Emerging wearable electrical items such as wearable energy production devices are essential for advanced biosensing. This is especially true as modern energy supply devices are made of stiff, bulky materials that are uncomfortable to wear.
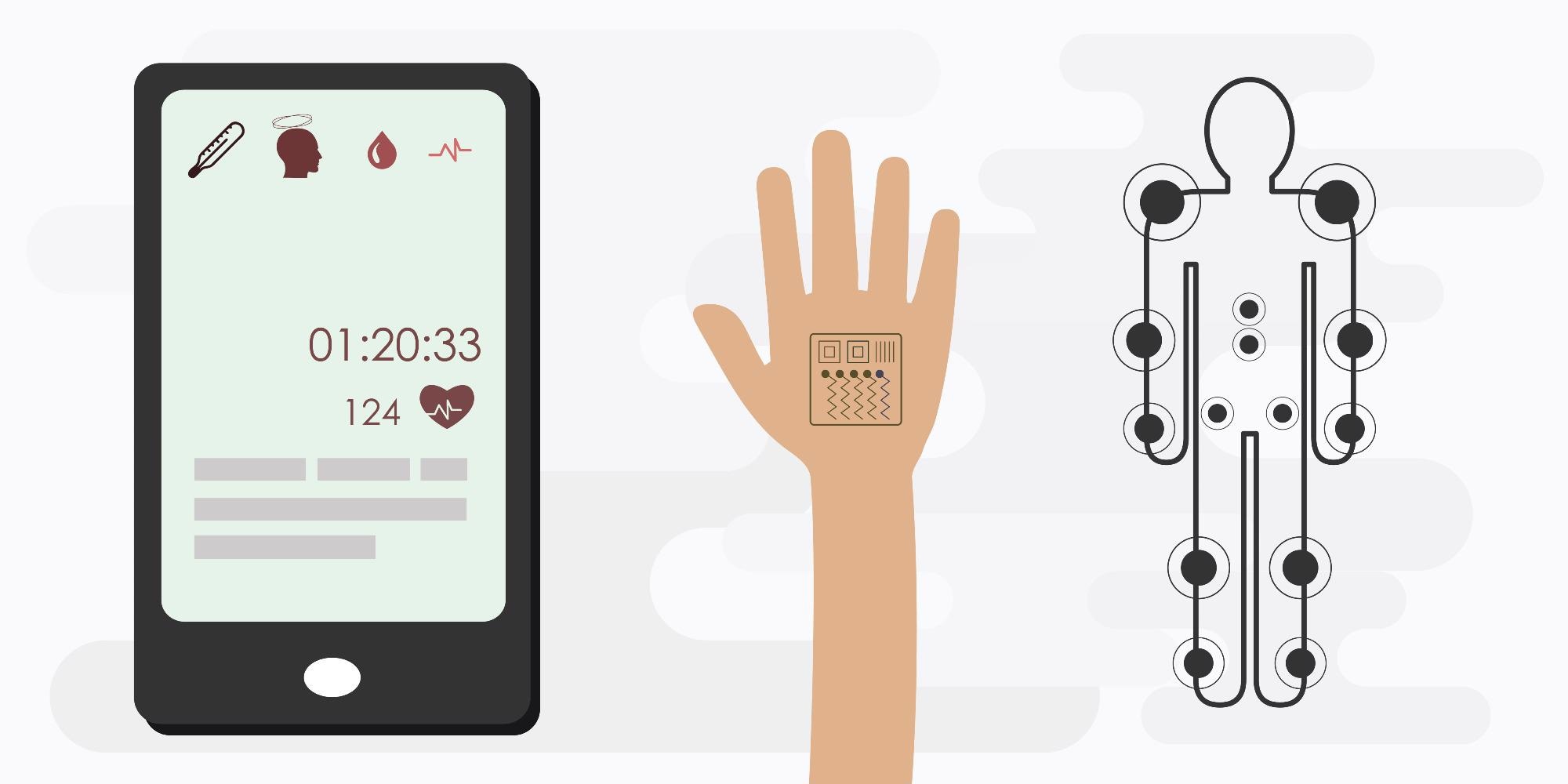
Image Credit: magic pictures/Shutterstock.com
The wearable sensor may be skin-friendly and ecologically friendly, and it offers a lot of nice features. Many sensors are now employed to assess human health and physical movement, but their sensitivity, environmental resistance, and mechanical qualities are all lacking.
Nanofiber membranes have emerged as a major branch of the sensing field as a result of the advancement of nanotechnology. Nanofiber membranes are commonly employed in sensor applications. For the manufacture of nanoscale fiber membranes, electrospinning is a straightforward and reliable approach.
Electrospinning fiber film offers several remarkable properties and can fulfill the demands of current technology. The synthesis, properties, and use of electrospun nanofibers in wearable sensors are discussed in research published to the MDPI journal biosensors.
Methodology
The precursor solution produces a nanofiber membrane under the simultaneous action of electrostatic force and surface tension. These pressures cause the solute to collect on the receiving device by stretching and forming a jet. Figure 1 depicts an electrospinning process with several collector types.
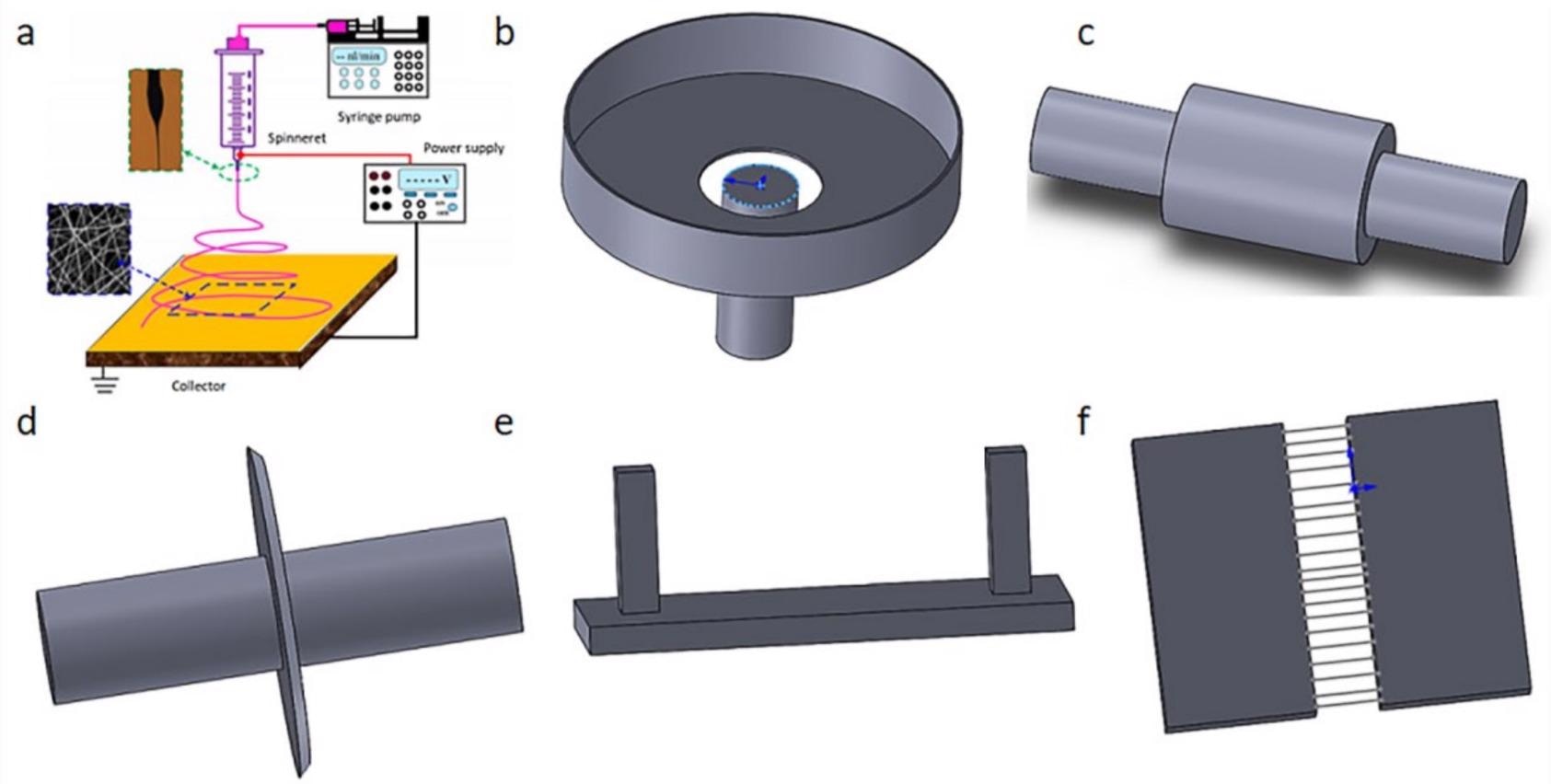
Figure 1. A typical electrospinning operation and different collector types. (a) Electrospinning principle diagram; (b) water bath collector; (c) roller collector; (d) disc collector; (e) magnetized collector; (f) parallel plate electrode collector. Image Credit: Xu, et al., 2022
The electrospinning equipment was altered during the research phase to achieve the nanofibers researchers desired, such as multi-jet electrospinning, centrifugal electrospinning, coaxial electrospinning, multilayer electrospinning, and compound field electrospinning.
