Interview conducted by Maria OsipovaApr 11 2022
In this interview, AZO Sensors addresses the advantages and differences of ultrasonic sensors versus optical sensors with Dylan Fyler.
Can you explain what ultrasonic sensors are and how they work?
Simply put, ultrasonic sensors generate and receive acoustic waves. The (sound) waves are inaudible to humans because the frequencies are greater than (ultra) the upper limit for our ears. In the same way a bat searches for prey, ultrasonic transducers measure the time-of-flight of an acoustic wave to determine the distance to a target. The acoustic signal generation occurs by driving a piezoceramic with an oscillating electrical pulse, usually the transducer's best operating frequency (resonance). This vibrates the ceramic, which creates a sound wave. A portion of the acoustic wave will reflect off a target (an echo) and return to the transducer, generating a similar but smaller voltage signal. Electronic circuits and microcontrollers can then be used to estimate the distance and size of the target.
What are some of the applications of these sensors, and would any of them be surprising or unexpected for people unfamiliar with the technology?
Industrial process measurement and control (in making paper and wood laminates), obstacle avoidance and mapping for robots, and flow measurement (acoustic anemometry) are a few examples. They are often used in automated car washes to sense vehicle position because the sound waves can easily penetrate the water mist. They have also been used in bowling alleys for upright pin detection and automatic scoring. However, the most common use is probably back-up sensors in cars.
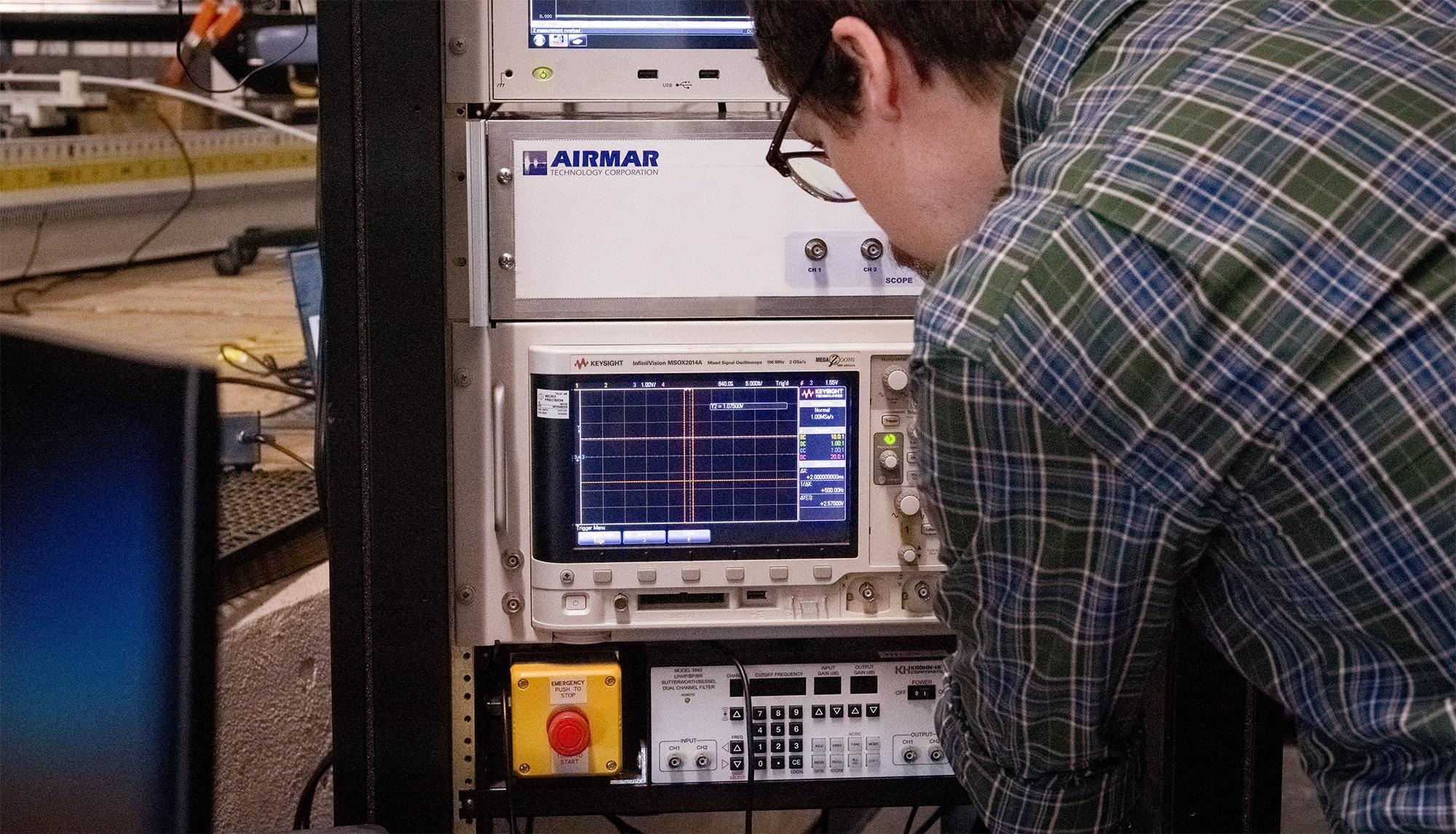
Image Credit: AIRMAR Technology Corporation
Can you explain the differences and advantages of ultrasonic sensors over optical sensors?
