The resistance of a polymer melt to a change in the molecular structure at the test temperatures can be established with a thermal stability test. The results of this test depend on the material formulation, residence time at that temperature, the temperature, presence of moisture and/or contaminates.
It is widely acknowledged that polymer rheological properties, namely shear viscosity, are extremely sensitive to the alterations in the polymer molecular weight and so monitoring of these parameters over time can supply information regarding the thermal stability of a polymer.
In the plastics industry, a thermal stability test has a number of uses. It can be employed to verify the stability of the polymer sample during an actual process (for example, injection molding or extrusion) or during a rheology test.
In this instance, it is advised to carry out the test at a constant shear rate, which corresponds to that in the actual process. This test technique can also be utilized to indicate the presence of a reactive chemical or moisture in the polymer.
This test can also supply information for kinematic analysis to calculate the kinetic constant of numerous reactions that could occur during the process. The graphs of apparent shear viscosity versus time for two different materials using a Dynisco LCR7001 capillary rheometer are shown in Figure 1.
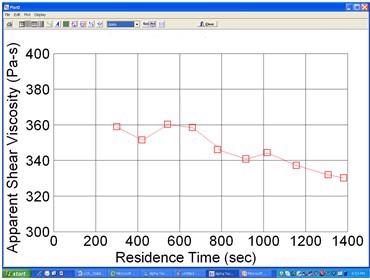
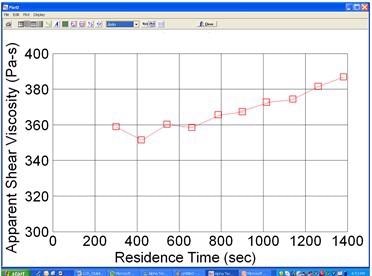
Figure 1. Changes of apparent shear viscosity over time for two different polymers. Image Credit: Dynisco
These graphs exhibit the alterations of apparent shear viscosity over about 23 minutes residence time at a constant temperature of 200 °C and a constant shear rate of 80 1/s. After about 13 minutes, the first graph demonstrates a minor reduction of the shear viscosity.
This can occur because of polymer degradation and possible chain scission of polymer melaleucas. However, the second graph demonstrates a steady increment of the shear viscosity over time. This can represent the presence of a chemical reaction like crosslinking or polymerization over time.
The thermal stability tests can be carried out at numerous temperatures and/or shear rates and a complete window into their process can be acquired, as can be observed in Figure 2.
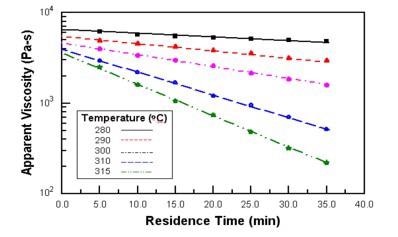
Figure 2. The results of multiple thermal stability tests at various temperature. Image Credit: Dynisco
References
- J.M. Dealy, P.C. Saucier, Rheology in Plastics Quality Control, Hanser (2000).
- A. Farahanchi, R. Malloy, M.J. Sobkowicz, Effects of Ultrahigh Speed Twin Screw Extrusion on the Thermal and Mechanical Degradation of Polystyrene, Polym. Eng. Sci. 56, 743–751 (2016).
- J.M. Dealy, K.F. Wissbrun, Melt Rheology and its Role in Plastics Processing: Theory and Applications, Van Nostrand Reinhold, New York (1990).
- T. Andersson, B. Stalbom, B. Wesslen, Degradation of Polyethylene. II. Degradation of Low-Density Polyethylene, Linear Low-density Polyethylene, and High-Density Polyethylene in Film Extrusion, J. Appl. Polym. Sci. 91, 1525–1537 (2004).
- R. Gendron, M.F. Champagne, Effect of Physical Foaming Agents on the Viscosity of Various Polyolefin Resins, J. Cell. Plast. 40, 131–143 (2004).
- N. Cheremisinoff, Polymer Rheology and Processing, CRC, (1993).
- P.J. Carreau, D.C.R. DeKee, R.P. Chhabra, Rheology of Polymeric Systems, Hanser, (1997).
- C.W. Macosko, Rheology Principals, Measurements, and Applications, Wiley-VCH, (1993).
- C.L. Rohn, Analytical Polymer Rheology, Hanser, (1995).
Acknowledgments
Azadeh Farahanchi, Rheological Scientist, Ph.D
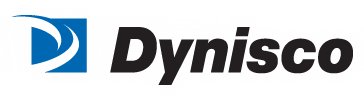
This information has been sourced, reviewed and adapted from materials provided by Dynisco.
For more information on this source, please visit Dynisco.