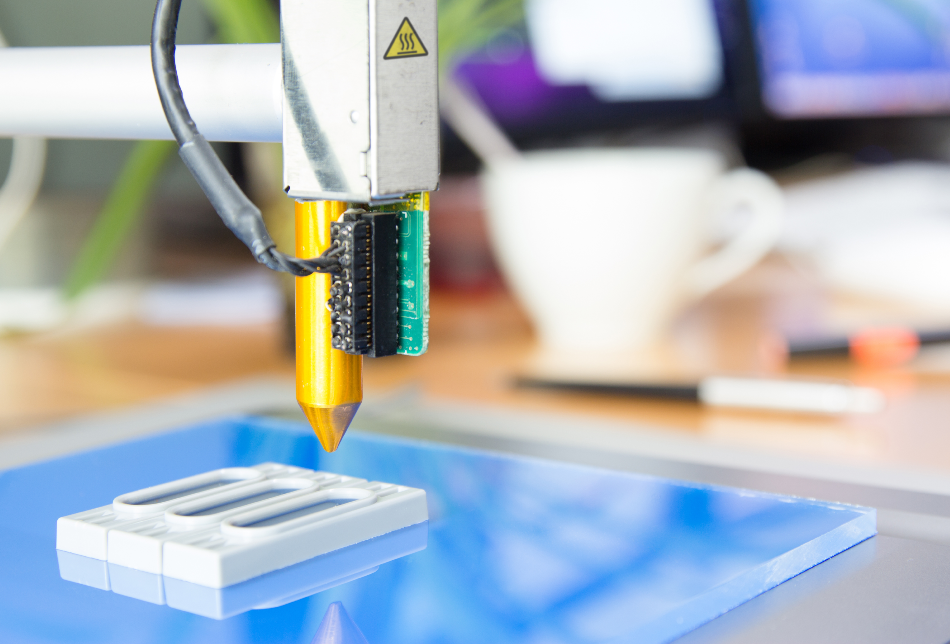
Alexander Kirch / Shutterstock
In April of this year, engineers based at Virginia Tech have shown that electronic sensors can be successfully printed using a conformal 3D printing technique. The potential applications for such a method are vast, their advancement will influence future smart objects that could be printed with electronic sensors embedded in them. The scientists at Virginia Tech focused their research on the 3D printing of advanced prosthetics with integrated sensors to improve on their function.
The Advent of Electronic Sensor Printing
Back in 2012, a team of researchers at the University of Warwick in the UK devised a conductive composite material that was successful as a medium to 3D print electronic sensors. The sensors they created had the capacity to sense capacitance change and mechanical flexing and was low cost enough to be viable for commercial production purposes.
The researchers, led by Simon Leigh, innovated a system of producing custom sensing devices that could be embedded within printed objects. They termed the word ‘carbomorph’ to describe the method of printing a simple conductive thermoplastic composite to create an embedded sensor. They saw the implications of their work influencing the future capabilities of 3D printed smart objects.
3D Printing Smart Objects with Integrated Sensors
This year, a team at Virginia Tech successfully established personalized wearable system interfaces in 3D printed prosthetics. They identified how state-of-the-art prosthetics contained these systems which were, until this point, not available in 3D printed versions. The team showed how 3D printed prosthetics were able to be improved through the integration of printed electronic sensors.
Through a system of printing sensors within the prosthetic, the engineers were able to insert them at the place of the intersection between a prosthetic and the wearer’s tissue. By doing this, researchers could collect data related to the prosthetic’s function and comfort such as measuring the pressure across the tissue. The data was then analyzed in order to inform on how the prosthetic could be developed to fit and function better.
A form of 3D printing called conformal 3D printing was used to integrate the sensors into the material during printing. Through the ability to print the sensors directly into the material, rather than inserting them afterward, engineers were able to control aspects such as tissue hardness, allowing them to create sensors that blend in with the prosthetic. In addition, they were able to insert the sensors in difficult locations.
The team began with a goal to create a prosthetic for Josie Fraticelli, a local teenager. They took a 3D scan of a mold of Fraticelli’s limb and used this data to inform where the sensors would be best integrated into the form-fitting cavity of the prosthetic. Using conformal printing they created the prosthetic with integrated sensors that supported the need to deposit materials along the curved surfaces of the prosthetic with precision.
They were successful at creating a 3D prosthetic for the first time with integrated sensors. While this will allow prosthetic technology development to continue to improve and become cheaper, it also has huge implications on other technologies that will benefit from the capability of 3D printing sensors within a device, such as other smart objects.
Future Possibilities for Smart Objects
What was achieved by the team at Virginia Tech not only carries implications for the future of prosthetic design, it also carries wider implications for the future potentiality of smart devices. They’ve shown that it is entirely possible to print electronic sensors within a larger component, eliminating the need to add it after.
In addition, through the use of conformal printing, they have shown that the printing of sensors within contoured objects is also achievable. These two achievements open the door for future possibilities with smart objects.
Source
Disclaimer: The views expressed here are those of the author expressed in their private capacity and do not necessarily represent the views of AZoM.com Limited T/A AZoNetwork the owner and operator of this website. This disclaimer forms part of the Terms and conditions of use of this website.