Optical sensors are susceptible to being blocked out by dust and other debris present in industrial processes. Ultrasonic sensors can also tolerate far more surface contamination than optical sensors before degradation of the signal occurs. Optical sensors, by themselves, cannot measure distance unless a laser is used.
Laser-based ranging systems sense the distance from the sensor to a fixed point. However, suppose the target surface has a distributed height, such as grain in a hopper. In that case, diffuse sound beams from ultrasonic sensors will ensonify more of the target and provide an average height measurement over an area.
Ultrasonic sensors are also usually lower cost than optical sensors, and they are more compact for the resolution they offer than small radar systems.
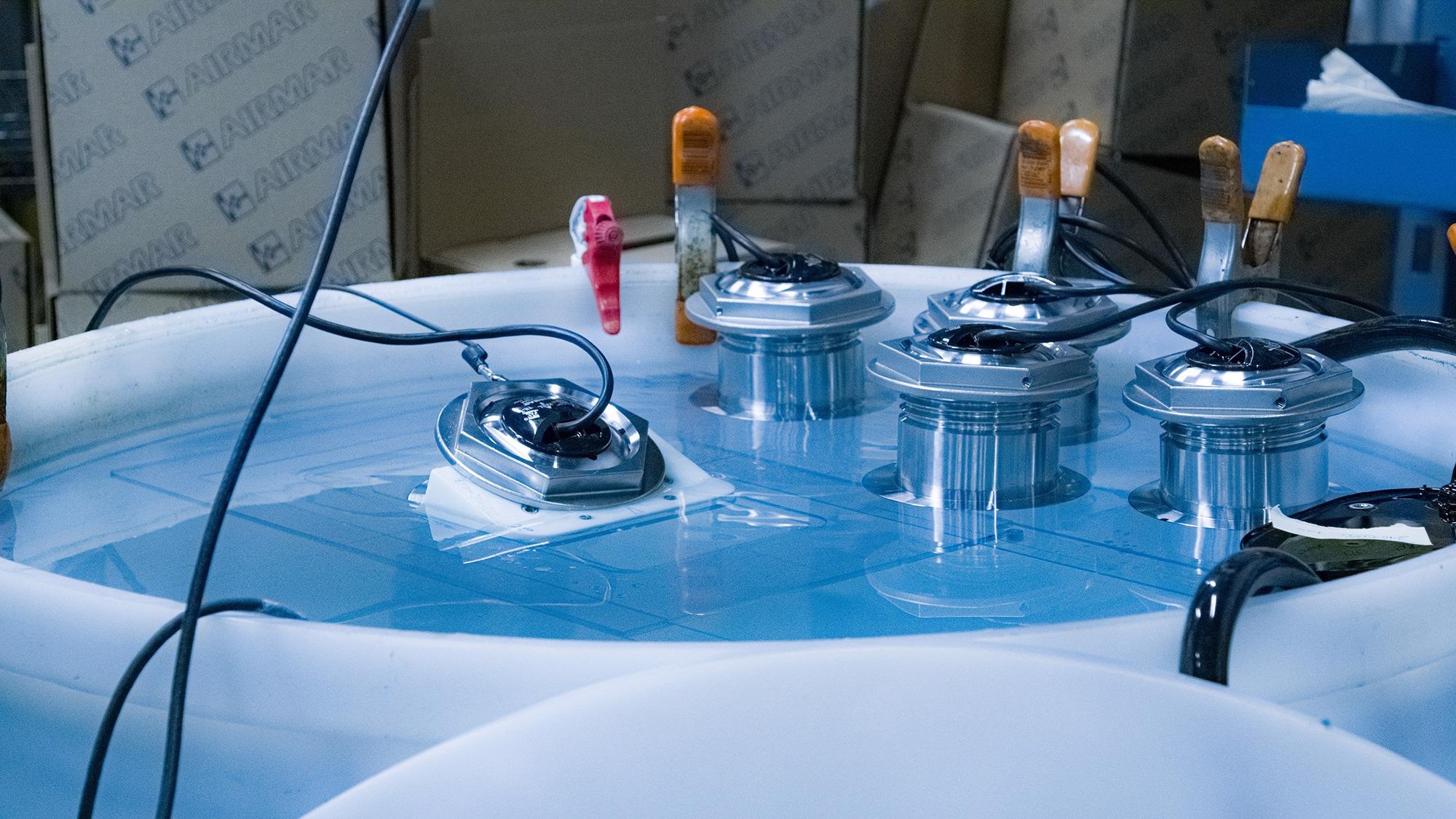
Image Credit: AIRMAR Technology Corporation
Can you explain the differences and advantages of ultrasonic sensors over radar?