The coaxial approach is another popular electrostatic spinning technique. A nanofiber membrane with a core-shell structure is created in this way. Figure 2 depicts a schematic representation of the coaxial spinning process used to manufacture the Al@GAP/NC/PVDF composite film.
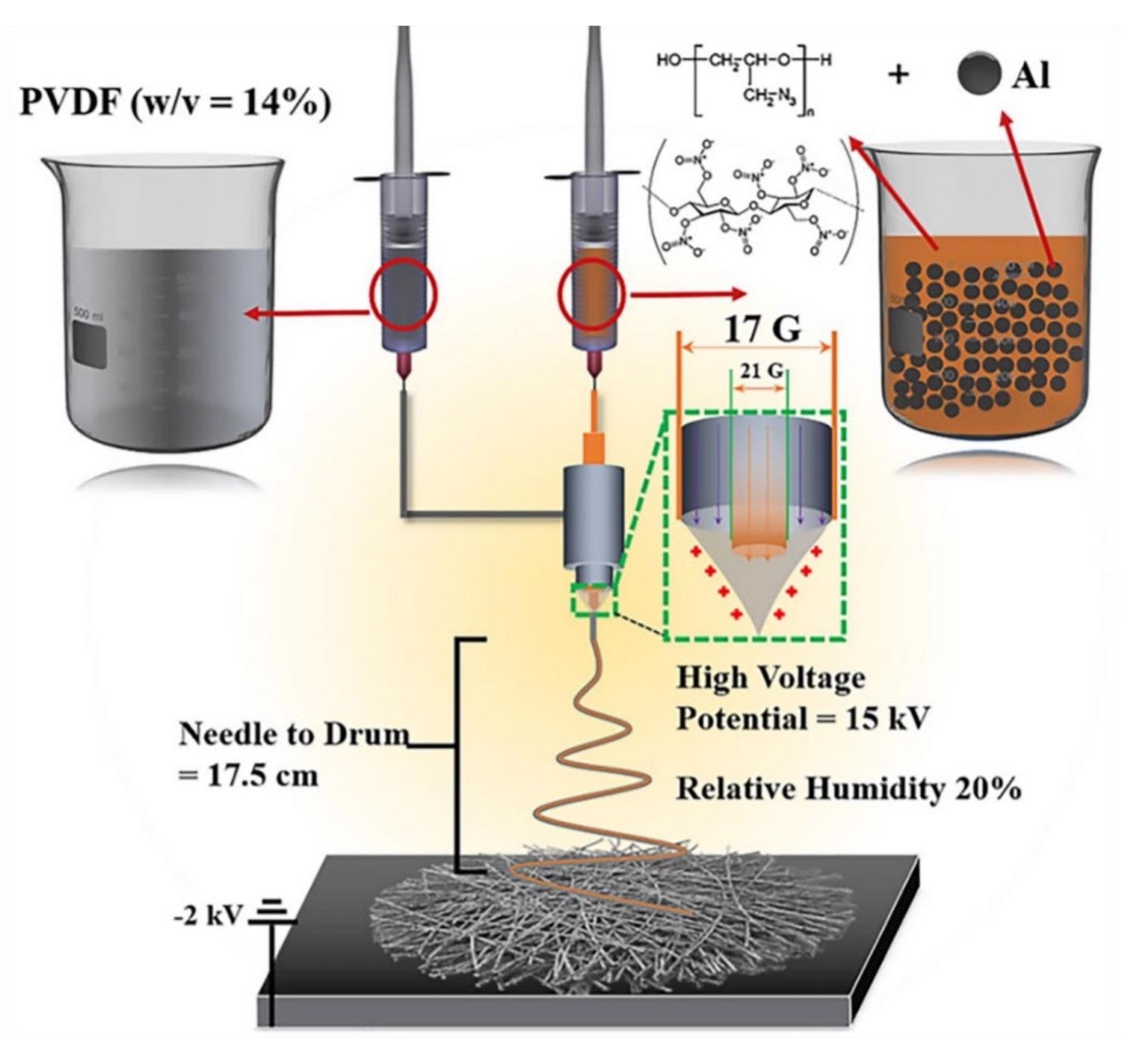
Figure 2. Schematic diagram of the preparation of the Al@GAP/NC/PVDF composite film by the coaxial spinning method. Image Credit: Xu, et al., 2022
The main difference between centrifugal and regular electrospinning is that centrifugal electrospinning employs centrifugal force to stretch the solution and cause it to spin. A schematic representation of centrifugal electrospinning is shown in Figure 3.
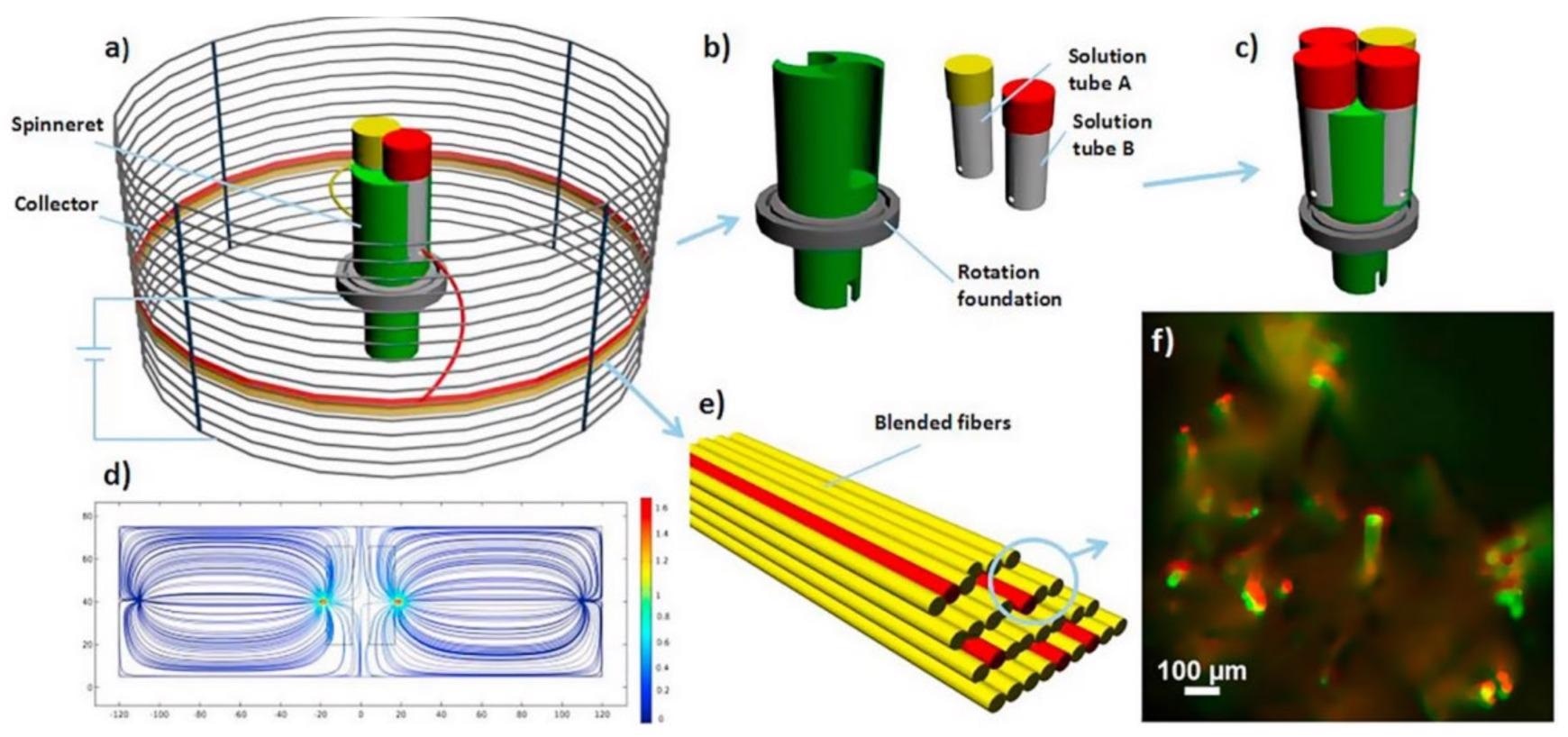
Figure 3. Schematic diagram of centrifugal electrospinning. (a) Structure chart; (b) rotating device; (c) nozzle is mounted on a rotating body; (d) electric field distribution map; (e) composite fiber; (f) fluorescence image of composite fiber. Image Credit: Xu, et al., 2022
Multi-jet electrospinning produces composite nanofibers, which can be blended to increase electrospinning yield. Composite fiber materials offer a broader range of applications than single polymer fiber materials, according to studies. A schematic illustration of multi-jet electrospinning is shown in Figure 4.
