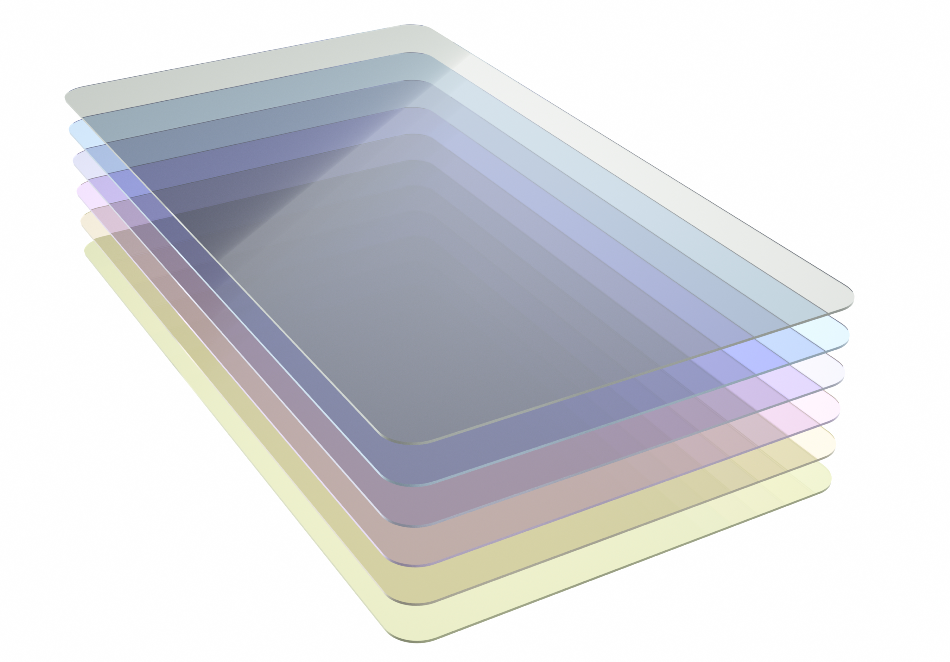
OliveTree / Shutterstock
Many emerging technologies, and automation, in particular, require high-quality sensors, and to meet these growing demands, manufacturers are focused on developing small sensors for a reasonable cost.
Thin film sensors are being hailed as the solution to the increasing demands of modern technology. Made with scientific thin-film deposition processes, these sensors are capable of detecting everything from temperature to pressure to gas concentration.
Thin film technology enables the creation of incredibly small sensors with superior operational abilities, like better response times, durability and versatility.
Thin Film Deposition
As the name indicates, thin film deposition is a kind of process used to produce extremely thin layers of material, ranging from a few nanometers to around 100 micrometers in thickness. While these processes are used to make state-of-the-art sensors, thin film deposition has been used for decades to make everything from CDs to semiconductors.
Generally speaking, thin film deposition can be split into two groups: chemical deposition and physical vapor deposition.
Chemical Deposition involves a highly reactive fluid precursor generating a chemical transformation on a surface to fabricate a desired coating. Chemical vapor deposition (CVD) is a standard kind of chemical deposition known to create high-purity, high-performance thin films.
Physical vapor deposition (PVD) is a category of technologies involving a source material being released and laid down on a substrate via mechanical or thermodynamic means. The two most typical methods of PVD are thermal evaporation and sputtering.
Thermal Evaporation is based on the heating of solid source material in a high-vacuum chamber until the source material evaporates, generating significant vapor and vapor pressure. The evaporated material is then directed through the vacuum chamber so that it strikes the substrate, producing a thin film. This approach offers the benefits of a high deposition rate and significant thickness control.
Sputtering involves the pelting of source material with high-energy particles so that the source material is deposited onto a target substrate in a vacuum chamber. The chamber contains an inert gas and a negative charge is applied to the target material. Source material atoms are then “sputtered off” by being bombarded with atoms, and these particles then move across the chamber and deposit onto the substrate as a thin film.
Sensor Benefits of Thin Film Deposition
One of the main advantages of thin film deposition is the fabrication of a tight molecular bond between the substrate and the deposited film. This bond is free of organic materials and oxygen atoms that might absorb moisture or undesirably react over time.
Hence, thin film gauges are resistant to the issues seen in other strain gauges that use organic supporting materials. The absence of organics also allows these sensors to maintain their function at temperatures greater than 200 degrees Celsius. When thin film strain gauges are fabricated via sputtering, it also offers considerable process control that translates to good repeatability. Sputtering also translates to the tighter management of bridge resistance and zero balance compared to the more conventional production processes for these gauges.
Because the deposition rate is almost directly relative to input power, the rate can be slowed so that extremely thin films can be deposited in short periods of time. By adjusting various parameters, sensors can be created to meet challenging specifications.
Using Thin Film Sensors in Medicine
One of the more exciting uses of thin film sensors is in medicine. Typically, when fluids are delivered to the body with small pumps or irrigation systems, the flow of fluid can be disrupted by a kinked tube or pump failure, which can have disastrous repercussions.
Tube sensors are typically used to track pressure changes in these systems. These devices gauge the pressure applied to a sensor that has been placed against the wall of medical tubing or behind the pump. Thin film sensors used in the application offer superior repeatability, durability and precision.
Sources
Disclaimer: The views expressed here are those of the author expressed in their private capacity and do not necessarily represent the views of AZoM.com Limited T/A AZoNetwork the owner and operator of this website. This disclaimer forms part of the Terms and conditions of use of this website.