Sponsored by CSEMOct 23 2020
Structural health monitoring for preventive maintenance, integrated actuation, control feed-back of moveable mechanisms, and adaptive objects requires a heterogeneous integration of multiple technologies.
It is crucial to develop technologies and concepts to bring Additive Manufacturing (AM) beyond state-of-the-art technologies of topology optimization, enabling such functionalities while keeping the flexibility and versatility benefits of AM.
So, by combining advanced design, aerosol jet printing (AJP), ink-jet printing (IJP), laser powder bed fusion (LPBF), polymer casting and surface post treatment, CHAMELEON looks to develop technologies to manufacture metal-based 3D parts with embedded functionalities like electrical/pneumatic feedthroughs, compliant mechanisms, sensors and actuators.
The main applications will focus on markets already using AM in production that are requesting additional functionalities, for example medical, space and aeronautical applications. AM is becoming more important for the production of high-end components in applications such as aeronautics, space, and medical.
These industries have vital requirements for which AM has appealing features. Among them, they benefit hugely from a manufacturing technology that is able to create components that have complex geometries, suitable for moderate production volume in addition to weight reduction because of topology optimization.
Yet the majority of today's applications using AM, is for manufacturing "passive" elements that have no functionality except supplying a mechanical structure. It is crucial to develop technologies to bring new functionalities to grow the market attractiveness of AM, while keeping the benefits of flexibility and versatility of AM.
So, in order to elaborate complex AM-based Mechatronics devices, CSEM is investigating the opportunity to combine 3D with 2D printing to attain 3D compliant mechanisms with embedded sensors. CSEM has achieved the following milestones using LPBF AM technology in the past years:
- Compliant mechanism made by AM opening new design, reduced assembly steps and mass reduction.
- Minimum feature size decreased by a factor of more than two with stainless steel, aluminum and titanium alloys (reaching 100 µm features size with stainless steel).
- Demonstration of multiple 2D printed sensors by IJP and AJP.
- Embedded electrical wiring by combination of polymer casting, LPBF, and machining with the demonstration of a new slip ring rotor with RUAG Slip Rings SA©.
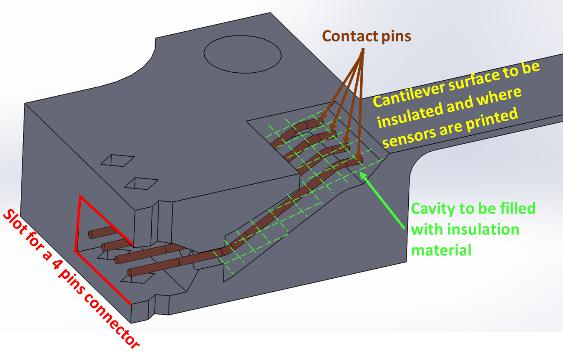
Figure 1. Cross section of the testing cantilever structure CAD design. Image Credit: CSEM
In this project CSEM has utilized and optimized the building blocks above. Furthermore, to show a complex mechatronics device, they have also successfully demonstrated:
- Inkjet printing (IJP) and aerosol jet printing development (AJP) to deposit electrical insulator layer and strain gauges on AM-flexure elements (see Figure 2). The measured gauge factor (GF) is 2 with silver based AJP gauge wires which are in-line with expected value with this technology.
- Laser smoothing of the metal surface to achieve <700 nm Ra surface roughness to supply a good quality surface for sensors printing.
- The integration of built-in electrical wires and connecting interfaces to avoid wires soldering steps. The dielectric insulator has been made by polymer casting method, as seen in Figure 1.
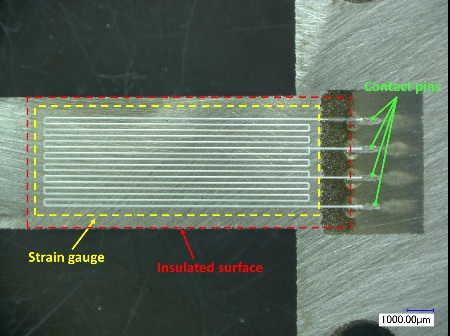
Figure 2. Printed strain gauge and insulation by Aerosol jet printing on a 300 μm-thick flexure element. Image Credit: CSEM
Currently, the demonstrator is under fabrication and is made up of a ±5 mm-stroke XY stage with a laser mounted on its output platform. The high precision linear motion will be achieved using integrated 300 µm-thick flexure elements, which include built-in electrical wires to supply the laser source and to deliver an interface for the printed strain sensors.
The actuation of the demonstrator will be external and the total structure will represent a volume of approximately 80x50x80 mm3.
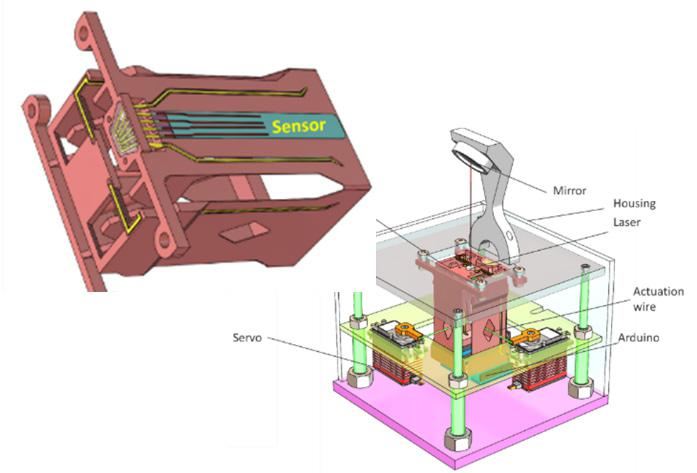
Figure 3. Final demonstrator consisting of the 3D printed XY-stage with embedded sensor and external actuator. A laser pointer is integrated to the moving platform to illustrate the capacity of the demonstrator. Image Credit: CSEM
Acknowledgments
Produced from materials originally authored by S. Lani, N. Hendricks, O. Chandran, H. Saudan, L. Kiener, F. Cosandier, N. Marjanovic, J. Schleuniger, J. Kaufman, R. Jose James from CSEM.
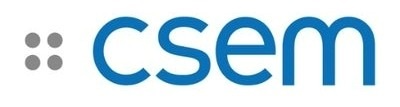
This information has been sourced, reviewed and adapted from materials provided by CSEM.
For more information on this source, please visit CSEM.