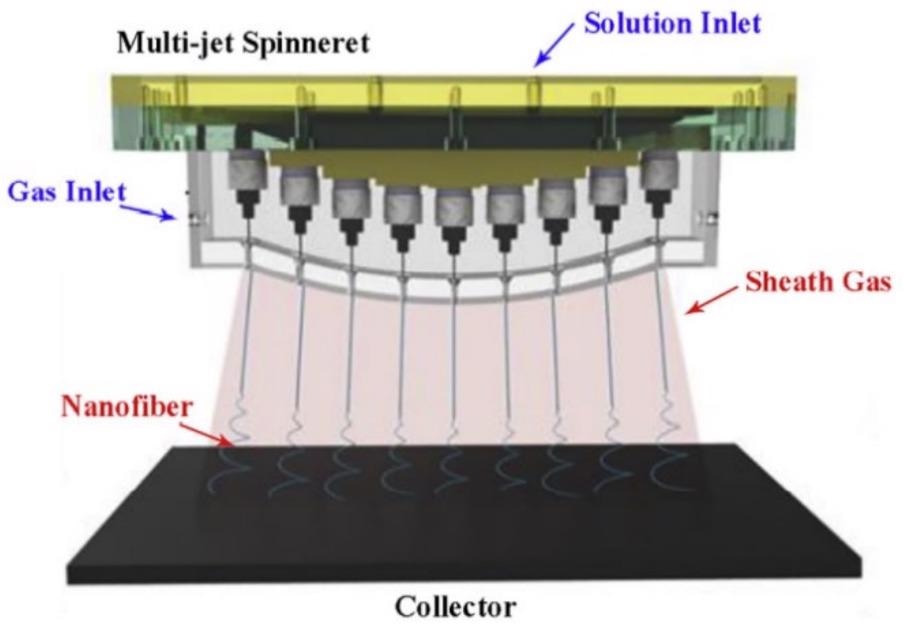
Figure 4. Schematic diagram of multi-jet electrospinning. Image Credit: Xu, et al., 2022
Multi-layer electrospinning spins a sequence of polymer materials. Multiple layers of composite fibers are formed by depositing these materials layer by layer on the collecting device. This composite fiber may be used in a variety of ways. Figure 5 shows a multilayer electrospinning schematic design.
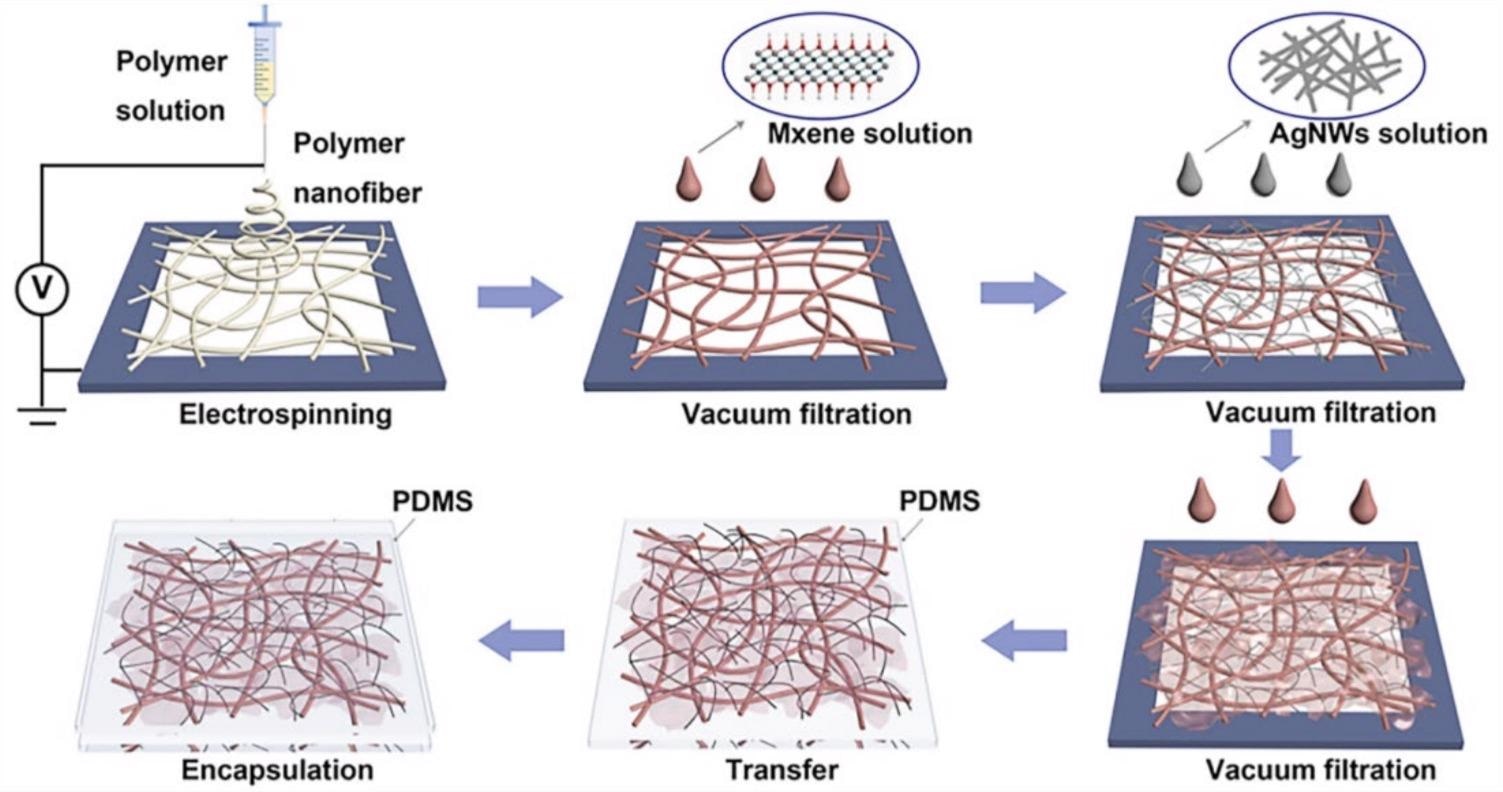
Figure 5. Schematic diagram of multilayer electrospinning. Image Credit: Xu, et al., 2022
These fields are introduced to improve fiber shape and performance, as well as to smooth out spinning. This type of compound field electrospinning is not comparable to standard electrospinning in terms of its operating mechanism. Figure 6 shows an electrospinning design with a higher magnetic field.
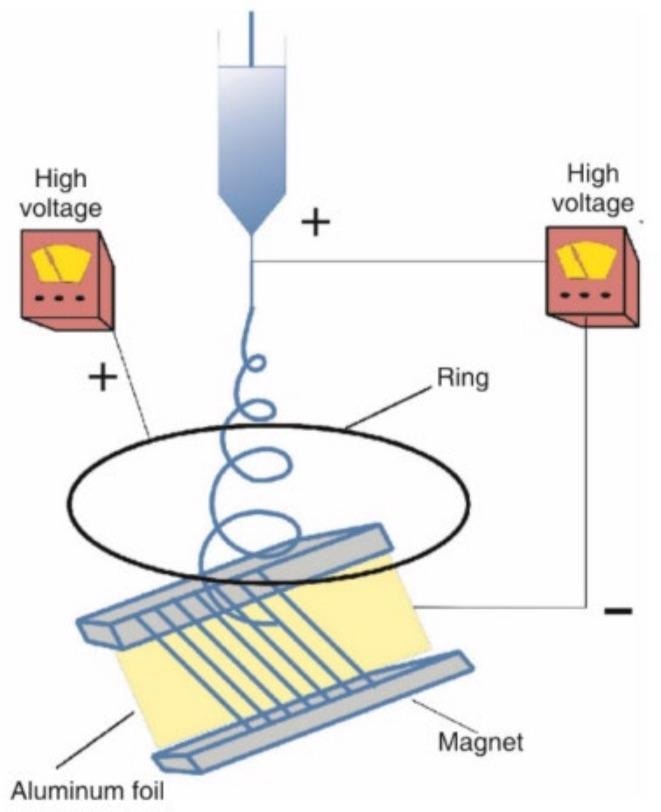
Figure 6. Schematic diagram of magnetic field electrospinning. Image Credit: Xu, et al., 2022
Many parameters impact the creation of nanofibers, including solution concentration, voltage, flow velocity, and the distance between the collector and the spinneret. The electrospinning settings can be changed to get the desired performance and look of the fiber film.
Core-shell structure, cobweb structure, hollow structure, grid structure, and other morphologies will be produced by electrospun nanofibers. The various fiber morphologies are seen in Figure 7.
