Sensors are used to guide production in many manufacturing environments. These sensors ensure that design parameters are adhered to, thus ensuring the quality of the end product. Industrial sensors typically measure temperature, pressure, force, or position. The types of measurements required determine the types of sensors used.
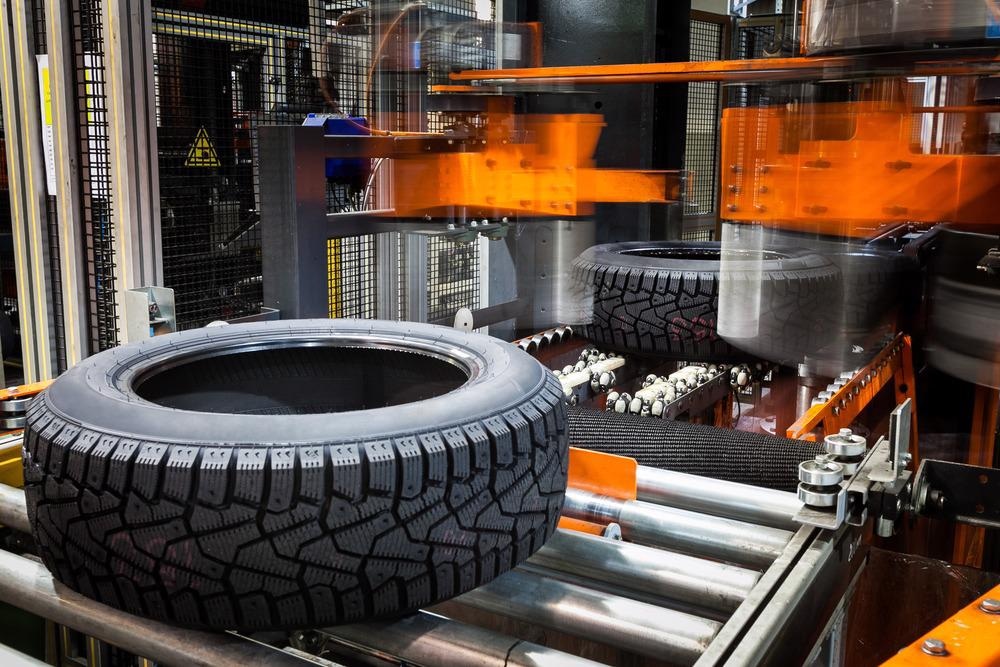
Image Credit: ShutterStock/Dobrovizcki
In certain manufacturing environments, dynamic measurements under extreme conditions are required. The tire manufacturing process, for example, produces corrosive gases, which may prevent some sensors from operating optimally.
Magnetostrictive linear position sensors, which measure distance along an axis of motion, play a critical role in factory automation. They are simple to install and provide accurate position feedback that helps automate advanced industrial machinery. These sensors are a cost-effective alternative to linear potentiometers.
In this article, we will discuss the basics of magnetostrictive technology, the advantages of magnetostrictive linear position sensors, and explore some of their practical applications.
How do Magnetostrictive Linear Position Sensors Work?
Magnetostriction describes the propensity of ferromagnetic materials to deform when placed in a magnetic field. In these materials, molecular dipoles and magnetic field boundaries (Bloch walls) rotate to align with the applied field. This results in deformation within the material. Thus, in magnetostrictive materials, electromagnetic energy is converted into mechanical energy.
Isotropic ferromagnetic materials, such as iron, copper, nickel, gold, or aluminum, are most effective in magnetostriction because they allow their molecular dipoles to rotate easily.
Magnetostriction was first observed by James Prescott Joule in 1842. The opposite effect, where applied mechanical stress produces a magnetic field, was first observed by Enrico Villari in 1865. In 1858, Gustav Wiedemann observed torsional oscillations in a ferromagnetic rod that was subjected to a combined longitudinal and circular magnetic field (the latter caused by the flow of an electric current). Thus, the Joule effect, the Villari effect, and the Wiedemann effect are notable effects in magnetostriction.
Magnetostrictive linear position (displacement) sensors measure the distance between a position magnet and a sensing module. Parts do not wear out because the position magnet does not touch the sensing rod at any point.
The sensing rod is oriented along the axis of motion, and the position magnet is attached to the machine component being measured. An electronics module records the location of the position magnet.
A magnetostrictive position sensor comprises five core components:
Position magnet: The position magnet applies a magnetic field to the waveguide.
Waveguide: The waveguide constitutes the heart of the apparatus. It is so-called because it carries an ultrasonic wave during measurement. This wave (strain wave) results from the interaction between the magnetic field at the position magnet and the field induced in the waveguide by the electronics module (called an interrogation pulse).
