In this interview, AZoSensors talks to Terry Arden, Chief Executive Officer at LMI Technologies, about their FocalSpec® 3D line confocal sensors.
To begin, can you give us an introduction to FocalSpec® 3D line confocal sensors? Can you tell us about how FocalSpec® sensors utilize line confocal imaging (LCI)?
FocalSpec® sensors use line confocal imaging technology, a patented optical technique where white light emitting from a sensor's transmitter is split into a continuous spectrum of wavelengths and projected onto an object such that each wavelength maps to a unique height position.
The reflected wavelengths that are "in focus" return to the sensor's optical receiver that maps wavelength variation to height variation. The sensor's off-axis design allows it to simultaneously carry out 3D topography, 2D intensity, and multi-layer 3D tomography scanning.
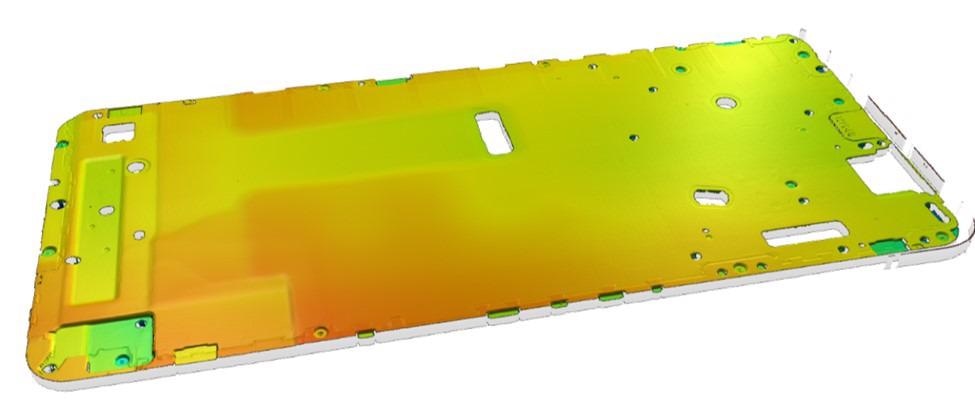
Image Credit: LMI Technologies
FocalSpec® 3D line confocal sensors can be integrated into real-time inline inspection and production systems to scan opaque, translucent, or transparent (glass) surfaces to produce high-quality 3D scan results.
What are some of the sensor's capabilities, including some of LCIs' key applications?
FocalSpec line confocal imaging (LCI) is a unique optical technology for metrology requiring resolutions down to 50 nm. In the past, confocal technology was limited to single point or multi-point sensors based on a coaxial design.
With FocalSpec LCI, a significant breakthrough is achieved using a novel off-axis confocal design that offers a line scan capability with numerous benefits over the traditional coaxial approach.
The key advantage of line confocal sensors is their ability to generate 3D topography (3D surface geometry), 3D tomography (multi-layer 3D), and 2D intensity data simultaneously over a 2k line scan at fast scan rates (e.g., 3-16 kHz). Confocal scanning avoids unwanted reflections from shiny metal surfaces, and the off-axis design permits multi-layer (tomography) scanning.
Confocal sensors acquire high-quality scan data with +/- 20 degrees' angular performance on mirror-like surfaces and +/- 80 degrees on opaque, matte surfaces. Excellent angular performance makes LCI sensors less sensitive to surface orientation when acquiring scan data and handles just about any surface—from transparent, mirror-like to opaque and shiny. Before line confocal was possible, single or multi-point coaxial confocal systems were the standard but required long scanning acquisition to generate a profile or area and were limited to measuring the top surface only.
One key application for LCI sensors is the inspection of cover glass on cellphones and tablets where LCI can see features under the top cover glass layer to reveal details about features such as fingerprint or camera lens assemblies. The combination of 3D tomography (multi-layer) and 2D intensity imaging can also identify defects such as delamination, scratches, or dust on the surface or inside of laminated glass, mobile phone displays, or any other type of transparent multilayered material like sealed medical packages. Contrary to different imaging systems, line confocal sensors detect the defect's location and identify in which layer the defect exists.
In general, 3D line confocal sensors have several advantages over competing machine vision technologies:
- The analysis does not require additional filtering - the imaging is based on the raw data, so what you see is what you measure.
- Any color combination can be measured: matte or glossy, dark or light.
- All surface types can be measured: mirror-like, glossy, transparent, translucent, curved, convex, concave, soft, fragile, porous.
- Provides laboratory-level resolution and accuracy for high-speed inline imaging.
What are some of the FocalSpec® 3D line confocal sensors' benefits in terms of seal integrity inspection?
In medical packaging applications, a sterile seal must be applied to ensure medical devices inside are safe to use. Today, sterile seal inspection is a random, time-consuming manual method that destroys the package during the inspection process. With FocalSpec® line confocal sensors, medical package inspection can be achieved with a non-contact, non-destructive approach to deliver 100% seal verification.