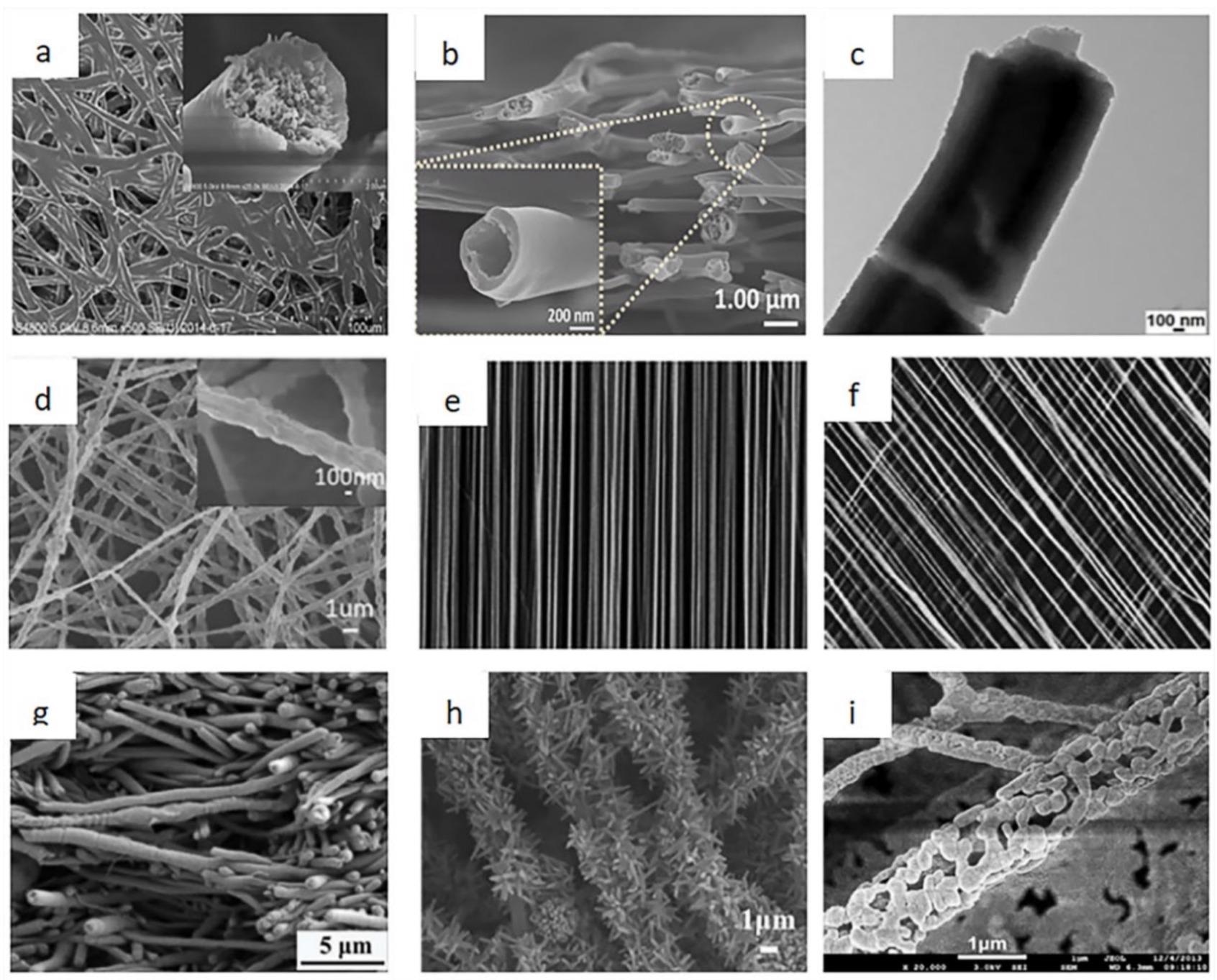
Figure 7. The different morphologies of the electrospun nanofibers. (a) Cobweb nanofiber; (b) hollow nanofiber; (c) core-shell nanofibers; (d) randomly distributed nanofibers; (e) aligned nanofibers; (f) patterned nanofibers; (g) composite nanofiber; (h) pine needle nanofibers; (i) hollowed-out nanofibers. Image Credit: Xu, et al., 2022
Discussion
The primary function of biosensors is to respond to biological information from the human body via additional biological materials and transform it into electrical signals. Scientists developed a wearable high-performance pressure sensor with PVDF-HFP as the key material for the fiber membrane. It works by sensing external pressure and converting it to an electrical signal, which is then sent back via a change in resistance.
Because of their superior qualities, electrospinning nanofibers are commonly employed in wearable sensors. Table 1 compares the electrospinning sensor to other sensors in terms of performance.
Table 1. Performance comparison with other sensors Source: Xu, et al., 2022
|
|
Sensitivity |
Linear Range |
Stability |
Ref. |
Glucose Sensor |
Electrospinning |
4022 μAmM-1 cm-2 |
0.0002–1 mM |
—— |
[29] |
others |
91.8 μAmM-1 cm-2 |
0–13.0 mM |
20 (90%)
100 (60%) |
[30] |
Blood pressure sensor |
Electrospinning |
60.28 kPa-1 |
0–24 kPa |
13,000 |
[31] |
others |
6.19 kPa-2 |
0–6 kPa |
—— |
[32] |
Body temperature sensor |
Electrospinning |
5.76 °C-1 |
24–48 °C |
100 |
[33] |
others |
8.962 nm °C-1 |
33–43 °C |
—— |
[34] |
Pressure Sensor |
Electrospinning |
1.49 kPa-1 |
—— |
around 1000 |
[35] |
others |
0.24 kPa-1 |
10.5–96.25 kPa |
around 1000 |
[36] |
Electrospinning-created nanomaterials have made a substantial contribution to the creation of wearable sensors. Nanomaterials have progressed from one-dimensional nanofibers to two-dimensional nanosheets, starting with zero-dimensional nanoparticles.
Pressure sensors, temperature sensors, biological sensors, strain sensors, and photoelectric sensors are the most common types of wearable sensors used to monitor physical health.
Through the heartbeat or pulse, the wearable pressure sensor can provide input on the body’s health. Sensors of this sort can be worn on the chest, neck, wrist, and fingers. On the other end, a display is linked to monitoring heart rate variations.
As technology advances, such sensors are increasingly being linked to smartwatches. A self-powered ultrasensitive wearable sensor for cardiac and pulse measurement has been developed by researchers. Figure 8 shows a sensor with triboelectric layers of PA and FEP films and electrodes of copper foils.
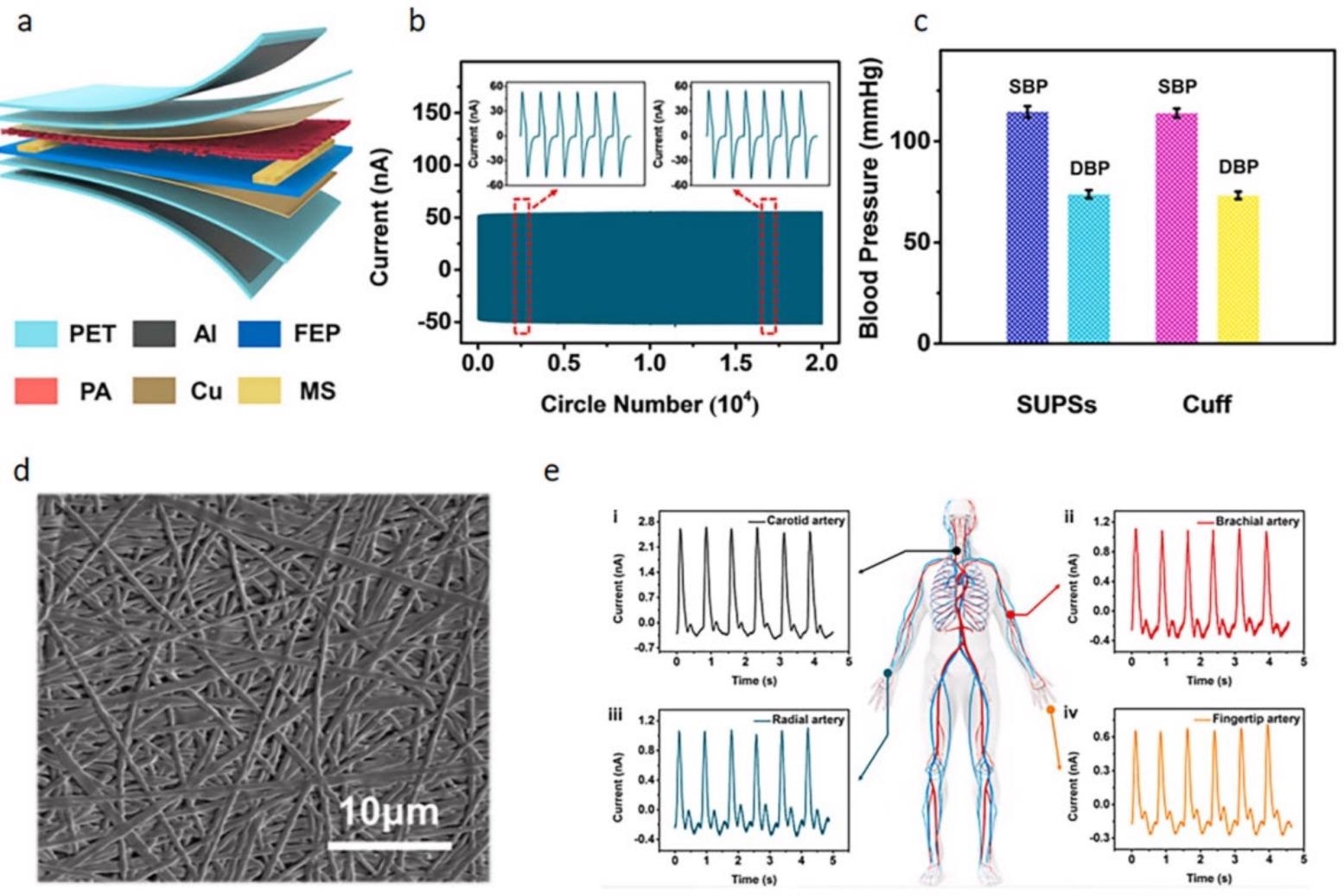
Figure 8. The construction diagram of the sensor and the monitoring diagram of blood pressure and pulse. (a) Schematic diagram of the sensor structure; (b) cycling stability of the sensor; (c) average blood pressure values measured by sensors and electronic sphygmomanometers; (d) SEM image of PA nanofiber membrane; (e) pulse signal under different arteries. Image Credit: Xu, et al., 2022
Figure 9 shows a pressure sensor that is free of sensory disturbance.