Ultrasonic sensors typically provide a lower-cost alternative to radar range sensors. For example, Airmar’s long range ultrasonic ART15 Airducer with a range of up to 60 meters is a great alternative. In addition, ultrasonic sensors can reflect a sound wave off most materials, whereas radar waves will not reflect off materials with small reflectivity (small dielectric constant).
What are some of the environmental factors that can hamper ultrasonic sensors, and how can these be overcome?
Since ultrasound-ranging devices rely on transmitting and receiving sound waves through the atmosphere, variations in humidity and temperature will impact both the time of flight and the amplitude of the acoustic wave. However, in systems where precision measurements are required, temperature and humidity sensors can be used to compensate for the effects.
What are the best targets for ultrasonic sensors, and why?
The diffuse conical sound beams transmitted from ultrasonic sensors generate the most signal when targeting wide surfaces. Increased surface area results in more acoustic waves being reflected to the source, resulting in a stronger signal to estimate the surface range. Almost all materials are sufficiently hard to reflect sound well. The only materials that do not reflect airborne sound well are very porous materials like lightweight foam and fiberglass wall insulation. Those materials also happen to be used for sound absorption and wall treatment in concert halls and acoustic measurement chambers.
What sets your ultrasonic transducers apart from others on the market?
All AIRMAR air-ranging transducers are tuned to maximize sensitivity and bandwidth by measuring and tuning each one. In addition, they are made to be durable for both interior and exterior use.
What advantages does this confer to the user?
Increased sensitivity improves the transducer's ability to sense targets at large distances, and increased bandwidth reduces the transducer ring-down time, allowing for sensing targets close to the source. The durability allows their use in challenging conditions.
How has this technology changed over recent years?
Changes in the transducer design to allow greater bandwidth signals, like Chirp. Broadband signals provide finer-ranging estimates and improve performance in long-range sensing applications without using excess power. The electronics revolution, particularly in miniaturizing and microprocessors, has been an enabler for the use of acoustic bandwidth.
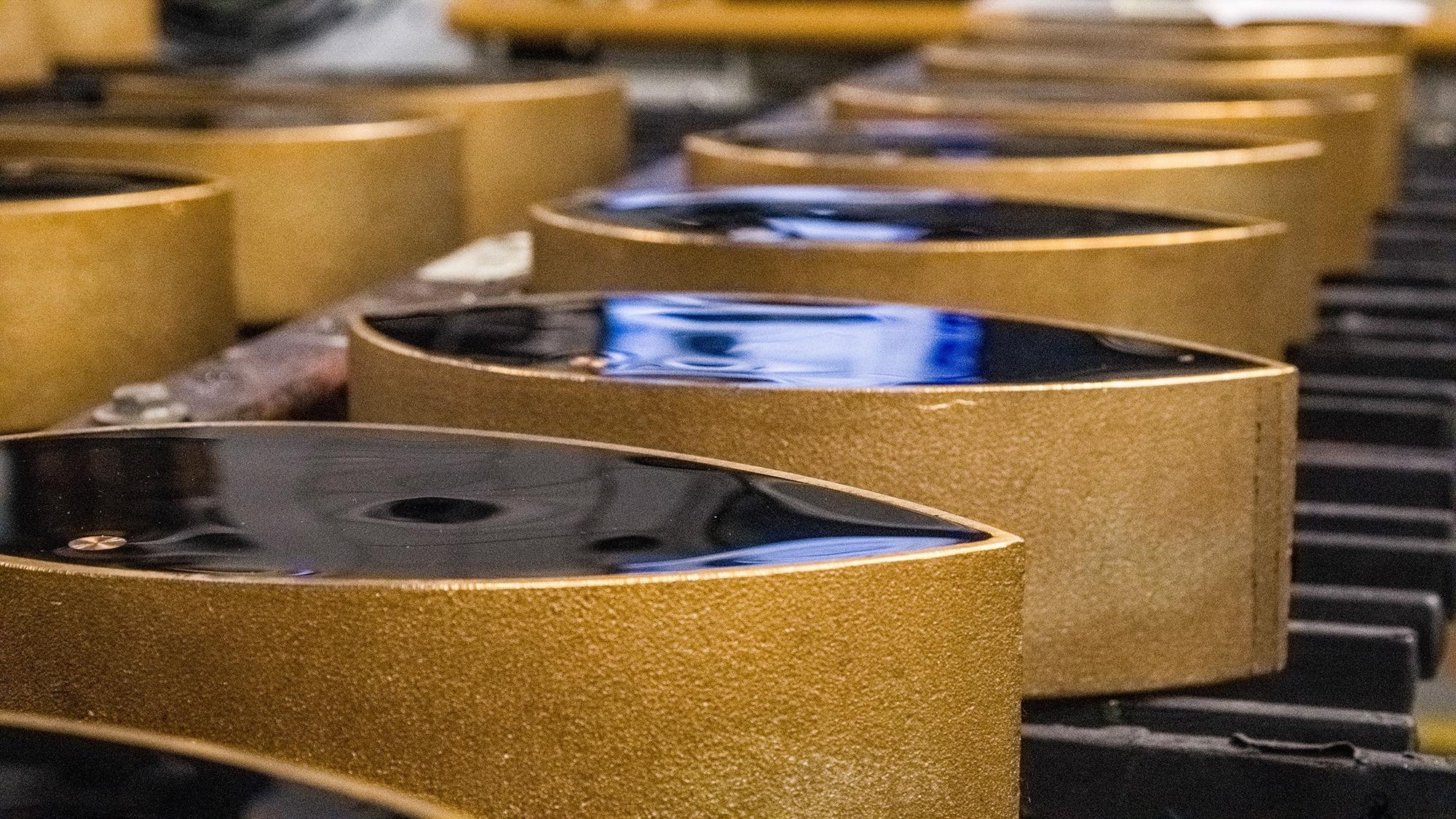
Image Credit: AIRMAR Technology Corporation
