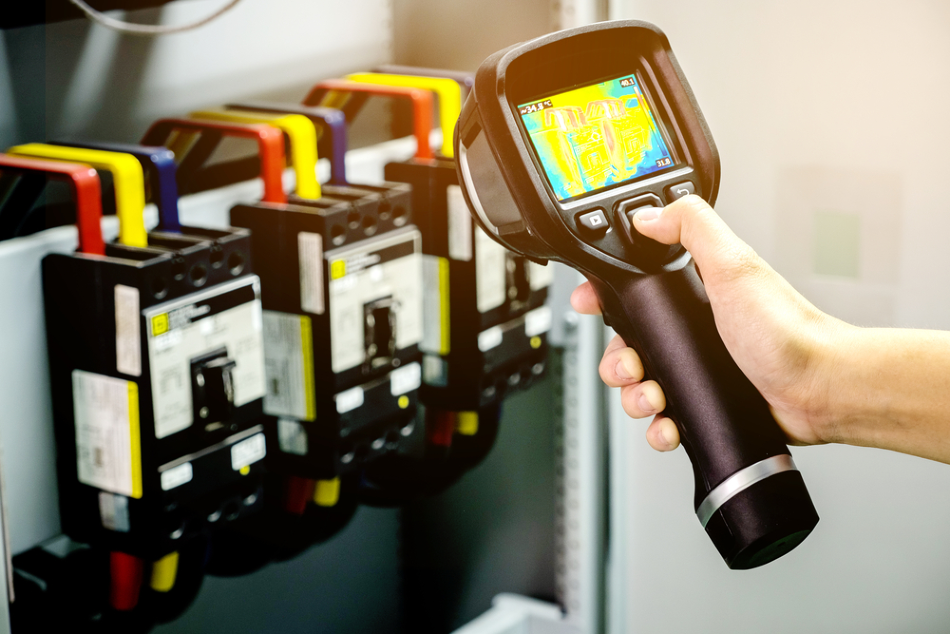
Image Credit: Joyseulay/Shutterstock.com
Thermal analysis refers to any technique for the study of materials that involves thermal control. Measurements are usually made on the basis of an increase or decrease in temperature. The temperature sensors that are popularly used in thermal analysis are thermocouples and platinum resistance thermometers.
There are several types of temperature sensors which are categorized according to the materials used and their operational principles:
- Thermistors: These are used to detect temperature variability according to the changes in the electrical resistance of ceramics or polymers.
- Resistance temperature detectors: This type of sensor indicates temperature values according to the changes in the electrical resistance of metals.
- Thermocouples: These are primarily based on the thermoelectrical effect generated in the junction of two dissimilar metals.
- Silicone-based sensors: This type of sensor is based on the principle of spreading resistance analysis of semiconductors.
There are different types of temperature sensors related to molecular sensing, biomedical, textile applications, and more. Each of these different temperature sensors has its own approaches and methods that allow them to be used in specific applications. Some of the commonly used temperature sensors for thermal analysis are discussed below:
Resistance Thermometers
These are the passive elements in electric circuits. The metals whose electrical resistance rises roughly quadratically with increasing temperature are usually used. The actual sensor used for this type of thermometer is made up of metal like platinum, nickel, copper, palladium or indium wire or, at low temperatures, germanium wire.
In the case of platinum thermometers, the wires are of 0.05 to 0.1 mm thick, wound on a mica holder or inside a ceramic capillary, or otherwise specially packed or self-supported. The range of standard applicability extends up to about 700 K, with time constant depending on the sensor type being in the order of seconds. Non-metals and semiconductor elements can be found to be useful at low temperatures.
Thermoelectric Thermometers
These are often called thermocouples. Thermoelectric thermometers are contact thermometers, whose sensor is a thermoelectric couple. Despite a number of disadvantages, they have retained their significance for most thermal analytical instruments. These are active measuring elements, whose thermoelectric voltage depends on many factors, such as chemical and structural homogeneity, quality of junction, material aging, and adjustable calibration.
The irrefutable advantages of this type of temperature sensor include the very small dimensions of the sensing element, a small time constant, rather high thermoelectric voltage, and a wide temperature range, up to 3000 K, depending on the type.
Monitoring Temperature Differences Using Sensors
The amount of IR radiation can be studied with a thermal sensor. In this type of sensor, radiation is converted into heat at a heat-absorbing membrane. Through a well-characterized thermal conductor, this heat flows into the bulk of the sensor. The temperature difference between both ends of the thermal conductor is a measure of the absorbed heat.
Seebeck sensors are commonly used to measure temperature differences. This is because it allows temperature differences to be measured offset-free. The output voltage of these sensors is proportionate to the temperature difference between the two junctions. However, the accuracy needed for the temperature sensor is much lower than for that of the temperature difference sensor.
For high-temperature sensors, solid electrolytes are applied globally to measure in situ free oxygen and oxygen involved in elevated temperature processes. The commercial use of such sensors began in the early sixties.
Accuracy and Stability of Temperature Sensors for Correct Thermal Analysis
The accuracy of temperature sensors should be consistently checked and calibrated. This is more vital during certain applications, for example, during thermal cycling or a heavy mechanical load. In several industrial applications, stability and good resolution over a certain time interval are more important than accuracy in regard to standards. Temperature sensors with a high level of accuracy are expensive because it requires frequent calibration and trimming procedures.
References and Further Reading
- Gerard C.M., Wang, M.G, and Ali H. 2018. Smart temperature sensors and temperature sensor systems. Smart Sensors and MEMS: Intelligent Devices and Microsystems for Industrial Applications, Second Edition. 57-87.
- Sestak J. 2005. Thermophysical examination and temperature control. 2005. Science of Heat and Thermophysical Studies. A Generalized Approach to Thermal Analysis. 378-411
Disclaimer: The views expressed here are those of the author expressed in their private capacity and do not necessarily represent the views of AZoM.com Limited T/A AZoNetwork the owner and operator of this website. This disclaimer forms part of the Terms and conditions of use of this website.