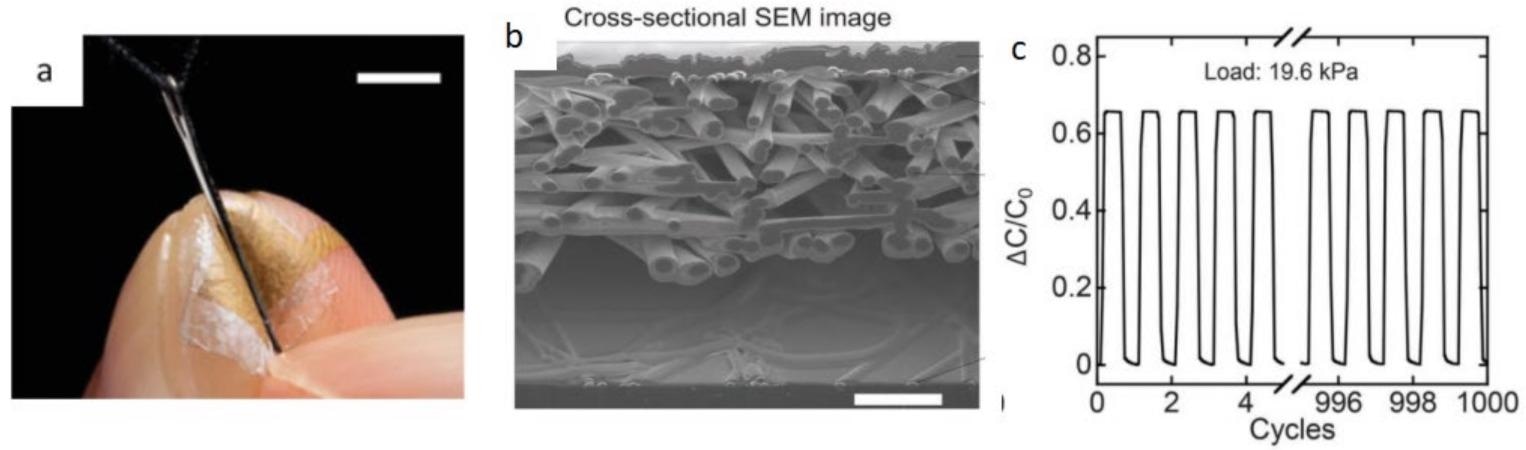
Figure 9. Schematic diagram of a pressure sensor without sensory interference. (a) Pressure sensor placed on index finger; (b) SEM image of the cross-section of the nanomesh sensor; (c) pressure sensitivity at 1000 cycles of pressure. Image Credit: Xu, et al., 2022
Figure 10 shows how researchers developed a clear and flexible fingerprint sensor that can sense tactile pressure and skin temperature. A pressure sensor, temperature sensor, and fingerprint sensor are all combined in one sensor.
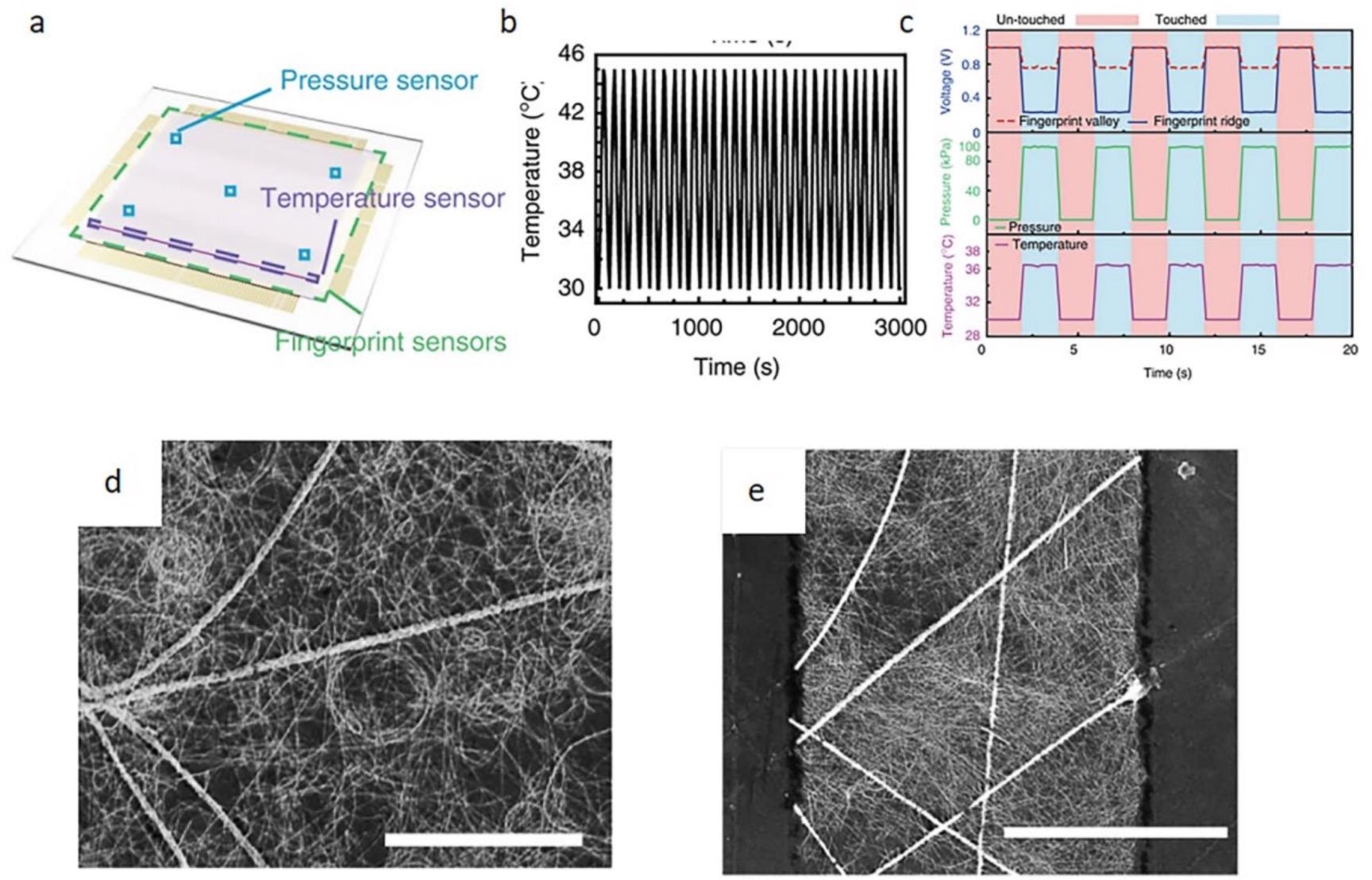
Figure 10. Sensor schematic diagram and performance characterization diagram. (a) Sensor schematic diagram; (b) stability graph with repeated loading and unloading; (c) sensor real-time sensorgram; (d, e) SEM images of a hybrid electrode and patterned hybrid electrode. Image Credit: Xu, et al., 2022
Figure 11 shows a schematic design of the electronic skin as well as an image captured by a scanning electron microscope. Although this type of electronic skin may be utilized for whole-body monitoring, its components’ degradability must be enhanced. Sweat or other contaminants may also have an impact on this electronic skin.
