In just ten years, there has been a significant increase in demand for greater data center storage and data transfer. This means that the load placed on backplane-to-backplane data server interconnects increases exponentially across each center.
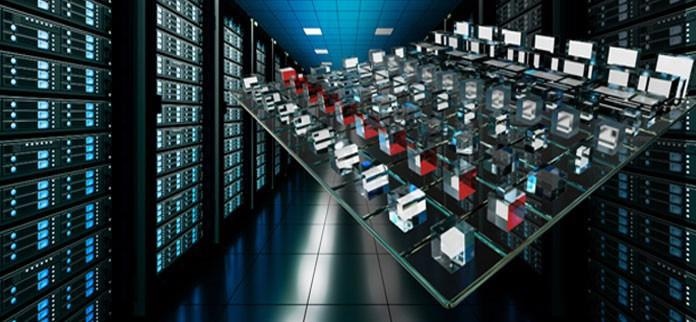
Image Credit: Iridian Spectral Technologies
Another aspect to factor into the equation is the fact that there will be a call for an improvement in data center interconnect bandwidth, which various factors will push along.
Amongst these factors are enhanced technologies (e.g., flash memory and solid-state drive) that in turn make cloud storage a more desirable option, as well as requirements for dynamic allocation of server, storage and network resources.
Both consumer and commercial users need and want continuous data availability, supported by the distribution of virtual computing and storage resources across various physical devices, and they expect that speeds will become faster in relation to that access.
As a single request can spark a series of data exchanges between servers in one or more data centers, cloud providers’ warehouse-scale data center servers have had to stay alert.
This has resulted in an increase from 10 GbE to 100 GbE network adapters in standard use; with 800 GbE (and even to 1.6 TbE) expected to become the new standard within the coming years.2
In a large data center that relies on common Clos topology (Fig. 1), hundreds of thousands of interconnects are a prerequisite to preserve effective communication across both internal and external servers i.e., data centers located elsewhere, off-site.
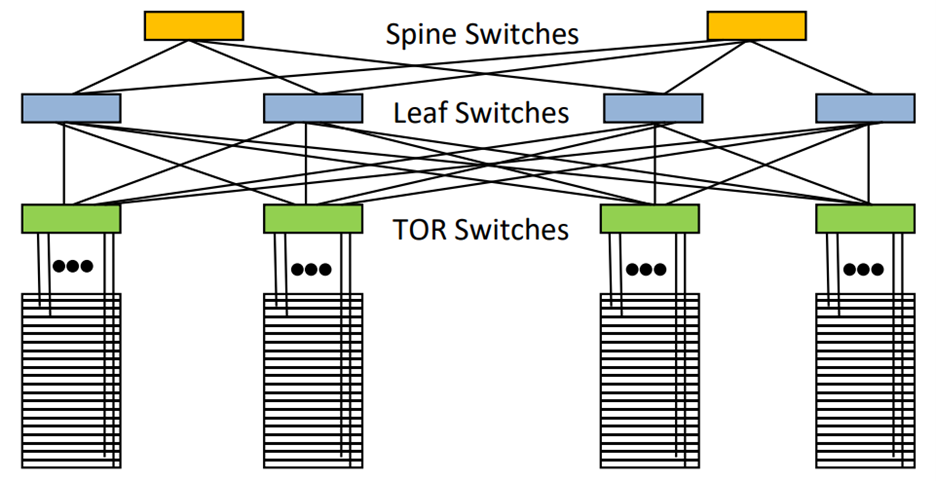
Figure 1. Clos Topology. Image Credit: Iridian Spectral Technologies
Clos delivers direct interconnection between top-of-rack (TOR) switches and other servers, but each leaf switch in the leaf spine architecture is connected to every switch across the whole fabric of the network. The connections between the spine switches to the leaf switches are as equal to the leaf switches to the TOR switches.