Line confocal imaging is a powerful method for automated medical seal verification. This technology develops high-resolution 3D and 2D scan data of the internal structure of the blister pack layers and pouches commonly used in medical packaging. With multi-layer data acquired from inline scans of the sealing regions, defect detection software can isolate contamination and air gaps, flag incomplete sealing, and detect defects such as wrinkles and burn marks.
- Automated inspection of pharmaceutical and medical packages
- High-resolution 3D images of transparent seal layers
- Fast, non-contact, non-destructive optical verification
- Detects internal seal defects invisible to the human eye
- User-programmable to handle different material types
Other medical applications solved by 3D line confocal sensors include scanning the depth and shape of embossed and etched 3D features, parting line flash of molded parts, surface roughness and texture of extruded parts and web medical products, and burr height in precision-stamped and micro-machined medical parts.
What are some of the advantages of factory automation?
Some of the benefits of factory automation include:
- 100% inspection - consistently and reliably
- Enabling instant detection of process changes and abnormal variation
- Reducing the time and labor needed for manual product sampling and quality control checks
- Providing reliable results without manual measurement and recording errors
- Generating quality reports of entire batches automatically
- Improving product surface quality, reduce claims, waste, and rejects
What role does FocalSpec® LCI technology play in measuring printed electronics, and how is this achieved?
Line confocal sensors can be used at various stages of the printed electronics manufacturing process, starting with substrate material development and manufacturing, where surface roughness is a crucial measurement.
FocalSpec® sensors offer a unique solution for inline roughness characterization of moving surfaces that allows manufacturers to achieve 100% inline quality control with laboratory accuracy. These sensors can easily integrate into existing manufacturing lines and deliver continuous non-contact, ultra-fast scanning and analysis of surface microtopography with real-time reporting for a range of automated production processes.
The sensor's dedicated application software processes profile data, and results are displayed in real-time along with Standard Deviation and Process Capability indices. Continuously updated trend and histogram charts are also available. Real-time data can be used to alert an operator of any unusual process change, and results can be fed back to the process control for an automatic real-time adjustment (e.g., closed-loop control system).
Can you explain how the sensors detect substrate materials, what materials it can detect, and the importance behind this?
All substrate materials can be detected with line confocal sensors whether they are shiny, glossy, or transparent (for example, glass or PET foil). Furthermore, defects can be identified, such as delamination, scratches, or impurities in coating and transparent substrates.
Line confocal sensors provide quick and accurate 3D topography (surface) imaging, whether it's for screen-printing, inkjet printing, or dispensing materials. They also provide step height and width measurement of printed structures. In addition to this, cemented or glued components on transparent substrates are easily captured.
In terms of other LCI sensors on the market, what sets FocalSpec's technology apart?
LCI and its unique off-axis optical design are patented worldwide.
What is next for FocalSpec® 3d line confocal sensors? Are there any expansion plans?
LMI is working on next-generation designs that reduce package size, weight, and cost and increases scanning speed so the technology can further grow into new markets and benefit from the unique features of LCI.
About Terry Arden
Terry Arden joined LMI Technologies in 2003 as Chief Technology Officer, where he applied his engineering and management skills to consolidate several worldwide R&D groups onto a common sensor platform. In 2009, he took over as CEO. He created the company’s flagship Gocator® product line, an all-in-one 3D smart sensor solution focused on delivering inline inspection for 100 percent quality control in today’s smart
factories.
Mr. Arden is passionate about the fusion of hardware and software for the greater goal of building “SmartWare" –– technology with the ability to see, think, and do. He believes vision technologies with deep learning capability provide a powerful combination to leverage designing and developing these smart solutions.
Mr. Arden holds a BSc. Degree in Computing Science and Mathematics from Simon Fraser University, and several patents in image processing and optical triangulation methods.
About LMI Technologies
As the global leader in 3D scanning and inspection, LMI Technologies works to advance quality and productivity with 3D sensor technology. Our award-winning, FactorySmart® laser, snapshot, and line confocal sensors improve factory production quality and efficiency by providing fast, accurate, reliable inspection solutions that leverage smart 3D technologies. Unlike contact based measurement or 2D vision, our non-contact solutions add 3D shape information critical to achieving 100% quality control.
To learn more about how LMI’s inspection solutions can benefit your business, we invite you to contact us at [email protected] or visit us at www.lmi3d.com to explore the possibilities of smart 3D technology.
Disclaimer: The views expressed here are those of the interviewee and do not necessarily represent the views of AZoM.com Limited (T/A) AZoNetwork, the owner and operator of this website. This disclaimer forms part of the Terms and Conditions of use of this website.