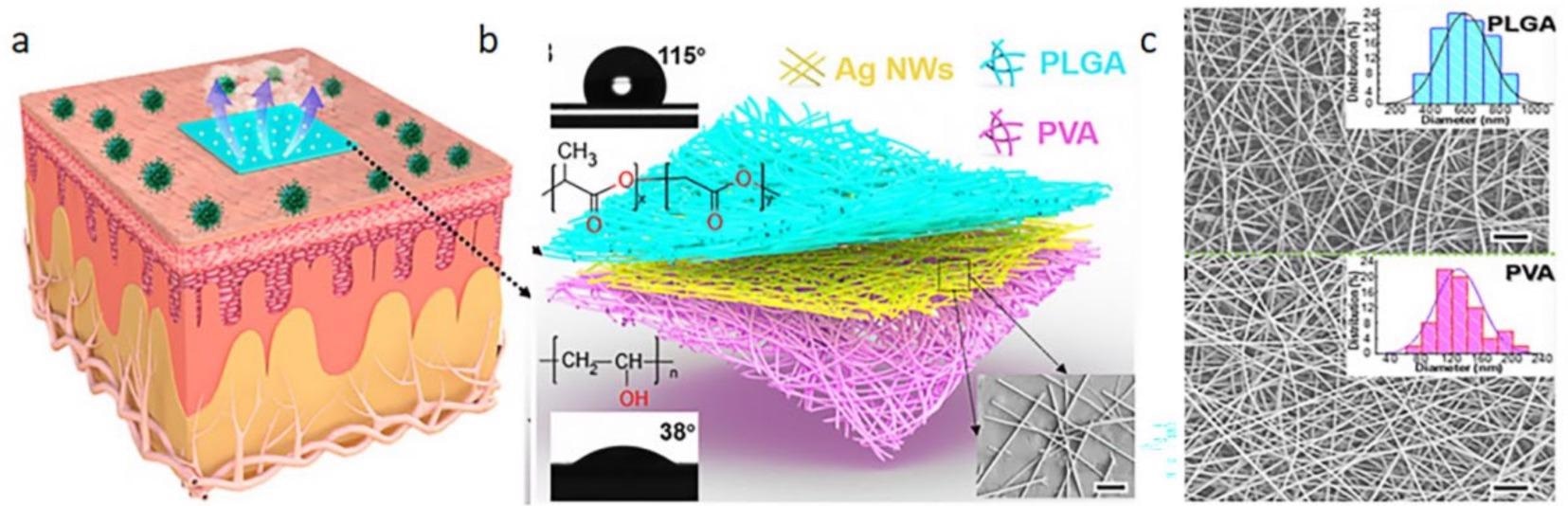
Figure 11. Schematic diagram of electronic skin and its scanning electron micrograph. (a) The electronic skin is attached to the epidermis; (b) electronic skin structure diagram; (c) SEM image of the upper and lower layers of material. Image Credit: Xu, et al., 2022
A schematic model of human movement detection is shown in Figure 12. Sensors can start picking up on the tiniest motions of the limbs. The sensor is coupled to a resistance meter, and the resistance change indicates the limb change amplitude.
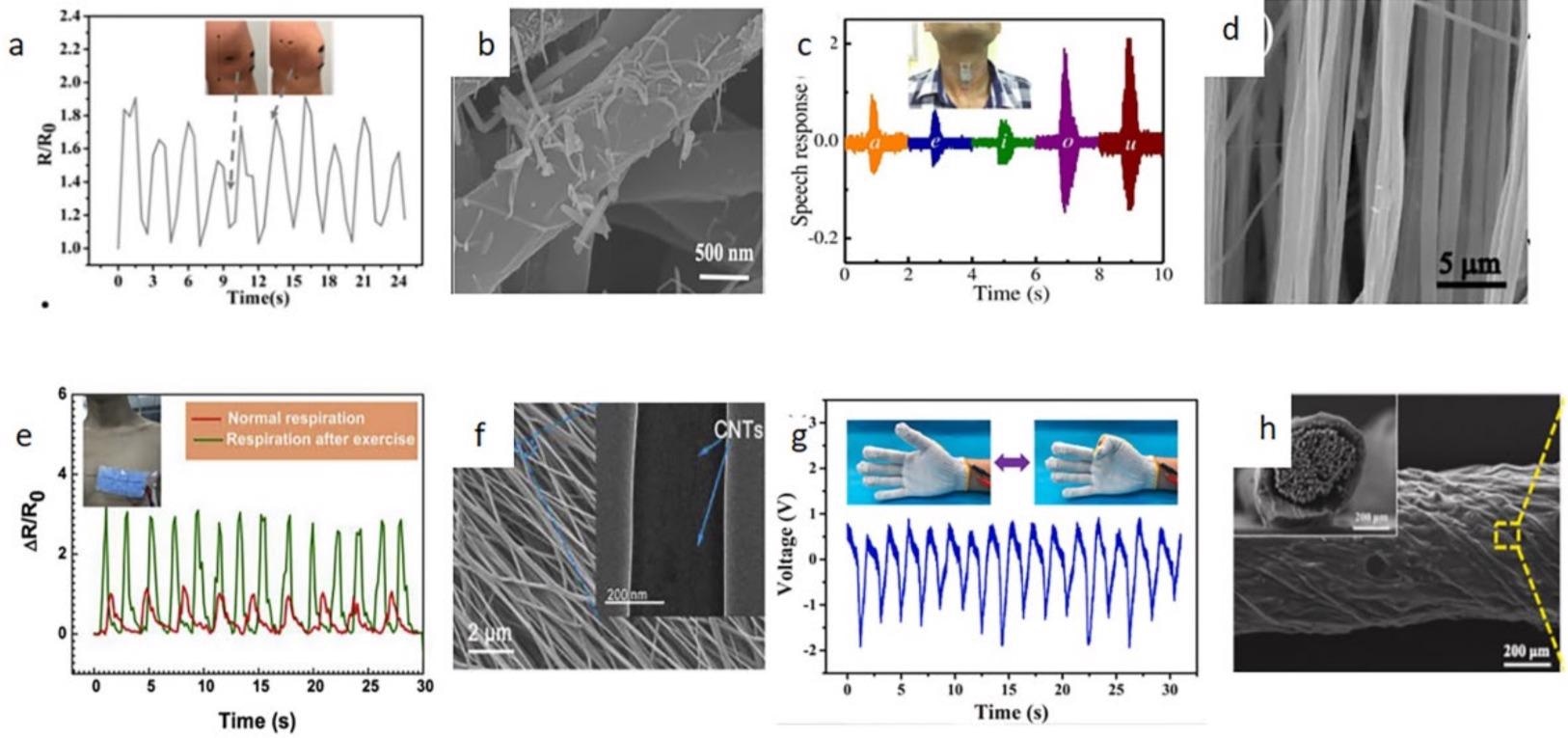
Figure 12. The response of the sensor in different parts and the SEM image of the fiber membrane. (a, b) knee bends; (c, d) swallow; (e, f) heartbeats; (g, h) Finger bends. Image Credit: Lin, et al., 2021; Kumar, et al., 2018; Kqa, et al., 2020; Guan, et al., 2021.
In addition, based on how much the arm swings, the sensor may increase the contrast of the LED light. The structure and conductivity of the power generating fabric are shown in Figure 13.
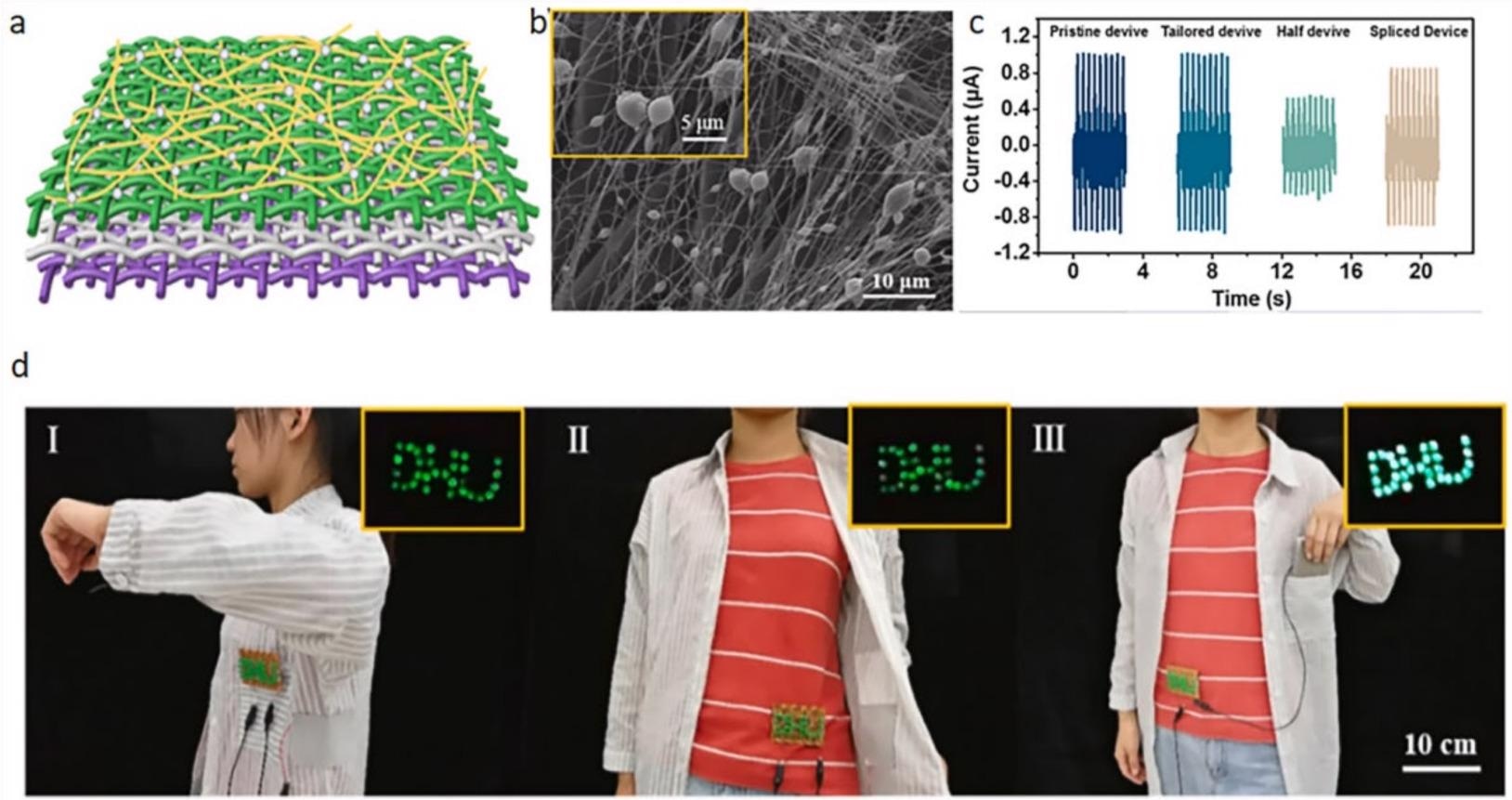
Figure 13. Model diagram and performance diagram of power generation fabric. (a) Model diagram, (b) SEM images, (c) voltage output under different conditions, (d) with different body movements, and the LED lights will glow. Image Credit: Xu, et al., 2022
Conclusion
The fast advancement of electrospinning technology in recent years has introduced new ways of thinking in people from all areas of life. In the area of sensors, the electrospinning technique is also commonly employed. Electrospun nanofibers exhibit a variety of characteristics, including high porosity, huge surface area, and superior elasticity. These outstanding results have set the groundwork for the creation of wearable sensors.
