Software and sensors connect farms and feed mills to streamline feed inventory. When it comes to feed management, feed mills and farms have frequently been conflicting forces.
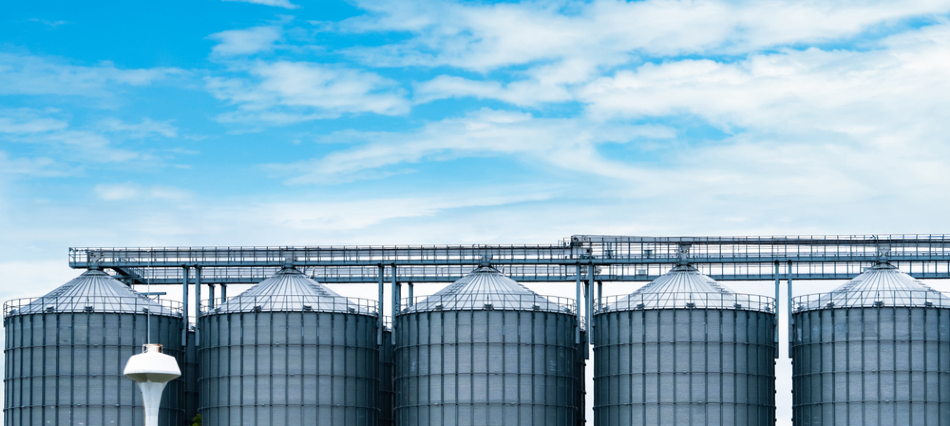
Image Credit: Shutterstock/Fahroni
While they have the shared goal of creating and delivering quality products, delivery schedules, and inventory management create challenges. Feed outages, weekend deliveries, and last-minute orders make feed mills frustrated and increase costs for farmers.
Technological innovation from BinMaster connects this gap, helping farmers and feed mills to work in synergy. FeedView, the latest inventory management solution, uses software and sensors to produce an efficient system that helps both entities to achieve their goals.
Frustration on the Farm
In the past, farmers have had the challenges of climbing bins, depending on guesswork, piles of paperwork, and lengthy spreadsheets to control feed demands. This has led to inaccurate inventory data and running out of or low on stock at the most demanding times.
FeedView evolves this process, meaning that projected and current feed inventory data can easily be accessed on any internet-connected device like a computer, phone, or tablet.
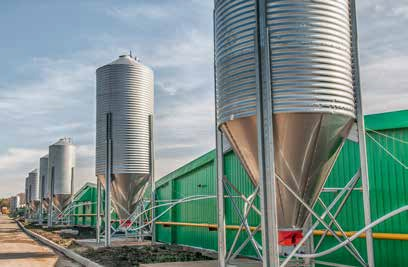
November 2019 - Milling and Grain. Image Credit: BinMaster
FeedView is a detailed feed management solution that blends a cloud-based, easy-to-use software with wireless, battery-powered level sensors.
Bin levels are automatically measured, and consumption is projected utilizing historical consumption rates to assist farmers in estimating outages and understanding when to organize deliveries.
Feed Mills Flustered
Emergency phone calls are frequently directed to mill managers. If a farm has run out of feed or will not have sufficient feed to make it through the weekend, mill employees will be called into work extra or on their day off to organize an unscheduled delivery.
Wasted feed or spills can also happen when the amount of feed in the truck does not fit into the silo upon arrival. These issues cause more expense to the mill and facilitate additional charges to be allocated to farmers, adding tension to the relationship.
FeedView helps feed mills because farmers are more informed about the status of their inventory and can take proactive measures when ordering. Farmers will also be aware of the available space within silos to prevent ordering a surplus of feed.
Orders can be delivered to the mill automatically or ahead of time utilizing an option in the FeedView software. Farmers also have the choice to enable the mill to remotely track feed silos on the farm and estimate future consumption according to historical use.
Feedview® Case Study
Feed monitoring decreased from two hours to 15 minutes a day when using wireless monitoring to optimize the productivity of the farm. While farms concentrate on finishing livestock, operations frequently have a streamlined team of only two or three people.
Taking the example of a leading hog producer in Nebraska, only two employees look after eight feed bins and four barns, preparing over 5,000 head for the market. Each barn has two silos used in combination within this operation.