Responding to progressive data center architectures and the ever-increasing demand for bandwidth, the conventional copper connections used to connect backplane to TOR switches, and TOR to leaf switches have been substituted for optical interconnects to support the higher data rate required.3
As such, data center designers and operators are always searching for optoelectronic transceiver components with increased capabilities that are also affordable, compact and energy-efficient.
Whilst standard transceiver components were once considered an option for use at these data rates in long-haul systems, they cannot be used in data centers since they are configured for longer-distance interconnects (generating a higher cost), while consuming more power and typically having a larger footprint.
Optical interconnect bandwidth enhancement makes use of various techniques, including single-mode fiber (SMF), multi-mode fiber (MMF), digital coherent optical transmission, dense wavelength division multiplexing (DWDM) and multiple spatial modes.
Each one of these techniques has been employed to boost optical interconnect data transfer rates to levels nearer to those of the long-haul fiber connections. This is a consequence of all data passing through long-haul fiber needing to be distributed around data centers at equivalent speeds or faster.
At each end of the fiber interconnect, the optical transceivers deployed generally use optical filters to regulate the different wavelength channels used in CWDM, DWDM, WDM and other multiple-wavelength configurations.
Filters deployed in these limited interconnect applications (≤ 1 km) utilize the same base filter coating technology as those filters found in long-haul and metro applications. Yet, the optical design and filter size and thickness are adapted to suit the needs of the specific requirements of the compact data center products.
As well as precise, compact form factors, designers merging these parts need high transmittance and nominal signal loss — as well as exceptional reflectance, if operating in reflection — protecting against the need to conduct any unnecessary amplification.
Related energy consumption is of utmost importance in this application, and using the highest quality optical interconnect available maximizes energy efficiency while significantly reducing the associated heat dissipation.
Custom filter solutions — including the standard single-wavelength bandpass and edge pass units utilized in WDM systems, in addition to DWDM edge filters — have demonstrated the ability to be an affordable and trusty solution to address such needs.
Etalons or other optical filters can also be incorporated into the integrated laser assembly (ITLA) sources in these systems.
Limited Space ≠ Limited Options
A server backplane combines numerous connectors; this means every single component containing a filter must be super-small to reduce the volume it occupies as much as necessary.
In large server farms, space is consumed by hundreds or even thousands of servers with expensive maintenance costs per square foot since the large space must be kept temperature-controlled and physically secure.
Thus, the ability to make considerable savings where space is concerned (e.g., trimming 30% or 40% of each component’s physical volume) across hundreds of thousands or even millions of components has a major impact.
Distributed data centers located in urban environments — smaller locations interlinked to produce, in essence, one giant data center — call for the same space-saving requirements due to the huge costs per square foot of real estate in more populated areas.
The cost to produce such products at scale has seen a considerable amount of component and filter manufacturing move to Asia.
However, Iridian Spectral Technologies has more than 20 years of filter design experience, proprietary design tools and automation throughout part manufacture, cutting and testing for optimal efficiency and high-quality part production while still manufacturing and running its processes in North America.
A significant investment in automation has enabled Iridian to manufacture etalons and filters at high volumes and retain high quality standards consistently while keeping the costs per unit relatively low.
Iridian sells its product to low-cost manufacturers in Asia and elsewhere on a regular basis because it can offer excellent standards and expertise in both design and manufacturing processes.
Iridian Spectral Technologies’ design process typically fits the client’s needs and stated wavelength preferences: i.e., which wavelengths need to be multiplexed and how they will be spaced (e.g., do they necessitate 5 nm, 10 nm, or 20 nm spacing between each laser wavelength).
Moreover, the client must stipulate the desired tolerance on those sources, which helps determine the appropriate bandwidth. From there, an investigation of the conditions of use is carried out — particular attention is paid to the angle of incidence and the beam’s cone angle.
Subsequently, a study of the form factor and part size based on where the customer needs the component to fit is conducted, accounting for both the space available for the component and the normal operating temperature – data centers are usually are air-conditioned; thus, temperature is not generally much of a concern.
In design scenarios, similar to the ones previously detailed, Iridian closely collaborates with the client’s chief technical officer or technical team to deliver a filter solution before initial production begins.