Electronics module: As previously stated, an interrogation pulse is initiated in the waveguide by the electronics module. As this happens, a timer starts. This timer stops once the electronics module receives the return pulse. Since the time delay to the position magnet is proportional to its distance, a distance can be calculated.
Strain wave converter: The strain wave converter receives the strain wave from the location of the position magnet. The strain wave (return pulse) travels along the waveguide towards the electronics module at roughly ten times the speed of sound (about 3000 m/s).
Damp: Since another strain wave also travels in the waveguide in the direction opposite to the return pulse, it is eliminated by the damp to prevent interference.
Magnetostrictive Linear Position Sensors vs Potentiometers
There are two ways sensors measure displacement (or distance): by the distance covered between two points or by the angular displacement (rotations) of a component. Thus, linear position sensors measure the straight-line displacement between two points, whereas rotational position sensors measure the number of rotations of a given component - For example, the number of times a robot’s wheels rotate tells the sensor how far it has traveled.
Potentiometers are commonly used as position sensors because they are inexpensive. A potentiometer is a resistor with three points of contact on a resistive element, a sliding or rotating contact (wiper) that moves along this resistive element, and a mechanism that moves the wiper from one end of the element to the other. A housing unit encapsulates both the resistive element and the wiper. Thus, the entire unit forms an adjustable voltage divider.
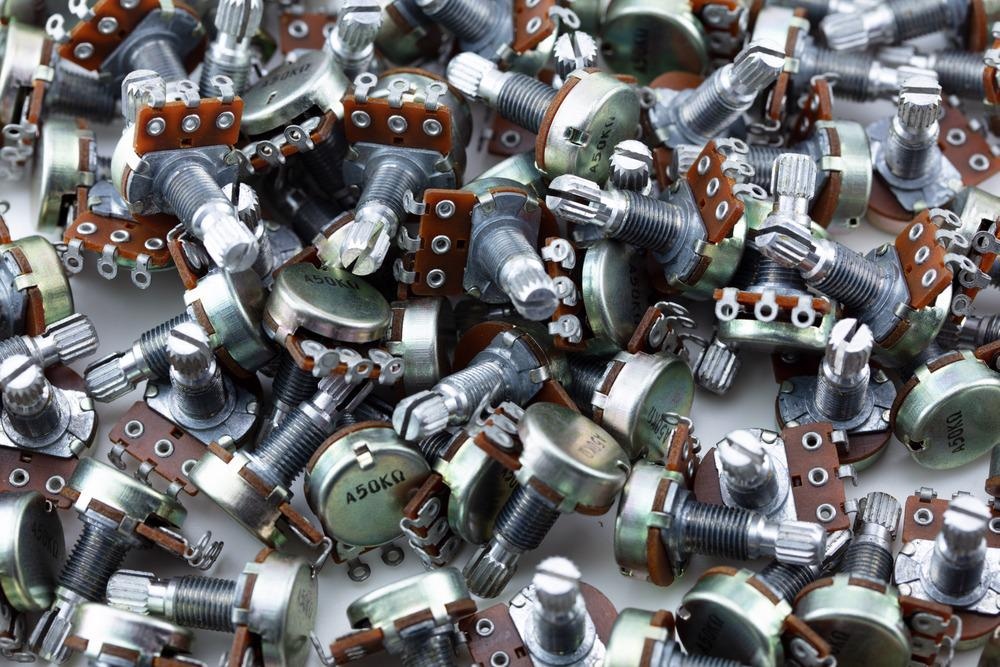
Image Credit: ShutterStock/optimarc
Potentiometers are manufactured in a range of shapes and sizes. The important thing to remember is that contamination can enter at any point in the path of the potentiometer’s wiper, thus compromising reliability. Compare this with a magnetostrictive linear position sensor, where the position magnet does not touch the sensing rod, and parts do not wear out.
Another advantage of a magnetostrictive sensor is that it can detect the location of the position magnet even when there is a barrier between the magnet and the sensing rod. This barrier can be a cylinder wall, for example, or a transmission case. The barrier can be any non-magnetic material, including plastics, ceramics, aluminum, and stainless steel.
Moreover, by incorporating multiple position sensors, magnetostrictive position sensors can affect multiple position measurements using only one sensing rod. In a plastics blow molding machine, for example, the injector motion, mold closing, and ejector can be measured using just one sensing rod. Some sensors incorporate up to 15 position magnets.
