefits of Zero Maintenance Air Induction Systems. SAE Technical Paper Series, 1(2005), 1015–1028.
- Ziesmer, D. A., Chuey, M. D., & Hazelton, L. (2010). Frequency Domain Characterization of Mass Airflow Sensors. SAE Technical Paper Series, 1(1988), 987–995. https://doi.org/10.4271/930325
- Freymuth, P. (1977). Frequency response and electronic testing for constant-temperature hotwire anemometers. Journal of Physics E: Scientific Instruments, 10(7), 705–710.
Disclaimer: The views expressed here are those of the author expressed in their private capacity and do not necessarily represent the views of AZoM.com Limited T/A AZoNetwork the owner and operator of this website. This disclaimer forms part of the Terms and conditions of use of this website.