A small puddle of mysterious fluid underneath a vehicle is the last thing any owner wants to see. It is easy to get complacent regarding observation and maintenance as EV’s use electrons instead of diesel or petrol as fuel and need much less maintenance than their Internal combustion engine (ICE) counterparts.
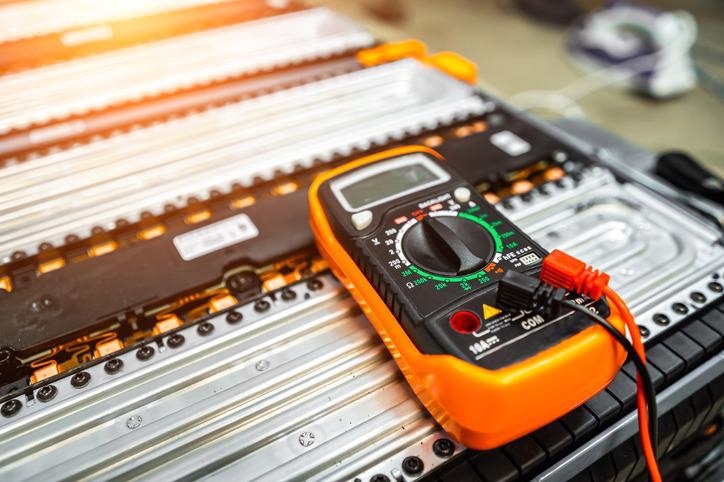
Image Credit: Amphenol Advanced Sensors
Even though a vehicle is designed to run on electricity, this does not mean it is immune to leaks. Leaks are one of the most common issues owners face in maintaining their truck or car.
Regular maintenance and observation for any unusual stains or fluids on the garage floor or driveway can prevent expensive and potentially catastrophic issues later, as EVs usually do not have frequent oil change intervals like their ICE counterparts. Many EVs also contain a suite of sensors that will check your fluids for you.
Electric vehicles usually contain coolant to supply thermal management (heating or cooling) of the various high energy electronics systems. These include the inverters, motors and battery pack.
Modern electric vehicles possess substantially more complex coolant control systems than their ICE predecessors, utilizing both refrigerant and coolant to control the temperatures of numerous components through the utilization of heat pumps, heat exchangers, various valves and sensors.
Having accurate, reliable sensors to monitor temperature, fluid level, pressure and quality is the best way your design can prevent a small leak of any sort from turning into a big problem. Some advanced EV designs can even sense if the coolant is leaking into an area where it could cause damage to the vehicle, for example, near the battery cells.
Four Leaks to Watch for in Electric Vehicle Battery Packs (Plus the Sensors Needed For Monitoring)
Leak detection is an absolute necessity for monitoring the battery health of an electric vehicle, whether the vehicle is on the road or charging. The most critical leaks to look out for in an EV’s battery pack are those which influence its thermal management system; examples include:
- Electrolytes
- Coolant
- Dielectric oil
- Refrigerant
Electric Vehicle Battery Pack Leak: Liquid Coolant
Coolant is circulated in a closed-loop around an electric vehicle’s battery pack, cabin, inverter and possibly even the motors to keep temperatures within a suitable range of 15-45 °C, instead of circulating through an engine block like in an IC engine.
The thermal management system enables the inverter, battery and motors to function without overheating and triggering shutdown or power-limiting mode.
Sensor(S) Needed for Detection:
Electric vehicles need the following components to detect liquid coolant leaks:
Coolant breach sensors: This sensor provides a secondary technique for monitoring liquid coolant levels. A coolant breach sensor detects liquid near the battery cells should a coolant leak happen within the coolant lines inside the battery pack.
Additionally, a coolant breach sensor also monitors for the presence of other liquids, like water intrusion into the battery enclosure, which can lead to short circuits and corrosion.
Coolant level sensors: An EV battery’s thermal management system requires a certain level of liquid coolant to function properly, just like an ICE vehicle’s cooling system. This electric vehicle sensor type monitors the volume of liquid coolant within the battery’s thermal management system, as its name indicates.
Coolant temperature sensors: If there is insufficient cooling or aeration or if the coolant is unable to circulate properly, the coolant temperature sensor can supply intelligent information on whether or not the coolant is transferring heat efficiently.