As a major research topic, wearable sensors have received much interest. Wearable biosensors have a wide range of applications as well. It may, for example, track all elements of a person’s mobility to determine their overall health.
The major mechanics and influencing aspects of electrospinning technology are discussed in this article. It also discusses how they may be used as wearable sensors. Simultaneously, it describes their use in the field of wearable sensors it demonstrates numerous different application approaches.
While electrospinning technology has achieved some significant advances in the realm of wearable sensors, more research in industrial manufacturing and normal human usage is required. With the advancement of electrospinning technology, new forms of nanofibers may be used to increase the performance of sensory sensors.
Journal Reference
Xu, T., Ji, G., Li, H., Li, J., Chen, Z., Awuye, D.E. and Huang, J. (2022) Preparation and Applications of Electrospun Nanofibers for Wearable Biosensors. Biosensors, 12(3), p.177. Available Online: https://www.mdpi.com/2079-6374/12/3/177/htm.
References and Further Reading
- Jiang, Y., et al. (2021) A Wearable Strain Sensor Based on Polyurethane Nanofiber Membrane with Silver nanowires/polyaniline Electrically Conductive Dual-network. Colloids and Surfaces A: Physicochemical and Engineering Aspects, 629, p. 127477. doi.org/10.1016/j.colsurfa.2021.127477.
- Sengupta, D., et al. (2022) Skin-Inspired Flexible and Stretchable Electrospun Carbon Nanofiber Sensors for Neuromorphic Sensing. ACS Applied Electronic Materials, 4(1), pp. 308–315. doi.org/10.1021/acsaelm.1c01010.
- Lin, J., et al. (2021) Wearable sensors and devices for real-time cardiovascular disease monitoring. Cell Reports Physical Science, 2(8), p. 100541. doi.org/10.1016/j.xcrp.2021.100541.
- Zong, X., et al. (2003) Structure and morphology changes during in vitro degradation of electrospun poly(glycolide-co-lactide) nanofiber membrane. Biomacromolecules, 4(2), p. 416. doi.org/10.1021/bm025717o.
- Cao, M., et al. (2020) Wearable piezoresistive pressure sensors based on 3D graphene. Chemical Engineering Journal, 406, p. 126777. doi.org/10.1016/j.cej.2020.126777.
- He, C. H., et al. (2020) Taylor series solution for fractal Bratu-type equation arising in electrospinning process. Fractals, 28(1), p. 2050011. doi.org/10.1142/S0218348X20500115.
- Mohammadi, Z & Jafari, S M (2020) Detection of food spoilage and adulteration by novel nanomaterial-based sensors. Advances in Colloid and Interface Science, 286, p. 102297. doi.org/10.1016/j.cis.2020.102297.
- Xiaomei, W., et al. (2018) Tactile-Sensing Based on Flexible PVDF Nanofibers via Electrospinning: A Review. Sensors, 18(2), p. 330. doi.org/10.3390/s18020330.
- Zhou, C., et al. (2016) Electrospun nanofibers for cancer diagnosis and therapy. Biomaterials Science, 4(6), pp. 922–932. doi.org/10.1039/C6BM00070C.
- Wang, Y., et al. (2021) Fabrication of energetic aluminum core/hydrophobic shell nanofibers via coaxial electrospinning. Chemical Engineering Journal, 427, p. 132001. doi.org/10.1016/j.cej.2021.132001.
- Wang, L., et al. (2017) Multi-Compartment Centrifugal Electrospinning Based Composite Fibers. Chemical Engineering Journal, 330, pp. 541–549. doi.org/10.1016/j.cej.2017.07.179.
- Zheng, G., et al. (2020) Nanofiber membranes by multi-jet electrospinning arranged as arc-array with sheath gas for electrodialysis applications. Materials & Design, 189, p. 108504. doi.org/10.1016/j.matdes.2020.108504.
- Liu, J., et al. (2020) Highly stretchable and transparent triboelectric nanogenerator based on multilayer structured stable electrode for self-powered wearable sensor. Nano Energy, 78, p. 105385. doi.org/10.1016/j.nanoen.2020.105385.
- Guan, M., et al. (2019) Yarn-ball-shaped P2-Na2/3Fe1/2Mn1/2O2 nanofibers prepared by magnetic-assisted electrospinning method as high-performance cathode material for Na-ion batteries. Materials Letters, 254, pp. 24–27. doi.org/10.1016/j.matlet.2019.07.001.
- Wang, X., et al. (2021) Recent progress of electrospun porous carbon-based nanofibers for oxygen electrocatalysis. Materials Today Energy, 22, p. 100850. doi.org/10.1016/j.mtener.2021.100850.
- Elashnikov, R., et al. (2019) Effect of sterilization methods on electrospun cellulose acetate butyrate nanofibers for SH-SY5Y cultivation. Reactive and Functional Polymers, 143, p. 104339. doi.org/10.1016/j.reactfunctpolym.2019.104339.
- Xie, J & Weng, L (2015) Smart Electrospun Nanofibers for Controlled Drug Release: Recent Advances and New Perspectives. Current Pharmaceutical Design, 21(15), pp. 1944–1959. Available at: https://www.ingentaconnect.com/content/ben/cpd/2015/00000021/00000015/art00005.
- Liu, Y., et al. (2020) A review on recent advances in application of electrospun nanofiber materials as biosensors. Current Opinion in Biomedical Engineering, 13, pp. 174–189. doi.org/10.1016/j.cobme.2020.02.001.
- Wu, J., et al. (2016) A honeycomb-cobweb inspired hierarchical core-shell structure design for electrospun silicon/carbon fibers as lithium-ion battery anodes. Carbon, 98, pp. 582–591. doi.org/10.1016/j.carbon.2015.11.048.
- Poudel, M B & Han, J K (2021) Confinement of Zn-Mg-Al-Layered double hydroxide and α-Fe2O3 nanorods on hollow porous carbon nanofibers: A free-standing electrode for solid-state symmetric supercapacitors. Chemical Engineering Journal, 429, 132345. doi.org/10.1016/j.cej.2021.132345.
- Park, J. H., et al. (2020) Sequential Removal of Radioactive Cs by Electrochemical Adsorption and Desorption Reaction using Core-Shell Structured Carbon Nanofiber–Prussian Blue Composites. Chemical Engineering Journal, 399, p. 125817. doi.org/10.1016/j.cej.2020.125817.
- Li, X., et al. (2021) Boosting piezoelectric and triboelectric effects of PVDF nanofiber through carbon-coated piezoelectric nanoparticles for highly sensitive wearable sensors. Chemical Engineering Journal, 426, p. 130345. doi.org/10.1016/j.cej.2021.130345.
- Guo, F., et al. (2018) Lasing action from dye doped polymeric nanofibers: A comparison study of well aligned with randomly oriented nanofibers. Organic Electronics, 63, pp. 52–57. doi.org/10.1016/j.orgel.2018.08.046.
- Zhao, W., et al. (2020) Hot-pressed PAN/PVDF hybrid electrospun nanofiber membranes for ultrafiltration. Journal of Membrane Science, 611, p. 118327. doi.org/10.1016/j.memsci.2020.118327.
- Su, Y., et al. (2021) Bioinspired Superhydrophobic and Superlipophilic Nanofiber Membrane with Pine Needle-like Structure for Efficient Gravity-driven Oil/Water Separation. Separation and Purification Technology, 274, p. 119098. doi.org/10.1016/j.seppur.2021.119098.
- Ma, D., et al. (2015) RGO/InVO4 hollowed-out nanofibers: Electrospinning synthesis and its application in photocatalysis. Applied Surface Science, 353, pp. 118–126. doi.org/10.1016/j.apsusc.2015.06.067.