When the first silo is emptied, feed is taken from the second silo, and the unfilled silo is scheduled for a refill.
Prior to the installation of software and sensors, every silo had to be climbed by personnel, and a tape measure was plunged in to guess the amount of feed in each silo. Ascending silos, dropping a tape, and noting the measurements back in the office could spend around two hours a day, or 15 minutes for each silo.
This task had to be performed almost daily, through snow, rain, or shine. Measurements were written by hand and manually entered in a spreadsheet.
The amount of feed in the inventory was then established by inputting an estimate of the amount of feed left in each silo. There was sometimes insufficient time to perform feed inventory, which resulted in isolation between the farm and the mill.
Goodbye Tape Measures, Hello Sensors
The largest obstacle for silo measurement automation for this producer was the same as many other hog farms: the feed bins had no power connection available. A battery-operated sensor from BinMaster was the solution to this challenge as it removed the requirement for wiring.
Low-power level sensors are fixed on top of the bin via a hole cut in the roof. The sensor is focused on the feed close to the outlet of the bin and instantly records the levels of feed once an hour.
Level data is delivered using a wireless gateway to FeedView. FeedView processes the sensor data into tonnage and enables user-friendly reporting and tracking of feed orders, headcount adjustments, medicated supplements, and feed intake.
The farm’s aim was to streamline and save time during the process of ordering. They explained that the combination of software and level sensors increased the efficiency of their operation.
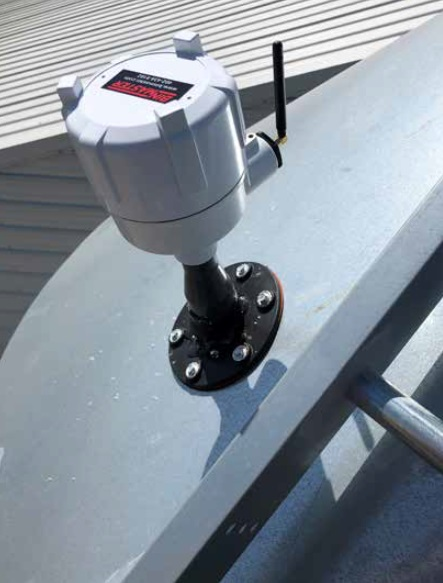
Image Credit: BinMaster
"With FeedView, I can reorder feed with confidence. We’ve eliminated most delivery emergencies and overfills, all without climbing feed bins… thanks to the wireless level sensors." Stated the Feed Order Manager.
Measurement consistency and the safety of personnel are upheld by utilizing technology, rather than making humans perform the work.
He added, “Using sensors to measure feed levels in bins saves a lot of time and is far safer than climbing ladders. Plus, the laser sensors are more accurate than a tape measure because they are aimed at a fixed point in the silo.”
Customer-Focused Features
Many of the options designed for FeedView were made in response to customer suggestions.
Some of the great feedback we got from our first customers was to add a feature that allowed them to place a feed order directly with the mill using the software. Now farms can view their recent feed orders without having to track them separately. It also allows them to see their order history and plan in advance when the next order needs to be placed.
Scott Hudson, Executive Vice President, BinMaster
FeedView is Feed Mill Friendly
Customers hate surprises when it comes to their feed inventory. Now, alerts are sent in advance before feed bin levels get low. They can also look at feed levels anytime and avoid the hassle and extra cost of an emergency or weekend delivery.
Nathan Grube, Regional Vice President, BinMaster
Employees can plan in advance and be alerted when it is time to order. Staff can also monitor feed levels at any time of the day, even on weekends, from their smartphone or computer. Farms can order the correct amount of feed and remove the issue of overages by using FeedView.
A Fast Return-on-Investment
The producer observed that FeedView offers a fast return on a long-term investment by removing common pain points. Animals can attain their target weight on schedule as they do not run out of food.
The bottom line is increased by avoiding additional delivery charges when food is needed immediately. Costs and weight are reduced by closing out with less than half a ton of feed when animals are sent for processing.

This information has been sourced, reviewed and adapted from materials provided by BinMaster.
For more information on this source, please visit BinMaster.