A number of battery systems will include temperature sensors at the outlet and inlet of heat-generating devices, like the motors, battery or inverters, in addition to the heat exchangers, supplying information on the efficiency of heat exchange.
Electric Vehicle Battery Pack Leak: Refrigerant
While all EVs with an air conditioning system utilize refrigerants to keep the passenger space cool, some manufacturers employ the same system to keep battery pack temperatures in check.
Refrigerant-based battery cooling takes two forms when utilizing heat pump systems, direct and indirect:
Indirect is where a vehicle’s coolant fluids flow through plates cooled by refrigerant. This cooling system is more complex and involves other components to keep coolant within an optimal range, like a chiller.
Direct is where refrigerant from the vehicle’s air conditioning system flows through a series of cooling plates within the battery pack in order to keep temperatures down.
Sensor(s) Required for Detection:
Two types of sensors are needed to detect refrigerant electric vehicle battery pack leaks are pressure sensors and temperature sensors.
Pressure Sensors
Simply put, a refrigerant system does not work when there is a loss of pressure within. Pressure sensors are usually the first sign of decreased performance and leakage within the system, as the expansion valves, compressor and evaporator all have an expected pressure at different points in the system.
It can be assumed that some of the refrigerant has leaked from the system if the system cannot attain target pressures.
Temperature Sensors
The ideal gas law applies to the refrigerant, as in high school physics. The combination of pressure sensing and temperature in the gas and liquid phase within the system is a good indicator as to whether or not there is enough refrigerant.
Carbon Dioxide (R744) Sensors
R744, a carbon dioxide-based refrigerant, is utilized in some of the most advanced refrigerant systems for EVs. There can be unsafe levels of carbon dioxide released into the breathable air space if the refrigerant leaks into the passenger compartment.
Non-dispersive spectroscopy enables the accurate measurement of the CO2 levels in the passenger compartment to establish whether a leak of refrigerant has happened.
Electric Vehicle Battery Pack Leak: Dielectric Oil
Superior battery pack temperature control is boasted by a newer battery pack thermal management system with promising applications; dielectric oil cooling.
Battery cells are immersed in dielectric oil that is circulated in a closed loop through the unit inside the battery pack. The oil, an engineered thermal conductive fluid, suppresses thermal events as well as keeps battery cells cool.
Sensor(s) Required for Detection:
Oil level / Quality / Dielectric Sensor
Battery pack thermal management with dielectric oil requires a specific level of fluid to work effectively, just like a coolant system. Furthermore, monitoring the quality and dielectric of the fluid will give an indication of the life expectancy of the fluid and supply excellent prognostic tools.
Oil Temperature Sensor
This is an indicator of the system’s functionality. It monitors for spikes in dielectric oil temperature, which may indicate issues with dielectric coolant flow, which may indicate damaged or kinked lines.
Electric Vehicle Battery Pack Leak: Electrolytes
Measuring the presence of electrolyte leakage is useful in monitoring an electric vehicle’s battery health for determining whether cells within the pack are failing because of age or other stress conditions.
These leaks would usually only happen within the battery enclosure. They cannot be seen outside the vehicle, so it is vital that sensors inside the battery detect this event.
Sensor(s) Required for Detection:
Electrolyte Leakage Detection Sensor
The electrolyte leakage from damaged cells usually contains volatile hydrocarbons, which can be detected by a hydrocarbon sensor.
Electric Car Battery Pack Thermal Management Performance & Safety
One of the most important elements in maintaining optimum safety and performance of an electric vehicle is maintaining proper coolant system function.
One sure way to destroy a combustion engine is running it without coolant. In the same way, an EV without coolant can damage the power electronics and battery. The good news is that most modern electric vehicles know when they require fluid and can alert their owners.
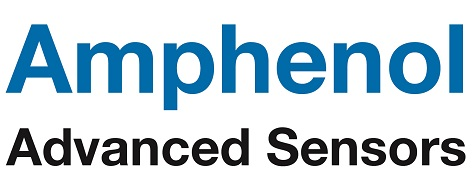
This information has been sourced, reviewed and adapted from materials provided by Amphenol Advanced Sensors.
For more information on this source, please visit Amphenol Advanced Sensors.