In the plastics industry, die swell has been employed as a qualitative indicator of polymer melt elasticity for the purposes of quality control. Die swell can also be used to analyze the smoothness of the extrudate within an extrusion process.
Die swell is where the extrudate expands upon exiting the die. It is caused by the molecular orientation produced by the flow in the die. The greatest extension happens close to the wall. The extrudate then recoils after exiting the die, which contracts the flow direction and causes it to expand in directions that are perpendicular to the flow
In other terms, this event is caused by the memory of the plastic materials. The extrudate attempts to return to its original molecular coil shape as it exits the die.
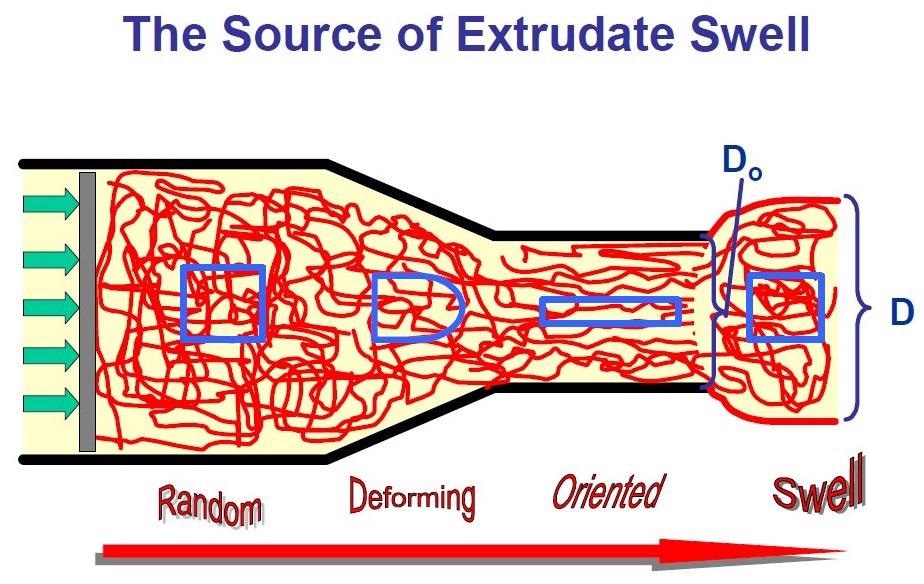
Image Credit: Dynisco
The diameter of the extrudates can be measured with a Dynisco LCR capillary rheometer, which uses a laser beam and CCD element detection.
This accessory component has an accuracy of +/- 0.003 mm, a response time of 1.4 ms, a measuring range of 0.13 to 23 mm and uses an 800 nm laser as a light source.
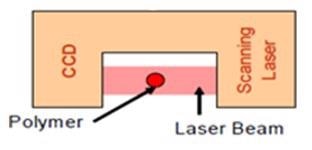
Image Credit: Dynisco
The capillary rheometer can be used in two different ways to analyze the die swell. For the ‘Steady State’ test type, the running die swell can be quantified while the piston is moving during a viscosity measurement. For the ‘Position and Delay’ sec test type, the relaxed die swell can be quantified when the piston is still in between viscosity measurements.
The relaxed die swell can be used to estimate the dimensions of the part, while the running die swell can be used to estimate the die swelling condition of the extrusion procedure.
Die swell can additionally be used to evaluate the smoothness of the extrudate. Extrudate distortion, for example, melt fracture, sharkskin and others can generate a noisy or cyclical die swell measurement.
The die swell ratio percentage can be determined using the below equation after establishing the die diameter:
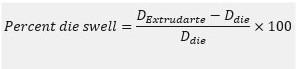
The die swell ratio percentage versus shear rate for three separate high density polyethylene samples is presented in Figure 1.
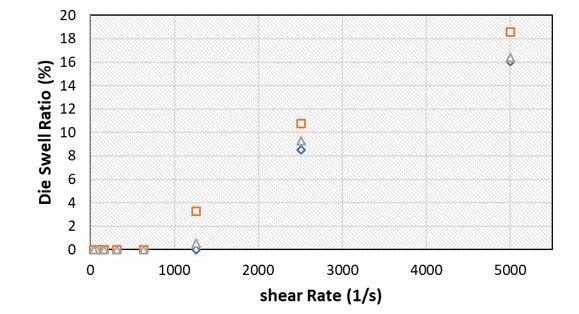
Figure 1. Die swell ratio percentage versus shear rate for three PP samples. Image Credit: Dynisco
As predicted, the die swell ratio declines as the shear rate decreases and when the shear rate is lower, viscoelastic plastic materials lose their elastic memory and die swell decreases as a result of this.
Die swell can be solved by utilizing a longer die, a larger die diameter, decreasing the shear rate, increasing the temperature, or tapering the die.
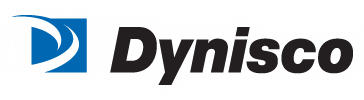
This information has been sourced, reviewed and adapted from materials provided by Dynisco.
For more information on this source, please visit Dynisco.