Vibration is a complicated measurement that comprises a number of different parameters. There are advantages and disadvantages in different measurement technologies based on the ultimate vibration measurement goals. This application note covers all these areas.
Vibration Measurement
Vibration is a cyclic or periodic displacement of an object around a center static position. These contributing factors have a complicated relationship with the rate and magnitude of vibration:
- The object’s own natural frequencies and stiffness.
- The amplitude and frequencies of any external energy source(s) inducing the vibration.
- The coupling mechanism between the vibration energy source and the object of interest.
Vibration measurement is complicated as it comprises many components:
- Velocity
- Displacement
- Frequency
- Acceleration.
These components can be measured as peak-to-peak, peak, average, RMS; each of which can be measured in the time domain (real-time, instantaneous measurements with an oscilloscope or data acquisition system) or frequency domain (vibration magnitude at different frequencies across a frequency spectrum), or just a single number for “total vibration.” Figures 1, 2, and 3 show vibration measurement in the time domain, frequency domain, and the display of total vibration.
.jpg)
Figure 1. Viewing vibration in the time domain reveals the instantaneous location of the vibrating surface at different moments in time.
.gif)
Figure 2. Viewing vibration in the frequency domain reveals the magnitude of vibration at different frequencies.
.jpg)
Figure 3. “Total Vibration” can be displayed with the TIR function on the MM190 Meter Module.
Impulse and Continuous Vibration Measurement
Continuous vibration measurements are used for operational testing and condition monitoring. It measures directly what happens to the object of interest under real operating conditions.
Impulse vibration involves striking the object with a calibrated hammer that determines impact force and then measures the resulting object vibration. This test type reveals resonances in the object to help in predicting its behaviour in operating conditions.
Vibration Measurement Equipment and Vibration Sensor Technology
Vibration is measured with the following instruments:
Measuring Vibration with Accelerometers
Accelerometers are tiny devices directly installed on the surface or within the vibrating object. They contain a tiny mass that is suspended by flexible components that operate like springs.
The movement of the accelerometer will cause the small mass to deflect proportionally to the rate of acceleration. Accelerometers can provide acceleration information in one or more axes.
Measuring Vibration with Non-contact Displacement Sensors
Non-contact displacement sensors mount with a tiny gap between the sensor (probe) and a surface of the vibrating object. Capacitive and eddy-current displacement sensors are excellent choices for high-resolution, high-speed measurements.
Since their outputs are displacement measurements, they are ideal for relative vibration (positional vibration) measurements. These measurements are done when the physical location of the surface of the vibrating object at any moment in time is a critical factor. Figures 4 and 5 show capacitive and eddy-current non-contact displacement sensors.
.jpg)
Figure 4. Capacitive non-contact displacement sensors.
.jpg)
Figure 5. Eddy-current, non-contact displacement sensors.
Instantaneous and Total Vibration
Outputs are produced on displacement sensors that can be observed in real-time on an oscilloscope or with a data-acquisition system. This real-time, instantaneous data offers precise vibration data which can be used to determine a machine’s performance as a function of time or angular location of a rotating part.
The tracking TIR option can be used if the vibration value is expected to change over time, which may be during an adjustment to the mechanical system. The peak-to-peak value is displayed in the tracking TIR, but peak values will slowly decay towards zero. These are shown in Figures 6 and 7.
.jpg)
Figure 6. “Total Vibration” can be measured with TIR (peak-to-peak) captures of the vibration signal.
.jpg)
Figure 7. Changing “total vibration” can be measured with Tracking TIR option of the MM190 Module.
Displacement Sensor Probe Mounting
A three-point clamp mount is not stable and is impacted by small form errors in roundness. While measuring vibration it is likely that the displacement sensors will also be exposed to vibration.
Smooth, cylindrical probes which are clamp mounted require careful consideration as they are more likely to be affected by a vibrating environment. There are different clamp mounting methods for cylindrical style probes. A common mounting method is a through-hole with a set screw to secure the probe. For measurements in a stable, non-vibrating environment not measuring at the sub-micron levels, this method is often sufficient.
For high-resolution measurements in a vibrating environment, a better system is required.
A “pinch clamp” mount in which a through-hole is tightened on the cylindrical probe is a better solution. The full-circumference clamp engages more of the surface of the probe and will provide a more stable mount.
The most stable clamping method uses a pinch clamp that clamps the probe at three or four points rather than the full circumference. This method remains stable in spite of roundness errors of the probe body or the clamp’s through-hole.
Figures 8 and 9 show the displacement sensor probe mounting.
.gif)
Figure 8. Set-screw mounting locks the probe along the probe’s axis, but there may still be movement in the other two axes, especially at the micro and nano levels.
.gif)
Figure 9. A clamp mount is a more stable mount than a set-screw mount. But at the micro and nano levels, form errors can result in only a two-point clamp much like a set-screw mount.
Environmental Considerations for Capacitive Sensors
Capacitive sensors require a clean, dry environment. Any change in the material between the probe and target will affect the measurement. All sensors have some sensitivity to temperature, but Lion Precision capacitive sensor systems are compensated for temperature changes between 20°C and 35°C with a drift of less than 0.04%F.S./°C.
Additional Eddy-Current Displacement Sensor Mounting Considerations
Eddy-current probe mounting must allow a metal-free space around the tip at least three times the probe diameter. Flush mounting requires a counterbore. Eddy-Current displacement sensors use a magnetic field that engulfs the end of the probe. As a result, the “spot-size” of eddy-current displacement sensors is about 300% of the probe diameter. This means any metallic objects within three probe diameters from the probe will affect the sensor output.
Multiple Eddy-Current Probes
When multiple probes are used with the same target, they must be separated by at least three probe diameters to prevent interference between channels. If this is unavoidable, special factory calibrations are possible to minimize interference.
Environmental Considerations for Eddy-Current Sensors
Linear displacement measurements with eddy-current sensors are immune to foreign material in the measurement area. The great advantage of eddy-current non-contact sensors is that they can be used in rather hostile environments. All non-conductive materials are invisible to eddy-current sensors. Even metallic materials like chips from a machining process are too small to interact significantly with the sensors.
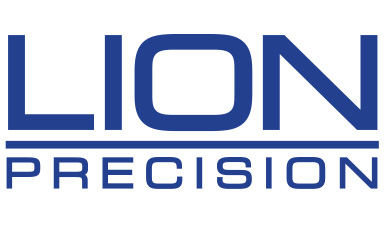
This information has been sourced, reviewed, and adapted from materials provided by Lion Precision.
For more information on this source, please visit Lion Precision.