What are some of the challenges that ultrasonic developers have faced, and how have you overcome these?
Ultrasonic ranging sensors are ideal for sensing in environments with hazardous chemicals. However, delicate materials used to construct the ultrasonic transducer can be damaged in these dangerous environments. Therefore, AIRMAR has developed ultrasonic transducers packaged in a rugged one-piece PVDF housing that can be deployed in caustic environments. The PVDF face of the housing is acoustically tuned to offer maximum transducer sensitivity while providing high durability.
What does the future hold for ultrasonic devices, and what developments are you excited to see?
Data fusion with passive optics (cameras) in robotic applications will expand the sales market. The transducer design and performance are also expected to improve by incorporating novel materials.
About AIRMAR Technology Corporation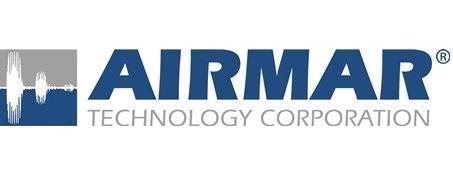
AIRMAR® Technology Corporation is a world-leading designer, manufacturer and supplier of high-performance ultrasonic industrial, marine and survey transducers, and ultrasonic WeatherStation® multisensors.
Airmar produces the most reliable, high-quality non-contact ultrasonic air transducers for use in today’s challenging commercial and industrial applications. Our Airducer® air-ranging transducers are critical components in the development of a myriad of measurement systems in fields that require liquid or solid levels, flow control, automation control, proximity sensing, obstacle avoidance, distance measurement and process control.
About Dylan Fyler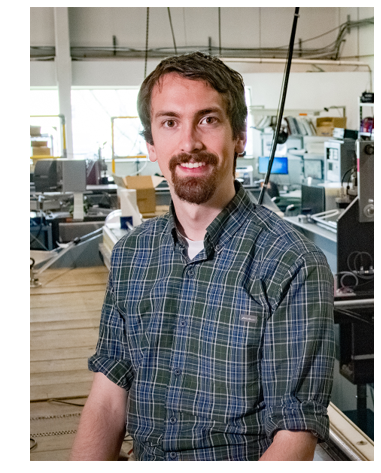
Dylan Fyler received his Bachelor of Science in Mechanical Engineering in 2015. He continued his education and earned a Master of Science in Mechanical Engineering, doing research focused on minimizing vibrations in gear trains. In 2016, he joined the research and development team at AIRMAR Technology Corporation as an acoustic engineer, working on designing and analyzing ultrasonic transducers for marine and industrial applications. His current research involves applying novel design techniques to develop transducer designs for specialized applications.
This information has been sourced, reviewed and adapted from materials provided by AIRMAR Technology Corporation.
For more information on this source, please visit AIRMAR Technology Corporation.
Disclaimer: The views expressed here are those of the interviewee and do not necessarily represent the views of AZoM.com Limited (T/A) AZoNetwork, the owner and operator of this website. This disclaimer forms part of the Terms and Conditions of use of this website.