- Kim, G J & Kim, K O (2020) Novel glucose-responsive of the transparent nanofiber hydrogel patches as a wearable biosensor via electrospinning. Scientific Reports, 10, p. 18858. doi.org/10.1038/s41598-020-75906-9.
- Young, K. O., et al. (2018) Wearable high-performance pressure sensors based on three-dimensional electrospun conductive nanofibers. NPG Asia Materials, 10, pp. 540–551. doi.org/10.1038/s41427-018-0041-6.
- Xu, Y., et al. (2021) Highly sensitive enzyme-free glucose sensor based on CuO–NiO nanocomposites by electrospinning. Composites Communications, 25, p. 100687. doi.org/10.1016/j.coco.2021.100687.
- Zhou, F., et al. (2022) A novel flexible non-enzymatic electrochemical glucose sensor of excellent performance with ZnO nanorods modified on stainless steel wire sieve and stimulated via UV irradiation. Ceramics International, 1, p. 332. doi.org/10.1016/j.ceramint.2022.01.332.
- Qin, Z., et al. (2022) Ultralight polypyrrole crosslinked nanofiber aerogel for highly sensitive piezoresistive sensor. Chemical Engineering Journal, 427, p. 131650. doi.org/10.1016/j.cej.2021.131650.
- Yeh, C. C., et al. (2019) Fabrication of a flexible wireless pressure sensor for intravascular blood pressure monitoring. Microelectronic Engineering, 213, pp. 55–61. doi.org/10.1016/j.mee.2019.04.009.
- Veeralingam, S & Badhulika, S (2020) Bi2S3/PVDF/Ppy-Based Freestanding, Wearable, Transient Nanomembrane for Ultrasensitive Pressure, Strain, and Temperature Sensing. ACS ACS Applied Bio Materials, 4(1), pp. 14–23. doi.org/10.1021/acsabm.0c01399.
- Wang, S. N., et al. (2018) A Mach-Zehnder interferometer-based High Sensitivity Temperature sensor for human body monitoring. Optical Fiber Technology, 45, pp. 93–97. doi.org/10.1016/j.yofte.2018.07.001.
- Chen, Y., et al. (2020) A Highly Sensitive and Wearable Pressure Sensor Based on Conductive Polyacrylonitrile Nanofibrous Membrane via Electroless Silver Plating. Chemical Engineering Journal, 394, p. 124960. doi.org/10.1016/j.cej.2020.124960.
- Huang, J., et al. (2021) Biomass-based wearable and Self-powered pressure sensor for human motion detection. Composites Part A: Applied Science and Manufacturing, 146, p. 106412. doi.org/10.1016/j.compositesa.2021.106412.
- Horne, J., et al. (2020) Recent developments in nanofiber-based sensors for disease detection, immunosensing, and monitoring-ScienceDirect. Sensors and Actuators Reports, 2(1), p. 100005. doi.org/10.1016/j.snr.2020.100005.
- Liu, C., et al. (2021) Current Development of Wearable Sensors Based on Nanosheets and Applications. TrAC Trends in Analytical Chemistry, 143, p. 116334. doi.org/10.1016/j.trac.2021.116334.
- Zhang, S. H., et al. (2017) Wearable Wide-Range Strain Sensors Based on Ionic Liquids and Monitoring of Human Activities. Sensors, 17(11), p. 2621. doi.org/10.3390/s17112621.
- Lee, J W & Yun, K S (2017) ECG Monitoring Garment Using Conductive Carbon Paste for Reduced Motion Artifacts. Polymers, 9(9), p. 439. doi.org/10.3390/polym9090439.
- Xu, L., et al. (2021) Self-powered ultrasensitive pulse sensors for noninvasive multi-indicators cardiovascular monitoring. Nano Energy, 81, p. 105614. doi.org/10.1016/j.nanoen.2020.105614.
- Lee, S., et al. (2020) Nanomesh pressure sensor for monitoring finger manipulation without sensory interference. Science, 370(6519), pp. 966–970. doi.org/10.1126/science.abc9735.
- Webb, R., et al. (2013) Ultrathin conformal devices for precise and continuous thermal characterization of human skin. Nature Materials, 12, pp. 938–944. doi.org/10.1038/nmat3755.
- Hong, S. Y., et al. (2016) Stretchable Active Matrix Temperature Sensor Array of Polyaniline Nanofibers for Electronic Skin. Advanced Materials, 28(5), pp. 930–935. doi.org/10.1002/adma.201504659.
- An, B. W., et al. (2018) Transparent and flexible fingerprint sensor array with multiplexed detection of tactile pressure and skin temperature. Nature Communications, 9, p. 2458. doi.org/10.1038/s41467-018-04906-1.
- Wu, X., et al. (2015) Thermally Stable, Biocompatible, and Flexible Organic Field-Effect Transistors and Their Application in Temperature Sensing Arrays for Artificial Skin. Advanced Functional Materials, 25(14), pp. 2138–2146. doi.org/10.1002/adfm.201404535.
- Song, Y., et al. (2020) Wireless battery-free wearable sweat sensor powered by human motion. Science Advances, 6(40), p. 9842. doi.org/10.1126/sciadv.aay9842.
- Wei, X., et al. (2021) Wearable Biosensor for Sensitive Detection of Uric Acid in Artificial Sweat Enabled by a Fiber Structured Sensing Interface. Nano Energy, 85, p. 106031. doi.org/10.1016/j.nanoen.2021.106031.
- Zhao, Y., et al. (2020) A wearable freestanding electrochemical sensing system. Science Advances, 6(12), p. eaaz0007. doi.org/10.1126/sciadv.aaz0007.
- Jang, J., et al. (2021) Smart contact lens and transparent heat patch for remote monitoring and therapy of chronic ocular surface inflammation using mobiles. Science Advances, 7(14), p. 7194. doi.org/10.1126/sciadv.abf7194.
- Peng, X., et al. (2020) A breathable, biodegradable, antibacterial, and self-powered electronic skin based on all-nanofiber triboelectric nanogenerators. Science Advances, 6(26), p. 9624. doi.org/10.1126/sciadv.aba9624.
- Nasiri, S & Khosravani, M R (2020) Progress and challenges in fabrication of wearable sensors for health monitoring. Sensors and Actuators A: Physical, 312, p. 112105. doi.org/10.1016/j.sna.2020.112105.
- Gang, G., et al. (2018) Recent progress of flexible and wearable strain sensors for human-motion monitoring. Journal of Semiconductors, 39, p. 011012. doi.org/10.1088/1674-4926/39/1/011012.
- Abro, Z. A., et al. (2019) A novel flex sensor-based flexible smart garment for monitoring body postures. Journal of Industrial Textiles, 49(2), pp. 262–274. doi.org/10.1177%2F1528083719832854.
- Cheng-Yu, H., et al. (2021) An FBG-based smart wearable ring fabricated using FDM for monitoring body joint motion. Journal of Industrial Textiles, 50(10), pp. 1660–1673. doi.org/10.1177%2F1528083719870204.
- Kondo, M., et al. (2020) Imperceptible magnetic sensor matrix system integrated with organic driver and amplifier circuits. Science Advances, 6(4), p. 6094. doi.org/10.1126/sciadv.aay6094.
- Lin, L., et al. (2021) Superhydrophobic and Wearable TPU Based Nanofiber Strain Sensor with Outstanding Sensitivity for High-Quality Body Motion Monitoring. Chemical Engineering Journal, 419, p. 129513. doi.org/10.1016/j.cej.2021.129513.
- Kumar, G S & Dipankar, M (2018) Synergistically Enhanced Piezoelectric Output in Highly Aligned 1D Polymer Nanofibers Integrated All-fiber Nanogenerator for Wearable Nano-Tactile Sensor. Nano Energy, 53, pp. 245–257. doi.org/10.1016/j.nanoen.2018.08.036.
- Kqa, C., et al. (2020) Weavable and stretchable piezoresistive carbon nanotubes-embedded nanofiber sensing yarns for highly sensitive and multimodal wearable textile sensor. Carbon, 170, pp. 464–476. doi.org/10.1016/j.carbon.2020.07.042.
- Guan, X., et al. (2021) Breathable, washable and wearable woven-structured triboelectric nanogenerators utilizing electrospun nanofibers for biomechanical energy harvesting and self-powered sensing. Nano Energy, 80, pp. 105549. doi.org/10.1016/j.nanoen.2020.105549.
- Qian, Q., et al. (2019) Highly flexible, breathable, tailorable and washable power generation fabrics for wearable electronics. Nano Energy, 58, pp. 750–758. doi.org/10.1016/j.nanoen.2019.02.010.
- Veeramuthu, L., et al. (2019) Smart garment energy generators fabricated using stretchable electrospun nanofibers. Reactive and Functional Polymers, 142, pp. 96–103. doi.org/10.1016/j.reactfunctpolym.2019.06.008.
- Nakata, S., et al. (2018) A wearable pH sensor with high sensitivity based on a flexible charge-coupled device. Nature Electronics, 1, pp. 596–603. doi.org/10.1038/s41928-018-0162-5.
- Wang, Y., et al. (2021) Wearable plasmonic-metasurface sensor for noninvasive and universal molecular fingerprint detection on biointerfaces. Science Advances, 7(4), p. 4553. doi.org/10.1126/sciadv.abe4553.