At this point, the client may test the part and feedback any useful details that can then be applied to a second sample round or, if all is well, move ahead with high-volume production.
Even setting high standards of care and attention, Iridian Spectral can distribute filters in around four weeks (from receipt of customer specs to initial delivery) and etalons in the region of eight weeks.
Iridian’s goal is to turn around a design and quote within 48-hours, and within eight to ten weeks increase unit delivery into the tens of thousands per week (i.e., volume production). Consider the below examples:
- Design Changes
A recent high-volume customer was hoping to transition from a free-standing component — where free space is present on both sides of the filter product — to a part that was much thinner, featuring an epoxy mount on the backside (i.e., epoxy applied directly to either send or receive optics).
This feature would mean the client’s module would be much more compact than a free-standing, edge-mounted orientation. The design threw up several challenges related to the cone angle (i.e., how the light is coupled into and out of the filter) that were tackled through an iterative process in collaboration with the client before moving on to high volume production.
- Volume Demands
A recent Iridian Spectral client needed 10,000 parts to be shipped per week: etalons measuring 7mm x 1.1mm.
- Precise Form Factors
A recent Iridian client requested a part with lateral dimensions 0.5mm and smaller, which necessitated an equipment upgrade. The main hurdle in that situation was handling after dicing; altering the vacuum pickup to house a smaller size.
Handling and packaging are the key issues when using miniaturized components, as is (in some cases) optical characterization. When fabricating smaller form factors, optical characterization is generally performed at the wafer level, after which the ‘good areas’ are mapped, meaning said good areas are ready for use before packing them for clients.
Iridian also provides its services as an additional or replacement source for clients whose existing product has been manufactured in high volumes previously — organizations seeking a supplementary partner to manufacture an identical pre-existing part with identical specs as the original, usually with higher package yield and reduced cost.
Iridian has invested as much as possible into developing in-house language skills to ensure that they are able to deal with customers all over the world. Working habits established before the pandemic also mean that the company has the ability to efficiently work remotely.
Final Thoughts
The progression of data centers for cloud storage and distributed computing has pushed the need for even better data transmission rates within data centers. Subsequently, this has necessitated innovative creativity in optical interconnects — both by design and the means of production to meet high-volume demand.
Iridian Spectral Technologies brings more than two decades of experience to the table to offer specialized optical filters and optoelectronics used in these centers.
Automated manufacturing, cutting and testing systems are commonly joined across all of Iridian’s products and product areas, guaranteeing maximum efficiency not only for this market area but across the entire business.
Using the same equipment with little or no reconfiguration, Iridian can load and produce a part for one client on one day and manufacture another client’s product the following day — all without jeopardizing quality or volume.
Furthermore, Iridian utilizes a number of various coating platforms, which enables the company to apply the most appropriate one to the part being produced: larger or smaller optics, higher- or lower-precision specifications.
Iridian is flexible and can adapt to the most efficient platform available for the application. Since Iridian works in numerous markets, the company possesses a broad range of tools to facilitate the most cost-effective solution, meeting the customer’s needs based on the product requirements.
References
- Zhou, X., Optical Fiber Technology (2017), http://dx.doi.org/10.1016/j.yofte.2017.10.002
- Ethernet Alliance, 2020 Ethernet Roadmap, https://ethernetalliance.org/
- Qixiang Cheng, Meisam Bahadori, Madeleine Glick, Sebastien Rumley, and Keren Bergmen, Optica, Vol. 5, No. 11 / November 2018 / Optica, p 1354-1370 https://www.osapublishing.org/optica/fulltext.cfm?uri=optica-5-11-1354&id=399361
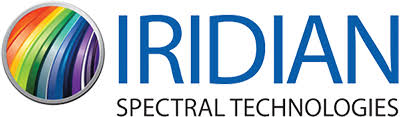
This information has been sourced, reviewed and adapted from materials provided by Iridian Spectral Technologies.
For more information on this source, please visit Iridian Spectral Technologies.