In short, magnetostrictive linear position sensors are:
- Compact
- Robust
- Ultraprecise
- Suitable for a wide range of applications
- Ideal for extreme operating environments
Practical Applications of Magnetostrictive Linear Position Sensors
Linear position sensors and transducers are used in varied applications, including test laboratories, industrial machinery, the automotive industry, and medicine. Specific applications include:
- Automotive: Suspension, transmission, and steering systems
- Semiconductors: Precision manufacturing
- Electric actuators: Linear and rotary position measurements
- Hydraulics: Process control and leakage detection systems
- Testing: Materials, automotive, aerospace, or geoseismic testing
Tire manufacturing, in particular, is a complex process resulting in heat and corrosive gases which affect the optimal performance of sensors. To avoid costly product failures, tire manufacturers need to optimize output, accuracy, reliability, and quality. Magnetostrictive linear position sensors are the ideal tools for such precision-sensitive applications.
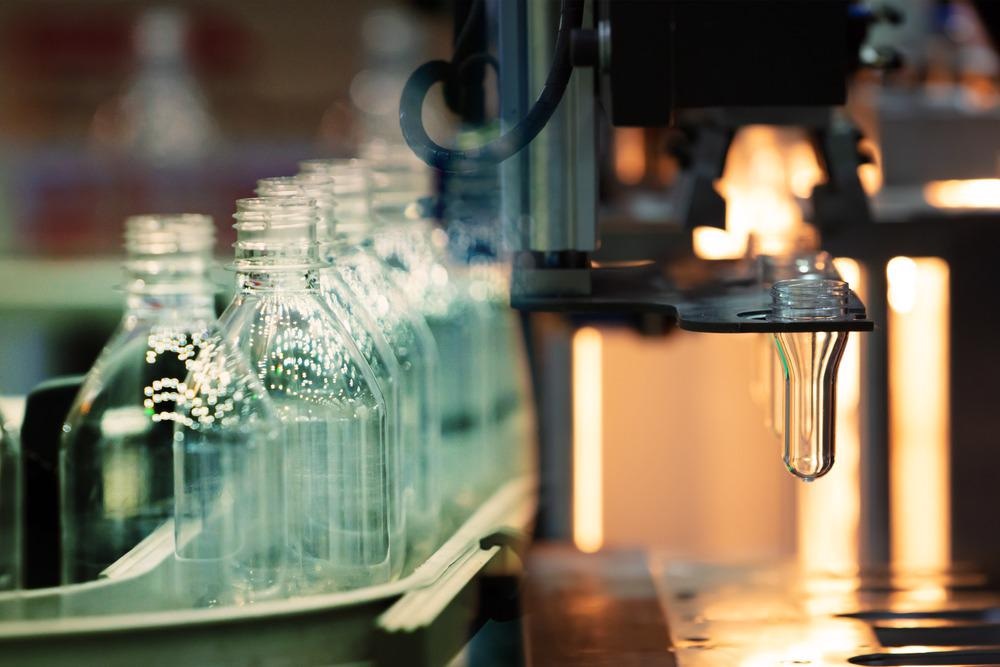
Image Credit: ShutterStock/MOLPIX
Elsewhere, in plastics manufacturing, a plastics blow-molding machine uses four axes (carriage position, injector screw position, mold eject, and mold closure) or more linear positioning to control production. Again, magnetostrictive linear position sensors are the ideal tools for such precision-sensitive applications.
Magnetostrictive Linear Position Transducers from AMETEK
AMETEK is one of the world’s leading manufacturers of linear (and rotary) position sensors.
Our Gemco flagship product line is a cost-effective alternative to linear potentiometers. This includes the BRIK 955 Series of easy-to-install linear displacement transducers. These linear position sensors are self-contained and do not comprise a can or head assembly. Therefore, all electronic components are incorporated into the sensor.
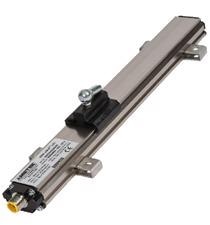
Gemco 955 Series BRIK Linear Displacement Transducer (LDT)
Image Credit: ShutterStock/optimarc
The 956 BLOK series are suited to applications where mounting a standalone rod or profile-style linear displacement transducer is not feasible. They are also self-contained, without the need for a can or head assembly. All electronics components are housed in a two-chamber rod and barrel-style housing.
References
AMETEK. What is Magnetostrictive Position Sensing? [online] Available at: https://www.ametekfactoryautomation.com/support/faq/magnetostrictive-measurement-explained
Yu, G. (2021) Magnetostriction. LibreTexts. [online] Available at: https://eng.libretexts.org/Bookshelves/Materials_Science/Supplemental_Modules_(Materials_Science)/Magnetic_Properties/Magnetostriction